Application of Nanotechnology in Mining Processes
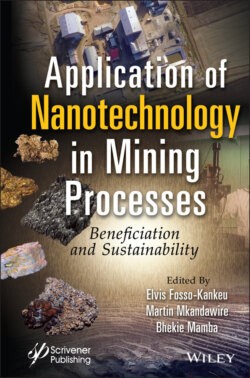
Реклама. ООО «ЛитРес», ИНН: 7719571260.
Оглавление
Группа авторов. Application of Nanotechnology in Mining Processes
Table of Contents
Guide
List of Illustrations
List of Tables
Pages
Application of Nanotechnology in Mining Processes. Beneficiation and Sustainability
Preface
1. Modified Dendrimer Nanoparticles for Effective and Sustainable Recovery of Rare Earth Element from Acid Rock Drainage
1.1 Introduction
1.2 Rare-Earth Element Occurrence in Acid Mine Drainage. 1.2.1 Acid Mine Drainage Generation and Effects
1.2.2 Rare-Earth Elements and Their Importance
1.2.3 Classical AMD Remediation and Treatment Methods
1.3 Dendrimer as Extraction Agent of Rare Earth Element in AMD
1.3.1 Poly(amidoamine) (PAMAM) Dendrimers
1.3.2 Principle REE Extraction Using PAMAM
1.4 Designed a Recovery System for REE from AMD. 1.4.1 Process Overview
1.4.2 Components and Their Functions. 1.4.2.1 Reactor 1 – Collection Tank
1.4.2.2 Reactor 2 – Mixing Tank
1.4.2.3 Reactor 3 – Separation Tank
1.4.2.4 Reactor 4 – Recovery of REEs Metals
1.5 Challenges and Opportunities for the Future of Metal Mining
1.6 Conclusion
Acknowledgment
References
2. Cellulose-Based Nanomaterials for Treatment of Acid Mine Drainage-Contaminated Waters
2.1 Introduction
2.2 Cellulose
2.2.1 Structure and Properties of Cellulose
2.2.2 Nanocellulose
2.3 Synthesis of CNFs and CNCs
2.3.1 Synthesis of CNFs
2.3.2 Synthesis of CNCs Through Acid Hydrolysis
2.3.3 Cationization for Anion Uptake
2.3.4 Application of CNF and CNC Nanocomposite in Metal and Anion Removal
2.4 Cellulose Composites
2.4.1 Cellulose/Chitosan Nanocomposites
2.4.2 Cellulose/Metal Oxide Nanoparticles: ZnO, Magnetic Iron Oxide Nanoparticles, Nano Zero-Valent Iron
2.5 Valorization of AMD-Contaminated Water and the Possible Uses of Recovered Elements
2.5.1 Sludge from AMD
2.5.1.1 Removal of Heavy Metals Using Sludge
2.5.1.2 Sludge as a Fertilizer
2.5.1.3 Sludge Used in Construction Material
2.5.2 Resource Recovery
2.6 Conclusion
References
3. Application of Nanomaterials for Remediation of Pollutants from Mine Water Effluents
3.1 Introduction
3.1.1 Mine Water Chemistry
3.2 Existing Treatment Methods of Mine Water and Their Limitations
3.3 Nanoremediation of Mine Water
3.4 Application of Nanomaterials for Mine Water Remediation
3.5 Conclusions and Future Perspectives
References
4. Application of Nanofiltration in Mine-Influenced Water Treatment: A Review with a Focus on South Africa
Abbreviations
4.1 Introduction. 4.1.1 Mine-Influenced Water. 4.1.1.1 Occurrence and Types of Mine-Influenced Water
4.1.1.2 Mine-Influenced Water Treatment
4.1.2 Reuse of Mine-Influenced Water
4.2 Nanofiltration for Mine-Influenced Water Treatment. 4.2.1 Introduction—Membrane Separation Technologies
4.2.2 Nanofiltration. 4.2.2.1 Background and Benefits
4.2.2.2 Types and Performances of Nanofiltration Membranes
4.2.2.3 Limitations and Challenges
4.2.2.4 Nanocomposite Membranes and Nanofillers
4.2.3 Membrane Distillation
4.3 Large-Scale Operations Using Nanofiltration or Reverse Osmosis. 4.3.1 Integration of Membrane and Conventional Treatment Approaches
4.3.2 Pilot-Scale Case Studies
4.3.3 Challenges of Scale-Up and Commercialization
4.3.3.1 Fouling
4.3.3.2 Membrane Selection
4.3.3.3 Modeling and Simulation of NF Systems
4.3.3.4 Cost Estimates
4.3.3.5 Environmental Considerations
