Plastics Process Analysis, Instrumentation, and Control
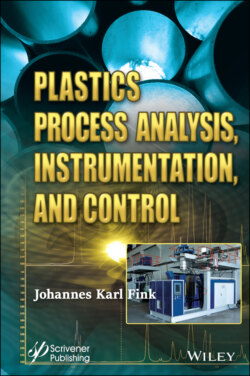
Реклама. ООО «ЛитРес», ИНН: 7719571260.
Оглавление
Группа авторов. Plastics Process Analysis, Instrumentation, and Control
Table of Contents
List of Illustrations
List of Tables
Guide
Pages
Plastics Process Analysis, Instrumentation, and Control
Preface
How to Use This Book
Index
Acknowledgements
1. General Aspects. 1.1 Subjects of the Book
1.2 Special Issues
1.3 Injection Molding. 1.3.1 Cost Estimation in Injection Molding
1.3.2 Cost Prediction Models
1.4 Miniature Molding Processes
1.5 Computer Determination of Weld Lines in Injection Molding
1.6 Extrusion Blow Molding. 1.6.1 Rapid Thermal Cycling Molding
1.6.2 Rapid Heat Cycle Molding
1.6.2.1 Reduction of Weld Lines
1.6.2.2 Lamellae Orientation of Isotactic Poly(propylene)
1.6.3 Injection Molding: Heating. 1.6.3.1 Modeling a Fast Mold Temperature
1.6.3.2 Hot Air Heating
1.6.3.3 Momentary Mold Surface Heating
1.6.3.4 Infrared Heating
1.6.3.5 Carbon-Bonded Graphene Coating
1.6.3.6 Induction Heating
1.7 Microcellular Injection Molding
1.8 Mold Cooling
1.9 Microcellular Foam Processing System
1.9.1 Gas-Assisted Injection Molding
1.9.1.1 Flow Visualization
1.9.1.2 Computer-Aided Engineering
1.9.1.3 Rubber Processing
1.9.1.4 Poly(lactic acid) Foams
1.9.2 Water-Assisted Injection Molding
1.10 Molding Machine for Granules
1.11 Foam Curing of Footwear
1.12 Injection Compression Molding
1.13 Hot Press System
1.14 Stamper Mold. 1.14.1 Recoding Media
1.14.2 Microscopic Structured Body
1.15 Plastic Waste
1.15.1 Marine Pollution
1.15.2 Human Health Effects
1.15.3 Recycling
1.15.3.1 Pollution Control
1.15.3.2 Bioplastics
1.15.3.3 Steam Cracker
1.15.3.4 Decomposition into Liquid Hydrocarbon Fuels
1.15.3.5 Decomposition in a Hot Oil Medium
1.15.3.6 Catalytic Cracking
References
2. Process Analysis
2.1 Concepts and Strategies
2.1.1 Chemometrics
2.1.2 Safety Risks
2.1.3 Feedback Procedures
2.2 Linear Systems. 2.2.1 Simple First-Order Systems. 2.2.1.1 LISREL Model
2.2.1.2 Metallocene Catalysts
2.2.2 Fractional Order Systems
2.2.3 Nonlinear Systems and Linearization. 2.2.3.1 Styrene Polymerization
2.2.3.2 Polymer Actuator Based on a Macroscopic Nonlinear Model
2.2.3.3 Cable-Driven Parallel Robots
2.2.3.4 Tumbling-Snake Model
2.2.3.5 Anchoraged Carbon Fiber-Reinforced Polymer and Concrete Surface
2.2.3.6 Cushion Curves of Polymer Foams
2.2.4 Characteristics of Systems. 2.2.4.1 Overshoot
2.2.4.2 Settling Time
2.2.5 Controllers and Controller Settings. 2.2.5.1 Controller for Polymer Extrusion
2.2.5.2 Temperature Control
2.2.5.3 Online Monitoring of Polymer Melting
2.2.5.4 Sliding Mode Controller
2.2.5.5 Micro Stereolithography
2.2.5.6 Flow Rate Controller for Petroleum Engineering
2.3 Twin-Screw Extrusion
References
3. Examples of Process Analysis. 3.1 Greenhouse Gas Balance. 3.1.1 Poly(ethylene furandicarboxylate)
3.1.2 Polyester Binder
3.2 Injection Molding Technology
3.2.1 Module for CAD Modeling of the Part
3.2.2 Module for Numerical Simulation of Injection Molding Process
3.2.3 Module for Calculation of Parameters of Injection Molding and Mold Design Calculation and Selection
