Additives for Waterborne Coatings
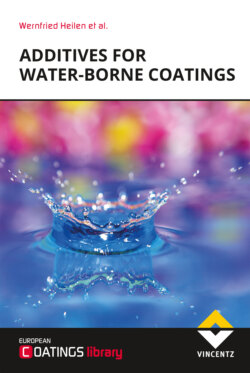
Реклама. ООО «ЛитРес», ИНН: 7719571260.
Оглавление
et al.. Additives for Waterborne Coatings
Foreword
1Introduction
1.1Literature
2Wetting and dispersing additives
2.1Modes of action
2.1.1Pigment wetting
2.1.2Grinding
2.1.3Stabilisation
2.1.3.1Electrostatic stabilisation
2.1.3.2Steric stabilisation
2.1.3.3Electrosteric stabilisation
2.1.4Influences on formulation
2.1.4.1Viscosity
2.1.4.2Colour strength
2.1.4.3Compatibility
2.1.4.4Stability
2.2Chemical structures
2.2.1Polyacrylate salts
2.2.2Polyphosphates
2.2.3Fatty acid and fatty alcohol derivatives
2.2.4Acrylic copolymers
2.2.5Maleic anhydride copolymers
2.2.6Alkyl phenol ethoxylates
2.2.7Alkyl phenol ethoxylate replacements
2.3Wetting and dispersing additives in different market segments
2.3.1Architectural coatings. 2.3.1.1Direct grind
2.3.1.2Pigment concentrates
2.3.2Wood and furniture coatings. 2.3.2.1Direct grind
2.3.2.2Pigment concentrates
2.3.3Industrial coatings. 2.3.3.1Direct grind
2.3.3.2Pigment concentrates
2.3.4Printing inks. 2.3.4.1Direct grind
2.3.4.2Pigment concentrates
2.4Tips and tricks
2.5Test methods. 2.5.1Particle size
2.5.2Colour strength
2.5.3Rub-out
2.5.4Viscosity
2.5.5Zeta potential
2.6Summary
2.7Literature
3Defoaming of coating systems
3.1Defoaming mechanisms
3.1.1Foam
3.1.1.1Causes of foam
3.1.1.2Types of foam
Liquid foams
Solid foams
Micro-foam
Macro-foam
Effect of time on foams/drainage
3.2Defoamers. 3.2.1Composition of defoamers
3.2.2Defoaming mechanisms
3.2.2.1Defoaming by drainage/slow defoaming
3.2.2.2Entry barrier/entry coefficient
3.2.2.3Bridging mechanism
3.2.2.4Spreading mechanism
3.2.2.5Bridging stretching mechanism
3.2.2.6Bridging de-wetting mechanism
3.2.2.7Spreading fluid mechanism
3.2.2.8Spreading wave mechanism
3.2.2.9Effect of fillers on the performance of defoamers
Influence on the entry barrier
Influence on bridging
3.2.2.10Summary
3.3Chemistry and formulation of defoamers. 3.3.1Active ingredients in defoamers
3.3.1.1Silicone oils (polysiloxanes)
3.3.1.2Mineral oils
3.3.1.3Vegetable oils
3.3.1.4Polar oils
3.3.1.5Molecular defoamers (gemini surfactants)
3.3.1.6Hydrophobic particles
3.3.1.7Emulsifiers
3.3.1.8Solvents
3.3.2Defoamer formulations
3.3.3Suppliers of defoamers
3.4Product recommendations for different binders
3.4.1Acrylic emulsions
3.4.2Styrene acrylic emulsions
3.4.3Vinyl acetate-based emulsions
3.4.4Polyurethane dispersions
3.5Product choice according to field of application
3.5.1Influence of the pigment volume concentration (PVC)
3.5.2Method of incorporating the defoamer
3.5.3Application of shear forces during application
3.5.4Surfactant content of the formulation
3.5.5Recommended tests for evaluating defoamers
3.6Tips and tricks
3.7Summary
3.8Literature
4Synthetic rheology modifiers
4.1General assessment of rheology modifiers
4.1.1Market overview
4.1.2Basic characteristics of rheology additives
Measuring the rheology profile of a coating system
4.1.3Main rheology modifiers
Thickeners of fossil origin
4.1.4ASE, HASE and HEUR chemistry. 4.1.4.1Synthesis of HEUR and PEPO
4.1.4.2Synthesis of ASE and HASE
4.2Requirements for rheology modifiers. 4.2.1Rheology
4.2.2Case study
4.3Ethoxylated and hydrophobic non-ionic thickeners. 4.3.1Associative properties of non-ionic additives
4.3.2From self-association to purely associative behaviour
4.3.3Associating mechanism for telechelic HEUR
4.3.4Associating mechanism of water-soluble polymers
Effect of polymer structure on the associating mechanism
4.3.5Associative behaviour of HEUR
4.3.6Mechanism of latex associativity – associative thickeners
4.4Alkali-swellable emulsions: ASEs and HASEs. 4.4.1Description
4.4.2Associative properties of HASE copolymer solutions
4.4.3ASEs
4.4.3.1Theoretical background
4.4.3.2Case study: ASE viscoelasticity
Conclusions:
4.5Influence of the latex’s characteristicson associative behaviour
4.5.1Role played by the specific surface of latex particles
4.5.2Influence of the nature of latex particle stabilisation
4.5.3Influence of the density of acid groups on particles
4.5.4Impact of particle surface energy
4.6Influence of additives in the continuous phase. 4.6.1Effect of surfactants. Modification of the particle surface
Rheological consequences
