Applications of Polymer Nanofibers
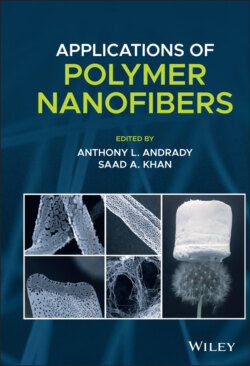
Реклама. ООО «ЛитРес», ИНН: 7719571260.
Оглавление
Группа авторов. Applications of Polymer Nanofibers
Table of Contents
List of Tables
List of Illustrations
Guide
Pages
Applications of Polymer Nanofibers
List of Contributors
Preface
Note
1 Electrospinning Parameters and Resulting Nanofiber Characteristics : Theoretical to Practical Considerations
1.1 Electrospinning Overview
1.2 Effect of Process Parameters
1.2.1 Theoretical Analysis
1.2.2 Experimental Results
1.3 Effect of Setup Parameters
1.4 Effect of Solution Parameters. 1.4.1 Polymer Solution Properties (Molecular Weight, Concentration, Viscosity, and Elasticity)
1.4.2 Solvent Selection
1.4.3 Additivities to Tune Solution Properties. 1.4.3.1 Surface Tension
1.4.3.2 Conductivity
1.5 Electrospinnable Systems
1.5.1 Nonpolymer Electrospinning
1.6 Advanced Fiber Characteristics. 1.6.1 Ribbons, Wrinkles, Branching, and Netting
1.6.2 Porous Fibers
1.6.3 Core–Shell Fibers. 1.6.3.1 Coaxial Electrospinning
1.6.3.2 Emulsion Electrospinning
1.7 Process Scalability
1.7.1 Melt Electrospinning
1.7.2 Needleless or “Free‐Surface” Electrospinning
1.7.3 Alternative Fiber Production Methods
References
2 Textile Applications of Nanofibers
2.1 Introduction of Nanofibers in Textile Applications
2.2 Fabrication of Nanofiber Yarns
2.2.1 Electrospinning
2.2.2 Bicomponent Spinning
2.2.3 Melt Blowing
2.2.4 Flash Spinning
2.2.5 Centrifugal Spinning
2.2.6 Formation of Nanofiber Yarns
2.3 Structure and Properties of Nanofiber Yarns
2.4 Fabrication of Nanofiber Fabrics
2.4.1 Nanofibrous Nonwoven Fabrics
2.4.2 Nanofibrous Woven Fabrics
2.5 Characteristics and Specialized Applications of Nanofiber Fabrics
2.5.1 Protective Clothing
2.5.2 Filter Fabrics
2.5.3 Wearable Devices
2.5.4 Functional Fabrics
2.5.5 Biomedical Textiles
2.6 Summary and Future Trends
References
3 Nanofiber Mats as High‐Efficiency Filters
3.1 Introduction
3.1.1 Background
3.1.2 Filtration Overview
3.1.3 Available Information
3.1.4 Scope of This Chapter
3.2 Filters Made with Nanofibers. 3.2.1 Consequences of Reducing Fiber Size
3.2.2 Slip Flow
3.2.3 Pressure Drop
3.2.4 Particle Collection Mechanisms
3.2.5 Evaluation
3.2.6 Nanofiber Media Modeling
3.3 Filtration Developments
3.3.1 Media Scale. 3.3.1.1 Support Substrates
3.3.1.2 Mixed Bead‐Fiber Systems
3.3.1.3 Unsupported Nanofiber Membranes
3.3.1.4 Multilayer Mats
3.3.1.5 Intermingled Nanofiber Mats
3.3.1.6 Mesh Substrates
3.3.1.7 Mat Morphological Modifications
3.3.2 Fiber Scale. 3.3.2.1 Functional Fibers
3.3.2.2 Coated Fibers
3.3.2.3 Combining Nanofibers and Nanoparticles for Dual Function
3.3.2.4 Core Shell Fibers
3.3.2.5 Electrostatics
3.4 Outlook
Acknowledgments
References
4 Nanofiber‐Based Chemical Sensors
4.1 Introduction
4.2 General Features of Sensors
4.3 Nanofibers as a Sensor Material
4.3.1 Nanofiber vs. Thin‐Film Geometry
4.4 Approaches to Nanofiber Sensor Design
4.5 Gravimetric Nanofiber Sensors. 4.5.1 Quartz Crystal Microbalance
4.5.2 Surface Acoustic Wave Resonators
4.6 Optical Sensors. 4.6.1 Colorimetric Sensors
4.6.2 Fluorescence Sensors
4.7 Electrochemical Sensors
4.7.1 Metal‐Oxide Sensors
4.7.2 Graphene‐Based Sensors
References
5 Nanofibers in Energy Applications
5.1 Overview
5.2 Energy Storage Applications
5.2.1 Rechargeable Batteries
