Organic Corrosion Inhibitors
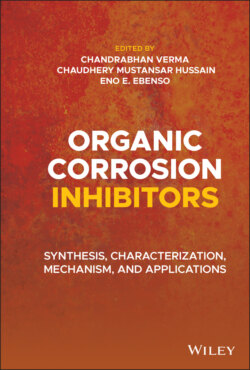
Реклама. ООО «ЛитРес», ИНН: 7719571260.
Оглавление
Группа авторов. Organic Corrosion Inhibitors
Table of Contents
List of Tables
List of Illustrations
Guide
Pages
Organic Corrosion Inhibitors. Synthesis, Characterization, Mechanism, and Applications
Preface
About the Editors
List of Contributors
1 An Overview of Corrosion
1 Introduction. 1.1 Basics About Corrosion
1.2 Economic and Social Aspect of Corrosion
1.3 The Corrosion Mechanism
1.3.1 Anodic Reaction
1.3.2 Cathodic Reactions
1.4 Classification of Corrosion
1.4.1 Uniform Corrosion
1.4.2 Pitting Corrosion
1.4.3 Crevice Corrosion
1.4.4 Galvanic Corrosion
1.4.5 Intergranular Corrosion
1.4.6 Stress‐Corrosion Cracking (SCC)
1.4.7 Filiform Corrosion
1.4.8 Erosion Corrosion
1.4.9 Fretting Corrosion
1.4.10 Exfoliation
1.4.11 Dealloying
1.4.12 Corrosion Fatigue
1.5 Common Methods of Corrosion Control
1.5.1 Materials Selection and Design
1.5.2 Coatings
1.5.3 Cathodic Protection (CP)
1.5.4 Anodic Protection
1.5.5 Corrosion Inhibitors
1.6 Adsorption Type Corrosion Inhibitors
1.6.1 Anodic Inhibitors
1.6.2 Cathodic Inhibitors
1.6.3 Mixed Inhibitors
1.6.4 Green Corrosion Inhibitors
References
2 Methods of Corrosion Monitoring
2.1 Introduction
2.2 Methods and Discussion. 2.2.1 Corrosion Monitoring Techniques
2.3 Conclusion
References
3 Computational Methods of Corrosion Monitoring
3.1 Introduction
3.2 Quantum Chemical (QC) Calculations‐Based DFT Method
3.2.1 Theoretical Framework
3.2.2 Theoretical Application of DFT in Corrosion Inhibition Studies: Design and Chemical Reactivity Prediction of Inhibitors