4.6.2Effect of co-solvents
4.6.3Influence of variations in the constituents of the pigment phase
4.7New trends in rheological profile requirement
4.8Literature
Acknowledgements
5Substrate wetting additives
5.1Mechanism of action. 5.1.1Water as a solvent
5.1.2 Surface tension
5.1.3Reason of the surface tension
5.1.4Effect of the high surface tension of water
5.1.5Substrate wetting additives are surfactants
5.1.6Mode of action of substrate wetting additives
5.1.7Further general properties of substrate wetting additives/side effects
5.2Chemical structure of substrate wetting additives. 5.2.1Basic properties of substrate wetting additives
5.2.2Chemical structure of substrate wetting additives important in coatings. 5.2.2.1Polyethersiloxanes
5.2.2.2Gemini surfactants
5.2.2.3Fluorosurfactants
Fluorinated polyacrylates
5.2.2.4Acetylenediols and modifications
5.2.2.5Sulfosuccinates
5.2.2.6Alkoxylated fattyalcohols
5.2.2.7Alkylphenol ethoxylates (APEO)
5.3Application of substrate wetting additives. 5.3.1Basic properties of various chemical classes
5.3.2Reduction of static surface tension
5.3.3Possible foam stabilisation
5.3.4Effective reduction in static surface tension versus flow
5.3.5Reduction of dynamic surface tension
5.3.6Which property correlates with which practical application?
5.3.6.1Craters
5.3.6.2Wetting and atomisation of spray coatings
5.3.6.3Rewettability, reprintability, recoatability
5.3.6.4Flow
5.3.6.5Spray mist uptake
5.4Use of substrate wetting additives in different market sectors
5.5Tips and tricks. 5.5.1Successful use of substrate wetting additives in coatings
5.5.2Metallic shades
5.6Test methods for measuring surface tension. 5.6.1Static surface tension
5.6.2Dynamic surface tension
5.6.3Dynamic versus static
5.6.4Further practical test methods. 5.6.4.1Wedge spray application
5.6.4.2One spray path
5.6.4.3Crater test
5.6.4.4Draw down
5.6.4.5Spray droplet uptake
5.6.5Analytical test methods
5.7Literature
6Improving performance with co-binders
6.1Preparation of co-binders
6.1.1Secondary dispersions
6.1.1.1Polyester dispersions
6.1.1.2Polyurethane dispersions
6.2Applications of co-binders. 6.2.1Co-binders for better property profiles
6.2.1.1Drying time
6.2.1.2Adhesion
6.2.1.3Hardness-flexibility balance
6.2.1.4Gloss
6.2.2Co-binders for pigment pastes
6.3Summary
6.4Literature
7Deaerators
7.1Mode of action of deaerators. 7.1.1Dissolution of micro-foam
7.1.2Rise of micro-foam bubbles in the coating film
7.1.3How to prevent micro-foam in coating films
7.1.4How deaerators combat micro-foam
7.1.4.1Deaerators promote the dissolution or formation of small micro-foam bubbles
7.1.4.2How deaerators promote the dissolution of micro-foam bubbles
7.2Chemical composition of deaerators. 7.2.1Silicone based products
7.2.2Silicone-free products
7.2.2.1Molecular defoamers
7.3Main applications according to binder systems
7.4Main applications by market segment
7.5Tips and tricks
7.6Evaluating the effectiveness of deaerators
7.6.1Test method for low to medium viscosity coating formulations
7.6.2Test method for medium to high viscosity coating formulations
7.6.3Further test methods for micro-foam
7.7Conclusion
7.8Literature
8Flow and levelling additives
8.1Mode of action
8.1.1Mode of action in water-borne systems without co-solvents
8.1.2Sagging
8.1.3Total film flow
8.1.4Mode of action in water-borne systems with co-solvents
8.1.5Mode of action in an example of a thermosetting water-borne system with co-solvents
8.1.6Surface tension gradients
8.1.7Summary
8.2Chemistry of active ingredients. 8.2.1Polyether siloxanes
8.2.2Polyacrylates
8.2.3Side effects of polyether siloxanes
8.2.4Slip
8.3Film formation
8.4Main applications by market segment. 8.4.1Industrial metal coating. 8.4.1.1Electrophoretic coating
8.4.1.2Water-borne coatings
8.4.2Industrial coatings
8.4.3Architectural coatings. 8.4.3.1Flat and semi-gloss emulsion paints
8.4.3.2High gloss emulsion paints
8.5Conclusion
8.6Test methods. 8.6.1Measurement of flow
8.6.2Measuring flow and sagging by DMA
8.6.3Measuring the surface slip properties
8.6.4Blocking resistance
8.7Literature
9Wax additives
9.1Raw material wax
9.1.1Natural waxes
9.1.1.1Waxes from renewable raw materials
9.1.1.2Waxes from fossil sources
9.1.2Semi-synthetic and synthetic waxes
9.1.2.1Semi-synthetic waxes
