Flow-Induced Vibration Handbook for Nuclear and Process Equipment
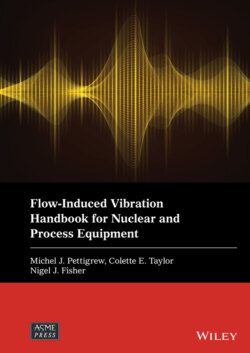
Реклама. ООО «ЛитРес», ИНН: 7719571260.
Оглавление
Группа авторов. Flow-Induced Vibration Handbook for Nuclear and Process Equipment
Table of Contents
List of Tables
List of Illustrations
Guide
Pages
Wiley‐ASME Press Series
Flow‐Induced Vibration Handbookfor Nuclear and Process Equipment
Preface
Acknowledgments
Contributors
1 Introduction and Typical Vibration Problems
1.1 Introduction
1.2 Some Typical Component Failures
1.3 Dynamics of Process System Components. 1.3.1 Multi‐Span Heat Exchanger Tubes
1.3.2 Other Nuclear and Process Components
References
Notes
2 Flow‐Induced Vibration of Nuclear and Process Equipment: An Overview
2.1 Introduction
2.1.1 Flow‐Induced Vibration Overview
2.1.2 Scope of a Vibration Analysis
2.2 Flow Calculations
2.2.1 Flow Parameter Definition
2.2.2 Simple Flow Path Approach
2.2.3 Comprehensive 3‐D Approach
2.2.4 Two‐Phase Flow Regime
2.3 Dynamic Parameters
2.3.1 Hydrodynamic Mass
2.3.2 Damping
Heat Exchanger Tubes in Gases
Heat Exchanger Tubes in Liquids
Damping in Two‐Phase Flow
2.4 Vibration Excitation Mechanisms
2.4.1 Fluidelastic Instability
Single‐Phase Cross Flow (Gas or Liquid)
Two‐Phase Flow
2.4.2 Random Turbulence Excitation
Single‐Phase Cross Flow
Two‐Phase Cross Flow
2.4.3 Periodic Wake Shedding
2.4.4 Acoustic Resonance
2.4.5 Susceptibility to Resonance
2.5 Vibration Response Prediction
2.5.1 Fluidelastic Instability
2.5.2 Random Turbulence Excitation
2.5.3 Periodic Wake Shedding
2.5.4 Acoustic Resonance
2.5.5 Example of Vibration Analysis
2.6 Fretting‐Wear Damage Considerations
2.6.1 Fretting‐Wear Assessment
2.6.2 Fretting‐Wear Coefficients
2.6.3 Wear Depth Calculations
2.7 Acceptance Criteria
2.7.1 Fluidelastic Instability
2.7.2 Random Turbulence Excitation
2.7.3 Periodic Wake Shedding
2.7.4 Tube‐to‐Support Clearance
2.7.5 Acoustic Resonance
2.7.6 Two‐Phase Flow Regimes
References
Note
3 Flow Considerations
3.1 Definition of the Problem
3.2 Nature of the Flow. 3.2.1 Introduction
3.2.2 Flow Parameter Definitions
Example 3-1 Flow in a Process Heat Exchanger
Example 3-2 Flow in a Nuclear Steam Generator
3.2.3 Vertical Bubbly Flow
3.2.4 Flow Around Bluff Bodies
3.2.5 Shell-Side Flow in Tube Bundles
3.2.6 Air-Water versus Steam-Water Flows
3.2.7 Effect of Nucleate Boiling Noise
3.2.8 Summary
3.3 Simplified Flow Calculation
Example 3-3 Flow in a Process Heat Exchanger Using Flow Paths
3.4 Multi-Dimensional Thermalhydraulic Analysis
3.4.1 Steam Generator
3.4.2 Other Heat Exchangers
Acronyms
Nomenclature
Subscripts
References
Notes
4 Hydrodynamic Mass, Natural Frequencies and Mode Shapes
4.1 Introduction
4.2 Total Tube Mass
4.2.1 Single‐Phase Flow
Example 4-1 Single‐Phase Total Tube Mass in a Process Heat Exchanger
4.2.2 Two‐Phase Flow
Example 4-2 Two‐Phase Total Tube Mass in a Nuclear Steam Generator
4.3 Free Vibration Analysis of Straight Tubes
4.3.1 Free Vibration Analysis of a Single‐Span Tube
