Fabrication of Metallic Pressure Vessels
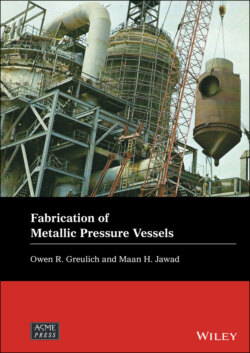
Реклама. ООО «ЛитРес», ИНН: 7719571260.
Оглавление
Maan H. Jawad. Fabrication of Metallic Pressure Vessels
Table of Contents
List of Tables
List of Illustrations
Guide
Pages
Wiley‐ASME Press Series
Fabrication of Metallic Pressure Vessels
Preface
Acknowledgments
1 Introduction. 1.1 Introduction
1.2 Fabrication Sequence
1.3 Cost Considerations
1.3.1 Types of costs
1.3.2 Design choices. 1.3.2.1 Major cost decisions – long term choices
1.3.2.2 Labor–material trade‐offs
1.3.2.3 Selecting a less expensive material
1.3.2.4 Selection of a material with a higher allowable stress
1.3.2.5 Component selection to eliminate operations
1.3.2.6 Enhanced inspection for higher joint efficiency
Example 1.1
1.3.2.7 Process choices
1.3.2.8 Forming
1.3.2.9 Fixturing
1.3.2.10 Welding
1.3.2.11 Hydrotesting
1.3.3 Shipping
1.3.4 General approach to cost control
1.4 Fabrication of Nonnuclear Versus Nuclear Pressure Vessels
1.5 Units and Abbreviations
1.6 Summary
2 Materials of Construction. 2.1 Introduction
2.2 Ferrous Alloys
2.2.1 Carbon steels (Mild steels)
2.2.1.1 Applications
2.2.2 Low alloy steels (Cr–Mo steels)
2.2.3 High alloy steels (stainless steels)
2.2.3.1 Martensitic stainless steel
2.2.3.2 Ferritic stainless steel
2.2.3.3 Austenitic stainless steel
2.2.4 Cost of ferrous alloys
2.3 Nonferrous Alloys
2.3.1 Aluminum alloys
2.3.2 Copper alloys
2.3.2.1 Tempers of copper alloys
Annealed tempers
Annealed tempers specified by average grain size
Cold worked tempers
Cold worked and stress relieved tempers
As‐manufactured tempers
Heat treated tempers
Welded tube tempers
2.3.3 Nickel alloys
2.3.4 Titanium alloys
2.3.5 Zirconium alloys
2.3.6 Tantalum alloys
2.3.7 Price of nonferrous alloys
2.4 Density of Some Ferrous and Nonferrous Alloys
Example 2.1
Solution
2.5 Nonmetallic Vessels
2.6 Forms and Documentation
2.7 Miscellaneous Materials
2.7.1 Cast iron
2.7.2 Gaskets. 2.7.2.1 Gasket types
2.7.2.2 Gasket containment
Example 2.2
Solution
References
3 Layout. 3.1 Introduction
3.2 Applications
3.3 Tools and Their Use
3.4 Layout Basics
3.4.1 Projection
3.4.2 Triangulation
3.5 Material Thickness and Bending Allowance
Example 3.1
Solution
3.6 Angles and Channels
Example 3.2
Solution
3.7 Marking Conventions
3.8 Future of Plate Layout
Reference
4 Material Forming. 4.1 Introduction
4.1.1 Bending versus three‐dimensional forming
4.1.2 Other issues
4.1.3 Plastic Theory
Example 4.1
Solution
4.1.4 Forming limits
4.1.4.1 For carbon steels
4.1.4.2 For high alloy steels
4.1.4.3 For ferritic steels with tensile properties enhanced by heat treatment
4.1.4.4 Calculation of forming limits
Example 4.2
Solution
4.1.4.5 Other factors affecting formability
4.1.5 Grain direction
4.1.6 Cold versus hot forming
4.1.7 Spring back
4.2 Brake Forming (Angles, Bump‐Forming)
4.2.1 Types of dies
4.2.2 Brake work forming limits
4.2.3 Crimping
4.2.4 Bending of pipes and tubes
4.2.5 Brake forming loads
4.3 Roll Forming (Shells, Reinforcing Pads, Pipe/Tube)
4.3.1 Pyramid rolls
4.3.2 Pinch rolls
4.3.3 Two‐roll systems
4.3.4 Rolling radius variability compensation
4.3.5 Heads and caps
4.3.5.1 Press forming
4.3.5.2 Spinning
4.3.5.3 Flanging
4.3.6 Hot forming
4.4 Tolerances
4.4.1 Brake forming tolerances
4.4.1.1 Bump forming
4.4.1.2 Angle and channel forming tolerances
4.4.2 Roll forming tolerances
4.4.3 Press forming tolerances
4.4.4 Flanging tolerances
Reference
5 Fabrication. 5.1 Introduction
5.2 Layout
5.3 Weld Preparation
5.3.1 Hand and automatic grinders
5.3.2 Nibblers
