Gas Insulated Substations
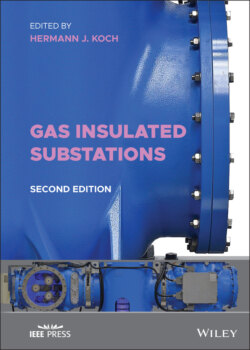
Реклама. ООО «ЛитРес», ИНН: 7719571260.
Оглавление
Группа авторов. Gas Insulated Substations
Table of Contents
List of Tables
List of Illustrations
Guide
Pages
Gas‐Insulated Substations
Editor Biography
Contributors
Foreword of Editor
Foreword PES Substations Committee
Foreword GE Grid Solutions
Foreword Hitachi Energy
Foreword Siemens Energy
Acknowledgements
1 Introduction
1.1 General
1.1.1 Organization
1.1.2 Experts of K2 and Location of Tutorial Presentations
1.1.3 Content of the Tutorial
1.2 Definitions
1.2.1 In IEEE and IEC Standards
1.2.2 Gas‐Insulated Metal‐Enclosed Switchgear
1.2.3 Compartment of GIS
1.2.4 Design Pressure of Enclosures
1.2.5 Gas Monitoring Systems
1.2.6 Gas Leakage Rate (Absolute)
1.2.7 Gas Leakage Rate (Relative)
1.2.8 Gas Pass Through Insulator
1.2.9 Gas Zone
1.2.10 Local Control Cubicle (or Cabinet) (LCC)
1.2.11 Support Insulator
1.2.12 Partition
1.2.13 Power Kinematic Chain
1.2.14 Design Pressure of Enclosures
1.2.15 Relative Pressure Across the Partition
1.2.16 Operating Pressure of Pressure Relief Device
1.2.17 Routine Test Pressure of Enclosures and Partitions
1.2.18 Type Test Pressure of Enclosures and Partitions
1.2.19 Rated Filling Pressure pre
1.2.20 Bushing
1.2.21 Main Circuit
1.2.22 Auxiliary Circuit
1.2.23 Design Temperature of Enclosures
1.2.24 Service Period
1.2.25 Transport Unit
1.2.26 Mixed Technologies Switchgear (MTS)
1.2.27 Disruptive Discharge
1.2.28 Fragmentation
1.2.29 Functional Unit
1.3 Standards and References. 1.3.1 Standards
1.3.2 Current Standards Most Relevant to GIS
1.3.2.1 General
1.3.2.2 GIS Enclosures
1.3.2.3 GIS Systems Above 52 kV
1.3.2.4 Gas‐Filled Bushings
1.3.2.5 Common Clauses for Switchgear
1.3.2.6 Sulfur Hexafluoride (SF6) Gas
1.3.2.7 High Voltage Testing on Control Systems
1.3.2.8 High‐Voltage Circuit Breakers
1.3.2.9 Disconnect and Grounding (Earthing) Switches
1.3.2.10 Safety and Grounding
1.3.2.11 Application Guides for Circuit Breakers
1.3.2.12 Application Guides for GIS
1.3.2.13 Application Guides for SF6
1.3.2.14 Reliability Evaluations
1.3.2.15 Cable and Transformer Interfaces
1.3.2.16 Seismic Design
1.3.2.17 Control Cabinets
1.3.2.18 Gas‐Insulated Transmission Line (GIL)
1.4 Ratings. 1.4.1 General
1.4.2 Rated Maximum Voltage
1.4.3 Rated Insulation Level
1.4.4 Rated Power Frequency
1.4.5 Rated Continuous Current
1.4.6 Rated Short Time Withstand Current
1.4.7 Rated Peak Withstand Current
1.4.8 Rated Duration of Short Circuit
1.4.9 Rated Supply Voltages
2 Basic Information
2.1 History. 2.1.1 General
2.1.2 Steps of Development
2.1.2.1 Factory Preassembled and Tested Units
2.1.2.2 Operating Life ≥ 50 Years
2.1.2.3 Major Inspection Not Before 25 Years
2.1.2.4 Motor Operated Self‐Lubricated Mechanisms
2.1.2.5 Minimal Cleaning Requirements
2.1.2.6 Corrosion Resistance
2.1.2.7 Low Fault Probability – High Reliability
2.1.2.8 Protection against Aggressive Environmental Conditions
2.1.2.9 Seismic Resistance
2.1.2.10 Space Requirements Less Than 20% of AIS
2.2 Physics of Gas‐Insulated Switchgear
2.2.1 Electric Fields
2.2.2 Breakdown in Gases
2.2.3 Excitation and Ionization
2.2.4 Free Electrons
2.2.5 Mean Free Path
2.2.6 Electron/Gas Molecule Impact
2.2.7 Breakdown
2.2.8 Sulfur Hexafluoride
2.2.9 Electric Field Control in GIS
2.2.10 GIS Circuit Breakers
2.3 Reliability and Availability. 2.3.1 General
2.3.2 Historical View
2.3.3 CIGRE Survey
2.3.3.1 CIGRE GIS Survey 1994
2.3.3.2 CIGRE GIS Survey 2012
GIS Failures
2.3.4 Reliability GIS versus AIS
2.4 Design. 2.4.1 Overview
2.4.2 SF6 Gas
2.4.3 Enclosure
2.4.4 Principles
2.4.5 Operation
2.5 Safety. 2.5.1 General
2.5.2 Design and Erection Requirements
2.5.2.1 Platforms and Ladders
2.5.2.2 Monitoring Devices
2.5.2.3 Thermal Expansion
2.5.2.4 Cable Connection to GIS
2.5.3 Building Requirements
2.5.3.1 Load and Ceiling
2.5.3.2 Air Conditions
2.5.3.3 Arc Fault Overpressure
2.5.3.4 Pipelines
2.5.3.5 Walls
2.5.3.6 Windows
2.5.4 Grounding/Earthing Requirements related to Safety
2.5.5 Burn Through of Enclosure
2.5.6 Work Behind Pressurized Insulators
2.5.7 SF6 Release to Buildings
2.6 Grounding and Bonding. 2.6.1 General
2.6.2 GIS Versus AIS Grounding
2.6.3 GIS Enclosure Currents
2.6.4 General Rules for GIS Grounding
2.6.5 Very Fast Transients
2.6.6 GIS Grounding Connection Details
2.7 Factors for Choosing Gas‐Insulated Substations. 2.7.1 General
2.7.2 Factors
2.7.3 Power System
2.7.4 Environment
2.7.5 Economics
2.7.6 Conclusion
2.8 Sulfur Hexafluoride (SF6) 2.8.1 What is Sulfur Hexafluoride?
2.8.1.1 Greenhouse Effect
2.8.1.2 Features of SF6
2.8.2 Background Information
2.8.2.1 Sulfur Hexafluoride
2.8.2.2 The Chemical Bond
2.8.2.3 Use of SF6
2.8.2.4 Use in Electrical Equipment
2.8.2.5 Other Gases
2.8.2.6 Nonelectrical
2.8.2.7 Physical
2.8.2.8 Thermodynamic
2.8.2.9 Liquefaction
2.8.2.10 Electric
2.8.2.11 Eco‐toxicity
2.8.2.12 Greenhouse Gas
2.8.2.13 Environmental Impact
2.8.2.14 Emissions
2.8.2.15 Standards and Guides for Related Equipment
2.8.2.16 Tightness
2.8.2.17 Closed Pressure Systems
2.8.2.18 Sealed Pressure System
2.8.2.19 Controlled Pressure Systems
2.8.2.20 Monitoring System
2.8.2.21 Toxicity
2.8.2.22 Gas Categories
2.8.2.23 New SF6 Gas
2.8.2.24 Technical Grade SF6 Gas
2.8.2.25 Nonarced Gas
2.8.2.26 Normally Arced Gas
2.8.2.27 Heavily Arced Gas
2.8.2.28 Reuse of SF6