3.2.4 Module for Mold Modeling
3.2.5 Examples of Testing
3.2.6 Molding Air Cooling
3.2.7 Cavity Pressure
3.2.8 Plastics Extruder Dynamics
3.2.9 History of Mathematical Modeling
3.2.10 Current Physical Components Concept
3.2.11 Process Stages. 3.2.11.1 Filling Stage
3.2.11.2 packing
3.2.11.3 Cooling
3.2.12 Data Envelopment Analysis
3.2.13 Taguchi Method
3.2.14 Tait Model
3.2.15 Phan-Thien-Tanner Model
3.2.16 Product Quality Prognosis
3.2.17 Production Predictive Control
3.2.18 Parameter Optimization for Energy Saving
3.2.19 Multilayer Control System
3.2.20 Smoothed Particle Hydrodynamics Method
3.2.21 Temperature-Dependent Adaptive Control
3.2.22 Micro-Injection Molding
3.2.22.1 Light Guide Plate
3.2.22.2 Micro Gear
3.2.22.3 Ejection Force
3.2.23 Immiscible Polymer Blends
3.2.23.1 Deformation Models
3.2.23.2 Results of Simulation
3.2.24 Resin Injection Molding
3.2.24.1 Classical Finite Element Procedure
3.2.24.2 Iterative Learning Control
3.2.25 Foam Injection Molding
3.2.26 Self-Optimizing Injection Molding Process
3.2.27 Machine Setup
3.2.27.1 Variable Displacement Pumps
3.2.27.2 Pressure Control
3.3 Shrinkage in Injection Molding
3.3.1 Factors that Affect the Shrinkage
3.3.2 Effect of a Cooling System
3.3.3 Influence of Molding Conditions on the Shrinkage and Roundness
3.3.4 Shear Viscosity
3.3.5 In-Situ Shrinkage Sensor
3.3.6 Semicrystalline Polymer
3.3.7 Thermoplastic Elastomers
3.3.8 Reprocessing of ABS
3.3.9 Sequential Simplex Algorithm with Automotive Ventiduct Grid
3.3.10 Taguchi, ANOVA, CAE, and Neural Network Methods. 3.3.10.1 Volume Shrinkage and Clamping Force
3.3.10.2 DVD-ROM Cover
3.3.10.3 Sisal-Glass Fiber Hybrid Biocomposite
3.3.10.4 Reduction of Warpage and Shrinkage
3.3.10.5 Neural Network Simulation
3.3.10.6 Multistage Modeling
3.3.10.7 Microgears
3.3.10.8 Linear Low-Density Poly(ethylene)
3.3.10.9 High-Density Poly(ethylene)
3.3.10.10 High-Density Poly(ethylene) Polymer Blends
3.3.10.11 Wood-Filled Poly(propylene)
3.3.10.12 Poly(propylene) and Poly(styrene)
3.4 Recycling by Extrusion. 3.4.1 Multiple In-Line Extruders
3.4.2 Mixed Post-Consumer Plastic Waste
3.4.3 Poly(methyl methacrylate)
3.4.4 Poly(ethylene terephthalate)
3.4.5 Poly(lactic acid)
3.4.6 Expanded Poly(styrene)
3.5 Batch Washing of Recycled Films. 3.5.1 Recycling of Poly(styrene) Waste
3.5.2 Textile Finishing
3.5.3 Removing Scrap from Containers
3.5.3.1 Discontinuous Batch Washing
3.5.3.2 Continuous Batch Tunnel Washer
3.5.4 Adsorption Isotherms and Desorption Rates
3.6 Self-Purging Microwave Pyrolysis
3.7 Purging and Plasticization in Injection Molding
3.7.1 Automatic Purging
3.8 Hot Runner Systems
3.8.1 Hot Runner Mold with Runner Pipe
3.8.2 Hot Runner System in Plastics Molding Tools
3.8.3 Manufacturing and Assembling of Hot Runner Systems
3.9 Blown Film Extrusion and Thickness Control
3.10 Residence Time Distribution for Biomass Pyrolysis
3.11 Reactive Extrusion
References
4. Process Instrumentation. 4.1 In-Mold Measurement
4.2 Temperature
4.2.1 Soft Actuator
4.2.2 Thermocouples
4.2.2.1 Small Temperature Probing
