Engineering Solutions for CO2 Conversion
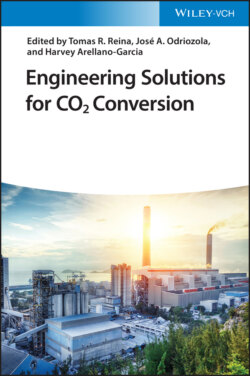
Реклама. ООО «ЛитРес», ИНН: 7719571260.
Оглавление
Группа авторов. Engineering Solutions for CO2 Conversion
Table of Contents
List of Tables
List of Illustrations
Guide
Pages
Engineering Solutions for CO2 Conversion
1 CO2 Capture – A Brief Review of Technologies and Its Integration
1.1 Introduction: The Role of Carbon Capture
1.2 CO2 Capture Technologies. 1.2.1 Status of CO2 Capture Deployment
1.2.2 Pre‐combustion
1.2.3 Oxyfuel
1.2.4 Post‐combustion
1.2.4.1 Adsorption
1.2.4.2 High‐Temperature Solids Looping Technologies
1.2.4.3 Membranes
1.2.4.4 Chemical Absorption
1.2.4.4.1 Advances on Process Configurations
1.2.5 Others CO2 Capture/Separation Technologies
1.2.5.1 Fuel Cells
1.2.5.1.1 Solid Oxide Fuel Cells (SOFCs)
1.2.5.1.2 Molten Carbonate Fuel Cells (MCFCs)
1.3 Integration of Post‐combustion CO2 Capture in the Power Plant and Electricity Grid
1.3.1 Integration of the Capture Unit in the Thermal Power Plant
1.3.2 Flexible Operation of Thermal Power Plants in Future Energy Systems
1.4 CO2 Capture in the Industrial Sector
1.5 Conclusions
References
Notes
2 Advancing CCSU Technologies with Computational Fluid Dynamics (CFD): A Look at the Future by Linking CFD and Process Simulations
2.1 Sweep Across the General Simulation Techniques Available
2.2 Multi‐scale Approach for CFD Simulation of Amine Scrubbers
2.3 Eulerian, Eulerian–Lagrangian, and Discrete Element Methods for the Simulation of Calcium Looping, Mineral Carbonation, and Adsorption in Other Solid Particulate Materials
2.4 CFD for Oxy‐fuel Combustion Technologies: The Application of Single‐Phase Reactive Flows and Particle Tracking Algorithms
2.5 CFD for Carbon Storage and Enhanced Oil Recovery (EOR): The Link Between Advanced Imaging Techniques and CFD
2.6 CFD for Carbon Utilization with Chemical Conversion: The Importance of Numerical Techniques on the Study of New Catalysts
2.7 CFD for Biological Utilization: Microalgae Cultivation
2.8 What Does the Future Hold?
References
3 Membranes Technologies for Efficient CO2 Capture–Conversion
3.1 Introduction
3.2 Polymer Membranes
3.3 Oxygen Transport Membranes for CO2 Valorization
3.3.1 Oxygen Transport Membrane Fundamentals
3.3.2 Application Concepts of OTMs for Carbon Capture and Storage (CCS)
3.3.3 Existing Developments
3.4 Protonic Membranes
3.4.1 Proton Defects in Oxide Ceramics
3.4.2 Proton Transport Membrane Fundamentals
3.4.3 Application Concepts of Proton Conducting Membranes
3.5 Membranes for Electrochemical Applications
3.5.1 Electrolysis and Co‐electrolysis Processes
3.5.1.1 Water Electrolysis
3.5.1.2 CO2 Co‐electrolysis
3.5.2 Synthesis Gas Chemistry
Power to methane
Power to methanol
3.5.3 Other Applications. 3.5.3.1 Methane Steam Reforming
3.5.3.2 Methane Dehydroaromatization
3.6 Conclusions and Final Remarks
References
4 Computational Modeling of Carbon Dioxide Catalytic Conversion
4.1 Introduction
4.2 General Methods for Theoretical Catalysis Research
4.3 Characterizing the Catalyst and Its Interaction with CO2 Using DFT Calculations
4.4 Microkinetic Modeling in Heterogeneous Catalysis
4.5 New Trends: High‐Throughput Screening, Volcano Plots, and Machine Learning. 4.5.1 High‐Throughput Screening
4.5.2 Volcano Plots and Scaling Relations
4.5.3 DFT and Machine Learning
4.5.3.1 Machine‐Learned Potentials
4.5.3.2 Descriptors to Predict Catalytic Properties
4.5.3.3 Future Challenges in HT‐DFT Applied to Catalysis
References
