Statistical Quality Control
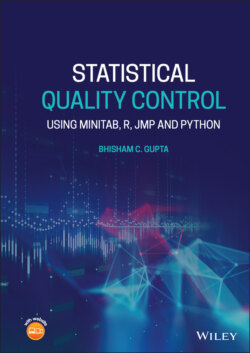
Реклама. ООО «ЛитРес», ИНН: 7719571260.
Оглавление
Bhisham C. Gupta. Statistical Quality Control
Table of Contents
List of Tables
List of Illustrations
Guide
Pages
Statistical Quality Control. Using Minitab, R, JMP, and Python
Preface
Audience
Topics Covered in This Book
Approach
Hallmark Features
Student Resources
Instructor Resources
Errata
Acknowledgments
About the Companion Website
1 Quality Improvement and Management. 1.1 Introduction
1.2 Statistical Quality Control
Definition 1.1
1.2.1 Quality and the Customer
1.2.2 Quality Improvement
1.2.3 Quality and Productivity
1.3 Implementing Quality Improvement
1.3.1 Outcomes of Quality Control
1.3.2 Quality Control and Quality Improvement
1.3.2.1 Acceptance Sampling Plans
1.3.2.2 Process Control
1.3.2.3 Removing Obstacles to Quality
1.3.2.4 Eliminating Productivity Quotas
1.3.3 Implementing Quality Improvement
1.4 Managing Quality Improvement
1.4.1 Management and Their Responsibilities
1.4.2 Management and Quality
1.4.3 Risks Associated with Making Bad Decisions
Definition 1.2
Definition 1.3
1.5 Conclusion
2 Basic Concepts of the Six Sigma Methodology. 2.1 Introduction
2.2 What Is Six Sigma?
2.2.1 Six Sigma as a Management Philosophy
2.2.2 Six Sigma as a Systemic Approach to Problem Solving
2.2.3 Six Sigma as a Statistical Standard of Quality
2.2.3.1 Statistical Basis for Six Sigma
2.2.4 Six Sigma Roles
2.3 Is Six Sigma New?
2.4 Quality Tools Used in Six Sigma
2.4.1 The Basic Seven Tools and the New Seven Tools
2.4.2 Lean Tools
2.4.2.1 Eight Wastes
2.4.2.2 Visual Management
2.4.2.3 The 5S Method
2.4.2.4 Value‐Stream Mapping
2.4.2.5 Mistake‐Proofing
2.4.2.6 Quick Changeover
2.5 Six Sigma Benefits and Criticism
2.5.1 Why Do Some Six Sigma Initiatives Fail?
Review Practice Problems
3 Describing Quantitative and Qualitative Data. 3.1 Introduction
3.2 Classification of Various Types of Data
3.3 Analyzing Data Using Graphical Tools
3.3.1 Frequency Distribution Tables for Qualitative and Quantitative Data
3.3.1.1 Qualitative Data
Example 3.1 Industrial Revenue Data with the Following Example
Solution
Example 3.2 Manufacturing Data
Solution
3.3.1.2 Quantitative Data
Example 3.3 Rod Manufacturing Data
Solution
3.4 Describing Data Graphically. 3.4.1 Dot Plots
Example 3.4 Shipment Data
Solution
3.4.2 Pie Charts
Example 3.5 Manufacturing Process
Minitab
R
3.4.3 Bar Charts
Example 3.6 Manufacturing Employee Data
Solution
Minitab
R
Example 3.7 Auto Parts Data
Solution
Example 3.8 Auto Parts Data
Solution
R
3.4.4 Histograms
Example 3.9 Fuel Pump Data
Solution
Minitab
R
3.4.5 Line Graphs
Example 3.10 Flu Vaccine Data
Solution
R
3.4.6 Measures of Association
Example 3.11 Medical Data
Solution
Minitab
R
3.5 Analyzing Data Using Numerical Tools
3.5.1 Numerical Measures
Definition 3.1
Definition 3.2
3.5.2 Measures of Centrality
3.5.2.1 Mean
Example 3.12 Hourly Wage Data
Solution
Example 3.13 Age Data
Solution
3.5.2.2 Median
Example 3.14 Rod Data
Solution
Example 3.15 Hourly Wage Data
Solution
3.5.2.3 Mode
Example 3.16
Solution
Example 3.17
Solution
Example 3.18
Solution
3.5.3 Measures of Dispersion
3.5.3.1 Range
Example 3.19
Solution
3.5.3.2 Variance
3.5.3.3 Standard Deviation
Example 3.20 Machining Data
Solution
Example 3.21
Solution
3.5.3.4 Empirical Rule
Example 3.22 Soft Drink Data
Solution
Example 3.23 Financial Data
Solution