4.2.2.2 Spray Processed Thermocouple
4.2.2.3 Surface-Mounted Thermocouples
4.2.3 Resistance Temperature Detectors. 4.2.3.1 Platinum-Based Resistance Temperature Detector
4.2.3.2 Planar Resistance Temperature Detector
4.2.3.3 Flexible Resistive Temperature Detectors
4.2.3.4 Analog-Digital Conditioning Circuit
4.2.3.5 Process Temperature Measurement
4.2.3.6 Infrared Temperature Sensors
4.2.3.7 Special Issues
4.2.4 Thin Film Miniature Temperature Sensors
4.2.5 Neural Networks
4.3 Position Transducers
4.3.1 Rotary Position Transducer
4.3.2 Linear Variable Differential Transformers
4.3.3 Optical Encoders
4.3.4 Thickness Gauges
4.3.4.1 Infrared Gauges
4.3.4.2 Nuclear Gauges
4.3.4.3 Ultrasonic Vibration
4.3.4.4 Capacitance
4.4 Composition of Matter. 4.4.1 IR Interferometer for Multilayer Film
4.4.2 X-Ray Diffraction
4.4.3 Ion Mobility-Mass Spectrometry
4.4.4 Test for Ice Adhesion Strength
4.4.5 Piezoelectric Coaxial Filament Sensors
4.4.6 Instrumentation for Impact Testing
4.4.7 Treatment of Titanium Surfaces
4.4.8 Spatial Differentiation of Sub-Micrometer Domains
4.5 Medical Issues. 4.5.1 Endoscopic Plastic Surgical Procedures
4.5.2 Medical Catheters
4.5.2.1 Microcatheters
4.5.2.2 Balloon Catheters
4.5.2.3 Surface Roughness
4.5.2.4 Slippery Coating Layer
4.5.2.5 Surface Modification of Poly(vinylchloride)
4.5.2.6 Biofouling from Cell or Bacteria Adhesion
4.5.3 Multichannel Plastic Joint
4.5.4 Transluminal Endoscopic Surgery
4.5.5 Wire-Actuated Universal-Joint Wrists
4.5.6 Musculoskeletal Disorders
References
5. Actuators and Final Control Elements. 5.1 Servo Valves
5.1.1 Nozzle Assembly for a Servo Valve
5.2 Servo Motors. 5.2.1 Hydraulic System
5.2.2 Functionally Graded Materials
5.3 Solenoid Valves
5.3.1 Design Verification Methodology
5.3.2 Small Solenoid Valve
5.3.3 High-Speed Solenoid Valve
5.3.4 Numerical Simulation
5.4 Heaters. 5.4.1 Conduction Heaters
5.4.2 Radiant Heaters
5.4.3 Heater Controls. 5.4.3.1 Rise Time
5.4.3.2 Current Proportioning
5.5 Drive Motors and Motor Speed Control for Extrusion. 5.5.1 Single-Drive Motor
5.5.2 Linear Induction Motor
5.5.3 Motor Power Consumption in Single-Screw Extrusion
5.5.4 Dual Motor Multi-Head 3D Printer
References
6. Analysis of Melt Processing Systems. 6.1 Process Parameter Determination of Plastic Injection Molding
6.1.1 Case-Based Reasoning Method
6.1.2 Knowledge-Based Reasoning Method
6.1.3 Rule-Based Reasoning Method
6.1.4 Fuzzy Reasoning Method
6.2 Process Parameter Determination of Plastic Injection Molding of LCDs
6.3 Processing History
6.3.1 Flow Defects
6.3.2 Biocomposites. 6.3.2.1 Poly(lactic acid) Talc
6.3.2.2 Poly(amide) 11
6.3.3 3D Printing
6.3.4 Semiconducting Polymer Blends
6.3.5 Van Gurp-Palmen Plot
6.3.6 Nanocrystal Composites
6.3.7 Melt-Mastication
6.3.8 Crystal Nucleation in Nanocomposites
6.4 Shear History
6.5 Extrusion Product Control. 6.5.1 Branched Structures
6.5.2 Big Area Additive Manufacturing
6.5.3 Single-Screw Extrusion Control
6.5.3.1 Control Approaches
6.5.4 Blown Film
6.5.4.1 Blown Tube Diameter
6.5.4.2 Control System for Collapsing Frame
6.5.5 Chill Roll Cast Film
6.5.5.1 Quick Release Sleeve Chill Roll