3.2.2.1 HOMO and LUMO Electron Densities
3.2.2.2 HOMO and LUMO Energies
3.2.2.3 Electronegativity (ɳ), Chemical Potential (μ), Hardness (η), and Softness (σ) Indices
3.2.2.4 Electron‐Donating Power (ω−) and Electron‐Accepting Power (ω+)
3.2.2.5 The Fraction of Electrons Transferred (ΔN)
3.2.2.6 Fukui Indices (FIs)
3.3 Atomistic Simulations
3.3.1 Molecular Dynamics (MD) Simulations
3.3.1.1 Total Energy Minimization
3.3.1.2 Ensemble
3.3.1.3 Force Fields
3.3.1.4 Periodic Boundary Condition
3.3.2 Monte Carlo (MC) Simulations
3.3.3 Parameters Derived from MD and MC Simulations of Corrosion Inhibition
3.3.3.1 Interaction and Binding Energies
3.3.3.2 Radial Distribution Function
3.3.3.3 Mean Square Displacement, Diffusion Coefficient, and Fractional Free Volume
Acknowledgments
Suggested Reading
References
4 Organic and Inorganic Corrosion Inhibitors: A Comparison
4.1 Introduction
4.2 Corrosion Inhibitors
4.2.1 Organic Corrosion Inhibitors
4.2.1.1 Azoles
4.2.1.2 Azepines
4.2.1.3 Pyridine and Azines
4.2.1.4 Indoles
4.2.1.5 Quinolines
4.2.1.6 Carboxylic Acid and Biopolymers
4.2.1.7 Inorganic Corrosion Inhibitors
4.2.1.8 Anodic Inhibitors
4.2.1.9 Cathodic Inhibitors
References
5 Amines as Corrosion Inhibitors: A Review
5.1 Introduction. 5.1.1 Corrosion: Basics and Its Inhibition
5.1.2 Amines as Corrosion Inhibitors
5.1.2.1 10‐, 20‐, and 30‐Aliphatic Amines as Corrosion Inhibitors
5.1.2.2 Amides and Thio‐Amides as Corrosion Inhibitors
5.1.2.3 Schiff Bases as Corrosion Inhibitors
5.1.2.4 Amine‐Based Drugs and Dyes as Corrosion Inhibitors
5.1.2.5 Amino Acids and Their Derivatives as Corrosion Inhibitors
5.2 Conclusion and Outlook
Important Websites
References
6 Imidazole and Its Derivatives as Corrosion Inhibitors
6.1 Introduction. 6.1.1 Corrosion and Its Economic Impact
6.2 Corrosion Mechanism
6.3 Corrosion Inhibitors
6.4 Corrosion Inhibitors: Imidazole and Its Derivatives
6.5 Computational Studies
6.6 Conclusions
References
7 Pyridine and Its Derivatives as Corrosion Inhibitors
7.1 Introduction
7.1.1 Pyridine and Its Derivatives as Corrosion Inhibitors
7.1.2 Literature Survey. 7.1.2.1 Substituted Pyridine as Corrosion Inhibitors
7.1.3 Pyridine‐Based Schiff Bases (SBs) as Corrosion Inhibitors
7.1.4 Quinoline‐Based Compounds as Corrosion Inhibitors
7.2 Summary and Outlook
References
8 Quinoline and Its Derivatives as Corrosion Inhibitors
8.1 Introduction
8.2 Quinoline and Its Derivatives as Corrosion Inhibitors
8.2.1 8‐Hydroxyquinoline and Its Derivatives as Corrosion Inhibitors
8.2.2 Quinoline Derivatives Other Than 8‐hydroxyquinoline as Corrosion Inhibitors
8.3 Conclusion and Outlook
References
9 Indole and Its Derivatives as Corrosion Inhibitors
9.1 Introduction
9.2 Synthesis of Indoles and Its Derivatives
9.3 A Brief Overview of Corrosion and Corrosion Inhibitors
9.4 Application of Indoles as Corrosion Inhibitors
9.4.1 Indoles as Corrosion Inhibitors of Ferrous Metals
9.4.2 Indoles as Corrosion Inhibitors of Nonferrous Metals
9.5 Corrosion Inhibition Mechanism of Indoles
9.6 Theoretical Modeling of Indole‐Based Chemical Inhibitors
9.7 Conclusions and Outlook
References
10 Environmentally Sustainable Corrosion Inhibitors in Oil and Gas Industry
10.1 Introduction
10.2 Corrosion in the Oil–Gas Industry. 10.2.1 An Overview of Corrosion
10.2.2 Corrosion of Steel Structures During Acidizing Treatment
10.2.3 Limitations of the Existing Oil and Gas Corrosion Inhibitors
10.3 Review of Literature on Environmentally Sustainable Corrosion Inhibitors. 10.3.1 Plant Extracts
10.3.2 Environmentally Benign Heterocycles
10.3.3 Pharmaceutical Products
10.3.4 Amino Acids and Derivatives
10.3.5 Macrocyclic Compounds
10.3.6 Chemically Modified Biopolymers
10.3.7 Chemically Modified Nanomaterials