5.2.1.1 Lithium‐Ion Batteries
5.2.1.1.1 Cathodes
5.2.1.1.2 Anodes
5.2.1.1.3 Separators
5.2.1.2 Sodium‐Ion
5.2.1.3 Beyond Li‐Ion
5.2.1.3.1 Lithium–Sulfur (Li–S)
Cathode
Interlayer
5.2.1.3.2 Sodium–Sulfur
5.2.1.3.3 Metal–Selenium
5.2.1.3.4 Metal–Air
5.2.2 Supercapacitors
5.2.2.1 Electric Double‐Layer Capacitor (EDLC)
5.2.2.1.1 Porous Carbon Nanofibers (pCNF)
5.2.2.1.2 Carbon Blends
5.2.2.2 Pseudocapacitors
5.2.2.2.1 Conductive Polymers
5.2.2.2.2 Metal Oxides
5.2.2.3 Separators
5.3 Energy Conversion Applications
5.3.1 Fuel Cells
5.3.1.1 Polymer Electrolyte Membrane Fuel Cell (PEMFC)
5.3.1.2 Alkaline Fuel Cell (AFC)
5.3.1.3 Solid Oxide Fuel Cell (SOFC)
5.3.1.3.1 Cathode
5.3.1.3.2 Anode
5.3.2 Photovoltaics
5.3.2.1 Dye‐Sensitized Solar Cells (DSSCs)
5.3.2.1.1 Photoanode
5.3.2.1.2 Electrolyte
5.3.2.2 Perovskite Solar Cells
5.3.2.3 Organic Photovoltaic (OPV)
5.4 Concluding Remarks
References
6 Electrospun Nanofibers for Drug Delivery Applications
6.1 Introduction
6.2 Methods for Encapsulation of Bioactive Molecules in Electrospun Nanofibers. 6.2.1 Blend Electrospinning
6.2.1.1 Delivery of Drugs
6.2.1.2 Delivery of Proteins
6.2.1.3 Fast‐Dissolving Electrospun Nanofibers
6.2.1.4 Stimuli–Responsive Nanofibers. 6.2.1.4.1 pH‐Dependent Release from Nanofibers
6.2.1.4.2 Temperature‐Dependent Release from Nanofibers
6.2.2 Coaxial Electrospinning
6.2.2.1 Delivery of Hydrophilic Drugs
6.2.2.2 Delivery of Hydrophobic Drugs
6.2.2.3 Delivery of Proteins, Enzymes, and Growth Factors
6.2.2.4 Delivery of Multiple Drugs
6.2.2.5 Stimuli–Responsive Nanofibers. 6.2.2.5.1 pH‐Dependent Release from Nanofibers
6.2.2.5.2 Temperature‐Dependent Release from Nanofibers
6.2.3 Emulsion Electrospinning
6.2.3.1 Single Electrospinning. 6.2.3.1.1 Delivery of Drugs
6.2.3.1.2 Delivery of Proteins, Growth Factors, Vitamins, and Hormones
6.2.3.2 Coaxial Electrospinning. 6.2.3.2.1 Delivery of Drugs
6.2.3.2.2 Delivery of Proteins and Growth Factors
6.3 Conclusion
References
7 Interfacing Electrospun Nanofibers with Microorganisms: Applications from Killing to Repelling to Delivering Living Microbes
7.1 Introduction
7.2 Brief Background on the Electrospinning Process
7.3 Electrospinning Process and Variables
7.4 Why It Is Important to Understand the Interactions Between Biomaterials and Microorganisms
7.5 Background on Antibacterial Surface Engineering
7.6 Background on Antifouling Surface Engineering
7.7 Polymer Selection for Nanofibrous Biomaterials
7.8 Electrospinning Techniques Tailor the Location of Active Agents
7.9 Blend Electrospinning Yields a Dispersed Active Agent
7.10 Coaxial and Emulsion Electrospinning Enables the Controlled Delivery of Active Agents
7.11 Coating Electrospun Mats Tailors Their Interactions with Cells
7.12 Antibacterial Nanofiber Mats
7.13 Multifaceted Delivery from Nanofibrous Mats
7.14 Antifouling Nanofiber Mats
7.15 Nanofibrous Mats Containing Living Cells
7.16 Conclusion
Acknowledgments
References
8 Advances in Functionalizing the Interior and Exterior of Polymer Nanofibers
8.1 Introduction
8.2 Nanofibers with Controlled Nanoparticle Distribution. 8.2.1 Thermodynamic Considerations of Polymer Blends
8.2.2 Hybrid Nanofibers with Polymer Blends
8.2.3 Hybrid Nanofibers in Electromagnetic Fields
8.2.4 Anisotropic Nanoparticles in Flow Fields