Example 4-3 Calculation of Frequency in a Process Heat Exchanger
Example 4-4 Calculation of Frequency in a Nuclear Steam Generator U‐Bend
4.3.2 Free Vibration Analysis of a Two‐Span Tube
4.3.3 Free Vibration Analysis of a Multi‐Span Tube
4.4 Basic Theory for Curved Tubes
4.4.1 Theory of Curved Tube In‐Plane Free Vibration
4.4.2 Theory of Curved Tube Out‐of‐Plane Free Vibration
4.5 Free Vibration Analysis of U‐Tubes
4.5.1 Setting Boundary Conditions for the In‐Plane Free Vibration Analysis of U‐Tubes Possessing Geometric Symmetry
4.5.2 Development of the In‐Plane Eigenvalue Matrix for a Symmetric U‐Tube
4.5.3 Generation of Eigenvalue Matrices for Out‐of‐Plane Free Vibration Analysis of U‐Tubes Possessing Geometric Symmetry
Example 4-5 Symmetric Steam Generator U‐Tube Free Vibration Analysis
4.5.4 Free Vibration Analysis of U‐Tubes Which Do Not Possess Geometric Similarity
4.6 Concluding Remarks
Nomenclature
References
5 Damping of Cylindrical Structures in Single‐Phase Fluids
5.1 Introduction
5.2 Energy Dissipation Mechanisms
5.3 Approach
5.4 Damping in Gases
5.4.1 Effect of Number of Supports
5.4.2 Effect of Frequency
5.4.3 Vibration Amplitude
5.4.4 Effect of Diameter or Mass
5.4.5 Effect of Side Loads
5.4.6 Effect of Higher Modes
5.4.7 Effect of Support Thickness
5.4.8 Effect of Clearance
5.5 Design Recommendations for Damping in Gases
Example 5-1 Calculation of Damping in a Gas Heat Exchanger
5.6 Damping in Liquids
5.6.1 Tube‐to‐Fluid Viscous Damping
5.6.2 Damping at the Supports
5.6.3 Squeeze‐Film Damping
5.6.4 Damping due to Sliding
5.6.5 Semi‐Empirical Formulation of Tube‐Support Damping
5.7 Discussion
5.8 Design Recommendations for Damping in Liquids
5.8.1 Simple Criterion Based on Available Data
5.8.2 Criterion Based on the Formulation of Energy Dissipation Mechanisms
Example 5-2 Calculation of Damping in a Process Heat Exchanger
Nomenclature
Subscript
References
6 Damping of Cylindrical Structures in Two‐Phase Flow
6.1 Introduction
6.2 Sources of Information
6.3 Approach
6.4 Two‐Phase Flow Conditions. 6.4.1 Definition of Two‐Phase Flow Parameters
6.4.2 Flow Regime
6.5 Parametric Dependence Study
6.5.1 Effect of Flow Velocity
6.5.2 Effect of Void Fraction
6.5.3 Effect of Confinement
6.5.4 Effect of Tube Mass
6.5.5 Effect of Tube Vibration Frequency
6.5.6 Effect of Tube Bundle Configuration
6.5.7 Effect of Motion of Surrounding Tubes
6.5.8 Effect of Flow Regime
6.5.9 Effect of Fluid Properties
6.6 Development of Design Guidelines
Example 6-1 Calculation of Damping in a Nuclear Steam Generator
6.7 Discussion. 6.7.1 Damping Formulation
6.7.2 Two‐Phase Damping Mechanisms
6.8 Summary Remarks
Nomenclature
Subscripts
References
Note
7 Fluidelastic Instability of Tube Bundles in Single‐Phase Flow
7.1 Introduction
7.2 Nature of Fluidelastic Instability
7.3 Fluidelastic Instability: Analytical Modelling
7.4 Fluidelastic Instability: Semi‐Empirical Models
7.5 Approach
7.6 Important Definitions
