Hydraulic Fluid Power
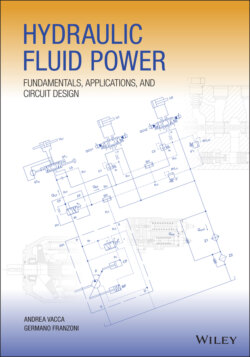
Реклама. ООО «ЛитРес», ИНН: 7719571260.
Оглавление
Andrea Vacca. Hydraulic Fluid Power
Table of Contents
List of Tables
List of Illustrations
Guide
Pages
Hydraulic Fluid Power. Fundamentals, Applications, and Circuit Design
Preface
Acknowledgments
Part I Fundamental Principles
Objectives
Chapter 1 Introduction to Hydraulic Control Technology
1.1 Historical Perspective
1.2 Fluid Power Symbology and Its Evolution
1.3 Common ISO Symbols
Example 1.1 Hydraulic schematic for a conveyor application
Solution:
Problems
2 Hydraulic Fluids
2.1 Ideal vs. Actual Hydraulic Fluids
2.2 Classification of Hydraulic Fluids
2.2.1 Mineral Oils (H)
2.2.2 Fire‐Resistant Fluids (HF)
2.2.3 Synthetic Fluids (HS)
2.2.4 Environmentally Friendly Fluids
2.2.5 Water Hydraulics
2.2.6 Comparisons Between Hydraulic Fluids
2.3 Physical Properties of Hydraulic Fluids
2.4 Fluid Compressibility: Bulk Modulus
2.5 Fluid Density
Example 2.1 Liquid compressibility
Solution:
2.6 Fluid Viscosity
2.6.1 Viscosity as a Function of Temperature
2.6.2 Viscosity as a Function of Pressure
2.7.1 Entrained Air
2.7.2 Gas Solubility
2.7.3 Equivalent Properties of Liquid–Air Mixtures
Example 2.2 Volumetric flow rate of a hydraulic pump
Solution
2.8 Contamination in Hydraulic Fluids
2.8.1 Considerations on Hydraulic Filters
Example 2.3 Solid contamination of a hydraulic oil according to the ISO Standard
Solution:
2.8.2 Filter Placement
2.9 Considerations on Hydraulic Reservoirs
2.9.1 Tank Volume
2.9.2 Basic Design of a Tank
Problems
Notes
Chapter 3 Fundamental Equations
3.1 Pascal's Law
3.2 Basic Law of Fluid Statics
3.3 Volumetric Flow Rate
3.4 Conservation of Mass
3.4.1 Application to a Hydraulic Cylinder
3.5 Bernoulli's Equation
3.5.1 Generalized Bernoulli's Equation
3.5.2 Major Losses
3.5.3 Minor Losses
3.6 Hydraulic Resistance
3.7 Stationary Modeling of Flow Networks
Example 3.1 Series and parallel hydraulic connections
Solution:
3.8 Momentum Equation
Example 3.2 Force on an elbow
Solution:
3.8.1 Flow Forces
Example 3.3 Flow force evaluation for two different valve designs
Solution:
Problems
Notes
Chapter 4 Orifice Basics
4.1 Orifice Equation
4.2 Fixed and Variable Orifices
4.3 Power Loss in Orifices
Example 4.1 Orifice Flow, Power Dissipation and Temperature Rise
Solution:
4.4 Parallel and Series Connections of Orifices
Example 4.2 Orifice Sizing
Solution:
4.5 Functions of Orifices in Hydraulic Systems
4.5.1 Orifices in Pressure and Return Lines
Example 4.3 Orifice as a Metering Element or a Compensator
Solution:
4.5.2 Orifices in Pilot Lines
Example 4.4 Leakage in a Cylinder
Solution:
Problems
Notes
Chapter 5 Dynamic Analysis of Hydraulic Systems
5.1 Pressure Build‐up Equation: Hydraulic Capacitance
Example 5.1 Simple dynamic model of a cylinder
Solution:
5.2 Fluid Inertia Equation: Hydraulic Inductance
Example 5.2 Pressure spike occurring at a cylinder end‐stop
Solution:
5.3 Modeling Flow Network: Dynamic Considerations
5.3.1 Validity of the Lumped Parameter Approach
5.3.2 Further Considerations on the Line Impedance Model
5.4 Damping Effect of Hydraulic Accumulators
Problems
References
Note
Part II Hydraulic Components
