3D Printing for Energy Applications
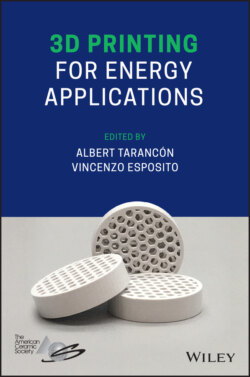
Реклама. ООО «ЛитРес», ИНН: 7719571260.
Оглавление
Группа авторов. 3D Printing for Energy Applications
Table of Contents
List of Tables
List of Illustrations
Guide
Pages
3D Printing for Energy Applications
Contributors
Introduction to 3D Printing Technologies
I.1 3D Printing Technologies
I.2 3D Printing Hierarchical, Material and Functional Complexity
I.3 3D Printing for Energy
I.4 Scope of the Book
References
1 Additive Manufacturing of Functional Metals
1.1 Introduction
1.1.1 Industrial Application of Metal AM in the Energy Sector
1.1.2 Geometrical Gradients in AM
1.1.3 Material Gradients in AM
1.2 Powder Bed Fusion AM
1.2.1 Geometric Gradients in PBF
1.2.2 Material Gradients in PBF
1.3 Direct Material Deposition. 1.3.1 Powder and Wire Feedstock for Near‐Net‐Shape AM
1.3.2 Functional Material Gradients in DED
1.4 Solid‐State Additive Manufacturing
1.5 Hybrid AM Through Green Body Sintering
1.5.1 Common AM Technologies for Green Body Manufacturing
1.5.2 CAD Design and Shrinkage Compensation
1.5.3 Additive Manufacture
1.5.4 Debinding and Sintering
1.5.5 Functionally Graded Components in Sintered Components
1.6 Conclusions
Acknowledgment
References
2 Additive Manufacturing of Functional Ceramics
2.1 Introduction
2.1.1 Why 3D Printing of Technical Ceramics?
2.1.2 Materials and Applications
2.2 Ceramics 3D Printing Technologies
2.2.1 Lamination Object Modeling (LOM)
2.2.2 Ceramics Extrusion
2.2.2.1 Robocasting/Direct Ink Writing
2.2.2.2 Fused Deposition of Ceramics
2.2.3 Photopolymerization
2.2.4 Laser‐Based Technologies
2.2.5 Jetting
References
3 3D Printing of Functional Composites with Strain Sensing and Self‐Heating Capabilities
3.1 Introduction
3.2 Carbon Nanotube Reinforced Functional Polymer Nanocomposites. 3.2.1 Strain Sensing of CNT Reinforced Polymer Nanocomposites
3.2.2 Resistive Heating of CNT Reinforced Polymer Nanocomposites
3.3 Printing Strategies. 3.3.1 Spray Deposition Modeling and Fused Deposition Modeling
3.3.2 Printing of Highly Flexible Carbon Nanotube/Polydimethylsilicone Strain Sensor
3.3.3 Printing of Carbon Nanotube/Shape Memory Polymer Nanocomposites
3.4 Strain Sensing of Printed Nanocomposites
3.5 Electric Heating Performance Analysis
3.6 Electrical Actuation of the CNT/SMP Nanocomposites
3.7 Conclusions
References
4 Computational Design of Complex 3D Printed Objects
4.1 Introduction
4.2 Dedicated Computational Design for 3D Printing
4.2.1 Overhang Angle Control Approaches
4.2.1.1 Local Angle Control
4.2.1.2 Physics‐Based Constraints
4.2.1.3 Simplified Printing Process
4.2.2 Design Scenarios
4.3 Case Study: Computational Design of a 3D‐Printed Flow Manifold
4.3.1 Fluid Flow TO
4.3.2 Front Propagation‐Based 3D Printing Constraint
4.3.3 Fluid TO with 3D Printing Constraint
4.4 Current State and Future Challenges
References
5 Multicomponent and Multimaterials Printing: A Case Study of Embedded Ceramic Sensors in Metallic Pipes
5.1 Multicomponent Printing: A Short Review