5.3.3 Flame cutting
5.3.4 Boring mills
5.3.5 Lathes
5.3.6 Routers
5.3.7 Other cutter arrangements
5.4 Forming
5.5 Vessel Fit Up and Assembly
5.5.1 The fitter
5.5.2 Fit up tools
5.5.3 Persuasion and other fit up techniques
5.5.4 Fixturing
5.5.5 Welding fit up
5.5.5.1 Shell course fit up
5.5.5.2 Nozzle fit up
5.5.6 Weld shrinkage
5.5.7 Order of assembly
5.6 Welding
5.6.1 Welding position
5.6.2 Welding residual stresses
5.6.3 Welding positioners, turning rolls, column and boom weld manipulators
5.6.3.1 Welding positioners
5.6.3.2 Turning rolls
5.6.3.3 Welding manipulators
5.7 Correction of Distortion
5.8 Heat Treatment
5.8.1 Welding preheat
5.8.2 Interpass temperature
5.8.3 Post weld heat treatment
5.9 Post‐fabrication Machining
5.10 Field Fabrication – Special Issues
5.10.1 Exposure to the elements
5.10.2 Staging area
5.10.3 Tool and equipment availability
5.10.4 Staffing
5.10.5 Material handling
5.10.6 Energy sources
5.10.7 PWHT
5.10.8 Layout
5.10.9 Fit up
5.10.10 Welding
5.11 Machining
5.12 Cold Springing
6 Cutting and Machining. 6.1 Introduction
6.2 Common Cutting Operations for Pressure Vessels
6.3 Cutting Processes
6.3.1 Plate cutting. 6.3.1.1 Shearing
6.3.1.2 Flame cutting
6.3.1.3 Plasma cutting
6.3.1.4 Laser cutting
6.3.1.5 Water jet cutting
6.3.2 Pipe, bar, and structural shape cutting. 6.3.2.1 Abrasive sawing
6.3.2.2 Cold saw
6.3.2.3 Band saw
6.3.2.4 Hack saw
6.3.2.5 Torch
6.3.2.6 Laser
6.4 Common Machining Functions and Processes
6.5 Common Machining Functions for Pressure Vessels. 6.5.1 Weld preparation
6.5.2 Machining of flanges
6.5.3 Tubesheets
6.5.4 Heat exchanger channels
6.5.5 Heat exchanger baffles
6.6 Setup Issues
6.7 Material Removal Rates
6.7.1 Feed
6.7.2 Speed
6.7.3 Depth of cut
6.8 Milling
6.9 Turning and Boring
6.10 Machining Centers
6.11 Drilling
6.12 Tapping
6.13 Water Jet Cutting
6.14 Laser Machining
6.15 Reaming
6.16 Electrical Discharge Machining, Plunge and Wire
6.17 Electrochemical Machining
6.18 Electron Beam Machining
6.19 Photochemical Machining
6.20 Ultrasonic Machining
6.21 Planing and Shaping
6.22 Broaching
6.23 3D Printing
6.24 Summary
Reference
7 Welding. 7.1 Introduction
7.2 Weld Details and Symbols
7.2.1 Single fillet welds
7.2.2 Double fillet welds
7.2.3 Intermittent fillet welds
7.2.4 Single‐bevel butt welds
7.2.5 Double‐bevel butt welds
7.2.6 J‐groove or double J‐groove welds
7.2.7 Backing strips
7.2.8 Consumables
7.2.9 Tube‐to‐tubesheet welds
7.2.10 Weld symbols
7.3 Weld Processes
7.3.1 Diffusion welding (DFW) 7.3.1.1 Process
7.3.1.2 Applications
7.3.2 Electron beam welding (EBW) 7.3.2.1 Process
7.3.2.2 Applications
7.3.3 Electrogas welding (EGW) 7.3.3.1 Process
7.3.3.2 Applications
7.3.4 Electroslag welding (ESW) 7.3.4.1 Process
7.3.4.2 Applications
7.3.5 Flux‐cored arc welding (FCAW) 7.3.5.1 Process
7.3.5.2 Applications
7.3.6 Flash welding. 7.3.6.1 Process
7.3.6.2 Applications
7.3.7 Friction stir welding (FSW) 7.3.7.1 Process
7.3.7.2 Applications
7.3.8 Gas metal‐arc welding (GMAW) 7.3.8.1 Process
7.3.8.2 Applications and characteristics
7.3.9 Gas tungsten‐arc welding (GTAW) 7.3.9.1 Process
7.3.9.2 Applications
7.3.10 Laser beam welding (LBW) 7.3.10.1 Process
7.3.10.2 Applications
7.3.11 Orbital welding
7.3.11.1 Applications
7.3.12 Oxyfuel gas welding (OFW) 7.3.12.1 Process
7.3.12.2 Applications
7.3.13 Plasma‐arc welding (PAW) 7.3.13.1 Process
7.3.13.2 Applications
7.3.14 Resistance spot welding (RSW) 7.3.14.1 Process
7.3.14.2 Application
7.3.15 Resistance seam welding (RSEW) 7.3.15.1 Process
7.3.15.2 Applications
7.3.16 Submerged‐arc welding (SAW) 7.3.16.1 Process
