Design for Excellence in Electronics Manufacturing
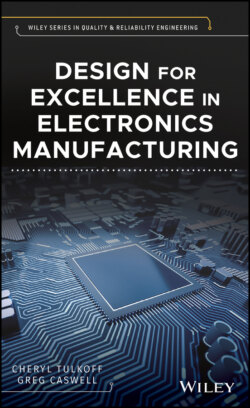
Реклама. ООО «ЛитРес», ИНН: 7719571260.
Оглавление
Cheryl Tulkoff. Design for Excellence in Electronics Manufacturing
Table of Contents
List of Tables
List of Illustrations
Guide
Pages
Series Title. Wiley Series in Quality & Reliability Engineering
Wiley Series in Quality & Reliability Engineering
Design for Excellence in Electronics Manufacturing
Contributors
List of Figures
List of Tables
Series Editor's Foreword by Dr. Andre Kleyner
Foreword
Preface
Acknowledgments
Acronyms
1 Introduction to Design for Excellence. 1.1 Design for Excellence (DfX) in Electronics Manufacturing
1.2 Chapter 2: Establishing a Reliability Program
1.3 Chapter 3: Design for Reliability (DfR)
1.4 Chapter 4: Design for the Use Environment: Reliability Testing and Test Plan Development
1.5 Chapter 5: Design for Manufacturability (DfM)
1.6 Chapter 6: Design for Sustainability
1.7 Chapter 7: Root Cause Problem‐Solving, Failure Analysis, and Continual Improvement Techniques
2 Establishing a Reliability Program
2.1 Introduction
2.2 Best Practices and the Economics of a Reliability Program
2.2.1 Best‐in‐Class Reliability Program Practices
2.3 Elements of a Reliability Program
2.3.1 Reliability Goals
2.3.2 Defined Use Environments
2.3.3 Software Reliability
2.3.4 General Software Requirements
Software Incident Reporting and Tracking
Success Testing Procedures
Functionality Requirement Verification via Dynamic Black Box Testing
User Interface Testing
Software Operational Stability Verification via Dynamic White box Testing
Software Self‐Diagnostics and Trouble Code Function Verification
Assembly, Service, and Telemetric Interface Feature Verification
Fault Tolerance and Robustness Testing
Processor Watchdog Supervisor Performance Evaluation
Fault Injection Testing
Using Stress Testing
Worst‐Case Testing
2.4 Reliability Data
2.4.1 Sources of Reliability Data
2.4.2 Reliability Data from Suppliers
2.5 Analyzing Reliability Data: Commonly Used Probability and Statistics Concepts in Reliability
2.5.1 Reliability Probability in Electronics
2.5.2 Reliability Statistics in Electronics
2.5.2.1 Basic Statistics Assumptions and Caveats
2.5.2.2 Variation Statistics
2.5.2.3 Statistical Distributions Used in Reliability. Discrete Distributions
Continuous Distributions
2.6 Reliability Analysis and Prediction Methods
Pareto Chart
MTBF
Reliability Growth Modeling
Block Diagrams
Automated Design Analysis
2.7 Summary
References
3 Design for Reliability. 3.1 Introduction
3.2 DfR and Physics of Failure
3.2.1 Failure Modes and Effects Analysis
3.2.2 Fault Tree Analysis
3.2.3 Sneak Circuit Analysis
3.2.4 DfR at the Concept Stage
3.3 Specifications (Product and Environment Definitions and Concerns)
3.4 Reliability Physics Analysis
3.4.1 Reliability Physics Alternatives
3.4.2 Reliability Physics Models and Examples
3.4.2.1 Arrhenius Equation
3.4.2.2 Eyring Equation
3.4.2.3 Black's Equation
3.4.2.4 Peck's Law
3.4.2.5 Norris‐Landzberg Equation
3.4.2.6 Creep Mechanisms
3.4.3 Component Selection
3.4.4 Critical Components
3.4.5 Moisture‐Sensitivity Level
3.4.6 Temperature‐Sensitivity Level
3.4.7 Electrostatic Discharge
3.4.8 Lifetime
3.5 Surviving the Heat Wave
3.6 Redundancy
3.7 Plating Materials: Tin Whiskers
3.8 Derating and Uprating
3.9 Reliability of New Packaging Technologies
3.10 Printed Circuit Boards
3.10.1 Surface Finishes
3.10.1.1 Organic Solderability Preservative (OSP)
3.10.1.2 Immersion Silver (ImAg)
3.10.1.3 Immersion Tin (ImSn)
3.10.1.4 Electroless Nickel Immersion Gold (ENIG)
3.10.1.5 Lead‐Free Hot Air Solder Leveled (HASL)
OSP (must address the ICT issue) is good for:
3.10.2 Laminate Selection
Let's look at those parameters in a little more depth
3.10.3 Cracking and Delamination
3.10.4 Plated Through‐Holes and Vias
3.10.5 Conductive Anodic Filament
3.10.6 Strain and Flexure Issues
3.10.7 Pad Cratering
3.10.8 PCB Buckling
3.10.9 Electrochemical Migration
