Corrosion Policy Decision Making
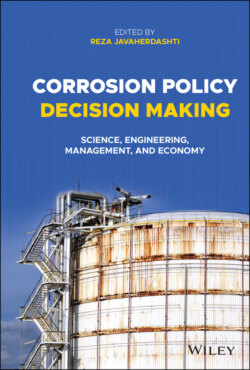
Реклама. ООО «ЛитРес», ИНН: 7719571260.
Оглавление
Группа авторов. Corrosion Policy Decision Making
Table of Contents
List of Tables
List of Illustrations
Guide
Pages
Corrosion Policy Decision Making. Science, Engineering, Management, and Economy
Preface
Authors and Contributors
1 Introduction
References
Notes
2 A Short Review of Some Important Aspects of the Science of Corrosion
2.1 Introduction
2.1.1 Essentials of Electrochemical Corrosion
2.1.2 Prediction of Corrosion
2.1.2.1 Standard Hydrogen Electrode/Electrochemical Series
2.1.2.2 Galvanic Series
2.1.2.3 Pourbaix Diagrams
2.2 Important Technical Treatment Strategies for Corrosion Treatment
2.2.1 Design Modification‐change/Materials Selection
2.2.2 Chemical Treatment
2.2.3 Electrical Treatment
2.2.4 Mechanical Treatment
2.2.5 Physical Treatment. 2.2.5.1 Paints, Coating Systems, and Premature Destruction in Industrial Facilities
2.2.5.2 Features of Substrate
2.2.5.3 Characteristics of the Environment and Local Features
2.2.5.3.1 Primer
2.2.5.3.2 Intermediate Layers
2.2.5.3.3 Topcoat
2.2.5.4 Paints Quality Control
2.2.5.5 Paint Warehousing and Storage
2.2.5.6 Role of Executors and Contractors
2.2.5.7 Surface Preparation
2.2.5.8 Technical Painting Operations
2.2.5.9 Inspection and Management
2.3 Conclusion
References
Notes
3 Smart Corrosion Management Elements
3.1 Introduction
3.1.1 Risk, Importance, and How They Are Interrelated?
3.1.2 Corrosion Management: What It Is and What It Is Not
3.1.3 Management of Corrosion
3.1.3.1 Corrosion Reactions Geometry
3.1.3.2 Failure
3.1.3.3 Corrosion Prevention and Corrosion Control
3.1.3.4 CM Model
3.1.4 Phase 1: Definition
3.1.5 Phase 2: Application
3.1.6 Phase 3: Monitoring
3.1.7 Phase 4: Feedback
3.1.7.1 Corrosion Cost Estimation Model
3.1.7.2 Corrosion Knowledge Management (CKM)
3.2 Management of Corrosion and COVID19
3.3 Environment
3.4 Application of Management of Corrosion Scheme to Underground Fire Water Ring4
3.5 Damage Management
3.6 Algorithm
3.7 Final Remarks
References
Notes
4 Economics and Corrosion
4.1 Introduction
4.2 Economics
4.2.1 What Is Economics
4.2.2 Gross Domestic Product
4.2.2.1 The Expenditure Approach
4.2.2.2 The Income Approach
4.2.2.3 The Value‐Added Approach
4.2.2.4 Income, Consumption, Saving, and Investment
4.2.2.4.1 Investment
4.2.2.5 Gross National Product
4.2.3 Introduction to National Account
4.2.3.1 Production Account, the Intermediate Consumption, and the Consumption of Fixed Capital
4.2.4 Net Present Value (NPV) and Net Future Value (NFV)
4.2.5 Input–Output Model in Economics
4.2.5.1 Technical Coefficients
4.2.5.2 Price and the Input–output Table
4.2.5.3 Dynamic Input–output Analysis
4.2.6 Depreciation, Consumption of Fixed Capital, or Corrosion
4.3 Corrosion Economics
4.3.1 Input–output Model in Corrosion
4.3.1.1 Matrix of Technical Coefficients
4.3.1.2 Matrix of Capital Coefficients
4.3.1.3 Input–output Model
4.3.1.4 Final Demand
4.3.1.5 World I, World II, World III
4.3.1.6 Estimating Corrosion Cost by Battelle
4.3.1.6.1 The Direct Cost of Corrosion per Unit of Output
4.3.1.6.2 Total Direct Costs of Corrosion
4.3.1.6.3 Direct and Indirect per Unit Costs of Corrosion
4.3.1.6.4 Total Direct and Indirect Costs of Corrosion
4.3.2 Life Cycle Cost (LCC)
4.3.2.1 Life‐Cycle Cost Model
4.3.2.1.1 The Dr. Reddy Formulation
4.3.2.1.2 The Professor Adeli Formulation
4.4 Corrosion and Sustainability
4.5 Conclusion
4.6 Summary
References
Notes
5 Effective Management of Process Additives (EMPA)
5.1 Introduction
5.2 A Gas Plant
5.3 Utilities
5.4 Process Additives (Chemicals)
5.5 Effective Management of Process Additives (EMPA)
5.5.1 Production Costs
5.5.2 Quality Control
5.5.3 Corrosion
5.5.4 Energy
5.5.5 Environment
5.5.6 Process Issues
5.5.6.1 Production Reduction
5.5.6.2 Off‐spec Products
5.5.6.2.1 Industrial Case One: Is Steam Condensate Deoiling and Polishing Package an Important Unit Operation?
5.5.6.2.2 Industrial Case Two: A Gas Heater Tube Failure that Influenced A Steam Generation and Distribution System
5.5.6.2.3 Increase MU Water Flowrate
5.5.6.2.4 Industrial Case Three: Corrosion in a Stabilizer Column due to Poor Chemical Performance in WWTP