2.8.2.29 Not Suited for Reuse
2.8.2.30 General Safety Rules and Recommendations (see Table 2.14)
2.8.2.31 Protection of Personnel (see Table 2.15) 2.8.2.32 Training of Personnel Handling SF6 is Required
2.8.2.33 Storage and Transportation
2.8.2.34 Methods for Storage of SF6 (see Table 2.16) 2.8.2.35 Containers for Transportation of SF6 (see Table 2.17)
2.8.3 Producer and User of SF6
2.8.4 SF6 Gas Handling. 2.8.4.1 General
2.8.4.2 Introduction
2.8.4.3 Recovery/Reuse of SF6
Gas‐Handling Procedures
Procedure Description Modules
2.8.4.4 Reporting and User Agreements
2.8.4.5 Labeling
2.8.4.6 Training and Certification
Example of SF6 Handling
2.8.5 Gas‐Handling Equipment. 2.8.5.1 Gas Reclaimer
2.8.5.2 Gas Filters
2.8.5.3 Compressors
2.8.5.4 Measuring Devices
2.8.5.5 Evacuation and Filling
2.8.5.6 Storage
2.8.5.7 Gas Recovery Process
2.8.6 Life Cycle Assessment Case Study: Würzburg
2.8.6.1 Object of the LCA
2.8.6.2 Primary Energy
2.8.6.3 Space Consumption
2.8.6.4 Global Warming Potential
2.8.6.5 Acid Rain and Nitrification Potential
2.8.6.6 Conclusion
2.8.7 Kyoto Protocol
2.8.7.1 Requirement for Each Party
2.8.7.2 Environmental Aspects of SF6
2.8.8 Requirements for the Use of SF6
2.8.9 Moisture in SF6 gas
2.9 Alternative Gasses to SF6
2.9.1 Introduction
2.9.2 Motivation to Use Alternative Gases. 2.9.2.1 Why Alternative Gases to SF6
2.9.2.2 Alternative Gases to SF6 to Cut CO2 Emissions
2.9.2.3 SF6 Emission Rate and SF6 Capacity
2.9.2.4 Possible SF6 Emissions in the Lifecycle Process of Gas‐Insulated Equipment
2.9.3 Requirements of Alternative Gases. 2.9.3.1 Introduction
2.9.3.2 Environment
2.9.3.3 Performance
2.9.3.4 Health and safety
2.9.3.5 Applications
2.9.4 Characteristics of Different Alternative Gases for GIS
2.9.5 Field Experience with SF6 Alternatives
2.9.6 Transition Period SF6 to Alternative Gases
2.9.7 Organizations Dealing with SF6 and Alternative Gases for GIS
2.9.8 Summary
2.10 When to Use Gas‐Insulated Substations
2.10.1 Factors to Consider for GIS as a Substation Design Tool. 2.10.1.1 Personnel Safety
2.10.1.2 Physical Space
2.10.1.3 Public Safety
2.10.1.4 Physical Security
2.10.1.5 Climatic Conditions and Wildlife
2.10.1.6 Extreme and Severe Weather Events
2.10.1.7 Earthquakes
2.10.1.8 Pollution
2.10.1.9 Corrosion
2.10.1.10 Availability
2.10.1.11 Maintainability
2.10.1.12 Meantime of Maintenance and Maintenance Cost
2.10.1.13 Meantime of Maintenance or Repair
2.10.1.14 Life Cycle Cost
2.10.2 When to Consider GIS. 2.10.2.1 Greenfield Projects. 2.10.2.1.1 EHV Transmission Substations
2.10.2.1.2 When Significant Grading and/or Soil Structure Enhancement Required
2.10.2.1.3 When Nonstandard Transmission Rights‐of‐Way Exist
2.10.2.1.4 When Aesthetics and Visual impact are Key Factors
2.10.2.1.5 When Transmission Access Locations are Complicated
2.10.2.1.6 When Reduction of Schedule Risks is Necessary
2.10.2.1.7 When Resiliency and Physical Security are Key Factors
2.10.2.1.8 When All Price Competitive Solutions are Considered
2.10.2.1.9 When Reliability and Availability are Key Factors
2.10.2.2 Brownfield Projects
2.10.2.2.1 When Expanding an Existing Substation
2.10.2.2.2 When New Transmission Access is Needed
2.10.2.2.3 When Constructability is Difficult
2.11 Comparison High Voltage and Medium Voltage AIS, MTS and GIS
2.11.1 AIS Technology Characteristics
2.11.2 GIS Technology Characteristics
2.11.3 Design and Construction of AIS
2.11.4 Design and Construction of GIS
2.11.5 Considerations for Selection AIS or GIS Technology
2.11.6 Power System Considerations
2.11.7 Environmental Considerations
2.11.8 Economic Considerations
2.11.9 Life Expectancy
2.11.10 Construction
2.11.11 Building Requirements
2.11.12 Equipment Installation
2.11.13 Grounding
2.11.14 Project Complexity
2.11.15 Expandability
2.11.16 Testing and Commissioning
2.11.17 Environmental Impact
2.11.18 Model Calculation for 145 kV
2.11.19 Safety
2.11.20 Security
2.11.21 Community Acceptance
2.11.22 EMF and a Potential Impact
2.11.23 Conclusion
References Chapter 2
3 Technology
3.1 General
3.1.1 Materials
3.1.2 Steel
3.1.3 Aluminum
3.2 Modular Components, Design, and Development Process. 3.2.1 Modular Design
3.2.1.1 Three‐Phase Enclosure
Circuit Breaker Module
Three‐Position Switch, Three‐Phase Encapsulated Module
Three‐Phase Encapsulated High‐Speed Grounding Switch Module
Three‐Phase Encapsulated Voltage Transformer Module
Three‐Phase Encapsulated Current Transformer Module
Three‐Phase Overhead Line Connection Module
Three‐Phase Encapsulated Cable Connection Module
Three‐Phase Encapsulated Surge Arrester Module
Three‐Phase Encapsulated Bus Bar
3.2.1.2 Single‐Phase Enclosure
Circuit Breaker Module
Disconnector and Ground Switch Module
Load‐Break Disconnector Switch Module
Single‐phase Current Transformer Module
Single‐phase Voltage Transformer Module
3.2.2 Design Features
3.2.3 Design Process
3.3 Manufacturing. 3.3.1 General
3.3.2 GIS Factory
3.3.3 Insulating Parts
3.3.4 Operation Rods and Tubes
3.3.5 Machining of the Enclosure
3.3.6 Cleaning and Degreasing
3.3.7 Pressure and Gas Tightness Test
3.3.8 Painting Enclosures
3.3.9 Preassembly of Functional Units
3.3.10 Final Assembly
3.3.11 Quality Assurance
3.3.12 Regional Manufacturing
3.4 Specification Development. 3.4.1 Introduction
3.4.2 Specification Documentation. 3.4.2.1 General
3.4.2.2 Detailed One‐Line Diagram