Objectives
Chapter 6 Hydrostatic Pumps and Motors
6.1 Introduction
6.2 The Ideal Case
6.3 General Operating Principle
6.4 ISO Symbols
6.5 Ideal Equations
6.6 The Real Case
6.7 Losses in Pumps and Motors
6.7.1 Fluid Compressibility
6.7.2 Internal and External Leakage
6.7.3 Friction
6.7.4 Other Types of Losses. Turbulent Losses
Churning Losses
Pressure‐Dependent Torque Loss
Incomplete Filling
6.8 Volumetric and Hydromechanical Efficiency
Example 6.1 Flow, torque and power consumption of an hydraulic pump
Solution:
6.8.1 Trends for Volumetric and Hydromechanical Efficiencies
Example 6.2 Hydraulic winch system
Solution:
6.9 Design Types
6.9.1 Swashplate‐type Axial Piston Machines
6.9.2 Bent Axis‐type Axial Piston Machines
6.9.3 Radial Piston Machines
6.9.4 Gear Machines
External Gear Machines
Internal Gear Machines
Gerotors and Orbit type machines
6.9.5 Vane‐type Machines
Problems
Notes
Chapter 7 Hydraulic Cylinders
7.1 Classification
7.2 Cylinder Analysis
Example 7.1 Supply pressure of a differential cylinder
Solution:
7.3 Ideal vs. Real Cylinder
Example 7.2 Supply pressure of two cylinders in series
Solution:
7.4 Telescopic Cylinders
7.4.1 Single Acting Telescopic Cylinder
7.4.2 Double Acting Telescopic Cylinder
Example 7.3 Double acting telescopic cylinder
Solution:
Problems
Notes
Chapter 8 Hydraulic Control Valves
8.1 Spring Basics
8.2 Check and Shuttle Valves. 8.2.1 Check Valve
8.2.2 Pilot Operated Check Valve
8.2.3 Shuttle Valve
8.3 Pressure Control Valves
8.3.1 Pressure Relief Valve
Direct Acting Pressure Relief Valve
Pilot Operated Pressure Relief Valve
8.3.2 Pressure‐reducing Valve
Direct Acting Pressure‐reducing Relieving Valve
Pilot Operated Pressure Reducing Valve
8.4 Flow Control Valves
8.4.1 Two‐way Flow Control Valve
8.4.2 Fixed Displacement Pump Circuit with a Two‐way Flow Control Valve
Example 8.1 Velocity control of a hydraulic motor
Solution:
8.4.3 Three‐way Flow Control Valve
8.4.4 Fixed Displacement Pump Circuit with a Three‐way Flow Control Valve
Example 8.2 – Flow rate of a three‐way flow control valve
Solution:
8.5 Directional Control Valves
8.5.1 Meter‐in and Meter‐out Configurations
8.5.2 Neutral Position
8.6 Servovalves
8.6.1 Characteristic of Servovalves
8.6.2 Servovalves vs. Proportional Valves
Example 8.3 Maximum power delivered by a servovalve
Solution:
Problems
Notes
Chapter 9 Hydraulic Accumulators
9.1 Accumulator Types
9.1.1 Weight‐loaded Accumulators
9.1.2 Spring‐loaded Accumulators
9.1.3 Gas‐charged Accumulators
9.1.4 Piston‐type Accumulators
9.1.5 Diaphragm‐type Accumulators
9.1.6 Bladder‐type Accumulators
9.2 Operation of Gas‐charged Accumulators
9.3 Typical Applications
9.3.1 Energy Accumulation
9.3.2 Emergency Supply
9.3.3 Energy Recuperation
9.3.4 Hydraulic Suspensions
9.3.5 Pulsation Dampening: Shock Attenuation
9.4 Equation and Sizing. 9.4.1 Accumulator as Energy Storage Device
9.4.2 Accumulator as a Dampening Device
Example 9.1 Using an accumulator to reduce the input power of a cyclic operation
Solution:
Problems
References
Note
Part III Actuator Control Concepts
Objectives
Chapter 10 Basics of Actuator Control
10.1 Control Methods: Speed, Force, and Position Control
10.2 Resistive and Overrunning Loads
