Bio-Based Epoxy Polymers, Blends, and Composites
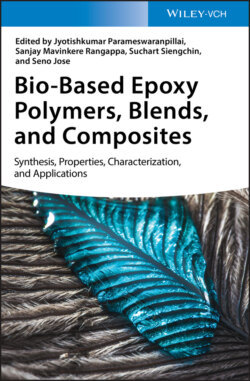
Реклама. ООО «ЛитРес», ИНН: 7719571260.
Оглавление
Группа авторов. Bio-Based Epoxy Polymers, Blends, and Composites
Table of Contents
List of Tables
List of Illustrations
Guide
Pages
Bio-Based Epoxy Polymers, Blends, and Composites. Synthesis, Properties, Characterization, and Applications
Dedication
Preface
About the Authors
1 Synthesis of Bio‐Based Epoxy Resins
1.1 Introduction
1.2 Plant Oil Bio‐Based Epoxy Resins
1.3 Substitutes for Bisphenol A Replacement. 1.3.1 Lignin‐Based Phenols
1.3.2 Vanilin
1.3.3 Cardanol
1.3.4 Isosorbide
1.3.5 Terpene Derivatives
1.4 Bio‐Based Epoxy Curing Agents
References
2 Natural/Synthetic Fiber‐Reinforced Bioepoxy Composites
2.1 Introduction
2.2 Synthetic and Natural Fibers
2.2.1 Synthetic Fibers
2.2.1.1 Organic Synthetic Fibers
2.2.1.2 Inorganic Synthetic Fibers
2.2.2 Natural Fibers
2.2.2.1 Plant‐Based Natural Fibers
2.2.2.2 Animal‐Based Natural Fibers
2.2.2.3 Mineral‐Based Natural Fibers
2.2.3 Hybrid Fiber Product
2.3 Bioepoxy
2.3.1 Natural Oil‐Based Epoxy
2.3.2 Isosorbide‐Based Epoxy (IS‐EPO)
2.3.3 Furan‐Based Epoxy
2.3.4 Polyphenolic Epoxy (Vegetable Tannins)
2.3.5 Epoxidized Natural Rubber (ENR)
2.3.6 Lignin‐Based Epoxy
2.3.7 Rosin‐Based Epoxy
2.4 Fiber‐Reinforced Bioepoxy Composites. 2.4.1 Synthetic Fiber‐Reinforced Bioepoxy Composites
2.4.2 Natural Fiber‐Reinforced Bioepoxy Composites
2.4.3 Natural–Synthetic Hybrid Fiber‐Reinforced Bioepoxy Composites
2.5 Future Perspectives
2.6 Conclusions
Acknowledgments
References
3 Polymer Blends Based on Bioepoxy Polymers
3.1 Introduction
3.2 Plant Oils. 3.2.1 Chemical and Physical Properties of Plant Oils
3.2.2 Chemical Modification of Plant Oils
3.3 Preparation of Bioepoxy Polymer Blends with Epoxy Resins
3.3.1 Castor Oil‐Based Bioepoxy Polymer Blend
3.3.2 Soybean Oil‐Based Bioepoxy Thermoset Polymer Blend
3.3.3 Linseed Oil‐Based Bioepoxy Thermoset Polymer Blend
3.3.4 Palm Oil‐Based Bioepoxy Thermoset Polymer Blend
3.4 Application of Bioepoxy Polymer Blends. 3.4.1 Paints and Coatings
3.4.2 Adhesives
3.4.3 Aerospace Industry
3.4.4 Electric Industry
3.5 Conclusion
References
4 Cure Kinetics of Bio‐epoxy Polymers, Their Blends, and Composites
4.1 Introduction
4.2 Fundamentals of Curing Reaction Kinetics
4.2.1 Curing Kinetic Theories: Isothermal and Non‐isothermal
4.3 Curing of Bio‐thermosets. 4.3.1 Curing Agents and Curing Reactions
4.4 Curing Kinetics of Bio‐epoxies and Blends
4.4.1 Curing Kinetics of Bio‐epoxy Composites
4.5 Case Study: Non‐isothermal Kinetics of Plant Oil–Epoxy–Clay Composite
4.6 Conclusion and Future Prospective
References
5 Rheology of Bioepoxy Polymers, Their Blends, and Composites
5.1 Introduction
5.2 Rheology of Bioepoxy‐Based Polymers
5.2.1 Natural Oil‐Based Epoxies
5.2.2 Isosorbide‐Based Epoxy Resins
5.2.3 Phenolic and Polyphenolic Epoxies