3.5.3.5 Interquartile Range
Example 3.24 Nurse Salary Data
Solution
3.5.4 Box‐and‐Whisker Plot
Example 3.25 Noise Data
Solution
3.6 Some Important Probability Distributions
3.6.1 The Binomial Distribution
Definition 3.3
Example 3.26
Solution
3.6.1.1 Binomial Probability Tables
Definition 3.4
Example 3.27
Solution
3.6.2 The Hypergeometric Distribution
Definition 3.5
Example 3.28
Solution
Example 3.29
Solution
3.6.2.1 Mean and Standard Deviation of a Hypergeometric Distribution
Example 3.30 Computer Shipments Data
Solution
Minitab
R
3.6.3 The Poisson Distribution
Definition 3.6
Definition 3.7
Example 3.31
Solution
3.6.3.1 Mean and Standard Deviation of a Poisson Distribution
3.6.3.2 Poisson Probability Tables
Example 3.32
Solution
Minitab (Binomial Distribution)
R
Minitab (Poisson Distribution)
R
3.6.4 The Normal Distribution
Definition 3.8
Definition 3.9
Example 3.33
Solution
Example 3.34
Solution
Minitab
R
Example 3.35
Solution
Minitab
R
Review Practice Problems
4 Sampling Methods. 4.1 Introduction
4.2 Basic Concepts of Sampling
Definition 4.1
Definition 4.2
Definition 4.3
Definition 4.4
Definition 4.5
4.2.1 Introducing Various Sampling Designs
Example 4.1
Definition 4.6
Definition 4.7
Definition 4.8
4.3 Simple Random Sampling
Definition 4.9
Definition 4.10
4.3.1 Estimating the Population Mean and Population Total
Example 4.2 Steel Casting Data
Solution
Example 4.3 Manufacturing Time
Solution
4.3.2 Confidence Interval for the Population Mean and Population Total
Example 4.4
Solution
4.3.3 Determining Sample Size
Example 4.5
Solution
4.4 Stratified Random Sampling
4.4.1 Estimating the Population Mean and Population Total
4.4.2 Confidence Interval for the Population Mean and Population Total
Example 4.6 Labor Cost Data
Solution
4.4.3 Determining Sample Size
Example 4.7
Solution
4.5 Systematic Random Sampling
4.5.1 Estimating the Population Mean and Population Total
4.5.2 Confidence Interval for the Population Mean and Population Total
4.5.3 Determining the Sample Size
Example 4.8 Timber Volume Data
Solution
Example 4.9
Solution
4.6 Cluster Random Sampling
4.6.1 Estimating the Population Mean and Population Total
4.6.2 Confidence Interval for the Population Mean and Population Total
Example 4.10 Repair Cost of Hydraulic Pumps
Solution
4.6.3 Determining the Sample Size
Example 4.11
Solution
Review Practice Problems
5 Phase I Quality Control Charts for Variables. 5.1 Introduction
5.2 Basic Definition of Quality and Its Benefits
5.3 Statistical Process Control
Definition 5.1
5.3.1 Check Sheets
Example 5.1 Paper Mill Data
5.3.2 Pareto Chart
5.3.3 Cause‐and‐Effect (Fishbone or Ishikawa) Diagrams
5.3.4 Defect‐Concentration Diagrams
5.3.5 Run Charts
5.4 Control Charts for Variables
5.4.1 Process Evaluation
5.4.2 Action on the Process
5.4.3 Action on the Output
5.4.4 Variation
5.4.4.1 Common Causes (Random Causes)
5.4.4.2 Special Causes (Assignable Causes)
5.4.4.3 Local Actions and Actions on the System
5.4.4.4 Relationship Between Two Types of Variation
5.4.5 Control Charts
5.4.5.1 Preparation for Using Control Charts
5.4.5.2 Benefits of Control Charts
5.4.5.3 Rational Samples for control Charts
5.4.5.3.1 Average Run Length. Definition 5.2
Definition 5.3
Example 5.2
Solution
5.4.5.3.2 Operating Characteristic Curve (OC Curve) Definition 5.4
Definition 5.5
Definition 5.6
5.5 Shewhart and R Control Charts
5.5.1 Calculating Sample Statistics
Example 5.3