10.2.1 Power Flow Depending on the Load Conditions
Problems
Note
Chapter 11 General Concepts for Controlling a Single Actuator
11.1 Supply and Control Concepts
11.2 Flow Supply – Primary Control
11.3 Flow Supply – Metering Control
11.4 Flow Supply – Secondary Control
11.5 Pressure Supply – Primary Control
11.6 Pressure Supply – Metering Control
11.7 Pressure Supply – Secondary Control
11.8 Additional Remarks
Note
Chapter 12 Regeneration with Single Rod Actuators
12.1 Basic Concept of Regeneration
Example 12.1 Supply pressure of a differential cylinder
Solution:
12.2 Actual Implementation
12.2.1 Directional Control Valve with External Regeneration Valves
12.2.2 Directional Control Valve with Regenerative Extension Position
12.2.3 Solution with Automated Selection of the Regeneration Mode
Problems
References
Part IV Metering Controls for a Single Actuator
Objectives
Chapter 13 Fundamentals of Metering Control
13.1 Basic Meter‐in and Meter‐out Control Principles
13.1.1 Meter‐in Control
Extension with Resistive Loads (DV in Position 1)
Retraction with Overrunning Loads (DV in Position 2)
13.1.2 Meter‐out Control
Extension with Resistive Loads (DV in Position 1)
Retraction with Overrunning Loads (DV in Position 2)
13.1.3 Remarks on the Meter‐in and the Meter‐out Controls
Example 13.1 Loaded meter‐out control
Solution:
Example 13.2 Analysis of meter‐in and meter‐out orifice
Solution:
13.2 Actual Metering Control Components
13.2.1 Single Spool Proportional DCVs
13.2.2 Independent Metering Control Elements
Example 13.3 Metering control of a forklift mast
Solution:
13.3 Use of Anticavitation Valves for Unloaded Meter‐out
Problems
Notes
Chapter 14 Load Holding and Counterbalance Valves
14.1 Load‐holding Valves
14.1.1 Pilot Operated Check Valve
Example 14.1 Application of a PO check valve
Solution:
14.2 Counterbalance Valves
14.2.1 Basic Operating Principle
14.2.2 CBV Architecture
Check Valve Operation
Pressure Relief Operation
Pilot Pressure Operation
14.2.3 Detailed Operation of CBV
Example 14.2 Counterbalance valve application vs. fixed orifice in the return line
Solution:
Example 14.3 Counterbalance valve application vs. relief valve in the return line
Solution:
14.2.4 Effect of the Pilot Ratio and of the Pressure Setting
Selection of CBV Parameters
14.2.5 Counterbalance Valve with Vented Spring Chambers
Problems
Notes
Chapter 15 Bleed‐off and Open Center Systems
15.1 Basic Bleed‐off and Open Center Circuits
15.2 Bleed‐off Circuit Operation
15.2.1 Energy Analysis
Example 15.1 Bleed‐off circuit to extend an actuator
Solution:
15.3 Basic Open Center System
15.3.1 Operation
15.3.2 Open Center Valve Design
15.3.3 Energy Analysis
Example 15.2 Open center system to control an actuator
Solution:
15.4 Advanced Open Center Control Architectures
15.4.1 Negative Flow Control. Basic Schematic
15.4.2 Operation
Pump Displacement Setting Mechanism
15.4.2 Positive Flow Control. Basic Schematic
Operation
Pump Displacement Setting Mechanism
15.4.3 Energy Analysis for Advanced Open Center Architectures
Problems
Notes
Chapter 16 Load Sensing Systems
16.1 Basic Load Sensing Control Concept
16.2 Load Sensing System with Fixed Displacement Pump. 16.2.1 Basic Schematic