7.3.16.2 Applications
7.3.17 Shielded metal‐arc welding (SMAW) 7.3.17.1 Process
7.3.17.2 Applications
7.3.18 Stud welding. 7.3.18.1 Process
7.3.18.2 Applications
7.4 Weld Preheat and Interpass Temperature
7.5 Post Weld Heat Treating
7.6 Welding Procedures
7.7 Control of Residual Stress and Distortion
7.8 Material Handling to Facilitate Welding
7.9 Weld Repair
7.10 Brazing
7.10.1 Applications
7.10.2 Filler metal
7.10.3 Heating
7.10.4 Flux
7.10.5 Brazing procedures
Reference
8 Welding Procedures and Post Weld Heat Treatment. 8.1 Introduction
8.2 Welding Procedures
8.3 Weld Preparation Special Requirements
8.4 Weld Joint Design and Process to Reduce Stress and Distortion
8.4.1 Reduced heat input
8.4.2 Lower temperature differential
8.4.3 Choice of weld process
8.4.4 Weld configuration and sequencing
8.5 Weld Preheat and Interpass Temperature
8.6 Welder Versus Welding Operator. 8.6.1 Welders
8.6.1.1 Manual welding
8.6.1.2 Semiautomatic arc welding
8.6.2 Welding operators
8.6.2.1 Machine welding
8.6.2.2 Automatic welding
8.6.3 Differences in qualifications
8.7 Weld Repair
8.7.1 Slag inclusion during welding
8.7.2 Surface indications after cooling of welds
8.7.3 Delayed hydrogen cracking after welding
8.7.4 Cracks occurring subsequent to PWHT
8.8 Post Weld Heat Treating
8.8.1 PWHT of carbon steels
8.8.2 PWHT of low alloy steels
8.8.3 Some general PWHT requirements for carbon steels and low alloy steels
8.8.4 PWHT of stainless steel
8.8.5 PWHT of nonferrous alloys
8.9 Cladding, Overlay, and Loose Liners
8.9.1 Cladding
8.9.2 Weld overlay
8.9.3 Loose liners
8.10 Brazing
8.10.1 Applications
8.10.2 Filler metal
8.10.3 Heating
8.10.4 Flux
8.10.5 Brazing procedures
Reference
9 Fabrication of Pressure Equipment Having Unique Characteristics. 9.1 Introduction
9.2 Heat Exchangers
9.2.1 U‐tube heat exchangers
9.2.2 Fixed heat exchangers
9.2.3 Floating head heat exchangers
9.2.4 Attachment of tubes‐to‐tubesheets and tubes‐to‐headers
9.2.5 Expansion joints
9.2.6 Assembly of heat exchangers
9.2.6.1 Bowing of tubesheets
9.2.6.2 Attachment of tubesheets to shells or channels
9.2.6.3 Rails for sliding tube bundles in shells
9.3 Dimpled Jackets
9.4 Layered Vessels. 9.4.1 Introduction
9.4.2 Fabrication of layered shells
9.5 Rectangular Vessels
9.6 Vessels with Refractory and Insulation
9.7 Vessel Supports
9.8 Summary
References
10 Surface Finishes. 10.1 Introduction
10.2 Types of Surface Finishes
10.2.1 Surface characteristics, unfinished
10.2.2 Passivation
10.2.3 Applied coatings. 10.2.3.1 Plating
10.2.3.2 Polymeric coatings
10.2.3.2.1 Paint
10.2.3.2.2 Other polymers
10.2.3.3 Thermally applied coatings
Reference
11 Handling and Transportation. 11.1 Introduction
11.2 Handling of Vessels and Vessel Components Within the Fabrication Plant
Example 11.1
Solution
11.3 Transportation of Standard Loads
11.4 Transportation of Heavy Vessels
11.4.1 Handling heavy vessels using specialty cranes
11.4.2 Shipping by truck
Example 11.2
Solution
11.4.3 Shipping by rail
Example 11.3
Solution
11.4.4 Shipping by barge or ship
Example 11.4
Solution
11.4.5 Shipping by air
11.5 Summary
12 ASME Code Compliance and Quality Control System. 12.1 Need for ASME Code Compliance
12.2 What the ASME Code Provides
12.3 Fabrication in Accordance with the ASME Code
12.4 ASME Code Stamping
12.4.1 Design calculations
12.4.2 Fabrication drawings
12.4.3 Material mill test reports
12.4.4 WPS for the vessel welds
12.4.5 Records of nondestructive (NDE) examination
12.4.6 Record of PWHT
12.4.7 Record of hydrotesting
12.4.8 Manufacturer’s Data Report, U‐1 Form