10.4 Conclusions and Outlook
References
11 Carbohydrates and Their Derivatives as Corrosion Inhibitors
11.1 Introduction
11.2 Glucose‐Based Inhibitors
11.3 Chitosan‐Based Inhibitors
11.4 Inhibition Mechanism of Carbohydrate Inhibitor
11.5 Conclusions
References
12 Amino Acids and Their Derivatives as Corrosion Inhibitors
12.1 Introduction
12.2 Corrosion Inhibitors
12.3 Why There Is Quest to Explore Green Corrosion Inhibitors?
12.4 Amino Acids and Their Derived Compounds: A Better Alternate to the Conventional Toxic Corrosion Inhibitors
12.4.1 Amino Acids: A General Introduction
12.4.2 A General Mechanistic Aspect of the Applicability of Amino Acids and Their Derivatives as Corrosion Inhibitors
12.4.3 Factors Influencing the Inhibition Ability of Amino Acids and Their Derivatives
12.5 Overview of the Applicability of Amino Acid and Their Derivatives as Corrosion Inhibitors
12.5.1 Amino Acids and Their Derivatives as Corrosion Inhibitor for the Protection of Copper in Different Corrosive Solution
12.5.2 Amino Acids and Their Derivatives as Corrosion Inhibitor for the Protection of Aluminum and Its Alloys in Different Corrosive Solution
12.5.3 For the Protection of Iron and Its Alloys in Different Corrosive Solution
12.6 Recent Trends and the Future Considerations
12.6.1 Synergistic Combination of Amino Acids with Other Compounds
12.6.2 Self‐Assembly Monolayers (SAMs)
12.6.3 Amino Acid‐Based Ionic Liquids
12.6.4 Amino Acids as Inhibitors in Smart Functional Coatings
12.7 Conclusion
References
13 Chemical Medicines as Corrosion Inhibitors
13.1 Introduction
13.2 Greener Application and Techniques Toward Synthesis and Development of Corrosion Inhibitors
13.2.1 Ultrasound Irradiation‐Assisted Synthesis
13.2.2 Microwave‐Assisted Synthesis
13.2.3 Multicomponent Reactions
13.3 Types of Chemical Medicine‐Based Corrosion Inhibitors. 13.3.1 Drugs
13.3.2 Expired Drugs
13.3.3 Functionalized Drugs
13.4 Application of Chemical Medicines in Corrosion Inhibition. 13.4.1 Drugs
13.4.2 Expired Drugs
13.4.3 Functionalized Drugs
Acknowledgments
References
14 Ionic Liquids as Corrosion Inhibitors
14.1 Introduction
14.2 Inhibition of Metal Corrosion
14.3 Ionic Liquids as Corrosion Inhibitors
14.3.1 In Hydrochloric Acid Solution
14.3.2 In Sulfuric Acid Solution
14.3.3 In NaCl Solution
14.4 Conclusion and Future Trends
Acknowledgment
Abbreviations
References
15 Oleochemicals as Corrosion Inhibitors
15.1 Introduction
15.2 Corrosion. 15.2.1 Definition and Economic Impact
15.2.2 Corrosion Inhibitors
15.3 Significance of Green Corrosion Inhibitors
15.4 Overview of Oleochemicals. 15.4.1 Environmental Sustainability of Oleochemicals
15.4.2 Production/Recovery of Oleochemicals
15.5 Literatures on the Utilization of Oleochemicals as Corrosion Protection
15.6 Conclusions and Outlook
References
16 Carbon Nanotubes as Corrosion Inhibitors
16.1 Introduction
16.2 Characteristics, Preparation, and Applications of CNTs
16.3 CNTs as Corrosion Inhibitors
16.3.1 CNTs as Corrosion Inhibitors for Ferrous Metal and Alloys
16.3.2 CNTs as Corrosion Inhibitors for Nonferrous Metal and Alloys
16.4 Conclusion
Conflict of Interest
Acknowledgment
Abbreviations
References
17 Graphene and Graphene Oxides Layers Application as Corrosion Inhibitors in Protective Coatings
17.1 Introduction
17.2 Preparation of Graphene and Graphene Oxides
17.2.1 Graphene
17.2.2 N‐doped Graphene and Its Composites
17.2.3 Graphene Oxides
17.3 Protective Film and Coating Applications of Graphene
17.4 The Organic Molecules Modified Graphene as Corrosion Inhibitor
17.5 The Effect of Dispersion of Graphene in Epoxy Coatings on Corrosion Resistance
17.6 Challenges of Graphene
17.7 Conclusions and Future Perspectives
References