5 An Overview of the Transition to a Carbon‐Neutral Steel Industry
5.1 Introduction
5.2 Global Relevance of the Steel Industry
5.2.1 Features that Make Steel a Special Material
5.3 Current Trends in Emission Policies in the World's Leading Countries in Steel Industry
5.4 Transition to a Carbon‐Neutral Production. A Big Challenge for the Steel Industry
5.4.1 Urea
5.4.2 Methanol and Formic Acid
5.4.3 Carbon Monoxide
5.4.4 Methane
5.5 CO2 Methanation: An Interesting Opportunity for the Valorization of the Steel Industry Emissions
5.6 Relevant Projects Already Launched for the Valorization of the CO2 Emitted by the Steel Industry
5.7 Concluding Remarks
References
6 Potential Processes for Simultaneous Biogas Upgrading and Carbon Dioxide Utilization
6.1 Introduction
6.2 Overview of Biogas General Characteristics and Upgrading Technologies to Bio‐methane Production. 6.2.1 Biogas Composition and Applications
6.2.2 Biogas Upgrading Processes
6.2.2.1 Water Scrubbing
6.2.2.2 Pressure Swing Adsorption
6.2.2.3 Chemical Scrubbing
6.2.2.4 Organic Physical Scrubbing
6.2.2.5 Membrane Separation
6.2.2.6 Cryogenic Separation
6.3 CCU Main Technologies
6.3.1 Supercritical CO2 as a Solvent
6.3.2 Chemicals from CO2
6.3.3 Mineral Carbonation
6.3.4 Fuels from CO2
6.3.5 Algae Production
6.3.6 Enhanced Oil Recovery (EOR)
6.4 Potential Processes for Biogas Upgrading and Carbon Utilization
6.4.1 Chemical Scrubbing Coupled with CCU
6.4.2 Membrane Separation Coupled with CCU
6.4.3 Cryogenic Separation Coupled with CCU
6.5 Conclusions
References
7 Biogas Sweetening Technologies
7.1 Introduction
7.2 Biogas Purification Technologies
7.2.1 Removal of Water Vapor (H2O(g))
7.2.2 Removal of Hydrogen Sulfide (H2S) and Other Sulfur‐Containing Compounds
7.2.2.1 In Situ Precipitation of H2S Through Air/Oxygen Injection
7.2.2.2 In Situ Precipitation of H2S Through Iron Chloride/Oxide Injection
7.2.2.3 Adsorption by Activated Carbon
7.2.2.4 Zeolite‐Based Sieve (Molecular Sieve)
7.2.2.5 Water Scrubbing
7.2.2.6 Organic Solvent Scrubbing
7.2.2.7 Sodium Hydroxide Scrubbing
7.2.2.8 Chemical Adsorption via Iron Oxide or Hydroxide (Iron Sponge)
7.2.2.9 Biological Filters
7.2.3 Removal of Siloxanes
7.2.3.1 Organic Solvent Scrubbing
7.2.3.2 Adsorption on Activated Carbon, Molecular Sieves, and Silica Gel
7.2.3.3 Membrane Separation
7.2.3.4 Biological Filters
7.2.3.5 Cryogenic Condensation
7.2.4 Removal of Volatile Organic Compound (VOCs)
7.2.5 Removal of Ammonia (NH3)
7.2.6 Removal of Oxygen (O2) and Nitrogen (N2)
7.3 Biogas Upgrading Technologies
7.3.1 Water Scrubbing
7.3.2 Organic Solvent Scrubbing
7.3.3 Chemical Scrubbing
7.3.4 Pressure Swing Adsorption
7.3.5 Polymeric Membranes
7.3.6 Cryogenic Treatment
7.4 Conclusions
References
8 CO2 Conversion to Value‐Added Gas‐Phase Products: Technology Overview and Catalysts Selection
8.1 Chapter Overview
8.2 CO2 Methanation. 8.2.1 Background
8.2.2 Fundamentals
8.2.3 Catalysts
8.2.3.1 Ruthenium‐Based Catalysts
8.2.3.2 Nickel‐Based Catalysts
8.2.3.3 Rhodium and Palladium‐Based Catalysts
8.3 RWGS Reaction. 8.3.1 Background
8.3.2 Fundamentals
8.3.3 Catalysts
8.3.3.1 Noble Metal‐Based Catalysts
8.3.3.2 Copper‐Based Catalysts
8.3.3.3 Ceria‐Based Support Catalysts
8.3.3.4 Carbide Support Catalysts
8.4 CO2 Reforming Reactions. 8.4.1 Background
8.4.2 Fundamentals
8.4.3 Catalysts
8.4.3.1 Noble Metal‐Based Catalysts
8.4.3.2 Ni‐Based Catalysts
8.4.3.3 Catalytic Supports
8.5 Conclusions and Final Remarks
References
9 CO2 Utilization Enabled by Microchannel Reactors