5.2 Multicomponent Printing: A Case Study on Piezoceramic Sensors in Smart Pipes. 5.2.1 Brief Introduction to AM of Embedded Sensors for Smart Metering
5.2.2 Fabrication of the Embedded Piezoceramic Sensor in Metallic Pipes. 5.2.2.1 Smart Coupling Fabrication Process Using EPBF Technology
5.2.2.2 Materials
5.2.2.3 Sensor Housing
5.2.2.4 Re‐poling of PZT
5.2.2.5 Impact in Sensing Properties Due to Heat‐Treatment Induced By AM Process
5.2.2.6 Smart Coupling Component
5.2.2.7 Compressive Force Sensing
5.2.2.8 Temperature Sensing
5.2.3 Impact of the AM and Performance of the Multicomponent Printed Device. 5.2.3.1 Compressive Force Sensing
5.2.3.2 Temperature Sensing
5.2.3.3 Crystalline Structure Analysis
5.3 Summary and Outlook
Acknowledgments
References
6 Tailoring of AM Component Properties via Laser Powder Bed Fusion
6.1 Introduction
6.2 Machines, Materials, and Sample Preparation
6.3 Sample Preparation and Characterization Techniques
6.4 Material Qualification and Process Development
6.5 Tailoring Grain Size via Adaptive Processing Strategies
6.6 Tailoring Material Properties By Using Powder Blends
6.7 Tailoring Properties By Using Special Geometries Such As Lattice Structures
Funding
Conflicts of Interest
References
7 3D Printing Challenges and New Concepts for Production of Complex Objects
7.1 Introduction
7.2 Geometrical Complexity
7.3 Material Complexity
7.4 Energy Requirements
7.5 Promising Metal Deposition Approaches
7.6 Multimaterial and Multi‐property SLA
7.7 Temporal Multiplexing
7.8 Resin Formulations with Multiple End‐States
7.9 Associated Processing Considerations
7.10 Bioprinting of Realistic and Vascularized Tissue
7.11 Emerging Volumetric Additive Processes
7.12 Computation for CAL
7.13 Material–Process Interactions in CAL
7.14 Current Challenges in CAL
7.15 Expanding the Capabilities of CAL
7.16 Concluding Remarks and Outlook
Acknowledgments
References
8 Current State of 3D Printing Technologies and Materials
8.1 3D Printing of Energy Devices. 8.1.1 Batteries
8.1.1.1 3D Printing Structured Electrodes
3D‐Structured Electrodes
Interdigitated Electrode Structures
8.1.1.2 3D Printing Solid Electrolytes
8.1.1.3 3D Printed Full Batteries
8.1.1.4 Conclusion and Outlook
References
9 Capacitors
9.1 Introduction
9.2 Capacitors and Their Current Manufacture
9.2.1 Capacitor Classifications, Operating Principles, Applications, and Current Manufacture
9.2.1.1 Electrostatic Capacitors
9.2.1.2 Electrolytic Capacitors
9.2.1.3 Electrochemical Capacitors
9.2.2 Capacitor Components: Function and Requirements
9.2.3 Performance
9.2.4 The Challenge of Manufacturing Capacitors
9.3 The Promise of Additive Manufacturing
9.4 Additive Manufacturing Technologies: Considerations for Capacitor Fabrication. 9.4.1 AM Process Categories
9.4.1.1 Material Extrusion – Fused Filament Fabrication
9.4.1.2 Material Extrusion – Direct Ink Writing
9.4.1.3 Vat Polymerization
9.4.1.4 Powder Bed Fusion
9.4.1.5 Material Jetting
9.4.1.6 Binder Jetting