12.4.9 Manufacturer’s Partial Data Report, U‐2 form
12.4.10 Name plate
12.5 Authorized Inspector and Authorized Inspection Agency
12.6 Quality Control System for Fabrication
12.6.1 Organizational chart
12.6.2 Authority and responsibility
12.6.3 Quality control system
12.6.4 Design and drawing control
12.6.5 Material control
12.6.6 Production control
12.6.7 Inspection
12.6.8 Hydrostatic and pneumatic testing
12.6.9 Code stamping
12.6.10 Discrepancies and nonconformances
12.6.11 Welding
12.6.12 Nondestructive examination
12.6.13 Heat treatment control
12.6.14 Calibration of measuring and test equipment
12.6.15 Records retention
12.6.16 Handling, storage, and shipping
12.7 Additional Stamps Required for Pressure Vessels
12.7.1 National Board stamping, NB
12.7.2 Jurisdictional stamping
12.7.3 User stamping
12.7.4 Canadian Registration Numbers
12.8 Non‐Code Jurisdictions
12.9 Temporary Shop Locations
Reference
13 Repair of Existing Equipment. 13.1 Introduction
13.2 National Board Inspection Code, NBIC, NB‐23
13.2.1 Repairs
13.2.2 Alterations
13.2.3 Reratings
13.2.4 Post weld heat treating of repaired components
13.2.5 Hydrostatic or pneumatic testing of repaired vessels
13.3 ASME Post Construction Code, PCC‐2
13.3.1 External weld buildup to repair internal thinning
13.3.2 Full encirclement steel reinforcing sleeves for pipes in corroded areas
13.3.3 Welded hot taps
Example 13.1
Solution
13.4 API Pressure Vessel Inspection Code, API‐510
13.5 API 579/ASME FFS‐1 Fitness‐For‐Service Code
13.6 Miscellaneous Repairs
13.6.1 Removal of seized nuts
13.6.2 Structural supports and foundation
References
Appendix A Units and Conversion Factors. A.1 Some Customary Units
A.2 Conversion Factors
A.3 Length Conversions
A.4 Miscellaneous Unit Conversions
Appendix B Welding Symbols
Reference
Appendix C Weld Process Characteristics. C.1 Weld Process Advantages and Disadvantages
C.2 Weld Process Applications
Appendix D Weld Deposition
Appendix E Shape Properties. E.1 Properties of Cross Sections
E.2 Properties of Solids
E.3 Properties of Hemispheres and Spherical Segments
E.4 Properties of Commonly Used Ellipsoidal Heads
E.5 Ellipsoidal Head General Formulas
Appendix F Pipe and Tube Dimensions and Weights
Appendix G Bending and Expanding of Pipes and Tubes
G.1 TEMA Requirements for U‐Tube Thinning
Example G.1
Solution
G.2 ASME B31 Code Requirements for Tube Thickness at U‐Bends
G.2.1 Thickness of straight tubes
G.2.2 Thickness of outside of bend
G.2.3 Thickness of inside of bend
Example G.2
Solution
G.3 Expansion of Tubes into Tubesheet Holes
Example G.3
References
Appendix H Dimensions of Some Commonly Used Bolts and Their Required Minimum Spacing
Appendix I Shackles
Reference
Appendix J Shears, Moments, and Deflections of Beams. Nomenclature
Case 1. Simply supported beam – concentrated load at center
Case 2. Simply supported beam – concentrated load at any point
Case 3. Cantilever beam – concentrated load at free end
Case 4. Cantilever beam – concentrated load at any point
Case 5. Simply supported beam – uniformly distributed load
Case 6. Cantilever beam – uniformly distributed load
Case 7. Beam overhanging two supports‐uniformly distributed load
Appendix K Commonly Used Terminology. K.1 Glossary
K.2 Acronyms and Other Letter Designations
Index. a
b
c
d
e
f
g
h
i
j
k
l
m
n
o
p
q
r
s
t
u
v
w
y
z
WILEY END USER LICENSE AGREEMENT
Отрывок из книги
Fabrication of Process Equipment
.....
Robust Adaptive Control for Fractional-Order Systems with Disturbance and Saturation
Mou Chen, Shuyi Shao, and Peng Shi
.....