18 Natural Polymers as Corrosion Inhibitors
18.1 An Overview of Natural Polymers
18.2 Mucilage and Gums from Plants
18.2.1 Guar Gum
18.2.2 Acacia Gum
18.2.3 Xanthan Gum
18.2.4 Ficus Gum/Fig Gum
18.2.5 Daniella oliveri Gum
18.2.6 Mucilage from Okra Pods
18.2.7 Corn Polysaccharide
18.2.8 Mimosa/Mangrove Tannins
18.2.9 Raphia Gum
18.2.10 Various Butter‐Fruit Tree Gums
18.2.11 Astragalus/Tragacanth Gum
18.2.12 Plantago Gum
18.2.13 Cellulose and Its Modifications
18.2.13.1 Carboxymethyl Cellulose
18.2.13.2 Sodium Carboxymethyl Cellulose
18.2.13.3 Hydroxyethyl Cellulose
18.2.13.4 Hydroxypropyl Cellulose
18.2.13.5 Hydroxypropyl Methyl Cellulose
18.2.13.6 Ethyl Hydroxyethyl Cellulose or EHEC
18.2.14 Starch and Its Derivatives
18.2.15 Pectin
18.2.16 Chitosan
18.2.17 Carrageenan
18.2.18 Dextrins
18.2.19 Alginates
18.3 The Future and Application of Natural Polymers in Corrosion Inhibition Studies
References
19 Synthetic Polymers as Corrosion Inhibitors
19.1 Introduction
19.2 General Mechanism of Polymers as Corrosion Inhibitors
19.3 Corrosion Inhibitors – Synthetic Polymers
19.4 Conclusion
Useful Links
References
20 Epoxy Resins and Their Nanocomposites as Anticorrosive Materials
20.1 Introduction
20.2 Characteristic Properties of Epoxy Resins
20.3 Main Commercial Epoxy Resins and Their Syntheses. 20.3.1 Bisphenol A Diglycidyl Ether (DGEBA)
20.3.2 Cycloaliphatic Epoxy Resins
20.3.3 Trifunctional Epoxy Resins
20.3.4 Phenol‐Novolac Epoxy Resins
20.3.5 Epoxy Resins Containing Fluorine
20.3.6 Epoxy Resins Containing Phosphorus
20.3.7 Epoxy Resins Containing Silicon
20.4 Reaction Mechanism of Epoxy/Amine Systems
20.5 Applications of Epoxy Resins
20.5.1 Epoxy Resins as Aqueous Phase Corrosion Inhibitors
20.5.2 Epoxy Resins as Coating Phase Corrosion Inhibitors
20.5.3 Composites of Epoxy Resins as Corrosion Inhibitors
20.5.4 Nanocomposites of Epoxy Resins as Corrosion Inhibitors
20.6 Conclusion
Abbreviations
References
Index. a
b
c
d
e
f
g
h
i
k
l
m
n
o
p
q
r
s
t
u
v
x
WILEY END USER LICENSE AGREEMENT
Отрывок из книги
Edited by
.....
This corrosion can be referred to as “intercrystalline corrosion”/“interdendritic corrosion” as tensile stress causes it along the grain or crystal boundaries. It might also be known as “intergranular stress corrosion cracking” and “intergranular corrosion cracking.” These corrosive attack prefers interdendritic paths. A microstructure examination using a microscope is needed for recognizing this degradation; however, at times, it is recognizable with eyes as in weld decay. The composition’s local differences like coring in alloy castings lead to this type of corrosion. The mechanism includes precipitation in grain boundaries like in the case of precipitating chromium carbides in steel. Intermetallic segregation at grain boundaries in aluminum is called “exfoliation.” This corrosion type might be prevented and controlled by using mild steel, low carbon type like using post‐weld treatment, etc.
Such a cracking occurs by the simultaneous action of a corrodent and sustained tensile stress. This bars the corrosion‐less sections, intercrystalline or trans‐crystalline corrosion, which might destroy an alloy without any stress. It is accompanied with hydrogen embrittlement. It might be a conjoint action of a susceptible material, a specific chemical species, and tensile stress. Sedriks and Turnbull reviewed the standard SCC testing [19–20]. Time‐consuming techniques, bulky specimens, and expensiveness limit the usage of SCC monitoring techniques. Stress corrosion cracking might be prevented by avoiding chemical species that causes it, controlling hardness and stress, using un‐crackable materials specific to environment and temperature/potential control of operation.
.....