Solution
5.5.2 Calculating Control Limits
Example 5.4
Solution
Minitab
R
5.5.3 Interpreting Shewhart and R Control Charts
5.5.4 Extending the Current Control Limits for Future Control
Example 5.5
Solution
5.6 Shewhart and R Control Charts When the Process Mean and Standard Deviation are Known
R
5.7 Shewhart and R Control Charts for Individual Observations
Example 5.6
Solution
Minitab
R
5.8 Shewhart and S Control Charts with Equal Sample Sizes
Example 5.7
Solution
Minitab
R
5.9 Shewhart and S Control Charts with Variable Sample Sizes
Example 5.8 Car Manufacturing Data
Solution
Minitab
R
5.10 Process Capability
Example 5.9
Solution
Review Practice Problems
6 Phase I Control Charts for Attributes. 6.1 Introduction
6.2 Control Charts for Attributes
Definition 6.1
6.3 The p Chart: Control Charts for Nonconforming Fractions with Constant Sample Sizes
6.3.1 Control Limits for the p Control Chart
6.3.2 Interpreting the Control Chart for Nonconforming Fractions
Example 6.1 Fuel Pump Data
Solution
Minitab
R
6.4 The p Chart: Control Chart for Nonconforming Fractions with Variable Samples Sizes
Example 6.2 Fuel Pump Data
Solution
Minitab
R
6.5 The np Chart: Control Charts for the Number of Nonconforming Units
6.5.1 Control Limits for np Control Charts
Example 6.3
Minitab
R
6.6 The c Control Chart – Control Charts for Nonconformities per Sample
Example 6.4 Paper Mill Data
Solution
Minitab
R
6.7 The u Chart
Example 6.5 Printed Boards
Solution
Minitab
R
Example 6.6
Solution
Minitab
R
Review Practice Problems
7 Phase II Quality Control Charts for Detecting Small Shifts. 7.1 Introduction
7.2 Basic Concepts of CUSUM Control Charts. 7.2.1 CUSUM Control Charts vs. Shewhart and R Control Charts
Example 7.1 Medical Equipment Data
Solution
7.3 Designing a CUSUM Control Chart
7.3.1 Two‐Sided CUSUM Control Charts Using the Numerical Procedure
Example 7.2
Solution
Example 7.3
Solution
7.3.2 The Fast Initial Response (FIR) Feature for CUSUM Control Charts
Example 7.4
Solution
Example 7.5
Solution
Minitab
R
7.3.3 One‐Sided CUSUM Control Charts
7.3.4 Combined Shewhart‐CUSUM Control Charts
7.3.5 CUSUM Control Charts for Controlling Process Variability
7.4 Moving Average (MA) Control Charts
Example 7.6
Solution
Example 7.7
Solution
Minitab
R
7.5 Exponentially Weighted Moving Average (EWMA) Control Charts
Example 7.8
Solution
Minitab
R
Review Practice Problems
8 Process and Measurement System Capability Analysis. 8.1 Introduction
8.2 Development of Process Capability Indices
8.3 Various Process Capability Indices. 8.3.1 Process Capability Index: Cp
Example 8.1 Car Engine Data
Solution
Example 8.2
Solution
Example 8.3
Solution
Example 8.4
Solution
8.3.2 Process Capability Index: Cpk
8.3.3 Process Capability Index: Cpm
Example 8.5
Solution
8.3.4 Process Capability Index: Cpmk
Example 8.6
Solution
8.3.5 Process Capability Index: Cpnst
8.3.5.1 Comparing Cpnst with Cpk and Cpm. Example 8.7 Bothe (2002)
Example 8.8 Bothe (2002)
Example 8.9 Pearn et al. (1992)
8.3.5.2 Other Features of Cpnst
8.3.6 Process Performance Indices: Pp and Ppk
8.4 Pre‐control
8.4.1 Global Perspective on the Use of Pre‐control – Understanding the Color‐Coding Scheme
8.4.2 The Mechanics of Pre‐control
8.4.3 The Statistical Basis for Pre‐control
8.4.4 Advantages and Disadvantages of Pre‐control
8.4.4.1 Advantages of Pre‐control
8.4.4.2 Disadvantages of Pre‐control
8.5 Measurement System Capability Analysis
