Processing of Ceramics
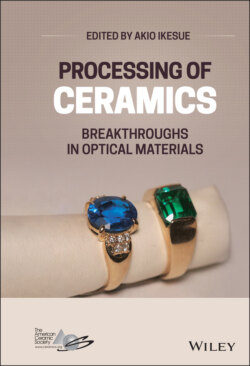
Реклама. ООО «ЛитРес», ИНН: 7719571260.
Оглавление
Группа авторов. Processing of Ceramics
Table of Contents
List of Tables
List of Illustrations
Guide
Pages
Processing of Ceramics. Breakthroughs in Optical Materials
List of Contributors
Preface
1 Introduction
1.1 Introduction
1.2 Technical Problem of Conventional Single Crystal
1.3 Problem of Conventional Translucent and Transparent Ceramics
1.4 Objective of Optical Grade Ceramics
1.5 Conclusions
References
2 Ceramic Laser/Solid‐State Laser
2.1 Background
2.2 Principle of Laser Generation. 2.2.1 Spontaneous Emission
2.2.2 Stimulated Emission and Laser Generation
2.3 Laser Ceramics. 2.3.1 Synthesis of Garnet‐Based Materials
2.3.2 Laser Oscillation by Monolithic Garnet Ceramics
2.3.3 Synthesis and Laser Performance of Sesquioxide Ceramics
2.3.4 Other Materials (CaF2, Pseudo Perovskite, ZnSe, ZnS, etc.)
2.3.5 Fiber Ceramics as Laser Gain Media
2.3.6 Optically Anisotropic Ceramics
2.3.7 Laser Oscillation by Composite Laser Elements
References
3 Scintillators
3.1 Background
3.1.1 Historical Development of Scintillators
3.1.2 Application of Scintillators
3.2 Physics of Scintillation
3.2.1 Characteristics of Scintillation Materials
3.3 Inorganic Single Crystal Scintillation Materials. 3.3.1 Halide Scintillators
3.3.2 Oxide Scintillators
3.4 Fabrication of Advanced Single Crystal and Ceramics Scintillators
3.4.1 Rare‐Earth Oxyorthosilicate Scintillators
3.4.2 Garnet Scintillators
3.4.3 GOS Ceramic Scintillators
3.4.4 (Y,Lu,Gd)2O3:Eu Ceramic Scintillators
3.5 Optimization of Single Crystal and Ceramic Scintillators. 3.5.1 Rare‐Earth Oxyorthosilicate Scintillators
3.5.2 Garnet Scintillators
3.5.3 GOS Ceramic Scintillators
3.5.4 (Y,Lu,Gd)2O3:Eu Ceramic Scintillators
3.6 Residual Problems and Future Trends
Acknowledgments
References
4 Magneto‐Optic Transparent Ceramics
4.1 Introduction
4.2 Theory of Magneto‐Optic Effect
4.2.1 Magneto‐Optic Effect in Paramagnetic Transparent Ceramics
4.2.2 Magneto‐Optic Effect in Ferromagnetic Material
4.2.3 Measurement of Verdet Constant, Insertion Loss, and Extinction Ratio
4.3 Important Parameter for Application
4.3.1 Thermal Lens Effect in Faraday Rotator
4.3.2 High Power Laser Irradiation
4.4 Paramagnetic Magneto‐Optic Ceramic Materials. 4.4.1 TGG Ceramics
4.4.2 TAG (Terbium Aluminum Garnet) Ceramics
4.4.3 Sesqui‐Oxide Ceramics
4.4.4 Pyrochlore Ceramics
4.5 Ferrimagnetic Magneto‐Optic Ceramics
4.5.1 Yttrium Iron Garnet
4.5.2 Bismuth Doped Yttrium Iron Garnet Ceramics
4.5.3 Cerium Doped Yttrium Iron Garnet Ceramics
4.6 Summary
References
5 Solid‐State Lighting
5.1 Introduction
5.2 Light Emitting Diodes (LEDs)
5.2.1 Brief History
5.2.2 Principle and Structure
5.2.3 Generation of White Light from LEDs
5.3 Fundamentals of Phosphor‐Converted White LEDs
5.3.1 Basic Principles of Luminescence. 5.3.1.1 Photoluminescence
5.3.1.2 Thermal Quenching
5.3.1.3 Quantum Efficiency
5.3.2 Key Parameters of White LEDs. 5.3.2.1 Luminous Efficacy
5.3.2.2 CIE Chromaticity Coordinates
5.3.2.3 Correlated Color Temperature
5.3.2.4 Color Rendering Index
5.4 Optical Ceramic Phosphors for High‐Power Solid‐State Lighting. 5.4.1 Introduction
5.4.2 Ceramic Phosphors for High‐Power White LEDs/LDs
5.4.2.1 Yellow‐Emitting Ceramic Phosphors. 5.4.2.1.1 YAG:Ce Ceramic Phosphors
5.4.2.1.2 TAG:Ce Ceramic Phosphor
5.4.2.1.3 GAGG:Ce Ceramic Phosphor
