Product Maturity 1
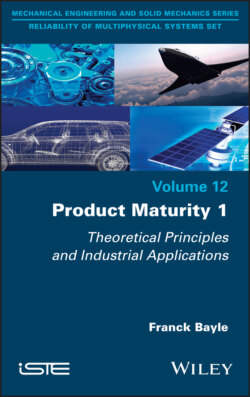
Реклама. ООО «ЛитРес», ИНН: 7719571260.
Оглавление
Franck Bayle. Product Maturity 1
Table of Contents
List of Illustrations
Tables
Guide
Pages
Product Maturity 1. Theoretical Principles and Industrial Applications
Foreword by Laurent Denis
Foreword by Serge Zaninotti
Acknowledgements
Introduction
1. Reliability Review
1.1. Failure rate
1.2. Temperature effect
1.3. Effect of maintenance
1.4. MTBF
1.5. Nature of the reliability objective
2. Maturity. 2.1. Context
2.2. Normative context and its implications. 2.2.1. Quality standards
2.2.2. Quality management system and product quality
2.2.3. Product quality and dependability
2.2.4. Product dependability and maturity. 2.2.4.1. Components and indicators
2.2.4.2. Product maturity
2.2.4.3. PDCA and product maturity
2.2.5. Standards in various domains
2.2.6. Perspectives. 2.2.6.1. Opportunity
2.2.6.2. Building a quantified product maturity indicator
2.2.6.2.1. Process risk quantified indicator
2.2.6.2.2. Product maturity quantified indicator
2.2.6.2.3. Process maturity quantified indicator
2.3. Building of maturity
2.4. Confirmation of maturity
3. Derating Analysis. 3.1. Derating
3.2. Rules provided by the manufacturers of components. 3.2.1. CMS resistors
3.2.1.1. Dissipated power. 3.2.1.1.1. Steady state
3.2.1.1.2. Transient state
3.2.1.2. Applied voltage. 3.2.1.2.1. Steady state
3.2.1.2.2. Transient state
3.2.2. Capacitors
3.2.2.1. Ceramic capacitors
3.2.2.2. Tantalum capacitors
3.2.2.2.1. Direct voltage
3.2.2.2.2. Dissipated power
3.2.2.3. Electrolytic capacitors
3.2.3. Magnetic circuits
3.2.4. Fuses
3.2.5. Resonators
3.2.6. Oscillators
3.2.7. Photocouplers
3.2.8. Diodes
3.2.9. Zener diodes
3.2.10. Tranzorb diodes
3.2.10.1. Maximum pulse power
3.2.10.2. Steady-state power
3.2.10.3. Pulse power
3.2.11. Low power bipolar transistors
3.2.12. Power bipolar transistors
3.2.13. Low power MOSFET transistors
3.2.14. High power MOSFET transistors
3.2.15. Integrated circuits
3.3. Reference-based approach
3.4. Creation of derating rules
3.4.1. Rules for constant temperature
3.4.2. Rule for voltage
3.5. Summary
4. Components with Limited Service Life
4.1. RDF 2000 guide. 4.1.1. Power transistor
4.1.2. Photocouplers
4.1.3. Switch or push button
4.1.4. Connectors
4.2. FIDES 2009 guide
4.2.1. Fans
4.2.2. Batteries
4.3. Manufacturer’s data
4.3.1. Wet electrolytic capacitor
4.3.2. Connectors
4.3.3. Relays
4.3.4. Optocouplers
4.3.5. Batteries
4.3.6. Fans
4.3.7. Flash memories
4.3.8. Potentiometers
4.3.8.1. Trimmers
4.3.8.2. Rotary potentiometers
4.3.9. Quartz oscillators
4.3.10. Voltage references
4.4. Summary of components with limited service life
5. Analysis of Product Performances
5.1. Analyses during the design stage. 5.1.1. Worst-case analysis
5.1.2. Quadratic analysis
5.1.3. Monte-Carlo analysis
5.1.3.1. Careful approach
5.1.3.2. Realistic approach
5.1.3.3. Example of the resistive bridge
5.1.4. Numerical simulations
5.2. Analyses during the manufacturing stage
6. Aggravated Tests
6.1. Definition
6.2. Objectives of aggravated tests
6.3. Principles of aggravated tests
6.3.1. Choice of physical constraints
6.3.2. Principle of HALT
6.3.3. Specific or additional constraints
6.3.4. Number of required samples
6.3.5. Operational test, diagnosis and identification of weaknesses
6.3.6. Monitoring specification
6.3.7. Instrumentation
6.3.8. Root cause analysis, corrective actions and breakdown management
6.3.8.1. Failure analyses
6.4. Robustness. 6.4.1. Estimation of robustness margins
6.4.2. Sufficient margins
6.4.2.1. The reliability objective is the probability to fulfill the mission
6.4.2.2. The reliability objective is an MTBF
7. Burn-In Test
7.1. Link between HALT and HASS tests
7.2. POS1 test
7.2.1. Miner’s approach
7.2.2. Approach according to the physical laws of failure
7.2.3. Zero-failure reliability proof approach
7.3. POS2 test
7.3.1. Influence of parameter Q
7.3.2. Influence of parameter p
7.3.3. Summary of the POS2 test
7.4. HASS cycle
7.4.1. Precipitation stage
7.4.2. Detection stage
7.5. Should burn-in tests be systematically conducted?
7.5.1. Constraints extrinsic to the equipment manufacturer
7.5.2. Constraints intrinsic to the equipment manufacturer
7.5.3. Decision criteria
7.6. Test coverage
7.7. Economic aspect of burn-in
7.7.1. No burn-in test is conducted
7.7.2. Burn-in test is conducted
8. Run-In. 8.1. Run-in principle
8.2. Stabilization
8.2.1. Proposed principle
8.2.2. Drift acceleration law
8.2.3. Choice of the drift model
8.2.4. Equivalent level of physical contribution
8.3. Expression of the corresponding degradation
8.4. Optimization of the stabilization time
8.5. Estimation of a prediction interval of the degradation
8.5.1. Principle of the stabilization method
List of Notations
List of Definitions. A
B
C
D
E
F
L
M
N
O
P
Q
R
S
T
List of Acronyms
References
Index. A, B
C, D
E, F
H, I
J, L
M, N
O, P
Q, R
S, T
V, W
WILEY END USER LICENSE AGREEMENT
Отрывок из книги
Reliability of Multiphysical Systems Set
.....
In this case, we can return to an exponential distribution because, for these values of the survival function, it is conservative, with respect to a Weibull distribution, whose shape parameter is greater than 1. Indeed, from a mathematical perspective, the ratio of the two survival functions can be calculated as follows:
with β > 1 and Tm = mission duration.
.....