Sustainable Practices in the Textile Industry
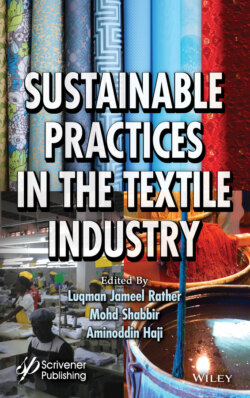
Реклама. ООО «ЛитРес», ИНН: 7719571260.
Оглавление
Группа авторов. Sustainable Practices in the Textile Industry
Table of Contents
List of Illustrations
List of Tables
Guide
Pages
Sustainable Practices in the Textile Industry
Preface
1. Extraction and Application of Natural Dyes
1.1 Introduction
1.2 What are Natural Dyes?
1.3 Why Natural Dyes?
1.4 What are Synthetic Dyes?
1.5 Sources of Natural Dyes
1.6 Types of Natural Dyes
1.6.1 Classification on the Basis of Their Chemical Constitution
1.6.2 Classification Based on Method of Application/Preparation
1.7 Natural Dyes Need Fixing Agent (Mordants) for Bonding
1.7.1 Metallic Mordants
1.7.2 Tannins and Tannic Acid
1.7.3 Oil Mordants
1.7.4 Bio-Mordants
1.7.5 Method of Application
1.8 Fibers/Fabrics Used for Natural Dyeing
1.8.1 Cellulosic Fiber
1.8.2 Protein Fiber
1.8.3 Synthetic Fiber
1.9 Extraction of Natural Dyes
1.10 Dyeing Process. 1.10.1 Preparation of Fabric Before Dyeing
1.10.2 Mechanism of Dyeing
1.10.3 Process of Dyeing
1.11 Evaluation of the Dyed Fabric. 1.11.1 Color Strength or K/S Value
1.11.2 Color Fastness Properties
1.12 Some Special Characteristics of Naturally Dyed Fabric. 1.12.1 Antimicrobial Properties
1.12.2 UV Protection
1.12.3 Deodorizing Finishing
1.12.4 Moth Resistant and Insect Repellent
1.13 Conclusion
1.13.1 Overview
1.13.2 Legislative Regulations for Synthetic Dyes
1.13.3 Sustainability Aspects of Natural Dyes
1.13.4 Practicality of Natural Dyes
Acknowledgement
References
2. Recent Advances in Non-Aqueous Dyeing Systems
2.1 Introduction
2.2 Supercritical Fluid Dyeing System
2.2.1 Application of Supercritical CO2 on Synthetic Fabric
2.2.2 Application of Supercritical CO2 on Natural Fabric
2.2.3 Dyes Solubility in Supercritical Fluids
2.3 Reverse Micelle Systems
2.3.1 Mechanism and Formation of Reverse Micelle
2.3.2 Application of Reverse Micelle Dyeing System
2.4 Solvent Dyeing
2.5 Silicone Non-Aqueous Dyeing
2.6 Conclusion
References
3. Structural Coloration of Textile Materials
3.1 Introduction
3.2 Thin-Film Interference
3.2.1 Principle of Thin-Film Interference
3.2.2 Multilayer Interference
References
4. Enzymatic Wet Processing
4.1 Introduction
4.2 Enzymes
4.3 Function of Enzymes
4.4 Classification of Enzymes
4.5 Αn-Amylase Enzyme for Desizing
4.6 Pectinase Enzyme for Scouring
4.7 Protease Enzyme for Wool Anti-Felting
4.8 Cellulase Enzyme for Biopolishing and Biostoning
4.9 Hairiness Removal Mechanism
4.9.1 During Scouring and Bleaching in Alkaline Condition
4.9.2 Applying Before Dyeing in Acidic Condition
4.10 Enzyme Decolorization of Textile Effluent
4.11 Enzymes for Increasing Dyeability of Different Fibers. 4.11.1 Application on Cotton
4.11.2 Application on Nylon
4.12 Conclusion
References
5. Coating Textiles: Towards Sustainable Processes
5.1 Introduction
5.2 Most Used Polymers for Coating Textiles
5.2.1 Polytetrafluoroethylene (PTFE)
5.2.2 Polyvinyl Acetate (PVAc)
5.2.3 Polyvinyl Alcohol (PVA)
5.2.4 Polyurethanes (PUs)
5.2.5 Polyvinyl Chloride (PVC) and Polyvinylidene Chloride (PVDC)
5.2.6 Polysiloxanes
5.2.7 Acrylics
5.2.8 Phosphorous-Based Polymers
5.3 Traditional Coating Methods
5.4 Environmental Friendly Polymers