8.3 As‐spun Nanofibers with Bioresponsive Properties. 8.3.1 Interior Incorporation of Antimicrobial Additives
8.3.2 Exterior Biofunctionalization of Polymer Nanofibers
8.4 Polymer Nanofibers with Postfunctionalized Surfaces
8.5 Nanofibers Produced by Directed Self‐Assembly
8.6 Concluding Remarks
Acknowledgments
References
9 Nanofiber Aerogels: Bringing a Third Dimension to Electrospun Nanofibers
9.1 Aerogels
9.1.1 Processing
9.1.2 Properties and Applications
9.1.3 Challenges
9.2 Nanofiber‐Based Aerogels
9.2.1 Historical Background
9.2.2 Fabrication of Nanofiber‐Based Aerogels (NFAs)
9.2.2.1 Electrospinning
9.2.2.2 Dispersion Preparation. 9.2.2.2.1 Dispersion Liquid
9.2.2.2.2 Homogenization of the Nanofiber Dispersion
9.2.2.3 Solid Templating. 9.2.2.3.1 Freeze Drying
9.2.2.3.2 Postprocessing
9.2.3 Applications. 9.2.3.1 Filtration
9.2.3.1.1 Oil–Water Separation
9.2.3.1.2 Aerosol Filtration
9.2.3.1.3 Dye Adsorption
9.2.3.2 Thermal Insulation
9.2.3.3 Building and Lightweight Construction
9.3 Future Perspectives
References
10 Micro and Nanofibers
10.1 Electrospinning
10.2 The Melt‐blowing Process
10.2.1 The Reicofil Process
10.2.2 The Biax Multirow Process
10.2.3 The Hills Process
10.3 “Splittable” Bicomponent Fibers
10.4 Partially “Soluble” Bicomponent Fibers
10.5 Fibrillating Bicomponent Fibers
References
Index. a
b
c
d
e
f
g
h
i
k
l
m
n
o
p
q
r
s
t
u
v
w
x
y
WILEY END USER LICENSE AGREEMENT
Отрывок из книги
Edited by
.....
Studies of electrospinning polystyrene or PEO from multiple solvents indicate that dipole moment, conductivity, and key solvent properties determine electrospinnability. Supaphol and coworkers considered 18 solvents for electrospinning polystyrene. Qualitatively, they found that solvents with high boiling point and high dipole moment that resulted in polymer solutions with high conductivity, low surface tension, and low viscosity led to fiber formation and minimized needle clogging (Jarusuwannapoom et al. 2005). Using PEO, smaller fibers were observed with solvents with higher dielectric constant (Son et al. 2004) and has been the focus of further investigation.
The dielectric constant of the solvent is critical in electrospinning. Practically, it is how much electrical charge the solvent is capable of holding which affects the surface charge density. Generally, higher dielectric constants are preferred for achieving uniform surface charge density that results in uniform nanofibers. The fiber size is also affected by the dielectric constant of the solvent. For example, an approximate twofold increase in poly(lactic‐co‐glycolic acid) fiber size was observed when the solvent was switched from hexafluoro‐2‐propanol (ε ~ 17) to chloroform (ε ~ 5). A similar trend has been observed in electrospinning polymers from mixtures of solvents to tune the dielectric constant; introducing a solvent with high dielectric constant generally reduces fiber size, for example PCL from mixtures of chloroform ε ~ 5 and DMF (ε ~ 17). An approximate threefold decrease in fiber diameter was achieved by increasing the volume fraction of DMF from 0% to 10%. However, changing solvents affects conductivity, surface tension, polymer chain conformation, and solvent volatility in addition to affecting dielectric constant. Therefore, the observed changes cannot be solely attributed to dielectric constant.
.....