Process Intensification and Integration for Sustainable Design
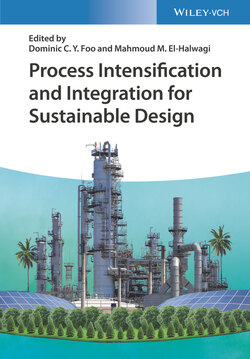
Реклама. ООО «ЛитРес», ИНН: 7719571260.
Оглавление
Группа авторов. Process Intensification and Integration for Sustainable Design
Table of Contents
List of Tables
List of Illustrations
Guide
Pages
Process Intensification and Integration for Sustainable Design
Copyright
Preface
Section 1 – Process Intensification
Section 2 – Process Integration
1 Shale Gas as an Option for the Production of Chemicals and Challenges for Process Intensification
1.1 Introduction
1.2 Where Is It Found?
1.3 Shale Gas Composition
1.4 Shale Gas Effect on Natural Gas Prices
1.5 Alternatives to Produce Chemicals from Shale Gas
1.6 Synthesis Gas
1.7 Methanol
1.8 Ethylene
1.9 Benzene
1.10 Propylene
1.11 Process Intensification Opportunities
1.12 Potential Benefits and Tradeoffs Associated with Process Intensification
1.13 Conclusions
References
2 Design and Techno‐Economic Analysis of Separation Units to Handle Feedstock Variability in Shale Gas Treatment
2.1 Introduction
2.2 Problem Statement
2.3 Methodology
2.4 Case Study
2.4.1 Data
2.4.2 Process Simulations and Economic Evaluation
2.4.2.1 Changes in Fixed and Variable Costs
2.4.2.2 Revenue
2.4.2.3 Economic Calculations
2.4.3 Safety Index Calculations
2.5 Discussion
2.5.1 Process Simulations
2.5.1.1 Dehydration Process
2.5.1.2 NGL Recovery Process
2.5.1.3 Fractionation Train
2.5.1.4 Acid Gas Removal
2.5.2 Profitability Assessment
2.5.3 High Acid Gas Case Economics
2.5.4 Safety Index Results
2.5.5 Sensitivity Analysis
2.5.5.1 Heating Value Cases
2.5.5.2 NGL Price Cases
2.6 Conclusions
Appendices
Appendix A: Key Parameters for the Dehydration Process
Appendix B: Key Parameters for the Turboexpander Process
Appendix C: Key Parameters for the Fractionation Train
Appendix D: Key Parameters for the Acid Gas Removal System
Abbreviations
References
3 Sustainable Design and Model‐Based Optimization of Hybrid RO–PRO Desalination Process
3.1 Introduction
3.2 Unit Model Description and Hybrid Process Design. 3.2.1 The Process Description
3.2.2 Unit Model and Performance Metrics. 3.2.2.1 RO Unit Model
3.2.2.2 PRO Unit Model
3.2.3 The RO–PRO Hybrid Processes
3.2.3.1 Open‐Loop Configuration
3.2.3.2 Closed‐Loop Configuration
3.3 Unified Model‐Based Analysis and Optimization
3.3.1 Dimensionless Mathematical Modeling
3.3.2 Mathematical Model and Objectives
3.3.3 Optimization Results and Comparative Analysis
3.4 Conclusion
Nomenclature. Greek Symbols
Roman Symbols
Subscripts
Abbreviations
References
4 Techno‐economic and Environmental Assessment of Ultrathin Polysulfone Membranes for Oxygen‐Enriched Combustion
4.1 Introduction
4.2 Numerical Methodology for Membrane Gas Separation Design
4.3 Methodology
4.3.1 Simulation and Elucidation of Mixed Gas Transport Properties of Ultrathin PSF Membranes (Molecular Scale)
4.3.2 Simulation of Mathematical Model Interfaced in Aspen HYSYS for Mass and Heat Balance (Mesoscale)
4.3.3 Design of Oxygen‐Enriched Combustion Using Ultrathin PSF Membranes
4.4 Results and Discussion
4.4.1 Simulation and Elucidation of Mixed Gas Transport Properties of Ultrathin PSF Membranes (Molecular)
4.4.2 Simulation of Mathematical Model Interfaced in Aspen HYSYS for Mass and Heat Balance (Mesoscale)
4.4.3 Design of Oxygen‐Enriched Combustion Using Ultrathin PSF Membranes
4.4.3.1 Membrane Area Requirement
4.4.3.2 Compressor Power Requirement
4.4.3.3 Turbine Power Requirement
4.4.3.4 Economic Parameter
4.5 Conclusion
Acknowledgment
References