5.4.1 Cyclodextrins
5.4.2 Chitin and Chitosan
5.4.3 Sodium Alginate
5.4.4 Polyethylene Glycols
5.4.5 Natural Rubber
5.4.6 Polyvinyl Alcohol
5.4.7 Dendrimers
5.4.8 Sericin
5.4.9 Polyphenols
5.5 Sustainable Coating Technologies
5.5.1 Powder Coating Technique
5.5.2 Sol–Gel Technology
5.5.3 Plasma Treatment
5.5.4 Electro-Fluidodynamic Technology
5.5.5 Supercritical Fluid Technology
5.5.6 Vapor Deposition Methods
5.6 Conclusion
References
6. A Review on Hydrophobicity and Fabricating Hydrophobic Surfaces on the Textiles
6.1 Introduction
6.2 Self-Cleaning Surfaces
6.3 Applications of Hydrophobic Surfaces
6.4 Basic Theories: Modeling of Contact Angle
6.4.1 Young’s Model
6.4.2 Wenzel Model (Homogeneous Interface)
6.4.3 Cassie–Baxter Model (Composite Interface)
6.5 Techniques to Make Super-Hydrophobic Surfaces
6.6 Methods of Applying Hydrophobic Coating on Textiles
6.6.1 Dip-Coating
6.6.2 Spray Coating
6.7 Contact Angles (CA) Measurement
6.8 Research Records on Hydrophobic Surface Production
6.9 Conclusion
References
7. UV Protection: Historical Perspectives and State-of-the-Art Achievements
7.1 Introduction
7.2 Fundamentals Regarding UV Protection of Textile Fabrics
7.2.1 The Design of the Woven Support Represents a Relevant Factor That Directly Affect UPF
7.2.2 The Synergism Between Structural Parameters and UV Protection of Textile Supports
7.2.3 Yarn Curve End up Being the Significant Determinant of the UV Security Attributes of Textile Supports
7.2.4 The Correlation Between Fabric Porosity and Cover Factor and UV Protection
7.2.5 Concepts of Ultraviolet Protection Factor and Sun Protection Factor
7.3 UV Stabilizers Beginnings and Initial Development. 7.3.1 UV Protection Finishing of Fabrics Using Nanoparticles
7.3.1.1 Inorganic Formulations With Nano-ZnO Particles
7.3.1.2 UV Shield of Cotton Support Conferred by TiO2 Nanoparticles
7.3.1.3 Formulations Containing Nanoparticles of ZnO, Titania, Silica, Silver, Carbon-Nanotubes, Graphene and Silver Onto Cotton Textiles
7.3.2 UV Protection of Fabrics by Dyeing of Textile Supports
7.3.3 Other Kind of Finishes
7.4 Conclusion
References
8. Synthetic and Natural UV Protective Agents for Textile Finishing
8.1 Introduction
8.2 Ultraviolet Radiation (UVR)
8.3 Importance of Ultraviolet Protective Finish
8.3.1 Ultraviolet Protection With Textiles
8.4 Methods of Blocking Ultraviolet Rays
8.5 Ultraviolet Protection Factor Measurement System. 8.5.1 In Vitro
8.5.2 In Vivo
8.6 Clothing Factors Affecting Ultraviolet Protection Factor
8.6.1 Fabric Structure
8.6.2 Fiber Physio-Chemical Nature
8.6.3 Dyeing
8.7 Mechanisms of UV Protection
8.8 Types of Ultraviolet Absorbers. 8.8.1 Organic
8.8.2 Inorganic
8.9 Commercial Ultraviolet Protective Clothing
8.10 Nanoparticle Coatings for Ultraviolet Protective Textiles
8.11 Durability of Ultraviolet Protective Finish
8.12 Conclusion
References
9. Sustainable Orientation of Textile Companies
9.1 Introduction
9.2 Textile Industry—Environmental, Social and Economic Issues
9.3 Circular Economy
9.4 Sustainability Circles
9.5 Circularity in the Supply Chain
9.6 Consumer Behavior of Sustainable Textile Products
9.7 Decision to Purchase Sustainable Textile Products
9.8 Policies and Strategies Used in the Sustainable Textile Industry
