Designing Weldments
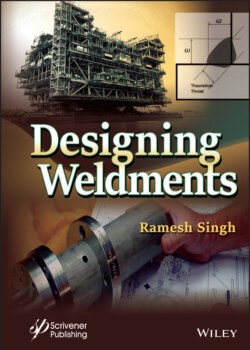
Реклама. ООО «ЛитРес», ИНН: 7719571260.
Оглавление
Группа авторов. Designing Weldments
Table of Contents
List of Tables
List of Figures
Guide
Pages
Designing Weldments
List of Figures
List of Tables
Foreword
Preface
1. Properties and Strength of Material
1.1 Introduction
2. Properties of Metals
2.1 Material Properties
2.1.1 Structure Insensitive Properties
2.1.2 Structure Sensitive Properties
2.1.3 Mechanical Properties
2.1.3.1 Modulus of Elasticity
2.1.3.2 Tensile Strength
2.1.3.3 Yield Strength
2.1.3.4 Fatigue Strength
2.1.3.5 Ductility
2.1.3.6 Elastic Limit
2.1.3.7 Impact Strength
2.1.3.7.1 Types of Impact Tests
2.1.3.7.2 IZOD Method
2.1.3.7.3 Charpy Impact Method
2.1.3.8 Energy Absorption in Impact Testing
2.1.3.9 Transition Temperature for Energy Absorption
2.1.3.10 Transition Temperature for Lateral Expansion
2.1.3.11 Drop-Weight Tear Test (DWTT)
2.1.3.12 Fracture Toughness
2.1.4 Low Temperature Properties
2.1.4.1 Metal Strength at Low Temperature
2.1.5 Elevated Temperature Properties
2.1.6 Physical Properties
2.1.6.1 Thermal Conductivity
2.1.6.2 Coefficient of Thermal Expansion
2.1.6.3 Melting Point
2.1.7 Electrical Conductivity
2.1.8 Corrosion Properties
3. Design: Load Conditions
3.1 Design of Welds
3.2 Design by Calculations
3.2.1 Different Types of Loading
3.2.2 Tension
3.2.3 Compression
3.2.4 Bending
3.2.5 Shear
3.2.6 Torsion
3.2.7 Flat Sections
3.2.8 Round Cross Sectionals
3.2.9 Transfer of Forces
4. Design of Welds and Weldments
4.1 Introduction
4.1.1 Structural Types that Affect Weld Design
4.2 Full Penetration Welds
4.3 Partial Penetration Welds
4.4 Groove Welds
4.4.1 Definitions of Terms Applicable to Groove Welds
4.4.1.1 Effective Length
4.4.1.2 Effective Size of CJP Groove Welds
4.4.1.3 Effective Weld Size (Flare Groove)
4.4.1.4 Effective Area of Groove Welds
4.5 Weld Grooves
4.5.1 Square Groove Welds
4.5.2 Single Bevel Groove Welds
4.5.3 Double Bevel Groove Weld
4.5.4 Single-V-Groove Weld
4.5.5 Double-V-Groove Welds
4.5.6 Single or Double-J-Groove Weld
4.5.7 Single or Double-U-Groove Weld
4.6 Fillet Welds
4.6.1 Definitions Applicable to Fillet Welds
4.6.1.1 Effective Length (Straight)
4.6.1.2 Effective Length (Curved)
4.6.1.3 Minimum Length
4.6.1.4 Intermittent Fillet Welds (Minimum Length)
4.6.1.5 Maximum Effective Length
4.6.1.6 Calculation of Effective Throat
4.6.1.7 Reinforcing Fillet Welds
4.6.1.8 Maximum Weld Size in Lap Joints
4.6.1.9 Effective Area of Fillet Welds
4.7 About Fillet Weld
4.7.1 Filet Weld Defined and Explained
4.7.1.1 Single Fillet Welds
4.7.1.2 Double Fillet Welds
4.7.1.3 Combined Groove and Fillet Welds
4.8 Weld Design and Loading
4.8.1 Common Conditions to Consider When Designing Welded Connections
4.8.2 Marking the Fabrication and Construction Drawings
4.8.3 Effective Areas
4.8.4 Effective Area of Groove Welds
4.9 Sizing Fillet Welds
4.9.1 Effective Length of Straight Fillet Welds
4.9.2 The Determination of Effective Throat of a Fillet Weld
4.9.2.1 Fillet Welds Joining Perpendicular Members
4.9.2.2 Fillet Weld in Acute Angle
4.9.2.3 Fillet Welds That Make Angle Between 60o and 80o
4.9.2.4 Fillet Welds That Make Acute Angle Between 60o and 30o
4.9.2.5 Reinforcing Fillet Welds
4.9.3 Fillet Welds - Minimum Size
4.9.4 Maximum Weld Size in Lap Joints
4.9.5 Skewed T-Joints
4.9.5.1 T–Joint Welds in Acute Angles Between 80° and 60° and in Obtuse Angles Greater Than 100°
4.9.5.2 T-Joint Welds in Angles Between 60° and 30°
4.9.5.3 T-Joint Welds in Angles Less than 30°
4.9.5.4 Effective Length of Skewed T-Joints
4.9.5.5 Effective Throat of Skewed T-Joints
4.9.5.6 Effective Area of Skewed T-Joints
4.10 Fillet Welds in Holes and Slots
4.10.1 Slot Ends
4.10.2 Effective Length of Fillet Welds in Holes or Slots
4.10.3 Effective Area of Fillet Welds in Holes or Slots
4.10.4 Diameter and Width Limitations
4.10.5 Slot Length and Shape
4.10.6 Effective Area of Plug and Slot Welds
4.11 Designing Calculations for Skewed Fillet Weld
4.12 Treating Weld as a Line
4.12.1 Calculation Approach
4.12.2 Finding the Size of the Weld
