Handbook of Large Hydro Generators
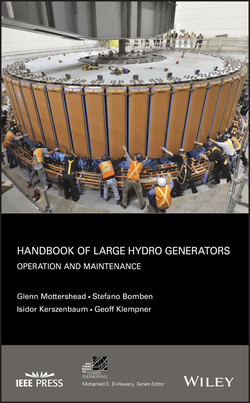
Реклама. ООО «ЛитРес», ИНН: 7719571260.
Оглавление
Geoff Klempner. Handbook of Large Hydro Generators
Table of Contents
List of Tables
List of Illustrations
Guide
Pages
HANDBOOK OF LARGE HYDRO GENERATORS. Operation and Maintenance
Preface
About the Authors
Acknowledgments
CHAPTER 1Principles of Operation of Synchronous Machines
1.1 Introduction to Basic Notions on Electric Power. 1.1.1 Magnetism and Electromagnetism
1.1.2 Electricity
1.2 ELECTRICAL–MECHANICAL EQUIVALENCE
1.3 ALTERNATING CURRENT (AC)
1.4 THREE‐PHASE CIRCUITS
1.5 BASIC PRINCIPLES OF MACHINE OPERATION
1.5.1 Faraday's Law of Electromagnetic Induction
1.5.2 Ampere–Biot–Savart's Law
1.5.3 Lenz's Law of Action and Reaction
1.5.4 Electromechanical Energy Conversion
1.6 THE SYNCHRONOUS MACHINE
1.6.1 Background
1.6.2 Principles of Construction
1.6.3 Rotor Windings
1.6.4 Stator Windings
1.7 SYNCHRONOUS MACHINE: BASIC OPERATION
1.7.1 Magnetic Representation
1.7.2 Generator Mode: Steady State Using Vectors
1.7.3 System Support: Reactive Power
1.7.4 Motor Operation
1.7.5 Equivalent Circuit
1.7.6 Machine Losses [4]
1.7.6.1 Stator Winding I2R Loss
1.7.6.2 Rotor I2R Loss
1.7.6.3 Core Loss
1.7.6.4 Stray Load Loss
1.7.6.5 Excitation System Losses
1.7.6.6 Friction and Windage Loss
1.7.6.7 Ventilating and Cooling Loss
1.8 REFERENCES
1.9 FURTHER READING
CHAPTER 2Generator Design and Construction
2.1 STATOR CORE. 2.1.1 Laminations
2.1.2 Lamination: Slot and Yoke Section
2.1.3 Core Piling (Stacking) and Clamping
2.2 STATOR FRAME
2.2.1 The Steel Box
2.2.2 The Soleplate
2.2.3 The “J or T” Hook
2.2.4 The Grout
2.3 ELECTROMAGNETICS
2.4 CORE‐END HEATING
2.5 FLUX AND ARMATURE REACTION
2.6 STATOR CORE AND FRAME FORCES
2.7 STATOR WINDINGS
2.8 STATOR WINDING WEDGES
2.9 ENDWINDING SUPPORT SYSTEMS
2.10 STATOR WINDING CONFIGURATIONS
2.11 STATOR TERMINAL CONNECTIONS
2.12 ROTOR RIM
2.13 ROTOR SPIDER/DRUM
2.14 ROTOR POLE BODY
2.15 ROTOR WINDING AND INSULATION
2.16 AMORTISSEUR WINDING
2.17 SLIP/COLLECTOR RINGS AND BRUSH GEAR
2.18 COOLING AIR
2.19 ROTOR FANS/BLOWER
2.20 ROTOR INERTIA, TORQUE, AND TORSIONAL STRESS
2.21 THRUST AND GUIDE BEARINGS. 2.21.1 Introduction
2.21.1.1 History of the Popular Kingsbury Thrust Bearing
2.21.1.2 First Application of the Pivoted Shoe Thrust Bearing
2.21.2 Important Concepts. 2.21.2.1 Oil Film and Oil Film Thickness
2.21.2.2 Loads and Load Displacement
2.21.3 Thrust Bearings
2.21.4 Thrust Bearing Pressure
2.21.5 Guide Bearings
2.21.5.1 Recommended Guide Bearing Gap and Gap Calculation
2.21.5.2 Bearing Gap Sample Calculation [9]
2.21.5.3 Bearing Insulation and Bearing Current
2.21.6 Deterioration and Failure of the Bearing Surface
2.21.6.1 Wiping Defined
2.21.6.2 Mechanism of Wiping
2.21.6.3 Classification of Wiping Damage
2.21.6.4 Appearance of Wiping
2.21.6.5 Causes of Wiping
2.21.6.6 Abrasion
2.21.6.7 Tin Oxide Damage
2.21.6.8 Overheating
2.21.6.9 Oil Starvation
2.21.6.10 Electrical Pitting
2.21.6.11 Fatigue
2.21.6.12 Cavitation
2.21.6.13 Oil
2.21.6.14 Operational Data
2.21.6.15 Upgrades and Uprates
2.22 REFERENCES
2.23 FURTHER READING
CHAPTER 3Generator Auxiliary Systems
3.1 OIL SYSTEMS
3.2 STATOR SURFACE AIR COOLING SYSTEM
3.2.1 Construction
3.2.2 Function
3.2.3 Replacement Surface Air Coolers
3.2.4 Maintenance
3.3 BEARING COOLING COILS AND WATER SUPPLY
3.4 STATOR WINDING DIRECT COOLING WATER SYSTEM
3.4.1 System Components and Functions
3.4.1.1 Centrifugal Pumps (1)
3.4.1.2 Heat Exchanger (2)
3.4.1.3 3‐Way Motor Valve (3)