4.4 Some Perspectives and Research Directions
References
5. Recovery of Gold from Thiosulfate Leaching Solutions with Magnetic Nanoparticles
Abbreviations
5.1 Introduction
5.2 Recovery of Precious Metals with Magnetic Nanohydrometallurgy
5.2.1 Superparamagnetism
5.2.2 Iron Oxide Nanoparticles
5.2.3 Selective Adsorption
5.2.4 Adsorption Mechanisms
5.2.5 Recovery of Gold
5.2.6 Recovery of Silver
5.2.7 Recovery of PGMs
5.3 Synthesis and Functionalization of Magnetic Nanoparticles
5.4 Characterization of Magnetic Nanoparticles
5.5 Recovery of Gold from Thiosulfate Leaching Solutions
5.5.1 Preparation of PEI-MNPs
5.5.2 Application of PEI-MNPs for Gold Adsorption from Synthetic Leaching Solutions
5.5.3 Application of PEI-MNPs for Gold Adsorption from Ore Leachates
5.6 Gold Elution and Reuse of the Adsorbent
5.7 Industrial Scale-Up and Challenges
5.7.1 High Gradient Magnetic Separation
5.7.2 Nanoparticle Aggregation and Agglomeration
5.7.3 Nanoparticle Dissolution
5.7.4 Magnetic Separation from a Solution
5.8 Environmental Concerns and Toxicity of MNPs
References
6. Recovery of Na2CO3 and Nano CaCO3 from Na2SO4 and CaSO4 Wastes
6.1 Introduction
6.2 Literature Survey. 6.2.1 Gypsum Reduction
6.2.2 Nano CaCO3. 6.2.2.1 Uses
6.2.2.2 Composition and Particle Size
6.2.3 Na2CO3. 6.2.3.1 Introduction
6.2.3.2 Uses
6.2.3.3 Chemical Properties
6.2.3.4 Physical Properties
6.2.3.5 Production Methods
6.3 Materials and Methods. 6.3.1 Feedstock, Chemicals and Reagents
6.3.2 Equipment
6.3.3 Experimental and Procedure. 6.3.3.1 Thermal Treatment
6.3.3.2 OLI Simulations and Beaker Studies
6.3.3.3 Na2S Formation
6.3.3.4 Ca(HS)2 Formation
6.3.3.5 Nano CaCO3 Formation
6.3.4 Analysis
6.3.5 OLI Software Simulations
6.4 Results and Discussion. 6.4.1 Direct Conversion of Na2SO4 to Na2S
6.4.2 CaSO4 Reduction. 6.4.2.1 CaS Formation
6.4.2.2 Ca(HS)2 Formation
6.4.3 Na2CO3 Production. 6.4.3.1 Indirect Conversion of Na2SO4 to Na2S
6.4.3.2 NaHCO3 Formation
6.4.3.3 NaHCO3 and NaHS Separation
6.4.3.4 Na2CO3 Formation
6.4.3.5 Up-Concentration of NaHS (Freeze Crystallization)
6.4.4 CaCO3 Formation. 6.4.4.1 Crude and Pure CaCO3 and Ca(HS)2 Formation
6.4.4.2 Nano CaCO3 Formation
6.5 Conclusions
Acknowledgments
References
7. Recovery of Drinking Water and Nanosized Fe2O3 Pigment from Iron Rich Acid Mine Water
7.1 Introduction. 7.1.1 Formation and Quantities
7.1.2 Legal Requirements
7.1.3 ROC Process
7.1.4 Raw Material Manufacturing
7.1.5 Objectives
7.2 Literature Review
7.2.1 Uses of Nanopigment
7.2.2 Production of Nanopigment
7.2.3 Market for Nanopigment
7.3 Materials and Methods. 7.3.1 Neutralization. 7.3.1.1 Feedstock
7.3.1.2 Equipment
7.3.1.3 Procedure
7.3.1.4 Experimental
7.3.1.5 Analytical
7.3.1.6 Characterization
7.3.2 Coagulation. 7.3.2.1 Feedstock
7.3.2.2 Equipment
7.3.2.3 Procedure
7.3.2.4 Experimental
7.3.3 Pigment Formation. 7.3.3.1 Feedstock
7.3.3.2 Equipment
7.3.3.3 Procedure
7.3.3.4 Experimental
7.3.3.5 Characterization of the Sludge
7.4 Results and Discussion. 7.4.1 Neutralization with MgO and Na2CO3
7.4.1.1 Solubilities of Alkalis and Products
7.4.1.2 Sludge Characteristics
7.4.1.3 Flocculant/Coagulant Selection and Dosing
7.4.1.4 Centrifugation
7.4.2 Concentration of Acid Mine Water
7.4.2.1 Freeze Crystallization
7.4.2.2 Forward Osmosis
7.4.2.3 Feasibility of Forward Osmosis and Freeze Desalination
7.4.3 Pigment Formation. 7.4.3.1 Effect of Temperature