5 Process Intensification of Membrane‐Based Systems for Water, Energy, and Environment Applications
5.1 Introduction
5.2 Membrane Electrocoagulation Flocculation for Dye Removal
5.3 Carbonation Bioreactor for Microalgae Cultivation
5.4 Forward Osmosis and Electrolysis for Energy Storage and Treatment of Emerging Pollutant
5.5 Conclusions and Future Perspective
List of Abbreviations and Symbols
References
6 Design of Internally Heat‐Integrated Distillation Column (HIDiC)
6.1 Introduction
6.2 Example and Conceptual Design of Conventional Column
6.3 Basic Design of HIDiC
6.4 Complete Design of HIDiC
6.4.1 Top‐Integrated Column
6.4.2 Bottom‐Integrated Column
6.4.3 Geometrical Analysis for Heat Panels
6.5 Energy Savings and Economic Evaluation
6.6 Concluding Thoughts
References
7 Graphical Analysis and Integration of Heat Exchanger Networks with Heat Pumps
7.1 Introduction
7.2 Influences of Heat Pumps on HENs
7.2.1 Case 1
7.2.2 Case 2
7.2.3 Case 3
7.2.4 Case 4
7.2.5 Case 5
7.2.6 Case 6
7.2.7 Case 7
7.3 Integration of Heat Pump Assisted Distillation in the Overall Process
7.3.1 Increase of Pinch Temperature
7.3.2 Decrease of Pinch Temperature
7.3.3 No Change in Pinch Temperature
7.3.4 Heat Pump Placement
7.4 Case Study
7.5 Conclusion
References
8 Insightful Analysis and Integration of Reactor and Heat Exchanger Network
8.1 Introduction
8.2 Influence of Temperature Variation on HEN. 8.2.1 Location of Cold and Hot Streams
8.2.2 Effect of Temperature Variation
8.3 Relation Among Reactor Parameters
8.3.1 Relation Among Temperatures, Selectivity, and Conversion of Reactor
8.3.1.1 CSTR
8.3.1.2 PFR
8.3.2 Reactor Characteristic Diagram
8.4 Coupling Optimization of HEN and Reactor
8.5 Case Study
8.6 Conclusions
References
9 Fouling Mitigation in Heat Exchanger Network Through Process Optimization
9.1 Introduction
9.2 Operation Parameter Optimization for Fouling Mitigation in HENs. 9.2.1 Description on Velocity Optimization
9.2.2 Fouling Threshold Model
9.2.3 Heat Transfer Related Models
9.2.4 Pressure Drop Related Models
9.3 Optimization of Cleaning Schedule
9.4 Application of Backup Heat Exchangers
9.5 Optimization Constraints and Objective Function. 9.5.1 Optimization Constraints
9.5.2 Objective Function
9.5.3 Optimization Algorithm
9.6 Case Studies. 9.6.1 Case Study 1: Consideration of Velocity Optimization Alone
9.6.1.1 Optimization Results
9.6.2 Case Study 2: Simultaneous Consideration of Velocity and Cleaning Schedule Optimization
9.6.2.1 Constraints for Case Study
9.6.2.2 Results and Discussion
9.6.2.3 Considering Backup Heat Exchanger
9.7 Conclusion
Acknowledgments
Nomenclature
Greek Letters
Subscripts
Superscripts
References
10 Decomposition and Implementation of Large‐Scale Interplant Heat Integration
10.1 Introduction
10.1.1 Reviews and Discussions for Stream Selection
10.1.2 Reviews and Discussions for Plant Selection
10.1.3 Reviews and Discussions for Plant Integration
10.2 Methodology. 10.2.1 Strategy 1 – Overview
10.2.2 Identification of Heat Sources/Sinks for IPHI from Individual Plants
10.2.3 Decomposition of a Large‐Scale IPHI Problem into Small‐Scale Subsections
10.2.4 Strategy 2 for Indirect IPHI
10.3 Case Study
10.3.1 Example 1
10.3.2 Example 2
10.4 Conclusion
List of Abbreviations and Symbols
References
11 Multi‐objective Optimisation of Integrated Heat, Mass and Regeneration Networks with Renewables Considering Economics and Environmental Impact
11.1 Introduction
11.2 Literature Review. 11.2.1 Regeneration in Process Synthesis
11.2.2 The Analogy of MEN and REN
11.2.3 Combined Heat and Mass Exchange Networks (CHAMENs)
11.3 Environmental Impact in Process Synthesis