3.4.1.4 Mechanical Filter and Strainer (4+5)
3.4.1.5 Expansion Tank (9)
3.4.1.6 Nitrogen Supply System (10)
3.4.1.7 Water Treatment Circuit: Ione Exchange Deionizer (11)
3.4.1.8 Water Treatment Circuit: Alkalization Unit (12)
3.5 EXCITATION SYSTEMS
3.5.1 Types of Excitation Systems
3.5.1.1 Rotating
3.6 EXCITATION SYSTEM PERFORMANCE CHARACTERISTICS
3.7 REFERENCES
CHAPTER 4Operation and Control
4.1 BASIC OPERATING PARAMETERS
4.1.1 Machine Rating
4.1.2 Apparent Power
4.1.3 Power Factor
Case 4.1
Case 4.2
4.1.4 Real Power
4.1.5 Terminal Voltage
4.1.6 Stator Current
4.1.7 Field Voltage
4.1.8 Field Current
4.1.9 Speed
4.1.10 Short Circuit Ratio
4.1.11 Volts Per Hertz
4.2 OPERATING MODES. 4.2.1 Shutdown
4.2.2 Field Applied Offline (Open Circuit)
4.2.3 Synchronized and Loaded (Online)
4.2.4 Start‐Up Operation
4.2.5 Online Operation
4.2.6 Shutdown Operation
4.3 MACHINE CURVES. 4.3.1 Open Circuit Saturation Characteristic
4.3.2 Short Circuit Characteristic
4.3.3 Capability Curves
4.3.3.1 Construction of Approximate Reactive Capability Curve
4.3.3.2 Limits Imposed by the Generator
4.3.3.3 Capability Curves Adjustments for Nonrated Terminal Voltage
4.3.4 V‐Curves
4.4 SPECIAL OPERATING CONDITIONS. 4.4.1 Unexcited Operation (“Loss‐of‐Field” Condition)
4.4.2 Negative Sequence Currents
4.4.3 Load Cycling and Repetitive Starts
4.4.4 Overloading
4.4.5 Loss of Cooling
4.4.6 Over Fluxing
4.4.7 Runaway and Overspeed
4.4.8 Loss of Lubricating Oil
4.4.9 Out‐of‐Step Synchronization and “Near” Short Circuits
4.4.10 Under and Over Frequency Operation (U/F and O/F)
4.5 BASIC OPERATION CONCEPTS. 4.5.1 Steady‐State Operation
4.5.2 Equivalent Circuit and Vector Diagram
4.5.3 Power Transfer Equation Between the Generator and the Connected System
4.5.4 Working with the Fundamental Circuit Equation
Case 4.3 Change in Excitation
Numerical Example
Case 4.4 Change in Power
4.5.5 Parallel Operation of Generators
4.5.6 Stability
4.5.6.1 Transients and Subtransients
4.5.7 Sudden Short Circuits
4.6 SYSTEM CONSIDERATIONS
4.6.1 Voltage and Frequency Variation
4.6.2 Negative Sequence Current
4.6.2.1 Calculation of Negative‐Sequence Currents
4.6.2.2 Solution
4.6.3 Over Current
4.6.4 Current Transients
4.7 GRID‐INDUCED TORSIONAL VIBRATIONS. 4.7.1 Determination of Shaft Torque and Shaft Torsional Stress
4.7.2 Material Changes Due to Torsional Vibrations
4.7.3 Types of Grid‐Induced Events
4.7.3.1 Short Circuits
4.7.3.2 Negative‐Sequence Occurrences
4.7.3.3 Out‐of‐Phase Synchronization
4.7.3.4 Out‐of‐Step Event
4.7.3.5 Load Rejection
4.8 EXCITATION AND VOLTAGE REGULATION. 4.8.1 The Exciter
4.8.2 Excitation Control. 4.8.2.1 Steady State
4.8.2.2 Transient
4.9 REFERENCES
4.10 FURTHER READING
CHAPTER 5Monitoring and Diagnostics
5.1 GENERATOR MONITORING PHILOSOPHIES
5.2 SIMPLE MONITORING WITH STATIC HIGH‐LEVEL ALARM LIMITS
5.3 DYNAMIC MONITORING WITH LOAD VARYING ALARM LIMITS
5.4 ARTIFICIAL INTELLIGENCE (AI) DIAGNOSTIC SYSTEMS
5.5 MONITORED PARAMETERS
5.5.1 Generator Electrical Parameters. 5.5.1.1 Generator Output Power
5.5.1.2 Generator Reactive Power
5.5.1.3 Three Stator Phase Currents
5.5.1.4 Stator Terminal Voltage
5.5.1.5 Field Current