Definition 8.1
Definition 8.2
Definition 8.3
8.5.1 Evaluating Measurement System Performance
8.5.2 The Range Method
Definition 8.4
Definition 8.5
Definition 8.6
Definition 8.7
Definition 8.8
Definition 8.9
Example 8.10
Solution
8.5.3 The ANOVA Method
Minitab
R
Interpretation of Two‐Way ANOVA Table with Interaction
Interpretation of Two‐Way ANOVA Table without Interaction
8.5.4 Graphical Representation of a Gauge R&R Study
8.5.5 Another Measurement Capability Index
Review Practice Problems
9 Acceptance Sampling Plans. 9.1 Introduction
9.2 The Intent of Acceptance Sampling Plans
9.3 Sampling Inspection vs. 100% Inspection
9.4 Classification of Sampling Plans
9.4.1 Formation of Lots for Acceptance Sampling Plans
9.4.2 The Operating Characteristic (OC) Curve
Example 9.1
Solution
9.4.3 Two Types of OC Curves
9.4.4 Some Terminology Used in Sampling Plans
Example 9.2
Solution
Method
Minitab
R
9.5 Acceptance Sampling by Attributes
9.5.1 Acceptable Quality Limit (AQL)
9.5.2 Average Outgoing Quality (AOQ)
9.5.3 Average Outgoing Quality Limit (AOQL)
9.5.4 Average Total Inspection (ATI)
Example 9.3
Solution
Example 9.4
Solution
9.6 Single Sampling Plans for Attributes
9.7 Other Types of Sampling Plans for Attributes
9.7.1 Double‐Sampling Plans for Attributes
9.7.2 The OC Curve
Example 9.5
Solution
Example 9.6
Solution
9.7.3 Multiple‐Sampling Plans
9.7.4 Average Sample Number
Example 9.7
Solution
9.7.5 Sequential‐Sampling Plans
Example 9.8
Solution
9.8 ANSI/ASQ Z1.4‐2003 Sampling Standard and Plans
9.8.1 Levels of Inspection
9.8.2 Types of Sampling
Example 9.9
Solution
9.9 Dodge‐Romig Tables
9.10 ANSI/ASQ Z1.9‐2003 Acceptance Sampling Plans by Variables
9.10.1 ANSI/ASQ Z1.9‐2003 – Variability Known
9.10.2 Variability Unknown – Standard Deviation Method
Example 9.10 Operation Temperature Data
Solution
9.10.3 Variability Unknown – Range Method
Example 9.11 Electrical Resistance Data
Solution
9.11 Continuous‐Sampling Plans
9.11.1 Types of Continuous‐Sampling Plans
9.11.2 Dodge’s Continuous Sampling Plans
9.11.3 MIL‐STD‐1235B
Review Practice Problems
10 Computer Resources to Support SQC: Minitab, R, JMP, and Python. 9.1 Introduction
Appendix A. Statistical Tables
Appendix B Answers to Selected Practice Problems. Chapter 3
Chapter 4
Chapter 5
Chapter 6
Chapter 7
Chapter 8
Chapter 9
Bibliography
End Notes
Index. A
B
C
D
E
F
G
H
I
J
L
M
N
O
P
Q
R
S
T
U
V
W
Z
WILEY END USER LICENSE AGREEMENT
Отрывок из книги
Bhisham C. Gupta
.....
Hiring a consulting firm that “specializes in quality improvement” and not taking control into their own hands is the biggest mistake made by top management of any organization. Hiring a consulting firm means top management is relinquishing their responsibility for sending the important message to their employees that quality improvement is a never‐ending policy of the company.
Top management should play an important role in team building and, as much as possible, should be part of the teams. Top management and supervisors should understand the entire process of quality improvement so that they can guide their employees appropriately on how to be the team players. Teamwork can succeed only if management supports it and makes teamwork part of their new policy. Forming a team helps to achieve quality improvement, and establishing plans is essential: it is part of the job or process of managing quality improvement.
.....