High-Performance Materials from Bio-based Feedstocks
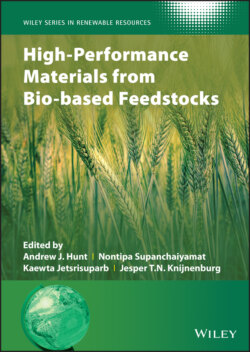
Реклама. ООО «ЛитРес», ИНН: 7719571260.
Оглавление
Группа авторов. High-Performance Materials from Bio-based Feedstocks
Table of Contents
List of Tables
List of Illustrations
Guide
Pages
Wiley Series in Renewable Resources
High‐Performance Materials from Bio‐based Feedstocks
List of Contributors
Series Preface
1 High‐performance Materials from Bio‐based Feedstocks: Introduction and Structure of the Book
1.1 Introduction
1.2 High‐performance Bio‐based Materials and Their Applications
1.2.1 Biomass Constituents. 1.2.1.1 Polysaccharides
1.2.1.2 Other Biopolymers
1.2.1.3 Proteins and Amino Acids
1.2.1.4 Active Biological Compounds
1.2.2 Bioderived Materials. 1.2.2.1 Polymers Derived from Biological Monomers
1.2.2.2 Carbon‐based Materials Derived from Biomass
1.2.2.3 Inorganic Materials Derived from Biomass
1.3 Structure of the Book
References
2 Bio‐based Carbon Materials for Catalysis
2.1 Introduction
2.2 Biomass Resources for Carbon Materials
2.2.1 Wood from Natural Forests
2.2.2 Agricultural Residues
2.3 Thermochemical Conversion Processes
2.3.1 Carbonization and Pyrolysis
2.3.2 Activation
2.3.2.1 Chemical Activation
2.3.2.2 Physical Activation
2.3.3 Hydrothermal Carbonization
2.3.4 Graphene Preparation from Biomass
2.4 Fundamentals of Heterogeneous Catalysis
2.5 Catalysis Applications of Selected Bio‐based Carbon Materials
2.5.1 Biochar
2.5.2 Modified Biochar
2.5.2.1 Tar‐reforming Processes
2.5.2.2 Biodiesel Production Processes
2.5.3 Biomass‐Derived Activated Carbon
2.5.4 Hydrothermal Bio‐based Carbons
2.5.5 Sugar‐Derived Carbon Catalysts
2.5.6 Carbon Nanotubes from Biomass
2.5.7 Graphene and Its Derivatives
2.6 Summary and Future Aspects
References
3 Starbon®: Novel Template‐Free Mesoporous Carbonaceous Materials from Biomass – Synthesis, Functionalisation and Applications in Adsorption, and Catalysis
3.1 Introduction
3.2 Choice of Polysaccharide
3.2.1 Synthetic Procedure. 3.2.1.1 Gelation
3.2.1.2 Drying of the Hydrogel
3.2.1.3 Pyrolysis of the Expanded Aerogel
3.2.2 Derivatisation
3.2.2.1 Sulphonation. 3.2.2.1.1 Method of Sulphonation
3.2.2.1.2 Characterisation of Sulphonated Material
3.2.2.2 N‐Starbons. 3.2.2.2.1 Methods of N Incorporation
3.2.2.2.2 Characterisation
3.2.2.3 Derivatisation via Bromination and Activation of Hydroxyl Functionality
3.2.3 Applications. 3.2.3.1 Catalysis
3.2.3.1.1 Sulphonated Starbon in Esterifications
3.2.3.1.2 Sulphonated Starbon in Dehydrations
3.2.3.1.3 Sulphonated Starbon in Amide Synthesis
3.2.3.1.4 Sulphonated Starbon in Acylations and Alkylations
3.2.3.1.5 Supported Metal Complexes
3.2.3.1.6 Photocatalytic Processes
3.2.4 Adsorption Processes
3.2.4.1 Adsorption of Gases
3.2.4.2 Adsorption or Organics from Solution
3.2.4.3 Metal Recovery
3.2.4.4 Adsorption and Release of Bioactives
3.2.5 Conclusion
References
4 Conversion of Biowastes into Carbon‐based Electrodes
4.1 Introduction
4.2 Conversion Techniques of Biowastes
4.2.1 Carbonization
4.2.1.1 Low‐Temperature Carbonization
4.2.1.2 High‐Temperature Pyrolysis
4.2.1.3 Other Carbonization Methods
4.2.2 Activation
4.2.2.1 Physical Activation
4.2.2.2 Chemical Activation
4.3 Structure and Doping. 4.3.1 Biowaste Selection