3.4.2.3 Primary Equipment Data
General Criteria
GIS Equipment Ratings and Service Conditions
Enclosure Design – Single Phase or Three Phase
Specific Equipment Requirements
Circuit Breakers
Disconnect Switches, Grounding Switches and Operators
Gas System and Gas Zone Configurations
Current Transformers
Inductive Voltage Transformers
Metal‐Enclosed Surge Arresters
SF6 Gas‐to‐Air Bushings
GIS to Cable Connections
GIS to GIB/GIL Connections
Power Transformer Bushing Connections
Local Control and Marshaling Cabinets
Ladders, Platforms, Stairs, and Walkways
3.4.2.4 Secondary Equipment Data
Protection, Control, and Monitoring Requirements
Relaying and Control Cabinets
Logic Diagrams for Numerical Relays
SCADA Interface Points
Wiring Connection and Interconnection Requirements
Annunciation and Alarms
Mimic Bus Diagram
3.4.2.5 Engineering and Logistics Studies. Engineering Studies
Transient Recovery Voltage (TRV) Conditions
Transient Over Voltage (TOV) Conditions
Very Fast Transient (VFT) Conditions
Insulation Coordination Studies
Thermal Rating Calculations
Effects of Ferro‐Resonance
GIS Resistance and Capacitance
Seismic Calculations
Electromagnetic Compatibility
Civil Engineering Aspects
Grounding and Bonding
Logistics Studies
3.4.2.6 Standards and Regulations
3.4.2.7 Test and Inspections
3.4.2.8 Project Deliverables
3.4.2.9 Project Specific Requirements
3.5 Instrument Transformers. 3.5.1 Current Transformers
3.5.2 Voltage Transformers
3.5.3 Transient Overvoltages of a CT and VT
3.6 Interfaces
3.6.1 Direct Connection Between Power Transformers and GIS
3.6.2 Cable Connections for Gas‐Insulated Switchgear for Rated Voltage above 52 kV
3.6.3 Bushings. 3.6.3.1 Purpose of Bushings
3.6.3.2 Bushing Standards
3.6.3.3 Bushing Rating
3.6.3.4 Bushing Construction
3.6.3.5 Application in Contaminated Environment
3.6.3.6 High Altitude Application
3.6.3.7 Bushing Terminal Loading
3.6.3.8 Gas Monitoring
3.6.4 Interface Project Applications
3.6.4.1 Cable Connection to GIS
3.6.4.2 Gas to Air Bushing Connection
3.7 Gas‐Insulated Surge Arresters
3.8 Gas‐Insulated Bus. 3.8.1 General
3.8.2 Three‐Phase Insulated Bus Duct
3.8.3 Single‐Phase Insulated Bus Duct
3.8.4 Bus Duct to Connect Overhead Lines
3.8.5 Bus Duct to Connect Circuit Breakers
3.8.6 Bus Duct to Connect Transformers
3.8.7 Bus Duct to Connect Cables
3.8.8 Bus Duct to Underpass Overhead Lines
3.8.9 Bus Duct Above Ground
3.8.10 Bus Duct Trench Laid
3.8.11 Bus Duct Laid in a Tunnel
3.8.12 Bus Duct Directly Buried
3.8.13 Shipment on Site
3.8.14 Assembly on Site
3.9 Guidelines for GIS. 3.9.1 General
3.9.2 Scope
3.9.3 GIS Guide Content
3.9.4 Different Layouts and One‐Line Diagrams
3.9.5 Benefits and Drawbacks of GIS
3.9.6 Local Control Cabinets (LCC)
3.9.7 Partitions
3.9.8 GIS Grounding
3.9.9 Partial Discharge (PD) Measurements
References
4 Control and Monitoring
4.1 General
4.2 GIS Monitoring
4.2.1 Gas Monitoring
4.2.1.1 Gas Monitoring Practices
4.2.2 Partial Discharge
4.2.2.1 Defect Types
4.2.2.2 Partial Discharge (PD) Discharge Measurements
Electrical Methods
Acoustic Methods
Chemical Techniques
4.2.3 PD Monitoring Strategies
4.2.4 Circuit Breaker Monitoring
4.2.5 Other Monitoring
4.3 Local Control Cabinet. 4.3.1 General
4.3.2 Bay Controller
4.3.3 Control Schemes. 4.3.3.1 Control Mode Selection
Off Mode
Local (BCU) Mode
Remote Level Mode
4.3.3.2 Interlocking
4.3.3.3 Synchronism and Voltage Selection
4.3.3.4 Autoreclosing and Related Synchrocheck Functions
4.3.3.5 Pole Discrepancy Monitoring (for Single‐Pole CB)
4.4 Digital Communication. 4.4.1 General
4.4.2 Basic Digital Communication Standard
4.4.2.1 Communication Requirements (Part 5)
4.4.3 Switchgear‐Related Communication Standard. 4.4.3.1 General
4.4.3.2 Location of Controls
4.4.3.3 Operation of Switchgear. Opening/Closing Command
Calculation of Operation Time
Measuring Operation Time
4.4.3.4 Type Tests
4.4.3.5 Routine Tests
4.4.4 Normative References. 4.4.4.1 Digital Communication‐Related Standards
IEC 61850
IEC 62271‐3:2006
4.4.5 Classifications. 4.4.5.1 Timing Requirements. Opening and Closing Times for Circuit Breakers
Opening Operation
Closing Operation
References
5 Testing
5.1 General
5.2 Type Tests
5.2.1 Dielectric Tests
5.2.2 Measurement of the Resistance of the Main Circuits
5.2.3 Temperature Rise Tests
5.2.4 Short‐Time Withstand Current and Peak Withstand Current Tests
5.2.5 Tightness Tests
5.2.6 Low‐ and High‐Temperature Tests
5.2.7 Proof Tests for Enclosures
5.2.8 Circuit Breaker Design Tests
5.2.9 Switch Operating Mechanical Life Tests
5.3 Routine Tests
5.3.1 Dielectric Tests
5.3.2 Measurement of the Resistance of the Main Circuits
5.3.3 Tightness Tests
5.3.4 Pressure Tests of Enclosures
5.3.5 Mechanical Operation Tests
5.3.6 Tests on Auxiliary and Control Circuits
5.3.7 Pressure Tests on Partitions
5.4 Onsite Field Testing
5.4.1 Gas Leakage and Gas Quality (Moisture, Purity, and Density)
5.4.2 Electrical Tests: Contact Resistance
5.4.3 Electrical Tests: AC Voltage Withstand
5.4.4 Electrical Tests: AC Voltage Withstand Requirements and Conditions
5.4.5 Electrical Tests: AC Voltage Withstand Configurations and Applications
5.4.6 Electrical Tests: DC Voltage Withstand Tests
5.4.7 Mechanical and Electrical Functional and Operational Tests
5.4.8 Connecting the GIS to the Electrical System
5.5 Guidelines for Onsite Tests
5.5.1 General