9.1.2.2Synthetic waxes
9.2From wax to wax additives
9.2.1Wax and water. 9.2.1.1Wax emulsions
9.2.1.2Wax dispersions
9.2.2Micronized wax additives
9.3Wax additives for the coating industry. 9.3.1Mode of action
9.3.2Coating properties. 9.3.2.1Surface protection. Mechanical resistance
Surface slip
Water repellence
Anti-blocking
9.3.2.2Gloss reduction
9.3.2.3Texture and structure
9.3.2.4Rheology control
9.4Summary
10Light stabilisers
10.1Introduction
10.2Light and photo-oxidative degradation
10.3Stabilisation options for polymers
10.3.1UV absorbers
Mode of action of UV absorbers
10.3.2Radical scavengers
10.3.2.1Antioxidants
10.3.2.2Sterically hindered amines
Basicity of HALS
Mode of action of HALS
10.4Light stabilisers
10.4.1Market overview
10.4.2Application fields and market segments
10.4.2.1Application specific product selection. Protective wood coatings
Coatings for plastics
Industrial coatings
UV curable systems
Automotive coatings (OEM)
Automotive coatings (refinish)
Recommended dose levels
10.5Conclusions
10.6Test methods and analytical determination. 10.6.1UV absorbers
10.6.2HALS
10.6.3Weathering methods and evaluation criteria
10.6.3.1Accelerated exposure tests
10.6.3.2Further evaluation criteria
10.7Literature
11In-can and dry film preservation
11.1Sustainable and effective in-can and dry film preservation
11.2In-can preservation. 11.2.1Types of active ingredients
11.2.2Selection of active ingredients for the preservation system
11.2.3Plant hygiene
11.3Dry film preservation
11.3.1Conventional dry film preservatives
11.3.2New, “old” actives
11.3.3Improvements in the ecotoxicological properties
11.4External determining factors
11.5Prospects
Literature
12Hydrophobing agents
12.1Mode of action. 12.1.1Capillary water absorption
12.1.2Hydrophobicity
12.1.3How hydrophobing agents work
12.2Chemical structures
12.2.1Linear polysiloxanes and organofunctional polysiloxanes
12.2.2Silicone resins/silicone resin emulsions
12.2.3Other hydrophobing agents
12.2.4Production of linear polysiloxanes
12.2.5Production of silicone resin emulsions
12.2.5.1Secondary emulsification process
12.2.5.2Primary emulsification process
12.3Water-borne architectural paints. 12.3.1Synthetic emulsion paints
12.3.2Silicate emulsion paints
12.3.3Emulsion paints with silicate character (SIL paints)
12.3.4Siloxane architectural paints with strong water-beading effect
12.3.5Silicone resin emulsion paints
12.4Conclusions
12.5Appendix. 12.5.1Façade protection theory according to Künzel
12.5.2Measurement of capillary water absorption (w-value)
12.5.3Water vapour diffusion (sd-value)
12.5.4Simulated dirt pick-up
12.5.5Pigment-volume concentration (PVC):
12.6Literature
13Functional silica with unique properties
Next-generation particle morphology for performance in coatings
13.1Natural versus synthetic silica
13.1.1Gas phase process: fumed silica
13.1.2Conventional wet process: precipitated silica and silica gel
13.1.3Continuous process technology for spherical precipitated silica. A new technology for old challenges
13.2Particle characteristics. 13.2.1Particle size and particle size distribution
13.2.2The significance of filler particle morphology in coatings
13.2.3Spherical precipitated filler performance in architectural paints
13.3Test methods
13.4Results
13.5Spherical precipitates and paint rheology
13.6Conclusion
13.7Literature
Authors
Stichwortverzeichnis
Отрывок из книги
Since the publication of the 1st edition of this book almost ten years ago, some areas of paint applications have seen further technological developments that have driven significant advances in the coatings industry.
In general, the use of water-borne coatings worldwide has increased by 13 % over the last six years. 92 % are used as architectural coatings, while 8 % find application in industrial coatings. The annual growth rate is expected to be 2.5 to 2.8 % for the next 3 years [1].
.....
Figure 3.7: a) Bridging of a defoamer droplet with a positive bridging coefficient, b) and c) Stretching of a defoamer bridge till collapse
The prerequisite for the bridging stretching mechanism is that the defoamer droplet is deformable. Due to their inflexible geometry hydrophobic particles cannot defoam via the bridging stretching mechanism [5] [6] [8].
.....