3.10.9.1 Temperature
3.10.9.2 Relative Humidity
3.10.9.3 Voltage Bias
3.10.9.4 Conductor Spacing
3.10.9.5 Condensation
3.10.10 Cleanliness
3.10.10.1 Chloride
3.10.10.2 Bromide
3.10.10.3 Cations
3.10.10.4 Weak Organic Acids
3.10.10.5 Cleanliness Testing
3.11 Non‐Functional Pads
3.12 Wearout Mechanisms
3.12.1 IC Wearout
3.13 Conformal Coating and Potting
3.13.1 Silicone
3.13.2 Polyurethane
3.13.3 Epoxy
3.13.4 Acrylic
3.13.5 Superhydrophobics
References
4 Design for the Use Environment: Reliability Testing and Test Plan Development. 4.1 Introduction
4.1.1 Elements of a Testing Program
Chemical or contaminant:
Mechanical:
Electrical:
When overstress issues are detected:
4.1.2 Know the Environment
Product: Flow monitor on oil pipelines
4.2 Standards and Measurements
4.3 Failure‐Inducing Stressors
4.4 Common Test Types
4.4.1 Temperature Cycling
4.4.2 Temperature‐Humidity‐Bias Testing
4.4.3 Electrical Connection
4.4.4 Corrosion Tests. Salt Spray or Fog
Corrosive Gases
4.4.5 Power Cycling
4.4.6 Electrical Loads
4.4.7 Mechanical Bending
4.4.8 Random and Sinusoidal Vibration
4.4.9 Mechanical Shock
4.4.10 ALT Testing
4.4.11 Highly Accelerated Life Testing (HALT)
HALT:
Traditional testing:
4.4.12 EMC Testing Dos and Don'ts
4.5 Test Plan Development
4.5.1 The Process
Definitions:
4.5.2 Failure Analysis
4.5.3 Screening Tests
4.5.4 Case Study One. Industrial application:
Typical chemicals used in exposure testing:
4.5.5 Case Study Two
4.5.6 Case Study Three
References
5 Design for Manufacturability. 5.1 Introduction
5.2 Overview of Industry Standard Organizations
ANSI
IPC
Comments on IPC Class 2 vs. Class 3
JEDEC
ASTM
MIL
IEC
IEEE
UL
5.3 Overview of DfM Processes
5.3.1 The DfM Process
5.4 Component Topics
5.4.1 Part Selection
5.4.2 Moisture Sensitivity Level (MSL)
5.4.3 Temperature Sensitivity Level (TSL)
5.4.4 ESD
5.4.5 Derating
5.4.6 Ceramic Capacitor Cracks
5.4.7 Life Expectancies
5.4.8 Aluminum Electrolytic Capacitors
5.4.9 Resistors
5.4.10 Tin Whiskers
5.4.11 Integrated Circuits
5.5 Printed Circuit Board Topics
5.5.1 Laminate Selection. Discussion of Tg
5.5.2 Surface Finish
5.5.3 Discussion of Different Surface Finishes. Hot air solder leveled (HASL)
Electroless‐nickel‐immersion‐gold (ENIG)
Electroless‐nickel‐electroless‐palladium‐immersion‐gold (ENEPIG)
Immersion Silver (ImAg)
Organic Solderability Preservative (OSP)
Immersion Tin (ImSn)
5.5.4 Stackup
5.5.5 Plated Through‐Holes
5.5.6 Conductive Anodic Filament (CAF) Formation
5.5.7 Copper Weight
5.5.8 Pad Geometries
5.5.9 Trace and Space Separation
5.5.10 Non‐Functional Pads
5.5.11 Shipping and Handling
5.5.12 Cleanliness and Contamination
Section 6.1 of J‐STD‐001
5.6 Process Materials
5.6.1 Solder
5.6.2 Solder Paste
5.6.3 Flux
5.6.4 Stencils
5.6.5 Conformal Coating
Silicone
Polyurethane
Epoxy
Acrylic
Parylene
Superhydrophobic
5.6.6 Potting
5.6.7 Underfill
5.6.8 Cleaning Materials
5.6.9 Adhesives
5.7 Summary: Implementing DfM
References
6 Design for Sustainability. 6.1 Introduction
6.2 Obsolescence Management
6.2.1 Obsolescence‐Resolution Techniques. Use of Existing Stock
Reclamation of Parts
Alternate Parts
Substitute Parts
Aftermarket Parts
Lifetime Buys
Emulation
Circuit Board Redesign
6.2.1.1 Industry Standards
6.2.1.2 Asset Security
6.3 Long‐Term Storage
6.4 Long‐Term Reliability Issues
Solderability
Intermetallic Formation
Stress‐Driven Diffusive Voiding
Tin Whiskers
Moisture
Kirkendall Voiding
Summary of Failure Modes of Stored Electronic Components
6.5 Counterfeit Prevention and Detection Strategies
The Impact of Counterfeits
Counterfeit Definitions
New
Used
Refurbished
Demo
Obstacles to a Successful Anti‐Counterfeit Program
Cost‐Effective Counterfeit Protection Approach
Anti‐Counterfeit Best Practices
Primary Industry Standards
Defense Federal Acquisition Regulation Supplement (DFARS) (US Government) Requirements for Anti‐Counterfeit Programs
Counterfeit Sources
Counterfeit Reporting
Counterfeit Detection
Basic Validation Process Flow