5.5.2 Circuit Breaker Operational Tests from Local Control Cabinet and from Individual Mechanism
5.5.3 Disconnect Switch (DS), Grounding Switch (GS) Operational Tests from Local Control Cabinet and from Individual Mechanism
5.5.4 Current Transformer
5.5.5 Voltage Transformer
5.6 Best Practice for On‐Site Field Testing
5.6.1 Gas Leakage
5.6.2 Gas Quality
5.6.3 Power Frequency AC Withstand Voltage. 5.6.3.1 Introduction
5.6.3.2 Pretesting Precautions
5.6.3.3 Testing Existing and New Equipment
5.6.3.4 Testing GIS Equipment Including Cable Connections
5.6.3.5 Air Electrical Clearances During Testing
5.6.3.6 Testing GIS Equipment Including Cable Connections
5.6.3.7 Testing GIS Equipment Including Surge Arresters Connections
5.6.3.8 Locating an Internal Failure
References
6 Installation
6.1 General
6.2 Installation. 6.2.1 Introduction
6.2.2 Safety Considerations and Assembly Tips
6.2.3 General Project Planning Outline
6.2.4 Future GIS Expansion Considerations
6.2.5 Advance Planning and Preliminary Site Evaluation
6.2.5.1 Document Control
6.2.5.2 An Initial Site Assessment and Survey
6.2.5.3 Site Transportation Access
6.2.5.4 Security
6.2.5.5 Material Storage
6.2.5.6 Environment, Health and Safety Plan (EHS)
6.2.5.7 Environmentally Sensitive Areas
6.2.5.8 Specialized Equipment Requirements
6.2.6 Training. 6.2.6.1 General
6.2.6.2 Construction and Assembly Crew
6.2.6.3 Operational and Maintenance Crew
6.2.6.4 Dispatch Crew
6.2.6.5 Other On‐Site Personnel Not Directly Involved with Assembly
6.2.7 Material Receipt and Control. 6.2.7.1 General
6.2.7.2 Bus Bar, Disconnect Ground Switch, Circuit Breaker Shipping
6.2.7.3 Incoming Material Inspection
6.2.7.4 SF6 Gas Management
6.2.8 Installation/Assembly Instructions. 6.2.8.1 General
6.2.8.2 Shipping Covers
6.2.8.3 Large Pieces
6.2.8.4 Clean Bus and Flange
6.2.8.5 Lubricants and Sealants
6.2.8.6 Tools
6.2.8.7 Bus Bar Assembly
6.2.8.8 SF6 Gas Handling
6.2.8.9 Retro‐Fit
6.2.9 Gas‐Insulated Substation Tests. 6.2.9.1 Construction Visual Inspections
6.2.9.2 Control Cable
6.2.9.3 Bus Gas Leak Checks
6.2.9.4 Gas Density Monitor and Local Alarm Tests
6.2.9.5 Primary Circuit Resistance
6.2.9.6 SF6 Gas Quality Tests
6.2.9.7 Circuit Breaker Tests
Mechanism Stroke, Wipe Measurement
Open/Close Operation Including Anti‐pumping
Travel and Timing Test
Low Gas Tripping and Block Close Operations
6.2.9.8 Ground and Disconnect Switch and Circuit Breaker Interlock Tests
6.2.9.9 High‐Voltage Bus and Equipment Conditioning Tests
6.2.9.10 Instrument Transformer Tests
6.2.9.11 Other Tests/Records. AC Station Service Measurements, Heater and Control Cabinet Light Operations
Final Circuit Breaker Counter Readings
Turnover Gas Zone Density Readings
6.2.10 Commissioning, Energization, and Outage Plan
6.2.11 Maintenance and Turnover Documents
6.3 Energization: Connecting to the Power Grid. 6.3.1 Grid Connection Considerations (Long‐Term Planning)
6.3.2 GIS Grounding System
6.3.3 Gas Zones
6.3.4 Operational Considerations
References
7 Operation and Maintenance
7.1 General
7.2 Operation of a Gas‐Insulated Substation. 7.2.1 General
7.2.2 Circuit Breaker
7.2.3 Disconnect Switches
7.2.4 Nonfault‐Initiating (Maintenance) Grounding Switches
7.2.5 High‐Speed (Fault‐Initiating) Grounding Switches
7.2.6 Three‐Position Disconnect/Grounding Switches
7.2.7 Voltage Transformers (VTs)
7.2.8 Current Transformers (CTs)
7.2.9 Switch Viewports
7.2.10 Gas Compartments and Zones
7.2.11 Interlocking
7.2.12 Local Control Cabinets (LCCs)
7.2.13 Alarms
7.2.14 Switching a GIS
7.2.15 Conclusion
7.3 Maintenance. 7.3.1 General
7.3.2 Common Maintenance Procedures
7.3.2.1 Visual Inspection
7.3.2.2 Minor Inspection
7.3.2.3 Major Inspection
7.4 SF6 Gas Leakage Repair
7.5 Repair. 7.5.1 Nature and Sources of Faults
7.5.2 Repair Times and Service Continuity
7.5.3 Examples of Repair
7.6 Extensions. 7.6.1 General
7.6.2 Work To Be Done When an Extension Is Planned from Initial Design Stage
7.6.3 Work To Be Done When an Extension Is Not Anticipated from Initial Design Stage
7.6.4 Service Continuity During Extension Work
7.6.5 Testing of Interface
7.7 GIS Retrofit or Upgrade. 7.7.1 Introduction
7.7.2 Challenges with Old GIS
7.7.3 Retrofit or Upgrade
7.7.3.1 Reliability
7.7.3.2 Safety
7.7.3.3 State‐of‐the‐Art Technology
7.7.3.4 Project Execution
7.7.3.5 Investment
7.8 Overloading and Thermal Limits. 7.8.1 General
7.8.2 Design for Continuous Rating Current
7.8.3 Determination of the Limits
7.8.4 Maximum Continuous Load Current
7.8.5 Short‐Time Overload Capability
7.8.6 Equations/Formulae to Calculate Overloads
7.9 Maintenance and Operations Pointers. 7.9.1 Design Considerations – Direct GIS Connections to Cable and Transformers
7.9.1.1 Testing
7.9.1.2 Repairs/Replacement
7.9.1.3 Spare Power Transformers
7.9.2 Construction Approach
7.9.3 Construction Planning
7.9.4 Installation Crew Training
7.9.5 Quality Assurance
7.9.6 SF6 Gas Management
7.9.7 Engineering Considerations
7.9.8 Spare Parts and Special Tool Accountability
7.9.9 Device Labeling
7.10 Lessons Learned. 7.10.1 Operator/Dispatcher Training
7.10.2 Improper Rigging – Dropped Bus
7.10.3 Retrofit Projects – Bench Marking on Retrofit Projects
7.10.4 Measurements Before Assembly
7.10.5 Bus Assembly Double Checks
7.10.6 Circuit Breaker Locking Pins
References
8 Applications
8.1 General
8.2 Typical GIS Layouts
8.2.1 Single Bus Arrangement