5.4.2.2 Red‐Emitting Ceramic Phosphors. 5.4.2.2.1 Red‐Emitting CaAlSiN3:Eu Ceramic Phosphor
5.4.2.2.2 Other Red‐Emitting Ceramic Phosphors
5.4.2.3 Green‐Emitting Ceramic Phosphors. 5.4.2.3.1 LuAG:Ce Green‐Emitting Ceramic Phosphor
5.4.2.3.2 Other Green‐Emitting Ceramic Phosphors
5.4.2.4 White‐Emitting Ceramic Phosphors
5.4.2.5 Composite Ceramic Phosphors with Novel Structure
5.4.3 Summary and Outlook
References
6 Passive Application/Window, Dome, and Armor
6.1 Background
6.2 Important Parameters. 6.2.1 Optical Properties
6.2.2 Mechanical Properties
6.2.3 Thermal Properties
6.3 Fabrication of Passive Ceramics
6.3.1 Spinel (MgO2Al4)
6.3.2 Aluminum Oxynitride (AlON)
6.3.3 Alumina (Al2O3)
6.3.4 Garnet (Y3Al5O12)
6.3.5 Yttria (Y2O3)
6.3.6 Zirconia (ZrO2)
6.3.7 Magnesia (MgO)
6.3.8 MgO‐Y2O3
6.3.9 Fluorides
6.4 Performance for Various Applications. 6.4.1 Performance Required for Armor Application
6.4.2 Performance Required for Infrared Windows
6.4.3 Performance Required for Optical System
6.5 Residual Problems and Future
References
7 Other Important Technologies
7.1 Surface Polishing (Finishing) and Coating. 7.1.1 Introduction on Surface Polishing
7.1.2 Laser Grade Polishing
7.1.3 Polishing Examples. 7.1.3.1 Measurement of Surface Figure Error/Transmitted Wavefront Error
7.1.3.2 Measurement of Surface Roughness
7.1.3.3 Measurement of Surface Imperfection
7.1.4 Introduction for Coating
7.1.5 Design of AR and HR Coating
7.1.6 Characteristic of Coated Film
7.1.7 Future Trends on Surface Polishing and Coating
7.2 Bonding Technology. 7.2.1 Problems of Existing Technology, Ceramic Composite Production, and Advantages
7.2.2 Microstructure and Thermal/Mechanical Properties of Bonding Interface
7.2.3 Optical Quality and Damage Characteristics of Bonded Ceramic Composites
7.3 Single Crystal Ceramics by SSCG (Solid‐State Crystal Growth) 7.3.1 Significance of Single Crystal Growth by Sintering Method
7.3.2 Single Crystal Growth Method by Sintering Method
7.3.3 Quality and Laser Characteristics of the Obtained Single Crystal
7.3.4 Synthesis of Noncubic Single Crystals by Sintering Method
7.4 Applications Using Ceramic Laser Technology
7.5 New Applications Using Transparent Ceramics. 7.5.1 Ceramic Jewels
7.5.2 Wireless Heating Element
7.5.3 Camera Lens
7.5.4 Screen for Mobile Phone
7.5.5 UV Transmission Lens for Lithography
7.6 Residual Problems and Future
References
Conclusion Remarks
Index. a
b
c
d
e
f
g
h
i
j
l
m
n
o
p
q
r
s
t
u
v
w
x
y
z
WILEY END USER LICENSE AGREEMENT
Отрывок из книги
Edited by
Akio Ikesue
.....
Figure 1.9 (a) Appearance of granulated Al2O3‐Y2O3 powders by spray drier and (b) internal structure of Al2O3‐Y2O3 powder compact after uniaxial press under 20 MPa.
The powder compact showed in the above figure is further pressed in CIP (cold isostatic press) machine at 140 MPa. Then, the pore size distribution of this sample after CIP was measured by using the mercury penetration method. The result is shown in Figure 1.10. The pore diameter of the sample using a binder with good crushing characteristics is concentrated at 30–40 nm, but large voids of μm size are detected in the other samples without a binder, resulting in structure defects (which induce light scattering sources at the end product). Once large structural defects are formed, it is difficult to completely remove them even by high‐pressure sintering techniques such as HP (hot press) and HIP (hot isostatic press) treatments.
.....