16.2.2 Operation
16.2.3 Energy Analysis
16.2.4 Saturation Conditions
16.3 Load Sensing Valve
Example 16.1 Hydraulic winch – LS system with fixed displacement pump
Solution:
16.4 Load Sensing System with Variable Displacement Pump. 16.4.1 Basic Schematic
16.4.2 Operation
16.4.3 Energy Analysis
16.4.4 Saturation Conditions
Example 16.2 Hydraulic winch: LS system with variable displacement pump
Solution:
16.5 Load Sensing Pump
Example 16.3 Operation of a differential pressure regulator
Solution:
16.6 Load Sensing Solution with Independent Metering Valves
16.7 Electronic Load Sensing (E‐LS)
Problems
Notes
Chapter 17 Constant Pressure Systems
17.1 Constant Pressure System with Variable Displacement Pump. 17.1.1 Basic Schematic and Operation
17.1.2 Energy Analysis
17.2 Constant Pressure System with Unloader (CPU)
17.3 Constant Pressure System with Fixed Displacement Pump. 17.3.1 Basic Schematic and Operation
Accumulator Charging Control Valve
17.4 Application to Hydraulic Braking Circuits
Problems
References
Notes
Part V Metering Controls for Multiple Actuators
Objectives
Chapter 18 Basics of Multiple Actuator Systems
18.1 Actuators in Series and in Parallel
18.1.1 Series Configuration
Example 18.1 – Agricultural machine with three augers
Solution:
18.1.2 Parallel Configuration
Both Actuators Moving
Only One Actuator Moves
Example 18.2 – Fan motor in parallel with actuator
Solution:
18.2 Elimination of Load Interference in Parallel Actuators
18.2.1 Solving Load Interference Using Compensators
18.2.2 Solving Load Interference with a Volumetric Coupling
18.3 Synchronization of Parallel Actuators Through Flow Dividers
18.3.1 Spool‐type Flow Divider
18.3.2 Spool‐type Flow Divider/Combiner
18.3.3 Volumetric Flow Divider/Combiner
Example 18.3 – Flow dividers
Solution:
Problems
Note
Chapter 19 Constant Pressure Systems for Multiple Actuators
19.1 Basic Concepts for a Multi‐Actuator Constant Pressure System. 19.1.1 Basic Schematic
19.1.2 Flow Saturation
19.1.3 Energy Analysis
19.2 Complete Schematic for a Multi‐Actuator Constant Pressure System
Example 19.1 Constant pressure system
Solution:
Problems
Chapter 20 Open Center Systems for Multiple Actuators
20.1 Parallel Open Center Systems. 20.1.1 Operation
20.1.2 Energy Analysis
20.1.3 Flow Saturation
20.1.4 Considerations On the Open Center Spool Design
Opening Areas
Opening Delay (Valve Timing)
20.1.5 Load Interference in Open Center Systems
Identical Spools
Different Spools
Example 20.1 Open center parallel system for multi‐actuator
Solution:
20.2 Tandem and Series Open Center Systems
20.2.1 Tandem Configuration
20.2.2 Series Configuration
20.3 Advanced Open Center Circuit for Multiple Actuators: The Case of Excavators
Problems
Notes
Chapter 21 Load Sensing Systems for Multiple Actuators
21.1 Load Sensing Systems Without Pressure Compensation (LS) 21.1.1 Basic Circuit
21.1.2 Energy Analysis
21.1.3 Valve Implementation and Extension to More Actuators
Example 21.1 Load sensing system without pressure compensators
Solution:
21.2 Load Sensing Pressure Compensated Systems (LSPC)
21.2.1 LSPC with Pre‐compensated Valve Technology. Basic Circuit
Energy Analysis
Valve Implementation and Architecture