8.2.2 Double Bus Arrangement
8.2.3 Ring Bus Arrangement
8.2.4 H‐Scheme Arrangement
8.2.5 Breaker and a Half Arrangement
8.3 Reference Projects. 8.3.1 500 kV Indoor GIS and 115 kV AIS. 8.3.1.1 Introduction
8.3.1.2 Technical Data
8.3.1.3 Electrical Layout
8.3.1.4 Physical Layout
8.3.2 115 kV GIS Switching Station. 8.3.2.1 Introduction
8.3.2.2 Technical Data
8.3.2.3 Electrical Layout
8.3.2.4 Physical Layout
8.3.2.5 Aerial View
8.3.3 345 kV and 4000 A Indoor Expendable Ring Bus GIS. 8.3.3.1 Introduction
8.3.3.2 Technical Data
8.3.3.3 Electrical Layout
8.3.3.4 Physical Layout
8.3.4 69 kV and 3150 A Indoor Double Bus GIS. 8.3.4.1 Introduction
8.3.4.2 Technical Data
8.3.4.3 Electrical Layout
8.3.4.4 Physical Layout
8.3.5 115 kV and 1200 A Container Ring Bus GIS. 8.3.5.1 Introduction
8.3.5.2 Technical Data
8.3.5.3 One Line Diagram
8.3.5.4 Physical Layout
8.3.6 115 kV and 2000 A Outdoor Single Bus GIS. 8.3.6.1 Introduction
8.3.6.2 Technical Data
8.3.6.3 Electrical Layout
8.3.6.4 Physical Layout
8.3.7 345 kV and 4000 A Indoor Breaker and Half‐Scheme GIS. 8.3.7.1 Introduction
8.3.7.2 Technical Data
8.3.7.3 Electrical Layout
8.3.7.4 Physical Layout
8.3.8 115 kV and 3150 A Indoor Ring Bus GIS. 8.3.8.1 Introduction
8.3.8.2 Technical Data
8.3.8.3 Electrical Layout
8.3.8.4 GIS Components
8.3.8.5 Physical Layout
8.3.9 69 kV and 2000 A, Indoor Ring Bus GIS. 8.3.9.1 Introduction
8.3.9.2 Technical Data
8.3.9.3 Electrical Layout
8.3.9.4 Physical Layout
8.3.9.5 Picture View
8.3.10 138 kV and 230 kV Outdoor Ring Bus GIS. 8.3.10.1 Introduction
8.3.10.2 Technical Data
8.3.10.3 Electrical One‐Line Diagram
8.3.10.4 Physical Layout
8.3.11 500 kV and 4000 A/8000 A Indoor Breaker and Third GIS. 8.3.11.1 Introduction
8.3.11.2 Technical Data
8.3.11.3 Electrical Layout
8.3.11.4 Physical Layout
8.3.12 69 kV and 1600 A Outdoor Single Bus GIS. 8.3.12.1 Introduction
8.3.12.2 Technical Data
8.3.12.3 Electrical Layout
8.3.12.4 Physical Layout
8.3.13 69 kV and 2000 A Underground GIS. 8.3.13.1 Introduction
8.3.13.2 Technical Data
8.3.13.3 Electrical Layout
8.3.13.4 Physical Layout
8.3.13.5 Photos of the Underground GIS
8.3.14 69 kV GIS under Severe Environment. 8.3.14.1 Introduction
8.3.14.2 Technical Data
8.3.14.3 Project Details
8.3.14.4 Physical Layout
8.4 GIS Case Studies
8.4.1 Public Service Electric and Gas Company – New Jersey. 8.4.1.1 230 kV, 80 kA Bergen Switching Station
8.4.2 Street House Project Study. 8.4.2.1 Metropolitan Area
8.4.2.2 GIL Technical Options
8.4.2.3 Street House Concept
8.4.2.4 Conclusion
8.4.3 City Junction Project Study. 8.4.3.1 Introduction
8.4.3.2 City Junction North Line
8.4.3.3 GIL Technical Options
8.4.3.4 Project Concept Study
Typical Solutions to Overcome Obstacles
Transfer Section from Overhead Line to GIL
Crossing the Highway Using Small Drilled Tunnels
Section with High‐Elevation Differences Along Highway Using a Large‐square Tunnel with Segments
Section with Narrow Space Using a Large‐Square Tunnel with Segments
Section Street Crossing Using a Large‐Square Tunnel on a Bridge
Section with Access Road Underpass Using a Large‐Square Tunnel with Segments
Undergrounding the Total Length by Using a Large Drilled Tunnel
8.4.3.5 Technical Design
Forced Ventilation
Forced Ventilation of a Deep Tunnel
Forced Ventilation of a Tunnel Closed to the Surface
Installation Process in a Tunnel
8.4.3.6 Conclusion
8.5 Mobile Substations. 8.5.1 General
8.5.2 Containerized GIS
8.5.3 Truck‐Mounted GIS. 8.5.3.1 General
8.5.3.2 Truck‐Mounted GIS of 72.5 kV
8.5.3.3 Truck‐Mounted GIS of 420 kV
8.5.3.4 Mobile High‐ and Medium‐Voltage Substations
8.5.4 Mobile Gas‐Insulated Substation. 8.5.4.1 General
8.5.4.2 Applications. Service Restoration
Project Support
Short‐Term Installation
8.5.4.3 Considerations. Physical Size. Stored
Installed
Weight. Stored
Installed
Equipment Layout
Equipment Connections
Personal Access
8.5.4.4 Mobile Gas‐Insulated Substation Applications. Transformer
Line Protection
Switch Bypass
8.5.4.5 Specifications
GIS
Trailer
8.5.4.6 Installation Plans
8.5.4.7 Conclusion
8.6 Mixed Technology Switchgear (MTS) 8.6.1 Introduction
8.6.2 Definition of MTS
8.6.3 MTS Design Features and Applications
8.6.4 MTS Application Examples
8.6.5 Conclusion
8.7 Future Developments. 8.7.1 Reduction of Size
8.7.2 Simpler Design
8.7.3 Life Cycle Cost Evaluations
8.7.4 Functional Specification
8.7.5 Intelligent GIS
8.7.6 Integrated Electronic Devices
8.7.7 Rogowski Coil
8.7.8 Capacitive Divider
8.8 Underground Substations
8.8.1 Introduction
8.8.2 Critical Aspects of Designing Underground Substations. 8.8.2.1 Soil and Ground Water
8.8.2.2 Fire Protection
8.8.2.3 Dust and Fresh Air Protection
8.8.2.4 Transformer Termination
8.8.2.5 Ventilation and Humidity
8.8.2.6 Noise Emissions
8.8.2.7 Electromagnetic Field
8.8.2.8 Control Room
8.8.2.9 People Protection
8.8.3 Risk and Common Issues
8.8.4 Architectural Concepts. 8.8.4.1 Introduction
8.8.4.2 Principal Solutions
8.8.4.3 Architectural Solutions
8.8.4.4 Model City Development Solution
8.8.4.5 Industrial Aesthetic Solution
8.8.5 Economics of Underground Substations
8.8.6 Typical Project Schedule
8.8.7 Conclusion
8.9 Special Substation Buildings
8.9.1 Introduction
8.9.2 Examples. 8.9.2.1 110/10 kV GIS Substation in City Centre
8.9.2.2 110/10 kV GIS Substation at Four Building Levels
8.9.2.3 Downtown Business District
