Underwater Inspection and Repair for Offshore Structures
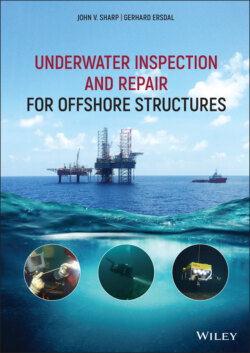
Реклама. ООО «ЛитРес», ИНН: 7719571260.
Оглавление
Gerhard Ersdal. Underwater Inspection and Repair for Offshore Structures
Table of Contents
List of Tables
List of Illustrations
Guide
Pages
Underwater Inspection and Repair for Offshore Structures
Preface
Definitions and abbreviations
1 Introduction to Underwater Inspection and Repair
1.1 Background
1.2 Why Do We Inspect and Repair Structures
1.3 Types of Offshore Structures
1.3.1 Fixed Steel Structures
1.3.2 Floating Structures
1.3.3 Concrete Platforms
1.4 Overview of this Book
1.5 Bibliographic Notes
References
Notes
2 Statutory Requirements for Inspection and Repair of Offshore Structures
2.1 Introduction
2.2 Examples of Country Statutory Requirements. 2.2.1 Introduction
2.2.2 Regulation in the US Offshore Industry
2.2.3 Regulation in the UK Offshore Industry
2.2.4 Regulation in the Norwegian Offshore Industry
2.3 Standards and Recommended Practices for Steel Structures. 2.3.1 Introduction
2.3.2 API RP‐2A and API RP‐2SIM (Structural Integrity Management)
2.3.3 API RP‐2FSIM (Floating Systems Integrity Management)
2.3.4 ISO 19902
2.3.5 ISO 19901‐9
2.3.6 NORSOK N‐005
2.4 Standards and Recommended Practices for Mooring Systems. 2.4.1 Introduction
2.4.2 API RP‐2MIM (Mooring Integrity Management)
2.4.3 IACS Guideline for Survey of Offshore Moorings
2.5 Standards and Guidance Notes for Concrete Structures. 2.5.1 Introduction
2.5.2 ISO 19903—Concrete Structures
2.5.3 Department of Energy Guidance Notes
2.5.4 NORSOK N‐005—Concrete Structures
2.6 Discussion and Summary
References
Notes
3 Damage Types in Offshore Structures
3.1 Introduction. 3.1.1 General
3.1.2 Corrosion
3.1.3 Cracking Due to Fatigue
3.1.4 Dents, Bows and Gouges Due to Impact
3.1.5 Cracking Due to Hydrogen Embrittlement
3.1.6 Erosion, Wear and Tear
3.1.7 Brittle Fracture
3.1.8 Grout Crushing and Slippage
3.2 Previous Studies on Damage to Offshore Structures
3.3 Previous Studies on Damage to Fixed Steel Structures
3.3.1 MTD Underwater Inspection of Steel Offshore Structures
3.3.2 MTD Review of Repairs to Offshore Structures and Pipelines
3.3.3 PMB AIM Project for MMS
3.3.4 HSE Study on Causes of Damage to Fixed Steel Structures
3.3.5 Single‐Sided Closure Welds
3.3.6 MSL Rationalization and Optimisation of Underwater Inspection Planning Report
3.3.7 Studies on Hurricane and Storm Damage
3.4 Previous Studies on Damage to Floating Steel Structures. 3.4.1 D.En. Studies on Semi‐Submersibles
3.4.2 SSC Review of Damage Types to Ship‐Shaped Structures
3.4.3 Defect Type for Tanker Structure Components
3.4.4 Semi‐Submersible Flooding Incident Data
3.5 Previous Studies on Damage Types to Mooring Lines and Anchors. 3.5.1 Introduction and Damage Statistics for Moorings
3.5.2 API RP‐2MIM Overview of Damage Types to Mooring Lines
3.5.3 HSE Studies on Mooring Systems
3.5.4 Studies on Corrosion of Mooring Systems
3.5.5 Studies on Fatigue of Mooring Systems
3.6 Previous Studies on Concrete Structures. 3.6.1 Concrete in the Oceans Project
3.6.2 Durability of Offshore Concrete Structures
3.6.3 PSA Study on Damage to Offshore Concrete Structures
3.7 Previous Studies on Marine Growth (Marine Fouling)
3.8 Summary of Damage and Anomalies to Offshore Structures. 3.8.1 General
3.8.2 Damage Types Specific to Steel Structures
3.8.3 Damage Types Specific to Concrete Structures
3.8.4 Summary Table of Damage to Different Types of Structures
3.9 Bibliographic Notes
References
Notes
4 Inspection Methods for Offshore Structures Underwater
4.1 Introduction to Underwater Inspection
4.2 Previous Studies on Inspection. 4.2.1 Introduction
4.2.2 SSC Survey of Non‐Destructive Test Methods
4.2.3 Underwater Inspection / Testing / Monitoring of Offshore Structures
4.2.4 HSE Handbook for Underwater Inspectors
4.2.5 MTD Underwater Inspection of Steel Offshore Structures
4.2.6 Department of Energy Fourth Edition Guidance Notes on Surveys