7.6.1 Tube Bundle Configurations
7.6.2 Flow Velocity Definition
7.6.3 Critical Velocity for Fluidelastic Instability
7.6.4 Damping
7.6.5 Tube Frequency
7.7 Parametric Dependence Study
7.7.1 Flexible versus Rigid Tube Bundles
7.7.2 Damping
7.7.3 Pitch‐to‐Diameter Ratio, P/D
7.7.4 Fluidelastic Instability Formulation
7.8 Development of Design Guidelines
Example 7-1 Fluidelastic Instability Calculation in a Single‐Phase Heat Exchanger
Example 7.2 Fluidelastic Instability Calculation in a Single‐Phase Heat Exchanger with Window Region
7.9 In‐Plane Fluidelastic Instability
7.10 Axial Flow Fluidelastic Instability
7.11 Concluding Remarks
Nomenclature
Subscript
References
8 Fluidelastic Instability of Tube Bundles in Two‐Phase Flow
8.1 Introduction
8.2 Previous Research
8.2.1 Flow‐Induced Vibration in Two‐Phase Axial Flow
8.2.2 Flow‐Induced Vibration in Two‐Phase Cross Flow
8.2.3 Damping Studies
8.3 Fluidelastic Instability Mechanisms in Two‐Phase Cross Flow
8.4 Fluidelastic Instability Experiments in Air‐Water Cross Flow. 8.4.1 Initial Experiments in Air‐Water Cross Flow
8.4.2 Behavior in Intermittent Flow
8.4.3 Effect of Bundle Geometry
8.4.4 Flexible versus Rigid Tube Bundle Behavior
8.4.5 Hydrodynamic Coupling
8.5 Analysis of the Fluidelastic Instability Results. 8.5.1 Defining Critical Mass Flux and Instability Constant
8.5.2 Comparison with Results of Other Researchers
8.5.3 Summary of Air‐Water Tests
8.6 Tube Bundle Vibration in Two‐Phase Freon Cross Flow. 8.6.1 Introductory Remarks
8.6.2 Background Information
8.6.3 Experiments in Freon Cross Flow
8.7 Freon Test Results and Discussion. 8.7.1 Results and Analysis
8.7.2 Proposed Explanations
8.7.3 Concluding Remarks
8.7.4 Summary Findings
8.8 Fluidelastic Instability of U‐Tubes in Air‐Water Cross Flow
8.8.1 Experimental Considerations
8.8.2 U‐Tube Dynamics
8.8.3 Vibration Response
8.8.4 Out‐of‐Plane Vibration
8.8.5 In‐Plane Vibration
8.9 In‐Plane (In‐Flow) Fluidelastic Instability. 8.9.1 In‐Flow Experiments in a Wind Tunnel
8.9.2 In‐Flow Experiments in Two‐Phase Cross Flow
8.9.3 Single‐Tube Fluidelastic Instability Results
8.9.4 Single Flexible Column and Central Cluster Fluidelastic Instability Results
8.9.5 Two Partially Flexible Columns
8.9.6 In‐Flow Fluidelastic Instability Results and Discussion
8.10 Design Recommendations
8.10.1 Design Guidelines
8.10.2 Fluidelastic Instability with Intermittent Flow
Example 8-1 Fluidelastic Instability in a Steam Generator U‐Bend
8.11 Fluidelastic Instability in Two‐Phase Axial Flow
8.12 Concluding Remarks
Nomenclature
Subscripts
References
Note
9 Random Turbulence Excitation in Single‐Phase Flow
9.1 Introduction
9.2 Theoretical Background
9.2.1 Equation of Motion
9.2.2 Derivation of the Mean-Square Response
9.2.3 Simplification of Tube Vibration Response
9.2.4 Integration of the Transfer Function
9.2.5 Use of the Simplified Expression in Developing Design Guidelines
9.3 Literature Search
9.4 Approach Taken