5.5.1.6 Field Voltage
5.5.1.7 Frequency
5.5.1.8 Volts per Hertz
5.5.1.9 Negative Sequence
5.5.2 Stator Core and Frame. 5.5.2.1 Core Temperatures
5.5.2.2 Core Vibration
5.5.2.3 Frame Vibration
5.5.3 Stator Winding
5.5.3.1 Conductor Bar/Coil Slot Temperatures
5.5.3.2 Stator Winding Differential Temperature
5.5.3.3 Stator Surface Air Cooling Water Inlet and Outlet Temperature and Water Flow
5.5.3.4 Stator Surface Air Cooler: Hot and Cold Air Temperatures
5.5.3.5 Stator Winding Differential Pressure
5.5.3.6 Stator Endwinding Vibration Monitoring
5.5.3.7 Stator Winding Ground Alarm/Trip
5.5.3.8 Stator Winding Partial Discharge Monitoring
5.5.3.9 Vibration Sparking
5.6 RADIO FREQUENCY MONITORING
5.7 CAPACITIVE COUPLING
5.8 STATOR SLOT COUPLER
5.9 ROTOR
5.9.1.1 Rotor Winding Temperature
5.9.1.2 Pole‐face Heating
5.9.1.3 Rotor Winding Ground Alarm
5.9.1.4 Rotor Winding Shorted Turns Detection
5.9.1.5 Shaft Speed
5.9.1.6 Rotor Vibration
5.9.1.7 Torsional Vibration Monitoring
5.9.1.8 Shaft Voltage and Grounding Brush
5.9.1.9 Bearing and Oil Temperatures
5.9.1.10 Online Airgap Monitoring
5.10 EXCITATION SYSTEM. 5.10.1.1 AC Power into Exciter
5.10.1.2 DC Power Out of Exciter
5.10.1.3 Main Exciter Cooling Air Inlet Temperature
5.10.1.4 Main Exciter, Cooling Air Outlet Temperature
5.10.1.5 Sliprings and Brush Gear, Cooling Air Inlet Temperature
5.11 REFERENCES
5.12 FURTHER READING
CHAPTER 6Generator Protection. 6.1 BASIC PROTECTION PHILOSOPHY
6.1.1 Generator Protection System
6.2 IEEE DEVICE NUMBER
6.3 BRIEF DESCRIPTION OF PROTECTIVE FUNCTIONS
6.3.1 Synchronizer and Sync‐Check Relays (Functions 15 and 25)
6.3.2 Stator Ground Protection (Functions 59G and 27TH)
6.3.3 Phase Backup Protection (Functions 21 and 51VC)
6.3.4 Volts/Hertz Protection (Function 24)
6.3.5 Reverse/Forward Power Protection (Functions 32R and 32F)
6.3.6 Over/Undervoltage Protection (Functions 59 and 27)
6.3.7 Loss of Field Protection (Function 40)
6.3.8 Stator Unbalanced Current Protection (Function 46)
6.3.9 Voltage Balance Protection (Function 60)
6.3.10 Breaker Failure Protection (Function 50BF)
6.3.11 Rotor Ground Fault Protection (Function 64F)
6.3.12 Inadvertent Energization Protection (50/27)
6.3.13 Out‐of‐Step Operation (Function 78)
6.3.14 Over‐/Under‐Frequency Protection (Function 81O/U)
6.3.15 Generator Differential Protection (Function 87)
6.4 TRIPPING AND ALARMING METHODS
6.5 REFERENCES
6.6 FURTHER READING
CHAPTER 7Inspection Practices and Methodology. 7.1 SITE PREPARATION
7.1.1 Foreign Material Exclusion
7.1.2 Foreign Material Exclusion Procedures
7.2 EXPERIENCE AND TRAINING
7.2.1 Safety Procedures: Electrical Clearances
7.3 INSPECTION FREQUENCY
7.4 GENERATOR ACCESSIBILITY
7.5 INSPECTION TOOLS
7.6 INSPECTION FORMS
HYDRO GENERATOR INSPECTION AND TEST REPORT. FORM 7.1: BASIC INFORMATION
HYDRO GENERATOR INSPECTION AND TEST REPORT. FORM 7.2: MACHINE INFORMATION
HYDRO GENERATOR INSPECTION AND TEST REPORT. FORM 7.3: MACHINE ACCESSIBILITY
HYDRO GENERATOR INSPECTION AND TEST REPORT. FORM 7.4: STATOR INSPECTION ITEMS
HYDRO GENERATOR INSPECTION AND TEST REPORT. FORM 7.5: ROTOR INSPECTION ITEMS