4.2.7 HSE Detection of Damage to Underwater Tubulars and Its Effect on Strength
4.2.8 MSL Rationalization and Optimisation of Underwater Inspection Planning Report
4.2.9 Projects on Testing of Inspection Methods and Their Reliability
4.2.10 Concrete in the Oceans Programme
4.3 Inspection and Inspection Methods. 4.3.1 Introduction
4.3.2 Visual Inspection
4.3.3 Ultrasonic Testing Methods
4.3.4 Electromagnetic Methods
4.3.5 Radiographic Testing
4.3.6 Flooded Member Detection
4.3.7 Rebound Hammer
4.3.8 Chloride Ingress Test
4.3.9 Electro‐Potential Mapping
4.3.10 Cathodic Protection Inspection
4.4 Deployment Methods. 4.4.1 Introduction
4.4.2 Divers
4.4.3 ROV and AUV
4.4.4 Splash Zone Access
4.4.5 Summary of Inspection Methods and Their Deployment
4.5 Competency of Inspection Personnel and Organisations. 4.5.1 Introduction
4.5.2 Regulatory Requirements on Competency
4.5.3 Requirements on Competency in Standards
4.5.4 Certification and Training of Inspectors
4.5.5 Trials to Study Inspector Competency
4.5.6 Organisational Competency
4.6 Reliability of Different Inspection Methods Underwater
4.7 Inspection of Fixed Steel Structures
4.8 Inspection of Concrete Structures
4.9 Inspection of Floating Structures and Mooring Systems
References
Notes
5 Structural Monitoring Methods
5.1 Introduction. 5.1.1 General
5.1.2 Historical Background
5.1.3 Requirements for Monitoring in Standards
5.2 Previous Studies on Structural Monitoring Methods
5.2.1 MTD Underwater Inspection of Steel Offshore Installations
5.2.2 HSE Review of Structural Monitoring
5.2.3 HSE Updated Review of Structural Monitoring
5.2.4 SIMoNET
5.3 Structural Monitoring Techniques. 5.3.1 Introduction
5.3.2 Acoustic Emission Technique
5.3.3 Leak Detection
5.3.4 Global Positioning Systems and Radar
5.3.5 Fatigue Gauge
5.3.6 Continuous Flooded Member Detection
5.3.7 Natural Frequency Monitoring
5.3.8 Strain Monitoring
5.3.9 Riser and Anchor Chain Monitoring
5.3.10 Acoustic Fingerprinting
5.3.11 Monitoring with Guided Waves
5.4 Structural Monitoring Case Study
5.5 Summary on Structural Monitoring
5.6 Bibliographic Notes
References
Notes
6 Inspection Planning, Programme and Data Management
6.1 Introduction. 6.1.1 General
6.1.2 Long‐Term Inspection Plan
6.1.3 Approaches for Long‐Term Inspection Planning
6.1.4 Inspection Programme
6.1.5 Integrity Data Management
6.1.6 Key Performance Indicators
6.2 Previous Studies on Long‐Term Planning of Inspections
6.2.1 PMB AIM Project for MMS
6.2.2 MSL Rationalization and Optimisation of Underwater Inspection Planning Report
6.2.3 HSE Study on the Effects of Local Joint Flexibility
6.2.4 HSE Ageing Plant Report
6.2.5 Studies on Risk‐Based and Probabilistic Inspection Planning
6.2.6 EI Guide to Risk‐Based Inspection Planning
6.3 Summary on Inspection Planning and Programme. 6.3.1 Introduction
6.3.2 Fixed Steel Platforms
6.3.3 Floating Steel Structures
6.3.4 Concrete Platforms
6.4 Bibliographic Notes
References
Note
7 Evaluation of Damage and Assessment of Structures
7.1 Introduction
7.2 Previous Studies on Evaluation of Damaged Tubulars. 7.2.1 Remaining Fatigue Life of Cracked Tubular Structures
7.2.2 Static Strength of Cracked Tubular Structures
7.2.3 Effect of Multiple Member Failure
7.2.4 Corroded Tubular Members
7.2.5 Dent and Bow Damage to Underwater Tubulars and Their Effect on Strength
7.2.6 Studies on Assessment of System Strength
7.2.7 PMB AIM Project for MMS
7.2.8 MSL Significant JIP for MMS
7.2.9 MSL Assessment of Repair Techniques for Ageing or Damaged Structures
7.3 Previous Studies on Evaluation of Damaged Plated Structures. 7.3.1 Introduction
7.3.2 SSC Studies on Residual Strength of Damaged Plated Marine Structures
7.4 Previous Studies on Evaluation of Damaged Concrete Structures. 7.4.1 Department of Energy Assessment of Major Damage to the Prestressed Concrete Tower
7.4.2 Department of Energy Review of Impact Damage Caused by Dropped Objects
7.4.3 HSE Review of Durability of Prestressing Components