4.3.2 Structure Control
4.3.3 Heteroatom Doping
4.4 Electrochemical Applications
4.4.1 Supercapacitors
4.4.2 Capacitive Deionization Cells
4.4.3 Hydrogen and Oxygen Evolution
4.4.4 Fuel Cells
4.4.5 Lithium‐Ion Batteries and Others
4.5 Conclusion and Outlook
Acknowledgments
References
5 Bio‐based Materials in Electrochemical Applications
5.1 Introduction
5.2 Fundamentals of Bio‐based Materials
5.2.1 Bio‐based Polymers
5.2.2 Carbonaceous Materials from Biological Feedstocks
5.3 Application of Bio‐based Materials in Batteries
5.3.1 General Concept of Metal‐Ion Batteries
5.3.1.1 Electrode Materials
5.3.1.1.1 Anode Materials
5.3.1.1.2 Cathode Materials
5.3.1.1.2.1 Organic Battery
5.3.1.1.2.2 Bio‐battery
5.3.1.2 Battery Separators
5.3.1.3 Solid Electrolytes
5.4 Application of Bio‐based Polymers in Capacitors. 5.4.1 General Concept of Electrochemical Capacitors
5.4.2 Electrode Materials
5.4.2.1 Electrochemical Double‐Layer Capacitor
5.4.2.1.1 Activated Carbon
5.4.2.1.2 Carbon Nanomaterials
5.4.2.1.3 Carbon Aerogels
5.4.2.2 Pseudocapacitors
5.4.2.2.1 Conductive Polymers
5.4.2.2.2 Metal Oxides
5.5 Alternative Binders for Sustainable Electrochemical Energy Storage
5.5.1 Polysaccharides and Cellulose‐based Binders
5.5.1.1 Cellulose‐based Materials
5.5.1.2 Natural Cellulose and Nanocellulose
5.5.1.3 Other Polysaccharides
5.5.2 Lignin
5.6 Application of Bio‐based Polymers in Fuel Cells
5.6.1 Chitosan
5.6.2 Other Biopolymers
5.7 Conclusion and Outlook
References
6 Bio‐based Materials Using Deep Eutectic Solvent Modifiers
6.1 Introduction
6.2 Bio‐based Materials
6.2.1 Ionic Liquids
6.2.2 Deep Eutectic Solvents
6.2.3 Morphological/Mechanical Modification
6.2.4 Chemical Modification
6.2.5 Composite Formation
6.2.6 Gelation
6.3 Conclusion
References
7 Biopolymer Composites for Recovery of Precious and Rare Earth Metals
7.1 Introduction
7.2 Mechanisms of Metal Adsorption. 7.2.1 Silver
7.2.2 Gold and Platinum Group Metals
7.2.3 Rare Earth Metals
7.3 Composite Materials and Their Adsorption
7.3.1 Cellulose‐based Composite Adsorbents. 7.3.1.1 Structure and Chemistry of Cellulose
7.3.1.2 Cellulose Composites for Precious Metal Adsorption. 7.3.1.2.1 Magnetic Cellulose Composites
7.3.1.2.2 Polymer‐Cellulose Composites
7.3.1.2.3 Other Cellulose Composites
7.3.1.3 Cellulose Composites for Rare Earth Metal Adsorption. 7.3.1.3.1 Polymer‐Cellulose Composites
7.3.1.3.2 Other Cellulose Composites
7.3.2 Chitosan‐based Composite Adsorbents. 7.3.2.1 Structure and Chemistry of Chitosan
7.3.2.2 Chitosan Composites for Precious Metal Adsorption. 7.3.2.2.1 Magnetic Chitosan Composites
7.3.2.2.2 Polymer‐Chitosan Composites
7.3.2.2.3 Other Chitosan Composites
7.3.2.3 Chitosan Composites for Rare Earth Metal Adsorption. 7.3.2.3.1 Magnetic Chitosan Composites
7.3.2.3.2 Polymer‐Chitosan Composites
7.3.2.3.3 Other Chitosan Composites
7.3.3 Alginate‐based Adsorbents. 7.3.3.1 Structure and Chemistry of Alginate
7.3.3.2 Alginate Composites for Precious Metal Adsorption
7.3.3.3 Alginate Composites for Rare Earth Metal Adsorption
7.3.4 Lignin‐based Composite Adsorbents. 7.3.4.1 Lignin Structure and Chemistry
7.3.4.2 Lignin Composites for Precious Metal Adsorption
7.3.4.3 Lignin Composites for Rare Earth Metal Adsorption
7.4 Conclusion and Outlook