HYDRO GENERATOR INSPECTION AND TEST REPORT. FORM 7.6: EXCITATION SYSTEM INSPECTION
HYDRO GENERATOR INSPECTION AND TEST REPORT. FORM 7.7: OTHER SYSTEMS
HYDRO GENERATOR INSPECTION AND TEST REPORT. FORM 7.8: WEDGE SURVEY
HYDRO GENERATOR INSPECTION AND TEST REPORT. FORM 7.9: ELECTRIC TEST DATA
HYDRO GENERATOR INSPECTION AND TEST REPORT. FORM 7.10: COMPREHENSIVE BRUSH ROUTINE INSPECTION
7.7 REFERENCES
CHAPTER 8Stator Inspection
8.1 STATOR FRAME SOLEPLATES
Arrangement 1
Arrangement 2
Arrangement 3
8.1.1 Frame Able to Move Freely on Soleplates or Locked Down so Frame Cannot Move
8.1.2 Dowel or Key Position (Not Twisted or Backed Out)
8.1.3 Grouting and Foundation Conditions: Cracking, Spawling, etc
8.2 STATOR FRAME: GENERAL
8.2.1 Broken or Cracked Welds on Frame Members
8.2.2 Stator Frame Splits, Alignment, Fretting, Movement
8.2.3 Stator Frame Shelves, Fretting, Broken or Cracked Welds
8.2.4 All Stator Hold‐down Bolts Set to the Correct Torque
8.2.5 Cleanliness
8.2.6 Stator Frame Overall Condition
8.3 STATOR CORE AIR DUCTS
8.3.1 I‐Beam/Vent/Duct Spacers Ability to Support Laminations, Is There Migration
8.3.2 Obstructions (Dirt, Grease, Grime) Preventing Airflow Leading to High Temperatures on Winding
8.4 STATOR CORE LAMINATIONS
8.4.1 Broken Teeth or Breaks at Keybar
8.4.2 Buckling or Wave
8.4.3 Movement of Laminations (into Airgap or Winding)
8.4.4 Looseness Using Pocket Knife
8.4.5 Core‐to‐Keybar Fretting
8.4.6 Alignment: Vertical at Core Split
8.4.7 Smearing
8.4.8 Signs of Overheating on Core‐ends or Main Core
8.4.9 Oil and Dust from Brakes or Other Dust‐like Debris
8.4.10 Fretting at Core Splits
8.4.11 Chevroning at Core Splits
8.4.12 Evidence of Arcing, Fusing, or Fretting on Core Packets
8.4.13 Flux Test Required?
8.5 STATOR CORE CLAMPING SYSTEM
8.5.1 Finger Condition
8.5.2 Core Clamping Stud/Bolt Tension
8.5.3 Core Stud or Keybar Weld on Frame
8.5.4 Free Hanging Core Stud Condition (Not Welded to Frame)
8.5.5 Circularity and Concentricity as per CEATI Standards
8.6 STATOR COILS/BARS
8.6.1 Carbonized Tracking Paths
8.6.2 Cleanliness
8.6.3 Evidence of Abrasion or Impact Damage Due to Foreign Material
8.6.4 Evidence of Girth Cracking (Bitumen Windings) at Location Where Coil/Bar Leaves the Slot
8.6.5 Semiconducting/Grading Tape or Paint Interface (White Powder)
8.6.6 Coil/Bar Puffiness (Bitumen Winding)
8.6.7 Dripping Bitumen into Generator Pit
8.6.8 Evidence of Corona Activity in Endwinding Components (White Powder)
8.6.9 Temperature Distribution Throughout the Winding
8.6.10 Water Boxes: Connections Leaking on Water or Winding Side
8.7 FLOW RESTRICTION IN WATER COOLED STATOR WINDINGS
8.7.1 Hoses, Fittings and Gaskets, in Water Cooled Stator Windings
8.7.2 Insulation Resistance (IR) Testing
8.7.3 Polarization Index (PI) Testing
8.7.4 Thermocouple/RTD Check
8.7.5 Partial Discharge (PD) Testing
8.7.6 High Potential Test per IEEE 95
8.7.7 Bypassed Coils
8.8 STATOR WEDGING SYSTEM
8.8.1 Looseness: Touch with One Finger While Tapping with the Other
8.8.2 Unacceptable Conditions: More Than 25% of Wedges Are Loose in a Slot, or Top or Bottom Wedge Is Loose
8.8.3 End Wedges Moving Out of Slot/Blocking of Ventilation Ducts