8.9.2.4 Hydropower Plant
8.9.2.5 Hydropower Storage Plant
8.9.2.6 Substation Building at Desert Conditions. 132/11 kV Substation
8.9.2.7 Residential Area City Substation
8.9.2.8 Three‐Voltage‐Level substation
Three‐Voltage‐Level Substation 1
Three‐Voltage‐Level Substation 2
8.9.2.10 Monument Substation
8.9.2.11 City Center Transmission Substation
8.9.2.12 Schoolyard Substation
8.9.2.13 Remote Area Substation
8.9.2.14 Futuristic Harbor Substation
8.9.3 Conclusion
References
Note
9 Advanced Technologies
9.1 General
9.2 Environment. 9.2.1 Environmental Life Cycle Assessment. 9.2.1.1 Introduction
9.2.1.2 LCA Process
9.2.1.3 LCA Relevance to GIS
9.2.1.4 Industry Response to Environmental Impacts
9.2.1.5 Life Cycle Assessment (LCA) Studies
9.2.1.6 End‐of‐Life Recycling
9.2.2 Eco Design. 9.2.2.1 Introduction
9.2.2.2 Eco‐Design Approach
9.2.2.3 Life Cycle Analysis
9.2.2.4 Examples of Eco‐Design Improvements in GIS. Management of Hazardous Substances
Reduction of Joule Losses
SF6 Gas Management
End‐of‐Life Management
Example of LCA between Two Generations of GIS
9.2.3 Environmental Impact Case Study: Transmission Project Using GIL or XLPE Cables. 9.2.3.1 General
9.2.3.2 Toxic Materials
9.2.3.3 Thermal Impact
9.2.3.4 Maximum Enclosure Temperature
9.2.3.5 Recycling of Materials
9.2.3.6 Fire Risk
9.2.3.7 Smoke and Toxic Gases
9.2.3.8 Noises and Vibrations
9.2.3.9 Cooling and Ventilation Systems
9.3 Life Cycle Cost Analysis. 9.3.1 Introduction
9.3.2 Scope
9.3.3 Coordination
9.3.4 Methodology
9.3.4.1 Cost of Acquisition and Installation (CA)
9.3.4.2 Cost of Operation (CO)
9.3.4.3 Cost of Renewal/Disposal (CR)
9.3.4.4 Residual Value
9.3.5 Procedure
9.3.5.1 Present Value
9.3.5.2 Study Period
9.3.5.3 Discount Rate
9.3.5.4 Escalation/Inflation Rate
9.3.6 Finalized LCCA
9.3.7 Reliability, Availability, Failure Rates, and Cost
9.4 Insulation Coordination Study. 9.4.1 General
9.4.2 Overvoltage
9.4.2.1 Backflash
9.4.2.2 Detailed Steps Adopted for Calculation of Various Parameters
9.4.2.3 Effect of the Circuit Configuration on the Rise Times at the Station Entrance
9.4.3 Grounding
9.5 Very Fast Transients. 9.5.1 General
9.5.2 Very Fast Transients in GIS
9.5.2.1 Simulation of VFT Phenomena
9.5.2.2 VFT Overvoltage (VFTO)
9.5.2.3 VFTO and Insulation
9.5.2.4 VFTO‐Related Failures. Insulation Failure
Disconnector Failure [13]
Insulated Flanges and Cable Terminations [14]
Impact of VFTO on Other Power Apparatus [15]
9.5.3 Transient Enclosure Voltage
9.5.3.1 TEV Generation and Propagation
9.5.3.2 Shock Hazard
9.5.3.3 TEV‐Induced Interference and Control Wire Transients
9.6 Project Scope Development. 9.6.1 Engineering Planning
9.6.2 Planning the GIS Project Construction and Installation
9.6.3 Site Preparation
9.6.4 Installation of the New GIS
9.6.5 Installation of GIS Extensions
9.6.6 Equipment Access
9.7 Risk‐Based Asset Management of Gas‐Insulated Substations and Equipment. 9.7.1 Introduction
9.7.2 Scope
9.7.3 Methodology. 9.7.3.1 Existing and Required Performance
Thermal Capabilities
Failure Modes
Minor Faults (Type 1)
Minor Faults (Type 2)
Major Faults (Type 3)
Internally and Externally Caused Types of Faults
Degradation Mechanisms Affecting the Switchgear
Periodic Condition Assessment and Diagnostic Methods
Preventive Maintenance Assessments
Major Maintenance Assessment
Comprehensive Life Cycle Management Program
9.7.4 Assessing Risk. 9.7.4.1 Projecting Future Performance and Bridging Gaps with Risk Assessment
9.7.4.2 Types of Risks
9.7.4.3 Assessing Risk Levels
9.7.4.4 Availability
9.7.4.5 Probability of Occurrence
9.7.4.6 Impact
9.7.4.7 Risk Assessment Procedure (A Simple Algorithm Example)
9.8 Health and Safety Impact. 9.8.1 General
9.8.2 Risk of Burning
9.8.3 Risk of Breathing Toxic Gases
9.8.4 Risk of Touching Toxic Materials
9.8.5 Risk of Electric Shock
9.9 Electromagnetic Field. 9.9.1 General
9.9.2 Electric Field in Operation
9.9.3 Electric Field during Short Circuit
9.9.4 Magnetic Field in Operation
9.9.5 Magnetic Field during Short Circuit
9.10 SF6 Decomposition Byproducts. 9.10.1 General
9.10.2 Byproducts and Toxicity
9.10.3 Impact on Worker Protection
9.10.4 Gas Analysis
9.11 Condition Assessment
9.11.1 Introduction
9.11.2 Visual Inspection. 9.11.2.1 Introduction
9.11.2.2 Mechanical Inspection and Stress
Visual Inspection Time Schedule for Mechanical Stress
Checklist for Visual Inspection Time Schedule for Mechanical Stress
9.11.2.3 Corrosion
Visual Inspection Time Schedule for Corrosion
Checklist for Visual Inspection Time Schedule for Mechanical Stress
9.11.2.4 Ground or Earthing Grid Connections
Visual Checks of the Grounding or Earthing Grid Connections
Checklist for Ground or Earth Grid Connections
9.11.2.5 Cross Bonding and Bonding Connections
Visual Checks of the Cross Bonding and Bonding Connections
Checklist for Cross Bonding and Bonding Connections
9.11.2.6 Pressure Relief Device
Visual Checks of the Pressure Relief Device
Checklist for the Pressure Relief Device
9.11.2.7 Bushing Terminations
Visual Checks of the Bushing Termination
Checklist for the Bushing Terminations
9.11.2.8 Local Control Cabinets
Relays/Control Switches
Visual Checks of the Relays/Control Switches
Checklist for the Relays/Control Switches
Gaskets
Visual Checks of the Relays/Control Switches
Checklist for the Relays/Control Switches
General Condition
Visual Checks of the General Condition