Example 21.2 Pre‐compensated load sensing system
Solution:
21.2.2 LSPC with Post‐Compensated Valve Technology
Basic Circuit
Energy Analysis
Valve Implementation and Architecture
Example 21.3 Post‐compensated load sensing system
Solution:
21.3 Flow Saturation and Flow Sharing in LS Systems
21.3.1 Flow Saturation with Pre‐Compensated LSPC
21.3.2 Flow Saturation with Post‐Compensated LSPC
21.4 Pre‐ vs. Post‐compensated Comparison
21.4.1 Pressure Saturation
21.4.2 Flow Saturation
21.4.3 Control Accuracy
Example 21.4 Flow saturation with LS systems
Solution:
21.5 Independent Metering Systems with Load Sensing
Problems
Notes
Chapter 22 Power Steering and Hydraulic Systems with Priority Function
22.1 Hydraulic Power Steering
22.2 Classification of Hydraulic Power Steering Systems
22.3 Hydromechanical Power Steering
22.4 Hydrostatic Power Steering
22.4.1 Hydrostatic Steering Unit Description
Example 22.1 Steering unit sizing
Solution:
22.4.2 Types of Hydrostatic Steering Units
22.5 Priority Valves
22.5.1 Priority Valve for a Fixed Displacement Flow Supply
Example 22.2 Priority valve and power beyond feature
Solution:
22.5.2 Priority Valve for Load Sensing Circuits
Problems
References
Part VI Hydrostatic Transmissions and Hydrostatic Actuators
Objectives
Chapter 23 Basics and Classifications
23.1 Hydrostatic Transmissions and Hydrostatic Actuators. 23.1.1 Basic Definitions
23.1.2 Supply Concepts Used in Hydrostatic Transmissions and Hydrostatic Actuators
23.2 Primary Units for Hydrostatic Transmissions and Hydrostatic Actuators
23.2.1 Constant Speed Prime Mover and Variable Displacement Pump
23.2.2 Variable Speed Prime Mover and Fixed Displacement Pump
23.2.3 Variable Speed Prime Mover and Variable Displacement Pump
23.3 Over‐center Variable Displacement Pump
23.4 Typical Applications
23.5 Classification Summary
Note
Chapter 24 Hydrostatic Transmissions
24.1 Main Parameters for a Hydrostatic Transmission
Example 24.1 Properties of a hydrostatic transmission
Solution:
24.2 Theoretical Layouts
24.2.1 Pump and Motor with Fixed Displacement (PFMF)
24.2.2 Variable Displacement Pump and Fixed Displacement Motor (PVMF)
24.2.3 Fixed Displacement Pump and Variable Displacement Motor (PFMV)
24.2.4 Variable Displacement Pump and Variable Displacement Motor (PVMV)
24.2.5 Variable Displacement Pump and Dual Displacement Motor (PVM2)
Example 24.2 Hydrostatic transmission layouts
Solution:
24.3 Open Circuit Hydrostatic Transmissions
24.3.1 Open Circuit HT with Flow Supply: Basic Circuit
24.3.2 Open Circuit HT with Flow Supply: Common Implementation
Open Circuit Displacement Regulator
Alternative Implementation with Electric Feedback
Open Circuit HTs with Pressure Supply
The Case of Hydrostatic Fan Drives
Example 24.3 Fan drive sizing
Solution:
24.4 Closed Circuit Hydrostatic Transmissions
24.4.1 Charge Circuit and Filtration
24.4.2 Cross‐port Pressure Relief Valves
24.4.3 Flushing Circuit
Example 24.4 Sizing the flushing circuit and the charge pump for a HT
Solution:
24.5 Closed Circuit Displacement Regulators
24.5.1 Electrohydraulic Displacement Regulator for Closed Circuit Pumps
24.5.2 Automotive Control for Closed Circuit Pumps
Conceptual Schematic