8.8.4 Slot Packing Filler Migration
8.8.5 Greasing or Powder Along the Wedge Groove
8.8.6 Mechanical Damage
8.9 STATOR ENDWINDING. 8.9.1 Evidence of Partial Discharge Activity Between Coil/Bar Endwinding (White Powder)
8.9.2 Vibration Damage‐loose Bracing
8.9.3 Vibration Probe Condition
8.9.4 Bull Ring (Surge Ring) Top and Bottom Supports in Good Condition
8.9.5 Circuit Rings: Bracing, Blocking, Lashing Tight
8.9.6 Connections: Jumpers, Series, Epoxy Filled Cap Condition – Overheating
8.10 MAIN AND NEUTRAL END LEADS, CABLES, VTS, CTS, AND INSULATORS. 8.10.1 Discoloration Due to Overheating
8.10.2 Looseness Due to Vibration
Tracking
8.10.3 Connections Tight
8.10.4 Continuity
8.10.5 Signs of Partial Discharge
8.11 REFERENCES
CHAPTER 9Rotor Inspection
9.1 ROTOR SPIDER WITH SHRUNK LAMINATED RIMS
9.1.1 Spider Arm Rim Support Shelf Fretting or Cracking: NDE Required
9.1.2 Spider (Drum Style) Support Shelf Fretting: NDE Required
9.1.3 Welds: Visual and NDE, Cracks at Welds at Start Point on Material or Along Length
9.1.4 Fretting at Shaft Coupling
9.2 ROTOR RIM. 9.2.1 Circularity, Concentricity, and Verticality as per OEM Specifications for in Service (Poles on or off Rotor)
9.2.2 Rim‐keys Fretting, Cracked Welds
9.2.3 Ventilation Duct Obstructions
9.2.4 Balance Weights Mounting: Weld or Mounting Condition
9.2.5 Fan Blades
9.3 ROTOR POLES. 9.3.1 Is Air‐gap Uniformity Safe for Operation?
9.3.2 Axial Elevation with Respect to the Stator: Within OEM Specifications
9.3.3 Physical Damage to Pole Bodies
9.3.4 Pole‐face Burning
9.3.5 Amortisseur Condition
9.3.6 Pole Collar Condition
9.3.7 Turn Insulation Migration
9.3.8 Interpole Wedging (Blocking) Condition
9.3.9 Interpole Connections: Evidence of Looseness, Cracking, or Heating
9.3.10 Pole‐keys: Fretting, Movement, Looseness
9.3.11 Pole Fixation/Attachment Cracking
9.3.12 DC Leads Condition from Slipring to Field Connections, Bolted Joints, Support Blocks, Heating
9.3.13 Field Winding Copper Resistance Test
9.3.14 Micro‐ohm Check for Connections
9.3.15 Insulation Resistance (IR) Test
9.3.16 Polarization Index (PI) Test: For Units That Have Encapsulated Field Coils Only
9.3.17 Impedance Test
9.4 ROTOR BRAKES
9.4.1 Nonuniformly Worn Shoes
9.4.2 Adjacent Track Segments Are Level Within 0.25 mm (0.010″) of Each Other
9.4.3 Runout over Entire Track
9.4.4 NDE for Cracks on Brake Track Segments
9.4.5 Blued Spots with Hard Oxide Film
9.4.6 Warping of Track, Broken or Loose Bolts
9.4.7 Broken Brake Cylinder Return Springs
9.4.8 Stuck Brakes Alarm: Brake Micro Switches
9.4.9 Operate Brakes with Unit Shut Down and Check Entire System for Leaks
9.5 REFERENCES
9.6 FURTHER READING
CHAPTER 10Auxilliaries Inspection
10.1 EXCITATION: FIELD BREAKER
10.1.1 Contact Condition and Mechanical Linkages
10.1.2 Cable or Bus Condition
10.1.3 Shunt Discoloration
10.1.4 Discharge Resistor
10.1.5 Insulation Resistance of Cable and Field Breaker
10.2 EXCITATION: STATIC EXCITER COMPONENTS
10.2.1 Thyristor Bridge Condition
10.2.2 Cooling Fans Operational
10.3 BRUSHLESS EXCITER. 10.3.1 Cleanliness
10.3.2 Diode or Thyristor Condition
10.3.3 Connections Tight
10.3.4 Cable/Bus Condition