Checklist for the General Condition
Control and Power Cables
Visual Checks of the Control and Power Cables
Check List for the Control and Power Cables
Heaters
Visual Checks of the Heaters
Checklist for the Heaters
9.11.2.9 Breaker Operation Inspection
Compressed Air Operational Systems
Visual Checks of the Compressed Air Operational Systems
Checklist for the Compressed Air Operational Systems
Hydraulic Operational Systems
Visual Checks of the Hydraulic Operational Systems
Checklist for the Hydraulic Operational Systems
Spring Operational Systems
Visual Checks of the Spring Operational Systems
Checklist for the Spring Operational Systems
9.11.2.10 Operating Mechanism and Linkage
Visual Checks of the Operating Mechanism and Linkage
Checklist for the Operating Mechanism and Linkage
9.11.2.11 Gas Piping and Decentralized Gas Density Sensors
Visual Checks of the Gas Piping and Decentralized Gas Density Sensors
Checklist for the Gas Piping
Check‐list for the Decentral Gas Density Sensors
9.11.2.12 Gas Density Monitoring Equipment
Visual Checks of the Gas Density Monitoring Equipment
Checklist for the Gas Density Monitoring Equipment
9.11.2.13 Foundation Settlement
Visual Checks of the Foundation Settlement
Checklist for the Foundation Settlement
9.11.2.14 Supporting Structure
Visual Checks of the Supporting Structure
Checklist for the Supporting Structure
9.11.2.15 Instrument Transformer Connections
Visual Checks of the Instrument Transformer Connections
Checklist for the Instrument Transformer Connections
9.11.3 Testing. 9.11.3.1 Introduction
9.11.3.2 In Service Testing
Partial Discharge (PD) Measurement
PD Measurement Recommendation
SF6 Gas Density Monitoring
SF6 Gas Density Monitoring Recommendation
SF6 Gas Content
SF6 Gas Content Recommendation
SF6 By‐products
SF6 Gas By‐products Recommendation
SF6 Leakage Rate
Alarm History
Online Gas Density Monitoring
Trending Data
SF6 Gas Leakage Rate Recommendation
SF6 Gas Moisture Measurement
SF6 Gas Moisture Measurement Recommendation
Radiology
Radiology Measurement Recommendation
Contact Resistance by Thermal Imaging
Contact Resistance by Thermal Imaging Recommendation
Dynamic Resistance Measurement on Circuit Breakers
Dynamic Resistance Measurement on Circuit Breakers Recommendation
9.11.3.3 Out of Service Testing
Circuit Breaker Timing and Travel Curve
Circuit Breaker Timing and Travel Curve Recommendation
Grading Capacitors
Grading Capacitors Recommendation
I2t Analysis
I2t Analysis Recommendation
Secondary Cable Megger
Secondary Cable Megger Recommendation
Circuit Breaker Main Circuit Resistance Test
Circuit Breaker Main Circuit Resistance Test Recommendation
Instrument Transformer Testing
Instrument Transformer Testing Recommendation
Set Point of Compressed Air System
Set Point of Compressed Air System Recommendation
Set Point of Hydraulic System
Set Point of Hydraulic System Recommendation
Set Point of Spring‐Operated System
Set Point of Spring‐Operated System Recommendation
Interlocking Checks
Interlock Checks Recommendation
9.11.4 Data Collection
9.11.4.1 Spare Parts Availability of Manufacturer Obsoleted Design
Spare Parts Availability of Manufacturer Obsoleted Design Recommendation
9.11.4.2 Age of Components
Age of Components Recommendation
9.11.4.3 Identification of Critical Parts
Identification of Critical Parts Recommendation
9.11.4.4 Circuit Breaker Drive Details
Circuit Breaker Drive Details Recommendation
9.11.4.5 Health Index and Probability of Failure
Health Index and Probability of Failure Recommendation
9.11.4.6 Known Issues with Equipment from Manufacturer
Known Issues with Equipment from Manufacturer Recommendation
9.11.4.7 Maintenance Practices & History
Maintenance Practices & History Recommendation
9.11.4.8 Electrical Loading & Rating
Electrical Loading & Rating Recommendation
9.11.4.9 Mechanical Stresses
Mechanical Stresses Recommendation
9.11.4.10 Environmental Conditions
Environmental Conditions Recommendation
9.11.4.11 Operating Practices
Operating Practices Recommendation
9.11.4.12 Load Growth
Load Growth Recommendation
9.11.4.13 Other Information from User
Other Information from User Recommendation
9.11.4.14 SF6 Nameplate Volume Verification
SF6 Nameplate Volume Verification Recommendation
9.11.4.15 Circuit Breaker/High Speed Ground Switch Fault Clearing Data
Circuit Breaker/High Speed Ground Switch Fault Clearing Data Recommendation
9.11.5 Recommendations. 9.11.5.1 General
9.11.5.2 Preventative Maintenance
9.11.5.3 Upgrades & Retrofits
Circuit Breaker Upgrade
Circuit Breaker Controlled Switching
Circuit Breaker Operational Drive
Gas Density Monitoring
Online Moisture Monitoring
Partial Discharge System
9.11.5.4 Recommendations from All Items Above
9.11.6 Life Extension Options. 9.11.6.1 General
9.11.6.2 New GIS
9.11.6.3 New Components
9.11.6.4 Extended Maintenance
9.11.6.5 Retrofit Options
9.11.6.6 Additional Sensors and Data Evaluation
9.11.7 Condition‐Based Analytics
9.11.8 Conclusion
References Section 9.11
9.12 Gas‐Insulated Substations for Enhanced Resiliency
9.12.1 Introduction
9.12.2 Historical Physical Threat Events – Natural and Human‐Caused
9.12.3 Resilience Methodology Using Gas‐Insulated Substations
9.12.4 Prepare
9.12.4.1 Tropical Cyclone Winds
9.12.4.2 Tropical Cyclone Heavy Rains
9.12.4.3 Storm Surge and Coastal Flooding