9.1 Introduction
9.2 Transport Phenomena and Heat Exchange in Microchannel Reactors
9.2.1 Microfluidics and Mixing Flow
9.2.2 Heat Exchange and Temperature Control
9.3 Application of Microreactors in CO2 Capture, Storage, and Utilization Processes
9.3.1 CO2 Capture and Storage (CCS)
9.3.2 CO2 as a Feedstock for Producing Valuable Commodity Chemicals
9.3.2.1 Methanation of Carbon Dioxide (Sabatier Reaction)
9.3.2.2 CO2‐to‐Methanol and Dimethyl Ether (DME) Transformation
9.3.2.3 CO2‐to‐Higher Hydrocarbons and Fuels
9.3.2.4 Production of Cyclic Organic Carbonates
9.4 Concluding Remarks and Future Perspectives
References
10 Analysis of High‐Pressure Conditions in CO2 Hydrogenation Processes
10.1 Introduction
10.2 Thermodynamic Aspects
10.2.1 Le Chatelier Principle as a Simple Way to Understand the Effect of Pressure in Chemical Reactions
10.2.2 Equilibrium Composition Calculations of High‐Pressure Gas Reactions Based on the Computerized Gibbs Energy Minimization
10.3 Overview of Some Industrial Approaches Focused on the Production of Valuable Compounds form CO2 Using a Carbon Capture and Utilization (CCU) Approach
10.3.1 Industrial Production of Methanol
10.3.2 Production of Methane
10.4 Techno‐Economic Considerations for the Methanol Production from a CCU Approach with the Use of High Pressure
10.5 Concluding Remarks
References
Notes
11 Sabatier‐Based Direct Synthesis of Methane and Methanol Using CO2 from Industrial Gas Mixtures
11.1 Overview
11.2 Methane Synthesis of Gas Mixtures
11.2.1 Thermodynamics of Methane Conversion
11.2.2 Experimental Setup, General Definitions, and Catalysts
11.2.3 Industrial Gas Mixtures
11.3 Applications
11.3.1 APP‐01: Combustion Plant Flue Gas
11.3.2 APP‐02: Coke Oven Gas (COG)
11.3.3 APP‐03: Saline Aquifer Back‐Produced CO2
11.3.4 APP‐04: Biogenic CO2 Sources
11.3.5 APP‐05: Oxyfuel Operation in Gas Engines
11.3.6 APP‐06: Reusage of CH4 Product Gas Mixtures
11.4 Methanol Synthesis
Acknowledgments
References
12 Survey of Heterogeneous Catalysts for the CO2 Reduction to CO via Reverse Water Gas Shift
12.1 Introduction
12.2 RWGS Catalysts
12.2.1 Supported Metal Catalysts
12.2.1.1 Au‐Based Catalysts
12.2.1.2 Pt‐Based Catalysts
12.2.1.3 Rh‐Based Catalysts
12.2.1.4 Ru‐Based Catalysts
12.2.1.5 Pd‐ and Ir‐Based Catalysts
12.2.1.6 Cu‐Based Catalysts
12.2.1.7 Ni‐Based Catalysts
12.2.2 Oxide Systems
12.2.3 Transition Metal Carbides
12.3 Mechanism of RWGS Reaction
References
13 Electrocatalytic Conversion of CO2 to Syngas
13.1 Introduction
13.2 Production of Syngas
13.3 Electroreduction of CO2/Water Mixtures to Syngas
13.3.1 Effect of Cell Configuration and Chemical Environment
13.3.2 Effect of the Cathode Composition and Structure
13.3.3 Effect of the Reaction Parameters
13.3.4 Electrochemical Promotion of Catalyst (EPOC) for CO2 Hydrogenation
13.4 Conclusions
Acknowledgments
References
14 Recent Progress on Catalyst Development for CO2 Conversion into Value‐Added Chemicals by Photo‐ and Electroreduction
14.1 Introduction
14.2 CO2 Catalytic Conversion by Photoreduction
14.2.1 Principle of CO2 Photothermal Reduction
14.2.2 Catalyst Development for CO2 Photothermal Reduction
14.3 CO2 Catalytic Conversion by Electroreduction
14.3.1 Principle of CO2 Electrocatalytic Reduction
14.3.2 Catalysts Development for CO2 Electroreduction
References
15 Yolk@Shell Materials for CO2 Conversion: Chemical and Photochemical Applications
15.1 Overview
15.2 Key Benefits of Hierarchical Morphology