10.3.5 Insulation Condition
10.4 STATIC EXCITER TRANSFORMER. 10.4.1 Cleanliness
10.4.2 Cables, Connections, and Bus Work
10.4.3 Insulation Resistance and Ratio Tests
10.5 EXCITATION: ROTATING EXCITERS. 10.5.1 Cleanliness Armature and Stator
10.5.2 Insulation Resistance Readings: Armature, Stator, and Interpole
10.5.3 Winding Condition: Armature, Stator, and Interpole
10.5.4 Wedging, Mounting, Banding
10.5.5 Airgap Clearance
10.5.6 Housing Condition, Cleanliness
10.5.7 Brush Neutral (Inductive Kick Test) If Exciter Has Been Removed and Replaced
10.6 EXCITATION: SLIPRINGS, COMMUTATOR, AND BRUSHES. 10.6.1 Cleanliness, Brush Replacement Frequency
10.6.2 Commutators Shows Evidence of Streaking, Threading, Grooving, Bar Edge Burning, Bar Face Burning, High Mica
10.6.3 Streaking
10.6.4 Threading
10.6.5 Grooving
10.6.6 Bar Edge Burning
10.6.7 Bar Face Burning
10.6.8 High Mica
10.6.9 Sliprings Show Evidence of Flat Spots, Burning, General Wear
10.6.10 Slipring Insulation Condition
10.6.11 Slipring Polarity Reversed Occasionally
10.6.11.1 Sliprings That Are Not Made from a Low Carbon Steel [9]
10.6.11.2 Low Carbon Steel Sliprings [9]
10.6.12 Slipring Runout <0.381 mm (0.015″)
10.6.13 Commutator Runout <0.381 mm (0.015″)
10.6.14 Commutator Mica Undercut
10.6.15 Is Grooved Chamfered on Commutator
10.6.16 Brushes and Brush Box Condition
10.6.17 Free Movement and Correct Pressure
10.6.18 Chattering, Noisy Brushes
10.6.19 Frayed Shunts
10.6.20 Springs, Cracked, Broken
10.6.21 Correct Spacing to Commutator or Slipring
10.6.22 Sparking
10.6.23 Brush Length
10.7 SURFACE AIR COOLERS. 10.7.1 Piping and Piping Support Condition
10.7.2 Leaks, Plugged Tubes, or Clogged Water Passages
10.7.3 Rated Water Flow (Test Valve Fully Open)
10.7.4 Damage to Cooler Fins or Tubes
10.7.5 Water Temperature in and Out of Coolers
10.7.6 Air Temperature in and Out of Cooler
10.8 FIRE PROTECTION. 10.8.1 Heat Activated Device (HAD)
10.8.2 Check Fire Suppression System Operation
10.8.3 Louver Test: Closing and Opening
10.9 GENERAL ITEMS. 10.9.1 Neutral Grounding Transformer, Switch, and Resistor
10.9.2 Creep Detector Operation
10.9.3 Generator Pit Heaters
10.9.4 Thermocouples/RTDs
10.9.5 Shaft Grounding Brush
10.9.6 Covers and Brackets
10.9.7 Flux or Vibration Probe Condition
10.9.8 Airgap Sensor Condition
10.9.9 Oil leaks on Piping Connections
10.10 THRUST AND GUIDE BEARING. 10.10.1 Cooling Water Flow
10.10.2 Lubricating Oil Levels
10.10.3 Bearing Temperatures: Any Significant Changes during Operation
10.10.4 External Cleanliness of the Bearing Assembly
10.10.5 Performance of the Flowmeter for the Water to the Oil Cooler
10.10.6 Verify Performance of the Water Detector (If Equipped)
10.10.7 Sample of the Bearing Oil for Analysis
10.10.8 Cleanliness of Lubricating Oil
10.10.9 Bearing Oil High/Low Level Alarms and Temperature Detector Devices
10.10.10 Thrust Bearing Bracket Foundation: Grouting Defects – Verify the Security of the Anchor Bolts and Dowels
10.10.11 Guide Bearing Clearance
10.10.12 Check the Cleanliness of the Oil: Water Heat Exchangers
10.11 MISCELLANEOUS AUXILIARIES. 10.11.1 Gauge Glasses for Cleanliness