Testing Techniques
Testing and Reporting Recommendations
Recommended Information:
Recommended Image List – As Needed:
Examples of Device‐Level Countermeasures
Mitigating Effects of Counterfeits
Anatomy of a Counterfeit Process: Steps Involved in Repackaging a Die
Conclusions
6.6 Supplier Selection
6.6.1 Selecting a Printed Circuit Board Fabricator
6.6.2 Auditing a Printed Circuit Board Fabricator
Materials and Process Audit
Planning Engineering
CAM/CAD
Documentation and Configuration Control
Certification and Training
Change Management
Fabrication Flow
Laboratory Analysis: Wet and Cross‐Section
Common PCB Defects
Shipping
Final Documentation Review
Conclusion
6.6.2.1 Selecting a Contract Manufacturer
6.6.2.2 Auditing a Contract Manufacturer
6.6.2.3 Summary
References
7 Root Cause Problem‐Solving, Failure Analysis, and Continual Improvement Techniques. 7.1 Introduction
7.1.1 Continual Improvement
7.1.2 Problem‐Solving
7.1.3 Identifying Problems and Improvement Opportunities
7.1.4 Overview of Industry Standard Organizations
ANSI
IPC
JEDEC
7.2 Root Cause Failure Analysis Methodology
7.2.1 Strategies for Selecting an Approach
7.2.2 The 5 Whys Approach
7.2.3 The Eight Disciplines (8D)
7.2.4 Shainin Red X: Diagnostic Journey
7.2.5 Six Sigma
7.2.6 Physics of Failure
7.3 Failure Reporting, Analysis, and Corrective Action System (FRACAS)
7.4 Failure Analysis
7.4.1 Failure Analysis Techniques
7.4.1.1 Visual Inspection
7.4.1.2 Electrical Characterization
7.4.1.3 Scanning Acoustic Microscopy
7.4.1.4 X‐Ray Microscopy
7.4.1.5 Thermal Imaging
7.4.1.6 SQUID Microscopy
7.4.1.7 Decapsulation
7.4.1.8 Cross‐Sectioning
7.4.1.9 Scanning Electron Microscope / Energy Dispersive X‐ray Spectroscopy (SEM/EDX)
7.4.1.10 Surface/Depth Profiling Techniques: Secondary Ion Mass Spectroscopy (SIMS), Auger
7.4.1.11 Focused Ion Beam (FIB)
7.4.1.12 Mechanical Testing: Wire Pull, Wire Shear, Solder Ball Shear, Die Shear
7.4.1.13 Fourier Transform Infra‐Red Spectroscopy FTIR
7.4.1.14 Ion Chromatography
7.4.1.15 Differential Scanning Calorimetry (DSC)
7.4.1.16 Thermomechanical Analysis / Dynamic Mechanical Analysis (DMA/TMA)
7.4.1.17 Digital Image Correlation (DIC)
7.4.1.18 Other Simple Failure Analysis Tools
7.4.2 Failure Verification
7.4.3 Corrective Action
7.4.4 Closing the Failure Report
7.5 Continuing Education and Improvement Activities
7.6 Summary: Implementing Root Cause Methodology
References
8. Conclusion to Design for Excellence: Bringing It All Together. 8.1 Design for Excellence (DfX) in Electronics Manufacturing
8.2 Chapter 2: Establishing a Reliability Program
8.3 Chapter 3: Design for Reliability (DfR)
8.4 Chapter 4: Design for the Use Environment: Reliability Testing and Test Plan Development
8.5 Chapter 5: Design for Manufacturability
8.6 Chapter 6: Design for Sustainability
8.7 Chapter 7: Root Cause Problem Solving, Failure Analysis, and Continual Improvement Techniques
Index
a
b
c
d
e
f
g
h
I
J
K
l
m
n
o
p
q
r
s
t
u
v
w
Z
WILEY END USER LICENSE AGREEMENT
Отрывок из книги
Dr. Andre Kleyner
Series Editor
.....
So, don't simply ask “Is the data accurate?” Instead, ask “Are we reasonably confident that the data presents a picture that is not significantly different from reality?”
Shedding further light on the topic of bias in scientific data and research are some foundations that have made it their mission to improve data integrity and study repeatability. Two such organizations are the Laura and John Arnold Foundation (LJAF) and the Center for Open Science (COS). The LJAF's Research Integrity Initiative seeks to improve the reliability and validity of scientific research across fields that range from governmental to philanthropy to individual decision making. The challenge is that people believe that if work is published in a journal, it is scientifically sound. That's not always true since scientific journals have a bias toward new, novel, and successful research. How often do you read great articles about failed studies?
.....