15.2.1 Confinement Effects
15.3 Materials for Chemical CO2 Recycling Reactions
15.3.1 CO2 Utilization Reactions
15.3.2 Photochemical Reactions with CO2
15.3.2.1 Principles of Photocatalysis
15.3.2.2 Prominent Materials
15.3.2.3 Benefits of YS in Photocatalysis
15.4 Synthesis Techniques for CS/YS: A Brief Overview
15.4.1 Soft Templating Techniques
15.4.2 Hard Templating Techniques
15.4.2.1 Metal Oxide/Carbide Shells
15.5 Future Advancement
References
16 Aliphatic Polycarbonates Derived from Epoxides and CO2
Abbreviations
16.1 Introduction
16.2 Aliphatic Polycarbonates. 16.2.1 Synthesis of the Monomers
16.2.2 Mechanistic Aspects of the Copolymerization of Epoxides and CO2
16.2.3 Thermal Stability and Possible Degradation Pathways
16.2.4 Mechanical Properties
16.3 Catalyst Systems for the CO2/Epoxide Copolymerization
16.3.1 Heterogeneous Catalysts
16.3.2 Overview of the Homogeneous Catalytic Systems
16.3.3 Terpolymerization Pathways
16.3.4 Limonene Oxide: Recent Advances in Catalysis and Mechanism Elucidation
16.4 Conclusion
References
17 Metal–Organic Frameworks (MOFs) for CO2 Cycloaddition Reactions
17.1 Introduction to MOF
17.2 MOFs as Catalysts
17.2.1 Active Sites in MOFs: Lewis Acid Sites. 17.2.1.1 Historical Overview
17.2.1.2 Tunability of the Lewis Acid Sites. 17.2.1.2.1 Nature of the Metal Cluster
17.2.1.2.2 Defect Generation
17.2.1.3 Active Sites in MOFs: Lewis Basic Sites
17.3 CO2 Cycloadditions
17.3.1 Reaction Mechanism
17.3.2 CO2 Cycloadditions Reactions Catalyzed by Lewis Acid MOFs
17.3.3 CO2 Cycloaddition Reactions Catalyzed by Lewis Acid and Basic MOFs
17.3.4 Defective MOFs for CO2 Cycloaddition Reactions
17.3.5 MOFs Having Functional Linkers for CO2 Cycloaddition Reactions
17.4 Oxidative Carboxylation
References
18 Plasma‐Assisted Conversion of CO2
18.1 Introduction
18.1.1 What Is a Plasma?
18.1.2 History
18.1.3 Electrification
18.1.4 Thermodynamics
18.1.5 Homogeneous Plasma Activation of CO2
18.1.6 Mechanisms
18.1.7 Plasma Reactors
18.1.8 Performance in Various Plasma Reactors
18.2 Plasma‐catalytic CO2 Conversion
18.2.1 Introduction
18.2.2 Mutual Influence of Plasma and Catalyst
18.2.3 Catalyst Development
18.2.4 Experimental Performance
18.2.4.1 CO2 Dissociation
18.2.4.2 Dry Reforming of Methane
18.2.4.3 CO2 Hydrogenation
18.2.4.4 Artificial Photosynthesis
18.3 Perspective
18.3.1 Models Describing Plasma Catalysis
18.3.2 Scale‐Up and Process Considerations
18.4 Conclusion
References
Index
WILEY END USER LICENSE AGREEMENT
Отрывок из книги
Edited by
Tomas R. Reina José A. Odriozola Harvey Arellano‐Garcia
.....
For large bandgap oxide materials (e.g. Ce, Ti, and Zr), the formation of proton defects at moderate temperatures takes places through the dissociative absorption of water [80]. Water dissociates into a hydroxide ion and a proton, the hydrogen ion then occupies an oxide ion vacancy, and the proton forms a covalent bond with a lattice oxygen. The formation of proton defects implies a significant weight gain; hence, the concentration of such defects can be measured by thermogravimetric analysis (TGA) as a function of temperature and water partial pressure.
Understanding the mechanism of proton conduction is of utmost importance for the development of novel materials. It is generally accepted that proton diffusion in protonic conductors occur via the Grotthuss‐type mechanism assisted by water molecules [81–83]. Moreover, hydrogen separation is driven by the hydrogen partial pressure difference across the membrane.
.....