7.4.3.2 Elemental Composition of Feed and Product Mineral
7.4.3.3 Morphological Characteristics of the Synthesized Pigments
7.4.4 Process Configurations. 7.4.4.1 Iron(III)-Rich Water (Kopseer Dam) (Process Configuration A)
7.4.4.2 Iron(II)-Rich Water (Top Dam) (Process Configuration B)
7.4.4.3 Tailings and Tailings Leachate
7.4.5 Economic Feasibility
7.5 Conclusion
7.6 Recommendation
Acknowledgments
References
8. Advances of Nanotechnology Applications in Mineral Froth Flotation Technology
Abbreviations
8.1 Introduction to Froth Flotation
8.2 Current Developments of Nanotechnology in the Mineral Froth Flotation Process
8.2.1 Nanobubbles in Mineral Froth Flotation
8.2.1.1 Generation and Conditions of Nanobubble Formation
8.2.1.2 Properties and Stability of Nanobubbles
8.2.2 General Overview of Applications of Nanobubbles in Mineral Froth Flotation and Recovery of Selected Minerals
8.2.2.1 Flotation of Fine and Ultrafine Mineral Particles Using Nanobubbles
8.2.2.2 Flotation of Coal Using Nanobubbles
8.2.2.3 Flotation of Phosphate Ore Using Nanobubbles
8.2.2.4 Interactive Relationship Between Nanobubbles, Collectors and Mineral Particles
8.2.3 Nanofrothers in Mineral Froth Flotation
8.2.4 Nanocollectors in Mineral Froth Flotation
8.2.4.1 Nanopolystyrene Collector
8.2.4.1.1 Flotation of Sulfide Ore Using Nanopolystyrene Collector
8.2.4.1.2 Flotation of Coal using Nanopolystyrene Collector
8.2.4.1.3 Optimization of the Flotation Capability of the Nanopolystyrene Collector
8.2.4.2 Cellulose-Based Nanocrystals Collector
8.2.4.2.1 Flotation of Quartz, Hematite and Aluminium Oxide Using Cellulose Nanocrystals
8.2.4.3 Carbon Black and Talc Nanoparticle Collectors. 8.2.4.3.1 Flotation of Malachite Using Carbon Black Nanocollector
8.2.4.3.2 Flotation of Quartz Using Talc Nanoparticles
8.2.5 Nanodepressants in Mineral Froth Flotation
8.3 Intellectual Property (IP) and Commercialization of Nanotechnology in Mineral Froth Flotation Technology
8.4 Current Research Gaps
8.5 Conclusion
References
9. Nanoscale Materials for Mineral Froth Flotation: Synthesis and Implications of Nanoscale Material Design Strategies on Flotation Performance
9.1 Introduction
9.2 Classification of Minerals
9.2.1 Chemical Classification of Minerals
9.3 Synthesis and Characterization of Nanoscale Materials
9.3.1 Top-Down Synthesis Approach
9.3.2 Bottom-Up Synthesis Approach
9.3.3 Characterization of Nanomaterials
9.3.4 Effect of Nanoparticle Size, Morphology and Structure on Flotation Performance
9.4 Nanoflotation Reagents and Mineral Particle Interaction in the Flotation Environment
9.4.1 Effect of Mineral Surface Properties on Recovery
9.4.1.1 Potential Strategies of Evaluating Surface Properties
9.4.1.2 Effect of Mineral Surface Electric Charge and Microstructure on Flotation and Potential Techniques for Tailoring Nanocollector Hydrophobicity
9.5 Nanotoxicology
9.6 Conclusion
References
Index
WILEY END USER LICENSE AGREEMENT
Отрывок из книги
Scrivener Publishing 100 Cummings Center, Suite 541J Beverly, MA 01915-6106
.....
11. Feris, L. and Kotze, L.J., The regulation of acid mine drainage in South Africa: law and governance perspectives. Potchefstroom Electron. Law J./Potchefstroomse Elektroniese Regsblad, 17, 5, 2104–2163, 2014.
12. Zhang, W. and Honaker, R., Process development for the recovery of rare earth elements and critical metals from an acid mine leachate. Miner. Eng., 153, 106382, 2020 Jul 1.
.....