9.4.2 Multi‐technology or Hybrid Printing
9.4.3 Complete Capacitor Devices Fabricatedby Additive Manufacturing
9.5 Summary and Outlook
Acronyms
References
10 3D‐Printing for Solar Cells
10.1 Introduction
10.2 Examples of 3D‐Printing for PV
10.3 Geometric Light Management. 10.3.1 Background
10.3.2 Optical Model for External Light Trapping
10.3.3 Design and 3D‐Printing of the External Light Trap
10.3.4 Characterization
10.4 Conclusions
References
11 3D Printing of Fuel Cells and Electrolyzers
11.1 Introduction
11.2 3D Printing of Solid Oxide Cells Technology
11.2.1 Solid Oxide Fuel Cells
11.2.1.1 SOFC Electrolyte
11.2.1.2 SOFC Electrodes
Anode
Cathode
11.2.2 Solid Oxide Electrolysis Cells
11.2.3 SOC Stacks and Components
11.3 3D Printing of Polymer Exchange Membranes Cells Technology
11.3.1 Polymeric Exchange Membrane Fuel Cells
11.3.1.1 PEMFC Electrolyte
11.3.1.2 PEMFC Catalysts Layer
11.3.1.3 PEMFC Gas Diffusion Layer
11.3.1.4 PEMFC Bipolar Plates and Flow Fields
11.3.2 Polymer Exchange Membrane Electrolysis Cells
11.3.2.1 PEMEC Liquid Gas Diffusion Layer
11.3.2.2 PEMEC Bipolar Plates and Flow Fields
11.3.2.3 Fully Printed PEMEC
11.4 3D Printing of Bio‐Fuel Cells Technology
11.5 Conclusions and Outlook
References
12 DED for Repair and Manufacture of Turbomachinery Components
12.1 Introduction
12.2 DED Based Repair of Turbomachinery Components
12.2.1 DED Process
12.2.2 Work Environment
12.2.3 Process Chain for the Repair of Turbine Blades
12.2.3.1 Step 1: “Machining & Preparation”
12.2.3.2 Step 2: “Reverse Engineering”
12.2.3.3 Step 3: “Generation of Tool Paths”
12.2.3.4 Step 4: “DED Process”
12.2.3.5 Step 5: “Adaptive Machining”
12.3 DED Based Hybrid Manufacturing of New Components
12.3.1 Hybrid Additive Manufacturing
12.3.2 Turbocharger Nozzle Ring
12.3.3 Hybrid Production Cell
12.3.4 Process Chain for Hybrid Additive Manufacturing of Nozzle Rings
12.3.4.1 Step 1: “Choice of DED Strategy”
12.3.4.2 Step 2: “DED Process”
12.3.4.3 Step 3: “Optical Metrology”
12.3.4.4 Step 4: “Adaptive Milling”
12.3.4.5 Step 5: “Joining of Top Ring”
12.4 Summary
Acknowledgments
References
13 Thermoelectrics
13.1 Introduction
13.2 Additive Manufacturing Techniques of Thermoelectric Materials. 13.2.1 Extrusion‐Based Additive Manufacturing Process
13.2.2 Fused Deposition Modeling (FDM) Technique
13.2.3 Stereolithography Apparatus (SLA) Process
13.2.4 Selective Laser Sintering (SLS) Process
13.2.5 Summary and Outlook
Acknowledgements
References
14 Carbon Capture, Usage, and Storage
14.1 Introduction
14.2 Can 3D Printing Be Used to Fabricate a CO2 Capture Process at Scale?
14.3 A Brief Note on 3D Printing and CO2 at Smaller Scales & Research Efforts
14.4 Conclusions
References
Index. a
b
c
d
e
f
g
h
i
j
k
l
m
n
o
p
r
s
t
u
v
x
y
z
WILEY END USER LICENSE AGREEMENT
Отрывок из книги
Edited by
.....
Hossein Heidari Department of Mechanical Engineering, University of California, Berkeley, CA, USA
Chi Chung Li Department of Mechanical Engineering, University of California, Berkeley, CA, USA
.....