Actual Implementation
24.5.3 Electrohydraulic Displacement Regulator for Motors
Automatic Pressure Regulator for Motors
Problems
Notes
Chapter 25 Hydrostatic Transmissions Applied to Vehicle Propulsion
25.1 Basic of Vehicle Transmission
25.2 Classification for Variable Ratio Transmission Systems
25.3 Power‐split Transmissions
25.3.1 Planetary Gear Train
25.3.2 Hydromechanical Power‐split Transmission
Analysis of an Output Coupled Hydromechanical Power Split Transmission
Analysis of an Input‐coupled Hydromechanical Power‐split Transmission
25.4 Hybrid Transmissions
25.4.1 Series Hybrids
25.4.2 Parallel Hybrids
25.4.3 Series‐parallel Hybrids (or Power‐split Hybrids)
25.5 Sizing Hydrostatic Transmissions for Propel Applications
25.5.1 Step 1: Maximum Tractive Effort Calculation
25.5.2 Step 2: Fixed or Variable Displacement Motor Selection
25.5.3 Step 3: Sizing of the Motor (Secondary Unit)
Given wheel ratio
Unknown wheel ratio
25.5.4 Step 4: Sizing of the Pump (Primary Unit)
Given pump‐engine speed ratio
Unknown pump ratio
25.5.5 Step 5: Check Results
Example 25.1 Sizing a hydrostatic transmission for a small wheel loader
Solution:
Problems
Note
Chapter 26 Hydrostatic Actuators
26.1 Open Circuit Hydrostatic Actuators
26.2 Closed Circuit Hydrostatic Actuators
26.2.1 Cylinder Extension
26.2.1.1 Extension in Pumping Mode (F>F*)
26.2.1.2 Extension in Motoring Mode (F<F*)
26.2.2 Cylinder Retraction
26.2.2.1 Retraction in Motoring Mode (F>F*)
26.2.2.2 Retraction in Pumping Mode (F<F*)
26.3 Further Considerations on the Charge Pump and the Accumulator
Example 26.1 Sizing a hydrostatic actuator with accumulator circuit
Solution:
26.4 Final Remarks on Hydrostatic Actuators
Note
Chapter 27 Secondary Controlled Hydrostatic Transmissions
27.1 Basic Implementation
27.2 Secondary Control Circuit with Tachometric Pump
27.3 Secondary Control Circuit with Tachometric Pump and Internal Force Feedback
27.4 Secondary Control Circuit with Electronic Control
27.5 Multiple Actuators
Problems
References
Notes
Appendix A Prime Movers and Their Interaction with the Hydraulic Circuit
Objectives
A.1 Corner Power Method and its Limitations
A.2 Diesel Engine and its Interaction with a Hydraulic Pump
A.2.1 Diesel Engine Regulation
A.2.2 Engine Stall
A.2.3 Overrunning Loads
A.2.4 Fuel Consumption
A.3 Electric Prime Movers
A.3.1 Brushed DC Electric Motors
A.3.1.1 DC Hydraulic Power Units
Example A.1 DC power unit sizing
Solution:
A.3.2 Induction Motor (or Asynchronous Motor)
A.3.3 Synchronous Motor
A.4 Power Limitation in Hydraulic Pumps
A.4.1 Torque Limiting Using Fixed Displacement Pumps
A.4.2 Torque Limiting Using Variable Displacement Pumps
References
Note
Index. A
B
C
D
E
F
G
H
I
L
M
N
O
P
R
S
T
V
W
Z
WILEY END USER LICENSE AGREEMENT
Отрывок из книги
Andrea Vacca
Maha Fluid Power Research Center
.....
The liquid absorbs the gas from the surroundings until the saturation state is reached. As long as the gas is dissolved, it does not influence the main properties of the fluid, particularly in terms of compressibility or viscosity.
The (maximum) volume of air dissolved in the liquid can be determined by the following equation, derived from the well‐known Henry–Dalton law:
.....