References
8 Bio‐Based Materials in Anti‐HIV Drug Delivery
8.1 Introduction
8.2 Biomedical Strategies for HIV Prophylaxis
8.3 Properties of Anti‐HIV Drug Delivery Systems
8.4 Bio‐based Materials for Anti‐HIV Drug Delivery Systems
8.4.1 Cellulose
8.4.2 Chitosan
8.4.3 Polylactic Acid
8.4.4 Carrageenan
8.4.5 Alginate
8.4.6 Hyaluronic Acid
8.4.7 Pectin
8.5 Conclusion
References
9 Chitin – A Natural Bio‐feedstock and Its Derivatives: Chemistry and Properties for Biomedical Applications
9.1 Bio‐feedstocks
9.1.1 Chitin
9.1.2 Chitosan
9.1.3 Glucan
9.1.4 Chitin–Glucan Complex
9.1.5 Polyphenols
9.2 Synthetic Route
9.2.1 Isolation of ChGC
9.2.2 Derivatives of ChGC and Its Modified Polymers
9.2.3 Preparation of D‐Glucosamine from Chitin/Chitosan–Glucan
9.3 Properties of Chitin, ChGC, and Its Derivatives for Therapeutic Applications
9.3.1 Antibacterial Activity
9.3.2 Anticancer Activity
9.3.3 Antioxidant Activity
9.3.4 Therapeutic Applications
9.4 Gene Therapy – A Biomedical Approach
9.5 Cs: Properties and Factors Affecting Gene Delivery
9.6 Organic Modifications of Cs Backbone for Enhancing the Properties of Cs Associated with Gene Delivery
9.6.1 Modification of Cs with Hydrophilic Groups
9.6.2 Modification in Cs by Hydrophobic Groups
9.6.3 Modification by Cationic Substituents
9.6.4 Modification by Target Ligands
9.7 Multifunctional Modifications of Cs
9.8 Miscellaneous
9.9 Conclusion
Acknowledgments
References
10 Carbohydrate‐Based Materials for Biomedical Applications
10.1 Introduction
10.2 Bio‐based Glycopolymers. 10.2.1 Chitin and Chitosan
10.2.2 Cellulose
10.2.3 Starch
10.2.4 Dextran
10.3 Synthetic Carbohydrate‐based Functionalized Materials
10.3.1 Glycomimetics
10.3.2 Presentation of Glycomimetics in Multivalent Scaffolds. 10.3.2.1 Glycodendrimers
10.3.2.2 Glycopolymers
10.3.2.3 Glyconanoparticles
10.4 Conclusion
References
11 Organic Feedstock as Biomaterial for Tissue Engineering
11.1 Introduction
11.2 Protein‐based Natural Biomaterials
11.2.1 Silk
11.2.2 Collagen
11.2.3 Decellularized Skins
11.2.4 Fibrin/Fibrinogen
11.3 Polysaccharide‐based Natural Biomaterials
11.3.1 Chitosan
11.3.2 Alginate
11.3.3 Agarose
11.4 Summary
References
12 Green Synthesis of Bio‐based Metal–Organic Frameworks
12.1 Introduction
12.2 Green Synthesis of MOFs
12.2.1 Solvent‐Free and Low‐Solvent Synthesis
12.2.2 Green Solvents
12.2.3 Sonochemical Synthesis
12.2.4 Electrochemical Synthesis
12.3 Bio‐based Ligands
12.3.1 Amino Acids
12.3.2 Aliphatic Diacids
12.3.3 Cyclodextrins
12.3.4 Other
12.3.5 Exemplars: Bio‐based MOFs Obtainable via Green Synthesis
12.4 Metal Ion Considerations
12.4.1 Calcium
12.4.2 Magnesium
12.4.3 Manganese
12.4.4 Iron
12.4.5 Titanium
12.4.6 Zirconium
12.4.7 Aluminium
12.4.8 Zinc
12.5 Challenges for Further Development Towards Applications
12.5.1 Stability Issues
12.5.1.1 Chemical Stability
12.5.1.2 Thermal Stability
12.5.1.3 Hydrothermal Stability
12.5.1.4 Mechanical Stability
12.5.2 Scalability and Cost
12.5.3 Competing Alternative Materials
12.6 Conclusion
References
13 Geopolymers Based on Biomass Ash and Bio‐based Additives for Construction Industry
13.1 Introduction
13.2 Pozzolan and Agricultural Waste Ash
13.3 Geopolymer
13.4 Combustion of Biomass
13.4.1 Open Field Burning
13.4.2 Controlled Burning