11.3.1 Life Cycle Assessment
11.4 The Synthesis Method and Model Formulation
11.4.1 Synthesis Approach
11.4.2 Assumptions
11.4.3 MINLP Model Formulation
11.4.3.1 HENS Model Equations
Overall Stream Heat Balance
Stage Heat Balance
Superstructure Inlet Temperature Assignment
Temperature Feasibility
Logical Constraints
Calculation of Driving Forces
Solar Panel and Heat Storage Vessel Design Equation
11.4.3.2 MEN and REN Model Equations
Overall Mass Balance for the Rich and Lean Streams
Mass Balances for Rich and Lean Streams in Each Stage
Assignment of Target and Supply Concentrations
Feasibility of the Rich and Lean Stream Concentrations
Relaxed Binary Variable
Logical Constraints
Driving Force for Mass Exchange
11.4.3.3 The Combined Economic Objective Function. The Economic Objective Function
Environmental Objective Function
Multi‐objective Function
11.4.3.4 Initializations and Convergence
11.5 Case Study
11.5.1 H2S Removal
11.5.1.1 Synthesis of MEN (The First Step)
11.5.1.2 Simultaneous Synthesis of MEN and REN (The Second Step)
11.5.1.3 Simultaneous Synthesis of MEN, REN, and HEN (The Third Step)
11.5.1.4 Absorption and Regeneration Temperature Optimization
11.5.1.5 The Synthesis of Combined Model Using MOO
11.6 Conclusions and Future Works
References
12 Optimization of Integrated Water and Multi‐regenerator Membrane Systems Involving Multi‐contaminants: A Water‐Energy Nexus Aspect
12.1 Introduction
12.2 Problem Statement
Given:
Determine:
12.3 Model Formulation
12.3.1 Material Balances for Sources
12.3.2 Mass and Contaminants Balances for Regeneration Units
12.3.3 Mass and Contaminant Balances for Permeate and Reject Streams
12.3.4 Mass and Contaminant Balances for Sinks
12.3.5 Modeling of the Regeneration Units
12.3.5.1 Performance of Regeneration Units
12.3.6 Logical Constraints
12.3.7 The Objective Function
12.4 Illustrative Example
12.5 Conclusion
Acknowledgments
12.A Appendix: Detailed Models for the ED and RO Modules
Nomenclature. Sets
Parameters
Continuous Variables
Integer Variables
Binary Variables
References
13 Optimization Strategies for Integrating and Intensifying Housing Complexes
13.1 Introduction
13.2 Methods
13.2.1 Total Annual Cost for the Integrated System
13.2.2 Fresh Water Consumption
13.2.3 GHGE Emissions
13.2.4 Environmental Impact
13.2.5 Sustainability Return of Investment
13.2.6 Process Route Healthiness Index
13.2.7 Multistakeholder Approach
13.3 Case Study
13.4 Results
13.5 Conclusions
References
14 Sustainable Biomass Conversion Process Assessment
14.1 Introduction
14.2 Methodology and Assumptions
14.3 Results and Discussion. 14.3.1 Environmental Indicators
14.3.2 Energy Indicators
14.3.3 Efficiency Indicators
14.3.4 Economic Indicators
14.4 Conclusions
Acknowledgments
References
Index
WILEY END USER LICENSE AGREEMENT
Отрывок из книги
Edited by Dominic C. Y. Foo MahmoudM. El-Halwagi
This book is intended to provide a compilation of the various recent developments in the fields of process intensification and process integration with focus on enhancing sustainability of the chemical processes and products. It includes state‐of‐the‐art contributions by world‐renowned leaders in process intensification and integration. It strikes a balance between fundamental techniques and industrial applications. Both academic researchers and industrial practitioners will be able to use this book as a guide to optimize their respective plants and processes.
.....
Figure 2.3 Glycol dehydration process.
Figure 2.4 shows a typical NGL recovery process used in natural gas processing.
.....