9.5 Discussion of Parameters. 9.5.1 Directional Dependence (Lift versus Drag)
9.5.2 Bundle Orientation
9.5.3 Pitch‐to‐Diameter Ratio (P/D)
9.5.4 Upstream Turbulence
9.5.5 Fluid Density (Gas versus Liquid)
9.5.6 Summary
9.6 Design Guidelines
Example 9-1 Random Excitation in Process Heat Exchanger Interior Flow
9.7 Random Turbulence Excitation in Axial Flow
Nomenclature
References
10 Random Turbulence Excitation Forces Due to Two-Phase Flow
10.1 Introduction
10.2 Background
10.3 Approach Taken to Data Reduction
10.4 Scaling Factor for Frequency
10.4.1 Definition of a Velocity Scale
10.4.2 Definition of a Length Scale
10.4.3 Dimensionless Reduced Frequency
10.4.4 Effect of Frequency
10.5 Scaling Factor for Power Spectral Density
10.5.1 Effect of Flow Regime
10.5.2 Effect of Void Fraction
10.5.3 Effect of Mass Flux
10.5.4 Effect of Tube Diameter
10.5.5 Effect of Correlation Length
10.5.6 Effect of Bundle and Tube-Support Geometry
10.5.7 Effect of Two-Phase Mixture
10.5.8 Effect of Nucleate Boiling
10.6 Dimensionless Power Spectral Density
10.7 Upper Bounds for Two-Phase Cross Flow Dimensionless Spectra
10.7.1 Bubbly Flow
10.7.2 Churn Flow
10.7.3 Intermittent Flow
Example 10-1 Random Excitation for Two-Phase Flow in SG U-Bend
Example 10.2 Random Excitation for SG U-Bend Using an Early Guideline
10.8 Axial Flow Random Turbulence Excitation
10.9 Conclusions
Nomenclature
References
11 Periodic Wake Shedding and Acoustic Resonance
11.1 Introduction
11.2 Periodic Wake Shedding
11.2.1 Frequency: Strouhal Number
11.2.2 Calculating Tube Resonance Amplitudes
11.2.3 Fluctuating Force Coefficients in Single‐Phase Flow
11.2.4 Fluctuating Force Coefficients in Two‐Phase Flow
11.2.5 The Effect of Bundle Orientation and P/D on Fluctuating Force Coefficients
11.2.6 The Effect of Void Fraction and Flow Regime on Fluctuating Force Coefficients
Example 11-1 Periodic Wake Shedding in Single‐Phase Flow
Example 11-2 Calculating Periodic Wake Shedding in a Moisture Separator Reheater
11.3 Acoustic Resonance
11.3.1 Acoustic Natural Frequencies
11.3.2 Equivalent Speed of Sound
11.3.3 Acoustic Natural Frequencies (fa)n,
11.3.4 Frequency Coincidence — Critical Velocities
11.3.5 Damping Criteria
11.3.6 Sound Pressure Level
11.3.7 Elimination of Acoustic Resonance
Example 11-3 Calculating Acoustic Resonance in a Moisture Separator Reheater
11.4 Conclusions and Recommendations
Nomenclature
References
12 Assessment of Fretting‐Wear Damage in Nuclear and Process Equipment
12.1 Introduction
12.2 Dynamic Characteristics of Nuclear Structures and Process Equipment
12.2.1 Heat Exchangers
12.2.2 Nuclear Structures
12.3 Fretting‐Wear Damage Prediction
12.3.1 Time‐Domain Approach
12.3.2 Energy Approach
12.4 Work‐Rate Relationships. 12.4.1 Shear Work Rate and Mechanical Power
12.4.2 Vibration Energy Relationship
12.4.3 Single Degree‐of‐Freedom System
12.4.4 Multi‐Span Beams Under Harmonic Excitation
12.4.5 Response to Random Excitation
12.4.6 Work‐Rate Estimate: Summary