6.5.5.2 Casting Apparatus
6.5.5.3 Reduced Chill Roll Buildup
6.5.5.4 Isotactic Poly(propylene) Films
6.5.6 Sheet
6.5.6.1 Simulation of Wrinkling of Viscoelastic Sheets
6.5.6.2 Composite Sandwiches
6.5.6.3 Viscoelastic Liquid Curtains
6.5.7 Profiles. 6.5.7.1 Drug Release Profile
6.5.7.2 Regression Models in Tubing Extrusion
6.5.7.3 Digital Processing of Images
6.5.8 Pipe and Tubing. 6.5.8.1 Plastic Pipe
6.5.8.2 Plastic Tubing
6.5.9 Automatic Screen Changers
6.6 Extrusion Blow Molding Parison Control
6.7 Injection Molding. 6.7.1 Ram Velocity Control
6.7.1.1 Electrohydraulic Control Circuit
6.7.1.2 Adaptive Controller
6.7.1.3 Computer Control System
6.7.1.4 Mold Modeling Software
6.7.2 Pressure Control
6.7.2.1 High-Pressure Transducers
6.7.2.2 Crystal-Based Piezoelectric Sensors
6.7.2.3 Wireless Piezoelectric Sensors
6.7.2.4 Thin-Film Piezoelectric Sensors
6.7.2.5 Thin-Film Piezoresistive Sensors
6.7.2.6 Strain Gauge Sensors
6.7.3 Gas-Assisted Control
6.7.4 System Diagnostics
6.7.4.1 Failure Cause Diagnostic Device
6.7.4.2 Fault Detection with Sensing Devices
6.7.4.3 Ultrasonic Sensors
6.7.4.4 Data Mining for Fault Diagnostics
6.7.5 Statistical Process and Quality Control
6.8 Thermoforming
6.8.1 Twin Sheet Thermoforming
6.8.2 Rotary Thermoforming
6.8.3 Process Model for Thermoforming
6.9 Rotomolding
6.9.1 Polymer Compositions for Rotomolding
6.10 Compounders. 6.10.1 History of Compounding
6.10.2 Types of Compounders. 6.10.2.1 Large Compounders
6.10.2.2 Toll Compounders
6.10.2.3 Speciality Compounders
6.10.3 Special Applications. 6.10.3.1 Granulates
6.10.3.2 Starch Plastics
6.10.3.3 Thermoplastic Polyolefin Elastomers
References
7. Auxiliary Equipment. 7.1 Crammer Feeder. 7.1.1 Crammer Feeder for Extruder
7.1.2 Devulcanization of Scrap Rubber
7.2 Dryers. 7.2.1 Drying Temperatures
7.2.2 Moisture Content
7.2.3 Resin Dryers
7.2.4 Pellet Dryers
7.2.4.1 Dryers for Plastic Granules
7.2.4.2 Cross-Flow Filter
7.2.4.3 Self-Cleaning Dryer
7.2.4.4 Noise Reduction
7.2.4.5 Dryer Control System
7.3 Pullers
7.3.1 Pullers in Extrusion. 7.3.1.1 Puller Speed in Extrusion
7.3.1.2 Extruded Synthetic Wood
7.3.2 Pullers in Injection Molding. 7.3.2.1 Friction Pullers
7.3.2.2 Foam Injection Molding
7.4 Chillers
7.5 Robots
References
Index. Acronyms
Chemicals
General Index
WILEY END USER LICENSE AGREEMENT
Отрывок из книги
Scrivener Publishing
.....
However, the thermal nanoimprint method has a problem as, in the filling stage of a fine structure of a high aspect ratio, the fluidity of the polymer is insufficient or a high pressure is needed. Also, the hot embossing method has a problem that, when the polymer is heated to the melting temperature, the fluidity of the polymer exceedingly increases and the polymer substrate only undergoes deformation of extending in a plane direction even when pressed, and thus the polymer is not filled into a deep groove portion of the fine structure in which flow resistance is large.
To address this problem, a method of manufacturing a molded product with a nanostructure and a microstructure has been proposed, which includes (59, 60):
.....