10.11.2 High Pressure Oil Start System for Leaks, Cleanliness of the Strainer, Proper Pressure Switch Operation
10.12 REFERENCES
CHAPTER 11Maintenance and Testing
11.1 STATOR CORE MECHANICAL. 11.1.1 Core Tightness
11.1.2 Core and Frame Vibration and Testing
11.2 STATOR CORE ELECTRICAL TESTS. 11.2.1 ELCID Testing
11.2.2 ELCID Test Procedure
11.2.3 High Energy Flux Test
11.2.3.1 Design of the Magnetizing Coil
11.2.3.2 Search Coil
11.2.3.3 Calculation of the Search Coil Voltage
11.2.3.4 Calculation of the Magnetizing Coil Turns and Amperage
11.2.4 Open Circuit Saturation Curve
11.2.5 Short Circuit Saturation Curve
11.2.6 Through‐Stud Insulation Resistance
11.3 STATOR WINDING MECHANICAL TESTS. 11.3.1 Wedge Tightness
11.3.2 Stator Endwinding Vibration
11.4 STATOR WINDING ELECTRICAL TESTS. 11.4.1 Pretesting Requirements
11.4.2 Components of the Winding
11.4.2.1 Insulation Materials [4, 6]
Warning
11.4.2.2 Strand Insulation [4]
11.4.2.3 Turn Insulation [4]
11.4.2.4 Groundwall Insulation [4]
11.4.2.5 Semiconducting Slot Coating [4]
11.4.2.6 Stress Control Coating [4]
11.4.3 Stator Winding Semiconducting/Stress Control Repair
11.4.4 AC Testing
11.4.4.1 Insulation Power‐Factor Test or Dissipation Factor Test
11.4.4.2 Slot Discharge and Corona Probe Tests
11.4.4.3 Offline Partial Discharge Tests
11.4.4.4 Probing for Partial Discharge
11.4.4.5 Winding Capacitance
11.4.4.6 Discharge Inception and Extinction Voltage
11.4.5 Very Low Frequency (VLF) Testing
11.4.6 DC Testing
11.4.6.1 Components of the Measured Direct Current [12]
11.4.6.2 Characteristics of the Measured Direct Current
11.4.6.3 Winding Resistance
11.4.6.4 Insulation Resistance (IR)
11.4.6.5 Effect of Surface Condition
11.4.6.6 Effect of Moisture
11.4.6.7 Effect of Temperature
11.4.6.8 Approximating KT
11.4.6.9 Equation for “Thermoplastic” Insulation Systems
11.4.6.10 Equation for Thermosetting Insulation Systems
11.4.7 Direct Versus Alternating Voltage Testing
11.4.8 Polarization Index (PI)
11.4.8.1 Polarization Index Correction
11.4.8.2 Applicability of Polarization Index When IR Is Greater Than 5000 MΩ
11.4.8.3 Effects of Continuous Voltage Stress Control Systems
11.4.8.4 Suitability for Operation or Continued Testing
11.4.9 Stepped or Ramped Voltage Test
11.4.10 DC High Potential Test
11.4.11 AC High Potential Test
11.5 ROTOR MECHANICAL TESTING. 11.5.1 Rotor Nondestructive Examination
11.5.1.1 Visual Inspection
11.5.1.2 Radiographic
11.5.1.3 Magnetic Particle
11.5.1.4 Liquid Penetrant
11.5.1.5 Ultrasonic
11.5.1.6 Ultrasonic Pulse Echo
11.5.1.7 Through Transmission
11.5.1.8 Phased Array
11.5.1.9 Eddy Current Testing (ECT)
11.5.2 Rotor NDE Specifics
11.5.2.1 Pole Fixation/Attachment Points [17]
11.5.2.2 Spider Arm and Hub Welds
11.5.2.3 Spider Arm Support Shelves
11.5.2.4 Rotor Blower Assembly
11.5.2.5 Disks and Air Vanes
Brake Track
11.6 ROTOR ELECTRICAL TESTING. 11.6.1 Winding Resistance
11.6.2 Insulation Resistance (IR)
11.6.3 DC Overvoltage Test
11.6.4 Shorted Turns
11.6.5 Traditonal Pole Drop Test
11.6.6 Impedance Test (VIW)
11.6.7 Recurrent Surge Oscillograph (RSO) Test
11.7 BEARINGS. 11.7.1 NDE
11.7.2 Insulation Resistance