5.5.6.3 Operation History 1
5.5.6.4 Operation History 2
5.5.6.4.1 Industrial Case Four: Corrosion in Seawater Thermal Desalination (Chlorination and Dechlorination of Seawater)
5.5.6.4.2 Industrial Case Five: Corrosion in the Boiler Due to Improper Chemical Control in the Face of an Operational Error
5.5.6.4.3 Industrial Case Six: Corrosion in Desalinated Water Distribution Pipelines Due to Remineralization Problems
5.5.6.5 Operation History 3
5.5.6.6 Operation History 4
5.6 Misleading Trends with Corrosion Conclusions
5.6.1 Phosphate Solution Preparation (Boiler Internal Treatment)
5.6.2 Putting A Kettle‐type Reboiler into Service that Has Been Under Maintenance
5.6.3 Problems in Sampling from Deaerator and Oxygen Scavenger Analyzation
5.6.4 Problems in Sampling and Analyzing Specific Conductivity from Demineralized Water
5.6.5 An Improper Sample Point and Mistake in Determining Free Residual Chlorine
5.7 Chemicals, Their Corrosion, and Impacts of Their Corrosions on the Environment
5.7.1 Operation History 5
5.8 Configuring EMPA
5.9 Setting up an EMPA
5.9.1 Description of Activities
5.9.1.1 Selection
5.9.1.2 Operation History 6
5.9.1.3 Operation History 7
5.9.1.4 Operation History 8
5.9.1.5 Operation History 9
5.9.1.6 Procurement
5.9.1.7 Operation History 10
5.9.1.8 Operation History 11
5.9.1.9 Delivery
5.9.1.10 Operation History 12
5.9.1.11 Operation History 13
5.9.2 Storage
5.9.2.1 Operation History 14
5.9.2.2 Operation History 15
5.9.2.3 Operation History 16
5.9.2.4 Operation History 17
5.9.2.5 Operation History 18
5.10 Consumption
5.10.1 Operation History 19
5.10.2 Operation History 20
5.10.3 Operation History 21
5.10.4 Operation History 22
5.10.5 Operation History 23
5.10.6 Operation History 24
5.10.7 Operation History 25
5.10.8 Operation History 26
5.10.9 Operation History 27
5.10.10 Operation History 28
5.11 Reporting
5.12 Documentation
5.13 Summary
Abbreviations
References
Note
6 Application of TRIZ for Corrosion Management
6.1 Introduction
6.2 Basic Structure of TRIZ
6.2.1 The Essence of TRIZ in 50 Words
6.3 Level of Invention
6.4 History of TRIZ
6.5 About the Founder of TRIZ. 6.5.1 Genrich Saulovich Altshuller
6.6 Contradiction as a Means to Formulate an Inventive Problem
6.7 Procedure of Inventive Design
6.8 Concept Development Using TRIZ
6.9 Contradiction Matrix (39 × 39)
6.9.1 List of the 39 Features
6.9.2 List of the 40 Principles
6.10 Using the TRIZ Matrix
6.10.1 TRIZ Problem Solving Methodology
6.10.2 Reality of the “Four‐Box Scheme” Theory
6.11 Physical Contradiction Resolution
6.12 Ideality and the Ideal Final Result (IFR)
6.13 TRIZ Crossover QMS
6.14 The Evolutionary S‐Curve
6.15 Nine Windows
6.16 Trends of Engineering System Evolution
6.17 Geometric Evolution of Linear Constructions
6.18 Trimming. 6.18.1 Making Things Better and Less Expensive
6.19 Input–Output–Trimming Operator (I–O–T)
6.20 Resource Analysis
6.21 Function Analysis
6.22 Substance‐Field Analysis
6.23 Tool‐Object‐Product (TOP) Function Analysis
6.24 Generic Model of a Function
6.24.1 Precise Description of a Function
6.24.2 Link between Functions
6.24.3 Increasing Effectiveness of Function Analysis
6.25 TRIZ Offers Five Basic Function Models
6.26 Psychological Inertia
6.27 Size‐Time–Cost Operator
6.28 Applying the 40 Inventive Principles in Corrosion Management
6.29 Conclusion
6.30 Glossary of TRIZ Terms
6.A TRIZ Contradiction Table
References
7 Environmental Impacts of Corrosion and Assessment Strategies
7.1 Introduction
7.1.1 Characterization of the Disaster
7.1.2 Why Environment?
7.1.3 Corrosion Impact and Corrosion Effect
7.1.4 Modeling Environmental Impacts
7.1.4.1 Necessary Elements for Construction of Corrosion Impact Modeling
7.2 Some Uses of Rule 365
7.2.1 Application of Rule 365 to Assess Corrosion Effects
7.3 Conclusions
References
Notes
Index. b
c
d
e
f
g
i
l
n
o
p
r
t
u
z
WILEY END USER LICENSE AGREEMENT
Отрывок из книги
Edited by
.....
Figure 2.8 Paint degradation on various substrates. (a) Rust on stainless steel in an oil platform in the Persian Gulf. (b) Rust on water‐line copper pipes in a gas processing unit. (c) Paint defect on cast iron.
.....