5.2.4 Epoxidized Natural Rubber‐Based Epoxies
5.2.5 Epoxy Lignin Derivatives
5.2.6 Rosin‐Based Resin
5.3 Rheology of Bioepoxy‐Based Composites
5.4 Rheology of Bioepoxy‐Based Blends
5.5 Conclusions and Future Scope
References
6 Dynamical Mechanical Thermal Analysis of Bioepoxy Polymers, Their Blends, and Composites
6.1 Focus
6.2 Bioepoxies and Reinforcers
6.3 Dynamic Mechanical Analysis and Polymer Dynamics
6.4 Applications
6.5 Conclusion
References
7 Mechanical Properties of Bioepoxy Polymers, Their Blends, and Composites
7.1 Introduction
7.2 Mechanical Properties of Bioepoxy Polymers
7.2.1 Effect of Modifying Bioepoxy Chemical Structure
7.2.2 Effect of Curing Agents
7.3 Blends of Bioepoxy Resin
7.3.1 Toughening Effect of EVO‐Based Resins
7.3.2 Effect of Chemical Interaction in Epoxy Blend
7.3.3 Increasing Content Effect of EVOs in Bioepoxy Blend
7.4 Bioepoxy‐Based Composites
7.4.1 Undesirable Effect of Moisture Absorption
7.4.2 Fiber‐Reinforced Bioepoxy Composite
7.4.2.1 Natural Fiber‐Reinforced Bioepoxy Composites
7.4.2.2 Synthetic Fiber‐Reinforced Bioepoxy Composites
7.4.2.3 Hybrid Fiber‐Reinforced Bioepoxy Composites
7.4.3 Bioepoxy‐Based Nanocomposites
7.4.3.1 Nanoclay‐Reinforced Bioepoxy Composites
7.4.3.2 Cellulose Nanofiller‐Reinforced Bioepoxy Composites
7.4.4 Multiscale Bioepoxy Composites
7.5 Conclusion
7.6 Future Perspectives and Recommendations
Acknowledgment
References
8 Bio‐epoxy Polymer, Blends and Composites Derived Utilitarian Electrical, Magnetic and Optical Properties
8.1 Introduction
8.2 Significance of Bioepoxy‐Based Materials
8.3 Bioepoxy‐Derived Utilitarian Electrical, Magnetic, and Optical Properties. 8.3.1 Bioepoxy‐Based Material: Electrical and Electronic Properties
8.3.2 Bioepoxy‐Based Material: Magnetic and Optoelectronic Properties
8.4 Conclusion
References
9 Spectroscopy and Other Miscellaneous Techniques for the Characterization of Bio‐epoxy Polymers, Their Blends, and Composites
9.1 Introduction
9.2 Various Methods for Epoxy Polymer Characterization. 9.2.1 FTIR Spectroscopy
9.2.1.1 How Phase Separation Process Can Affect the IR Spectrum
9.2.2 Nuclear Magnetic Resonance (NMR) Spectroscopy
9.2.3 Differential Scanning Calorimetry (DSC)
9.2.4 Thermogravimetric Analysis (TGA)
9.3 Various Bio‐Based Epoxy Polymers, Theirs Uses, and Methods of Characterization in Review
9.3.1 Fire‐Retardant‐Based Epoxy
9.3.2 (Lignocellulosic Biomass)‐Based Epoxy Polymers
9.3.3 Furan‐Based Epoxy Resin
9.3.4 Rosin Corrosive‐Based Epoxy
9.3.5 Itaconic Corrosive‐Based Epoxy
9.3.6 Self‐mending Epoxy Resin
9.3.7 Other Epoxy Polymers
References
10 Flame Retardancy of Bioepoxy Polymers, Their Blends, and Composites
10.1 Introduction
10.2 Methods for Analyzing Flame‐Retardant Properties
10.2.1 LOI (Limiting Oxygen Index)
10.2.2 UL‐94
10.2.2.1 Horizontal Testing (UL‐94 HB)
10.2.2.2 Vertical Testing (UL‐94 V)
10.2.3 Cone Calorimeter