13.4.3 Boiler Burning
13.4.4 Fluidized Bed Burning
13.5 Properties and Utilization of Biomass Ashes
13.6 Biomass Ash‐based Geopolymer
13.6.1 Rice Husk Ash‐based Geopolymer. 13.6.1.1 Rice Husk Ash Geopolymer
13.6.1.2 Rice Husk Ash Geopolymer with External Alumina Source
13.6.1.3 Properties of Rice Husk Ash‐based Geopolymer. 13.6.1.3.1 Fly Ash/Rice Husk Ash Geopolymer
13.6.1.3.2 Rice Husk Ash/Metakaolin Geopolymer
13.6.1.3.3 Rice Husk Ash/Al(OH)3 Geopolymer
13.6.2 Bagasse Ash‐based Geopolymer. 13.6.2.1 Bagasse Ash Geopolymer
13.6.2.2 Bagasse Ash Geopolymer with External Alumina Source
13.6.2.3 Properties of Bagasse Ash‐based Geopolymer. 13.6.2.3.1 Fly Ash/Bagasse Ash Geopolymer
13.6.2.3.2 Metakaolin/Bagasse Ash Geopolymer
13.6.2.3.3 Slag/Bagasse Ash Geopolymer
13.6.3 Palm Oil Fuel Ash‐based Geopolymer. 13.6.3.1 Palm Oil Fuel Ash Geopolymer
13.6.3.2 Palm Oil Fuel Ash with External Alumina Source
13.6.3.3 Properties of Palm Oil Fuel Ash‐based Geopolymer. 13.6.3.3.1 Fly Ash/Palm Oil Fuel Ash Geopolymer
13.6.3.3.2 Metakaolin/Palm Oil Fuel Ash Geopolymer
13.6.3.3.3 Palm Oil Fuel Ash Geopolymer
13.6.4 Other Biomass‐based Geopolymers
13.6.5 Use of Biomass in Making Sodium Silicate Solution and Other Products. 13.6.5.1 Use of Biomass in Making Sodium Silicate Solution
13.6.5.2 Use of Biomass Ash in Making Lightweight Aggregate
13.6.6 Fire Resistance of Bio‐based Geopolymer
13.7 Conclusion
References
14 The Role of Bio‐based Excipients in the Formulation of Lipophilic Nutraceuticals
14.1 Introduction
14.2 Emulsions and the Importance of Bio‐based Materials as Emulsifiers
14.2.1 Conventional Micro‐ and Nanoemulsions
14.2.2 Pickering‐Stabilised Emulsions
14.3 Novel Formulation Technologies: Colloidal Delivery Vesicles. 14.3.1 Microgels
14.3.2 Nanoprecipitation
14.3.3 Liposomes
14.3.4 Complex Coacervation
14.3.5 Complexation
14.4 Key Drying Technologies Employed During Formulation
14.4.1 Spray Drying
14.4.2 Spray‐Freeze Drying
14.4.3 Electrohydrodynamic Processing
14.4.4 Fluid Bed Drying
14.4.5 Extrusion
14.5 Conclusions and Future Perspectives
References
15 Bio‐derived Polymers for Packaging
15.1 Introduction
15.2 Starch
15.3 Chitin/Chitosan
15.4 Cellulose and Its Derivatives
15.4.1 Cellulose Nanocrystals
15.4.2 Cellulose Nanofibers
15.4.3 Bacterial Nanocellulose
15.4.4 Carboxymethyl Cellulose
15.5 Poly(Lactic Acid)
15.5.1 Bio‐based Toughening Agents Used in PLA Toughness Improvement
15.5.2 Toughening of PLA and Its Properties Related to Packaging Applications
15.6 Bio‐based Active and Intelligent Agents for Packaging
15.6.1 Active Agents
15.6.2 Intelligent Packaging
15.7 Conclusion
References
16 Recent Developments in Bio‐Based Materials for Controlled‐Release Fertilizers
16.1 Introduction and Historical Review. 16.1.1 Early Fertilizer Development and Its Impact on Environment
16.1.2 Controlled‐Release Fertilizer
16.2 Mechanistic View of Controlled‐Release Fertilizer from Bio‐based Materials
16.2.1 Coating Type
16.2.2 Matrix Type
16.2.3 Other Release Mechanisms
16.3 Controlled Release Technologies from Bio‐based Materials
16.3.1 Natural Polymers and Their Fertilizer Applications
16.3.1.1 Polysaccharides
16.3.1.1.1 Cellulose
16.3.1.1.2 Starch
16.3.1.1.3 Alginate
16.3.1.1.4 Chitosan
16.3.1.2 Lignin