9.12.4.4 Inland River and Flash Flooding
9.12.4.5 Severe Cold, Heavy Snow and Ice
9.12.4.6 Tornados
9.12.4.7 Severe Thunderstorm Micro Bursts
9.12.4.8 High Straight‐Line Winds
9.12.4.9 Earthquakes
9.12.4.10 Severe Humidity
9.12.4.11 Desert and Severe Heat
9.12.4.12 Human‐Caused Physical Attack
9.12.4.13 Human‐Caused Criminal Theft
9.12.5 Know the Threats, Vulnerabilities and Impacts
9.12.6 Prevent
9.12.6.1 The Tropical Cyclone, Storm Surge and Coastal Flooding Example
9.12.6.2 The Terrorist Physical Attack Example
9.12.7 Respond and Recover
9.12.8 Conclusions
References Section 9.12
9.13 Vacuum High Voltage Switching
9.13.1 Introduction
9.13.2 Advantages
9.13.3 History of Vacuum Circuit Breakers
9.13.3.1 History of Vacuum Switching Capabilities
9.13.4 Modeling and Simulation of the Vacuum Switching Electric Arc
9.13.4.1 Experimental Setup and Conditions
9.13.4.2 Modeling Post‐Arc Current
DSMC Simulation of Vapor Expansion
9.13.5 Control of Switching and Dielectric Strength
9.13.6 X‐radiation Emission
9.13.7 Vacuum Switching at Rated Voltages up to 550 kV and Beyond
9.13.8 Market Potential
9.13.9 Conclusions
References Setion 9.13
9.14 Low Power Instrument Transformer
9.14.1 Introduction
9.14.1.1 Advantages of Low Power Instrument Transformers
9.14.2 Basics of Current and Voltage Instrument Transformer
9.14.2.1 Current Measurement
9.14.2.2 Voltage Measurement
9.14.3 Low Power Current Sensor with Rogowski Coil
9.14.4 Low Power Voltage Sensor with Capacitive Dividers
9.14.5 Comparison Low Voltage and Conventional Instrument Transformers
9.14.5.1 LPIT Integration
9.14.5.2 Size and Weight Reduction
9.14.6 Interfaces
9.14.7 Conclusion
References Section 9.14
9.15 Digital Twin of GIS and GIL
9.15.1 Introduction
9.15.2 Basic definitions. 9.15.2.1 Asset Design Digital Twin Target: Figure Out Most Suitable Design
9.15.2.2 Asset Production Digital Twin Target: Increase Delivery Performance
9.15.2.3 Asset Operation Digital Twin Target: Increase Asset Performance
9.15.3 Data model set up. 9.15.3.1 Design Data Model of Environment
9.15.3.2 Data model of Production
9.15.3.3 Operation
9.15.4 Used Case Digital Twin of GIL. 9.15.4.1 Motivation
9.15.4.2 Project Information Model
9.15.4.3 Local Manufacturing
9.15.5 Used Case Digital Twin of GIS. 9.15.5.1 Merging Real and Virtual Operation
Connectivity Concept
9.15.5.2 Digital Twin Operated & Intelligent
Advanced Intelligence
Gas Density Trending & Prediction
9.15.5.3 User interface, App and Cyber Security
User Interface
APP
Cyber Security
9.15.6 Conclusions
References Section 9.15
9.16 Offshore GIS
9.16.1 Introduction
9.16.2 Types of Collection Platforms
9.16.3 General Offshore Requirements. 9.16.3.1 Risk Management
9.16.3.2 Redundancy
9.16.3.3 Electric Circuit Rating
9.16.3.4 Personnel Safety
9.16.3.5 Asset Safety
9.16.3.6 Engineering Studies
9.16.4 System Offshore Requirements
9.16.4.1 Cable Collector System of the Wind Farm
9.16.4.2 Overload Operation
9.16.4.3 Substation Design
9.16.4.4 Earthing/Grounding
9.16.4.5 Insulation Co‐ordination
9.16.4.6 Voltage Fluctuations
9.16.4.7 System Studies
9.16.5 Equipment Offshore Requirements
9.16.5.1 Medium Voltage Switchgear
9.16.5.2 Transformers and Reactors
9.16.5.3 High Voltage Switchgear
9.16.6 Example Applications of Offshore GIS. 9.16.6.1 AC GIS for 12 MW Wind Turbine
9.16.6.2 AC GIS Using Clean‐Air Insulation and Vacuum Interrupter. Nissum Bredning Wind Farm
GIS Bay of Clean Air Insulation and Vacuum Interrupter
Technical Data
Typical Configurations
Transportation of GIS
Packaging System for GIS
9.16.6.3 DC GIS for HV DC Offshore Converter Platform
14MW Wind Turbine
Applications
References Section 9.16
9.17 HVDC GIS
9.17.1 General
9.17.2 Introduction
9.17.3 History of Gas‐Insulated HVDC Systems
9.17.4 Special Aspects of HVDC Insulation
9.17.5 Modular Design of HVDC GIS
9.17.5.1 Disconnector and Earthing Switches
9.17.5.2 Surge Arrester
9.17.5.3 Voltage and Current Measurement
9.17.5.4 Interface Modules
9.17.5.5 Passive Modules
9.17.6 Testing of Gas‐Insulated HVDC Systems
9.17.6.1 Type and Special Tests. Dielectric‐Type Tests
Insulation System Test
Prototype Installation Test
9.17.6.2 Routine and On‐Site Tests. Routine Testing
On‐Site Testing
9.17.7 Standardization
9.17.8 Application of HVDC GIS
9.17.8.1 Converter Station
9.17.8.2 Transition Station
9.17.9 Conclusion
References Section 9.17
9.18 Digital Substation
9.18.1 Introduction
9.18.1.1 Trends
9.18.1.2 Challenges
9.18.1.3 Opportunities
9.18.2 Functional Concept
9.18.2.1 Data Collection
9.18.2.2 Transformer
9.18.2.3 GIS and Circuit Breaker
9.18.2.4 Surge Arrester
9.18.2.5 Instrument Transformers
9.18.2.6 Arc Suppression Coils
9.18.3 User‐Interface/APP
9.18.4 Exemplary Tests Impressions
9.18.4.1 Electro‐magnetic compatibility (EMC)
9.18.5 Operational Values of Digitalized Products
9.18.5.1 Performance Increase
9.18.5.2 Health, Safety and Environment
9.18.5.3 Cost Reduction
9.18.5.4 Risk Avoidance
9.18.6 More Functionality/Advanced Features
9.18.7 Conclusion
References Section 9.18
References Sections 9.1 to 9.10
10 Conclusion
Index. a
b
c
d
e
f
g
h
i
k
l
m
n
o
p
q
r
s
t
u
v
w
WILEY END USER LICENSE AGREEMENT
Отрывок из книги
Second Edition
Edited by
.....
IEC 60507: Artificial Pollution Tests on High‐Voltage Insulators to be Used on a.c. Systems
IEEE Std. C37.100: IEEE Standard Definitions for Power Switchgear
.....