10.2.3.1 Configuration
10.2.3.2 Controlling Factors: Heat Flux, Thickness, and Distance Between Sample Surface and Cone Heater
10.2.4 Microscale Combustion Calorimeter
10.3 Halogen‐Free Flame‐Retardant Market
10.4 Bioepoxy Polymers with Flame‐Retardant Properties
10.4.1 Lignocellulosic Biomass‐Derived Epoxy Polymers
10.4.1.1 Eugenol
10.4.1.2 Vanillin
10.4.2 Furan
10.4.3 Tannins
10.5 Use of Fillers for Improving Flame‐Retardant Properties of Bioepoxy Polymers
10.6 Conclusion
Acknowledgment
References
11 Water Sorption and Solvent Sorption of Bio‐epoxy Polymers, Their Blends, and Composites
11.1 Introduction
11.2 Bio‐epoxy Resins
11.2.1 Soybean Oil (SO)‐Based Epoxy Resins
11.2.2 Cardanol‐Based Epoxy
11.2.3 Lignin‐Based Epoxy
11.2.4 Gallic Acid (C7H6O5)‐Based Epoxy
11.2.5 Itaconic Acid (C5H6O4)‐Based Epoxy
11.2.6 Natural Rubber (NR)‐Based Epoxy
11.2.7 Rosin‐Based Epoxy
11.2.8 Furan‐Based Epoxy
11.2.9 Hempseed Oil‐Based Epoxy
11.2.10 Eugenol (C10H12O2)‐Based Epoxy
11.3 Conclusion
References
12 Biobased Epoxy: Applications in Mendable and Reprocessable Thermosets, Pressure‐Sensitive Adhesives and Thermosetting Foams
12.1 Introduction
12.2 Mendable and Reprocessable Biobased Epoxy Polymers
12.2.1 Extrinsic Self‐healing Biobased Epoxies
12.2.2 Intrinsic Self‐healing Biobased Epoxies
12.3 Pressure‐Sensitive Adhesives (PSAs) From Biobased Epoxy Building Blocks
12.4 Biobased Epoxy Foams. 12.4.1 Syntactic Foams from Biobased Epoxy Resins
12.4.2 Thermosetting Epoxy Foams
References
Index
WILEY END USER LICENSE AGREEMENT
Отрывок из книги
Edited by
Jyotishkumar Parameswaranpillai
.....
Two molecules of vanillin can also be coupled through the dehydration condensation with pentaerythritol, leading to obtain the bisphenol with the specific spiro‐ring structure (Figure 1.30) [66], which can be further reacted with epichlorohydrin to give the epoxy resin.
This vanillin‐based resin exhibits very interesting properties [107]. This solid resin with an epoxy value of 0.355 mol/100 g, cross‐linked with diamine hardeners, DDM or 3,9‐bis(3‐aminopropyl)‐2,4,8,10‐tetroxaspiro(5,5)undecane, has several relaxations. The first is the β‐relaxation, caused by the micro‐Brownian motion of the aromatic methoxy group, observed from 50 to 100 °C for the spiro‐ring‐type resin systems in both mechanical and dielectric measurements. The peak height and the activation energy of this relaxation are independent of the degree of curing. The second one is the relaxation caused by the hydrogen bonding between the methoxy and the hydroxyl groups at around 0 °C [108]. This relaxation behavior is expected to have a positive effect on the damping characteristics. Moreover, the fracture toughness of the spiro‐ring‐type epoxide resin with methoxy branches is considerably greater above the temperature region of the β‐relaxation than that of the bisphenol A type resin [109].
.....