11.8 HEAT‐RUN TESTING
11.8.1 Test Procedure
11.8.2 Acceptance Parameters
11.9 REFERENCES
CHAPTER 12Maintenance Philosophies, Upgrades, and Uprates. 12.1 GENERAL MAINTENANCE PHILOSOPHIES
12.1.1 Breakdown Maintenance
12.1.2 Planned Maintenance
12.1.3 Predictive Maintenance
12.1.4 Condition‐Based Maintenance (CBM)
12.2 OPERATIONAL AND MAINTENANCE HISTORY
12.3 MAINTENANCE INTERVALS/FREQUENCY
12.4 PLANNED OUTAGES
12.4.1 Minor Outage
12.4.2 Major Outage
12.4.2.1 Repair or Replacement
12.5 REHABILITATION, UPRATING/UPGRADING AND LIFE EXTENSION
12.5.1 Homework
12.5.2 Machine Knowledge
12.5.3 Calculations
12.5.4 Things to Consider
12.5.5 Heat Run
12.5.5.1 Generator Uprating Example. What Is the Original and New Rating?
Considerations
Mechanical
Electrical
Machine Stability on the System
Protection Settings
12.5.5.2 Generator Rehabilitation/Upgrade Example (Without Uprate) Existing Machine
What Is Expected?
Turbine Runner
Brakes
Cooling Coils
Field Coil and Pole Insulation
Stator Winding
Stator Core
Excitation
Heat Run
12.6 EXCITATION SYSTEM UPGRADES
12.6.1 Static Pilot and Conventional Rotating Main Exciter
12.6.2 Static Pilot and Rotating Brushless Diode Exciter
12.6.3 Rotating Brushless Thyristor Exciter
12.6.4 Full Static Exciters
12.6.4.1 Programmable Logic Controller (PLC)
12.6.4.2 Digital Voltage Regulator
12.6.4.3 Reactive Power Controller (VAr)
12.6.4.4 Power Factor Controller (PwFact)
12.6.4.5 Particular Power System Stabilizer PSS
12.6.5 Limiters. 12.6.5.1 Volts per Hertz Limiter (V/Hz)
12.6.5.2 Time‐delayed Over‐excitation Limiter (OEL)
12.6.5.3 Instantaneous Over‐excitation Limiter (OEL inst)
12.6.5.4 Under‐excitation Limiter (UEL)
12.6.5.5 Stator Current Limiter (SCL)
12.6.6 Automatic Voltage Regulator (AVR)
12.6.7 Reactive and Active Compensation or Droop
12.6.8 Field Current Regulator (FCR)
12.6.9 Digital Measuring Transducers
12.6.10 The Power Circuit
12.6.10.1 Excitation Transformer
12.6.10.2 Thyristor Rectifier Bridge
12.6.10.3 Field Flashing Circuit
12.6.10.4 De‐Excitation Circuit
12.7 WORKFORCE
12.8 SPARE PARTS
12.8.1 Auxiliaries
12.9 EFFECT OF UPRATING ON GENERATOR LIFE. 12.9.1 Stator Winding Insulation
12.9.2 Field Winding Insulation
12.9.3 Stator Core Insulation
12.10 REQUIRED INFORMATION, TESTS AND INSPECTION PRIOR TO UPRATING/UPGRADING
12.10.1 Stator
12.10.2 Rotor
12.11 MAINTENANCE SCHEDULE AFTER UPRATING
12.12 REFERENCES
Index
IEEE Press Series on Power Engineering
WILEY END USER LICENSE AGREEMENT
Отрывок из книги
IEEE Press 445 Hoes Lane Piscataway, NJ 08854
.....
The balance between the various forms of energy in the machine will determine its efficiency and cooling requirements, as well as its critical performance and construction parameters. Figure 1.5-4 depicts the principle of energy conversion as applicable to electric rotating machines.
The rudiments of electromagnetism have been presented along with the four basic laws of physics describing the physical processes existing in any electrical machine. Therefore, it is the right time to introduce the basic synchronous machine, which, is the type of electric machine used for all large hydro turbine driven generators.
.....