16.3.2 Bio‐based Modified Polymer Coatings for Controlled‐Release Fertilizer
16.3.2.1 Bio‐based Alkyd Resin
16.3.2.2 Bio‐based Polyurethane
16.3.3 Biochar and Other Carbon‐based Fertilizers
16.4 Conclusion and Foresight
Acknowledgments
References
Index. a
b
c
d
e
f
g
h
i
k
l
m
n
o
p
q
r
s
t
u
v
z
WILEY END USER LICENSE AGREEMENT
Отрывок из книги
Series Editor:
Christian V. Stevens, Faculty of Bioscience Engineering, Ghent University, Belgium
.....
Biodiesel, a fuel derived from renewable sources such as vegetable oils and animal fats, has received much attention due to the continuous reduction in petroleum reserves and environmental issues. Biodiesel production via transesterification (Figure 2.5), also known as alcoholysis, is currently the most attractive approach, and can be divided into non‐catalytic, biocatalytic, and chemical catalytic processes. The non‐catalytic process or supercritical alcohol process is carried out in conditions above critical temperature and pressure of the reaction mixture determined from the critical properties of alcohols and triglycerides. This process requires a relatively high reaction temperature of 230–450 °C and high pressure of 19–60 MPa, as well as excess methanol (molar ratio of oil to methanol approximately 1 : 40). These requirements are a limitation to the non‐catalytic process for biodiesel production on an industrial scale [99]. A biocatalytic or enzymatic process produces biofuel with a low environmental impact and can be performed at mild temperature and pressure. Such processes are also not sensitive to the free fatty acid and water content in the feedstock [100, 101]. However, enzyme stability, enzyme reuse, and the high cost of enzyme immobilization are the major drawbacks of this process. In conventional biodiesel production, chemical catalysts (both acidic and basic) are usually used. Solid catalysts have been widely applied in biodiesel production owing to their ease of separation from products and excess reactants. A number of research studies have been conducted on biodiesel production using various types of acidic and basic solid catalysts. Most common is the solid base catalyst or alkali catalyst that can catalyze transesterification reaction in even milder reaction conditions and shorter reaction time than acidic solid catalysts. Calcium oxide (CaO) solid base catalyst can be derived from calcium carbonate‐rich materials such as horn shell and eggshell. With the basic catalyst produced from calcined eggshell, the biodiesel yield reached 97% in transesterification of waste cooking oil and methanol at the ratio of 1 : 6 [102]. Nevertheless, the preparation of a solid base catalyst from calcium carbonate‐rich feedstocks requires high temperatures of 800–900 °C. In addition, the free fatty acid and moisture contents in the oil feedstock should be considered for alkali catalysts. Water molecules in the feedstock can hydrolyze triglycerides into diglycerides and monoglycerides, which yield a greater amount of free fatty acids. The alkali catalyst is able to convert free fatty acids into soap via the saponification side‐reaction. The free fatty acid in the feedstock should be lower than 2% for transesterification.
Figure 2.5 Transesterification of triglyceride.
.....