9.9 Conclusions
References
10. Sustainable Application of Ionic Flocculation Method for Textile Effluent Treatment
10.1 Introduction
10.2 Conventional Methods for Degradation of Textile Effluents
10.2.1 Biological Methods
10.2.2 Chemical Methods
10.2.3 Physical Methods
10.3 Surfactants
10.4 Adsorptive Micellar Flocculation (AMF)
10.5 Mechanism
10.6 Choice of Flocculant
10.7 Analysis and Calculations
10.7.1 Analysis of Reagents
10.7.2 Calculated Parameters
10.8 Optimization of Conditions for Better Removal of Dye Using AMF
10.8.1 Effect of Temperature
10.8.2 Effect of pH
10.8.3 Surfactant Dosage
10.8.4 Flocculant/Surfactant Ratio
10.8.5 Addition of Electrolyte
10.8.6 Contact Time and Stirring Speed
10.9 Potential Advantages of AMF
10.10 Application to Wastewaters
10.11 Conclusion
10.12 Future Prospective
References
11. Remediation of Textile Wastewater by Ozonation
11.1 Introduction
11.2 Sources of Wastewater
11.3 Ozonation Remediation for Textile Water
11.3.1 Impact of pH on Uptake of Organic Pollutants
11.3.2 Impact of Initial Dye Concentration
11.3.3 Impact of Inlet Ozone Concentration
11.3.4 Impact of Ozonation Time
11.4 Impact of Various Techniques in Combination Ozonation Process for Treatment of Textile Wastewater
11.5 Degradation of Dyes via Ozonation
11.6 Conclusion
References
12. Design of a New Cold Atmospheric Plasma Reactor Based on Dielelectric Barrier Discharge for the Treatment and Recovery of Textile Dyeing Wastewater: Profoks/CAP Reactor
12.1 Introduction
12.2 Advanced Oxidation Processes (AOP) in Wastewater Treatment
12.2.1 Cold Atmospheric Plasma Technology (CAP)
12.2.2 Formation and Chemical Reactivity of Reactive Oxygen Species (ROS)
12.2.3 CAP/AOP Application in Textile Wastewater Treatment
12.3 Profoks/CAP Wastewater Treatment and Water Recovery System
12.3.1 Profoks/CAP Wastewater Treatment and Water Recovery System and Textile Wastewater Recovery Studies
12.3.2 Profoks/CAP Wastewater Treatment and Water Recovery System and the Results of Treatability of Textile Wastewater and the Study of Water Recovery
12.3.3 Profoks/CAP Wastewater Treatment and Water Recovery System Investment and Operating Costs
12.4 Conclusion
References
13. Nanotechnology and its Application in Wastewater Treatment
13.1 Introduction
13.2 Nanotechnology
13.2.1 Adsorption
13.2.1.1 Carbon-Based Nanoadsorbents
13.2.1.2 Metal-Based Nanoadsorbents
13.2.1.3 Polymeric Nanoadsorbents
13.2.1.4 Zeolites
13.2.2 Membrane-Based Techniques
13.2.2.1 Nanofiber Membranes
13.2.2.2 Nanocomposite Membranes
13.2.2.3 Thin Film Nanocomposite Membranes
13.2.2.4 Nanofiltration Membranes
13.2.2.5 Aquaporin-Based Membranes
13.2.3 Metal Nanoparticles. 13.2.3.1 Silver Nanoparticles
13.2.3.2 Iron Nanoparticles
13.2.3.3 Titanium Dioxide Nanoparticles
13.3 Conclusion
References
Index
Also of Interest
WILEY END USER LICENSE AGREEMENT
Отрывок из книги
Scrivener Publishing
.....
22. Lacasse, K. and Baumann, W., Textile chemicals: Environmental data and facts, Springer, Dortmund, 2012.
23. Foguel, M.V., Ton, X.A., Zanoni, M.V., Maria Del Pilar, T.S., Haupt, K., Bui, B.T.S., A molecularly imprinted polymer-based evanescent wave fiber optic sensor for the detection of basic red 9 dye. Sens. Actuators B, 218, 222, 2015.
.....