7.4.4 HSE Review of Major Hazards to Concrete Platforms
7.4.5 Department of Energy Review of the Effects of Temperature Gradients
7.4.6 Concrete in the Oceans Review of Corrosion Protection of Concrete Structures
7.4.7 Norwegian Road Administration Guideline V441
7.5 Practice of Evaluation and Assessment of Offshore Structures. 7.5.1 General
7.5.2 Fixed and Floating Steel Structures
7.5.3 Concrete Structures
References
Notes
8 Repair and Mitigation of Offshore Structures
8.1 Introduction to Underwater Repair
8.2 Previous Generic Studies on Repair of Structures
8.2.1 UEG Report on Repair to North Sea Offshore Structures
8.2.2 MTD Study on Repairs of Offshore Structures
8.2.3 UK Department of Energy Fourth Edition Guidance Notes
8.2.4 DNV GL Study on Repair Methods for PSA
8.3 Previous Studies on Repair of Tubular Structures. 8.3.1 Grout Repairs to Steel Offshore Structures
8.3.2 UK Joint Industry Repairs Research Project
8.3.3 UK Department of Energy and TWI Study on Repair Methods for Fixed Offshore Structures
8.3.4 UK Department of Energy–Funded Work on Adhesive Repairs
8.3.5 Residual and Fatigue Strength of Grout‐Filled Damaged Tubular Members
8.3.6 Fatigue Life Enhancement of Tubular Joints by Grout Injection
8.3.7 ATLSS Projects on Repair to Dent‐Damaged Tubular Members
8.3.8 ATLSS Projects on Repair to Corrosion Damaged Tubulars
8.3.9 MSL Strengthening, Modification and Repair of Offshore Installations
8.3.10 MSL Underwater Structural Repairs Using Composite Materials
8.3.11 HSE Experience from the Use of Clamps Offshore
8.3.12 MSL Study on Neoprene‐Lined Clamps
8.3.13 MSL Repair Techniques for Ageing and Damaged Structures
8.3.14 MMS Studies on Hurricane Damage and Repair
8.3.15 BOEME Report on Wet Weld Repairs to US Structures
8.4 Previous Studies on Repair of Concrete Structures. 8.4.1 Introduction
8.4.2 Repair of Major Damage to Concrete Offshore Structures
8.4.3 Scaling of Underwater Concrete Repairs
8.4.4 Assessment of Materials for Repair of Damaged Concrete Underwater
8.4.5 Effectiveness of Concrete Repairs
8.5 Previous Studies on Repair of Plated Structures
8.6 Repair of Steel Structures. 8.6.1 Introduction
8.6.2 Selection of Mitigation and Repair Methods
8.6.3 Machining Methods (Grinding)
8.6.4 Re‐Melting Methods
8.6.5 Weld Residual Stress Improvement Methods (Peening)
8.6.6 Stop Holes and Crack‐Deflecting Holes
8.6.7 Structural Modifications
8.6.8 Underwater Welding
8.6.9 Doubler Plates
8.6.10 Removal of Structural Elements
8.6.11 Bonded‐Type Repairs
8.6.12 Structural Clamps and Sleeves
8.6.13 Grout Filling of Members
8.6.14 Grout Filling of Tubular Joints
8.6.15 Installation of New Structural Elements
8.6.16 Summary of Steel Repairs
8.7 Repair of Corrosion and Corrosion Protection Systems. 8.7.1 Introduction
8.7.2 Repair of Damaged Coatings
8.7.3 Replacement of Corroded Material
8.7.4 Repair or Replacement of the Corrosion Protection System
8.8 Repair of Mooring Systems
8.9 Repair of Concrete Structures. 8.9.1 Introduction
8.9.2 Choice of Repair Method
8.9.3 Concrete Material Replacement
8.9.4 Injection Methods
8.9.5 Repair of Reinforcement and Prestressing Tendons
8.9.6 Summary of Concrete Repairs
8.10 Overview of Other Mitigation Methods
8.11 Bibliographic Notes
References
Note
9 Conclusions and Future Possibilities. 9.1 Overview of the Book
9.2 Emerging Technologies
9.3 Final Thoughts
References
Index. a
b
c
d
e
f
g
h
i
j
k
l
m
n
o
p
q
r
s
t
u
v
w
WILEY END USER LICENSE AGREEMENT
Отрывок из книги
John V. Sharp
.....
Assessment was introduced in ISO 19902 (ISO 2007) as an option following engineering evaluation if anomalies identified during inspection require a more detailed analysis.
A possible outcome of the evaluation or the assessment is the implementation of prevention measures which include structural strengthening and reduction of loads on the structure or mitigation actions; these might include measures such as operational restrictions and possible de‐manning.
.....