12.5 Experimental Verification
12.6 Comparison to Time‐Domain Approach
12.7 Practical Applications: Examples
Example 12-1 Heat Exchanger Tubes
Example 12-2 Steam Generator U‐Bend Tubes
Example 12-3 Nuclear Fuels
Example 12-4 Piping Systems
12.8 Concluding Remarks
Nomenclature
References
Note
13 Fretting‐Wear Damage Coefficients
13.1 Introduction
13.2 Fretting‐Wear Damage Mechanisms
13.2.1 Impact Fretting Wear
13.2.2 Trends
13.2.3 Work‐Rate Model
13.3 Experimental Considerations. 13.3.1 Experimental Studies
13.3.2 Room‐Temperature Test Data
13.3.3 High‐Temperature Experimental Facility
13.3.4 Wear Volume Measurements
13.4 Fretting Wear of Zirconium Alloys. 13.4.1 Introduction
13.4.2 Experimental Set‐Up
13.4.3 Effect of Vibration Amplitude and Motion Type
13.4.4 Effect of Pressure‐Tube Pre‐Oxidation and Surface Preparation
13.4.5 Effect of Temperature
13.4.6 Effect of pH Control Additive and Dissolved Oxygen Content
13.4.7 Discussions
13.5 Fretting Wear of Heat Exchanger Materials
13.5.1 Work‐Rate Model and Wear Coefficient
13.5.2 Effect of Test Duration
13.5.3 Effect of Temperature
13.5.4 Effect of Water Chemistry
13.5.5 Effect of Tube‐Support Geometry and Tube Materials
13.5.6 Discussion
13.6 Summary and Recommendations
Nomenclature
References
Notes
Appendix A Component Analysis. A.1 Introduction
A.2 Analysis of a Process Heat Exchanger
Example 3-1 Flow in a Process Heat Exchanger
Example 4.1 Single‐Phase Total Tube Mass in a Process Heat Exchanger
Example 4-3 Calculation of Frequency in a Process Heat Exchanger
Example 5-2 Calculation of Damping in a Process Heat Exchanger
Example 7-2 FEI Calculation in a Single‐Phase Process Heat Exchanger with Window Region
Example 9-1 Random Excitation in Process Heat Exchanger Interior Flow
Example 11-1 Periodic Wake Shedding in Single‐Phase Flow
Example A-1 Fretting‐Wear Damage Prediction in a Process Heat Exchanger
A.3 Analysis of a Nuclear Steam Generator U‐Bend
Example 3-2 Flow in a Nuclear Steam Generator (SG)
Example 4-2 Two‐Phase Total Tube Mass in a Nuclear Steam Generator
Example 4-4 Calculation of Frequency in a Nuclear Steam Generator U‐Bend
Example 6-1 Calculation of Damping in a Nuclear Steam Generator
Example 8-1 Fluidelastic Instability in a Steam Generator U‐Bend
Example 10-1 Random Excitation for Two‐Phase Flow in Steam Generator U‐Bend
Example 10-2 Random Excitation for SG U‐Bend Using an Early Guideline
Example A-2 Fretting‐Wear Damage Prediction in a Steam Generator U‐Bend
Subject Index. a
b
c
d
e
f
g
h
i
j
l
m
n
o
p
q
r
s
t
u
v
w
WILEY END USER LICENSE AGREEMENT
Отрывок из книги
Fabrication of Process Equipment
.....
For single‐phase flow fo = Up/D and .
In most cases, the random excitation forces for interior tubes are significantly lower than for upstream tubes. The vibration response of the upstream tubes will be larger. Thus, it may not be necessary to consider the vibration response of interior tubes when they are otherwise identical to the upstream tubes.
.....