4.12.3 Calculated Stresses
4.12.4 Stress in Fillet Welds
4.12.5 Joint Configuration and Details
4.12.6 Compression Member Connections and Splices
4.12.7 Where There is an Issue of Through-Thickness Loading on the Base Plate
4.12.8 Determining the Capacity of Combinations of Welds
4.12.9 Corner and T-Joint Surface Contouring
4.12.10 Weld Access Holes
4.12.11 Welds with Rivets or Bolts
4.12.12 Joint Configuration and Details
4.12.12.1 Groove Welds - Transitions in Thicknesses and Widths
4.12.12.2 Partial Length CJP Groove Weld Prohibition
4.12.12.3 Flare Welds, Flare Groove and Intermittent PJP Groove Welds
4.12.12.4 Joint Configuration and Details
4.12.12.5 Termination of Fillet Welds
4.12.12.6 Fillet Welds in Holes and Slots
4.13 Design of Tubular Connections
4.13.1 Weld Joint Design
4.13.2 Uneven Distribution of Load
4.13.3 Collapse
4.13.4 Lamellar Tear and Lamination
4.13.5 Fatigue
4.14 Design for Cyclic Loading
4.14.1 Improving Fatigue Performance of Welds, and Evaluation of S-N Curves for Design
4.14.1.1 Typical Weld Flushing Plan
4.15 Aluminum
4.15.1 Aluminum Alloys and Their Characteristics
4.15.1.1 Aluminum Alloys Series 1xxx
4.15.1.2 Aluminum Alloy Series 2xxx
4.15.1.3 Aluminum Alloy Series 3xxx
4.15.1.4 Aluminum Alloy Series 4xxx
4.15.1.5 Aluminum Alloy Series 5xxx
4.15.1.6 Aluminum Alloy Series 6xxx
4.15.1.7 Aluminum Alloy Series 7xxx
4.15.2 The Aluminum Alloy Temper and Designation System
4.15.3 Wrought Alloy Designation System
4.15.4 Cast Alloy Designation
4.15.5 The Aluminum Temper Designation System
4.16 Welding Aluminum
4.16.1 Aluminum Welding Electrodes
4.16.2 Electrical Parameters
4.17 Design for Welding Aluminum
4.17.1 Effect of Welding on the Strength of Aluminum and its Alloys
4.17.2 Effect of Service Temperature
4.17.3 Type of Weld Joints for Aluminum Welding
4.17.3.1 Butt Joints
4.17.4 Lap Joint for Aluminum Welding
4.17.5 Use of T-Joints in Aluminum Welding
4.18 Distribution of Stress in Aluminum Weld Design
4.18.1 Shear Strength of Aluminum Fillet Welds
4.18.2 Fatigue Strength in Aluminum Welds
4.19 Heat and Distortion Control
4.19.1 Angular Distortion
4.19.2 Longitudinal Distortions
Circumferential Distortion
Rotational Distortion
Panel Distortion
Buckling and Wrapping
Twisting
How to Minimize Shrinkage
Preset to Offset Distortion
Over Welding, and Over Heating
Lower Heat Input
Reduce Number of Weld Pass to Reduce Excessive Heating
Preheat
Conduct Heat Away From the Weld Area
Place the Welds where the Shrinkage does Affect the Overall Dimensions and Appearance of the Weldment
5. Introduction to Welding Processes
5.1 Introduction
5.2 Shielded Metal Arc Welding (SMAW) Introduction
Process Fundamentals
How the Process Works
Power Sources
Identification of Welding Electrode
Example: E7018-1H4R
5.3 Gas Tungsten Arc Welding. Introduction
Process Description
GTAW Power Sources
AC Power Sources
The Alternator Type AC Welding Machines
Process Advantages and Limitations
5.4 Gas Metal Arc Welding. Introduction
Process Fundamentals
Equipment for GMAW Process
GMAW Power Sources
The Transformer Rectifiers
Inverters
5.5 Flux Cored Arc Welding (FCAW) Process Fundamentals
5.6 Submerged Arc Welding (SAW) Process Description
5.7 Electroslag Welding (ESW) Process Fundamentals
5.8 Plasma Arc Welding. Process Fundamentals
5.9 Stud Welding. Process Fundamentals
5.10 Oxyfuel Gas Welding. Process Fundamentals
Oxy Fuel Cutting and Shaping for Fabrication and Welding
Process Fundamentals
Purity of Oxygen
Choice of Fuel Gas
Acetylene
Propane
Methylacetylene and Propandiene (MAPP)
Propylene
Natural Gas
5.11 Hyperbaric Welding
5.12 Application of Welding Processes
6. Welding Symbols
6.1 Introduction
6.2 Common Weld Symbols and Their Meanings
6.2.1 The Basic Structure of Welding Symbol
6.2.2 Types of Welds and Their Symbols
6.3 Fillet Welds
6.3.1 The Length of the Fillet Weld
6.4 Groove Welds
6.4.1 Square Groove Welds
6.4.2 V-Groove Welds
6.5 Bevel Groove Welds
6.5.1 U-Groove Welds
6.5.2 J-Groove Welds
6.5.3 Flare-V Groove Welds
6.5.4 Flare Bevel Groove Weld
6.6 Plug and Slot Welds
7. Structural Design and Welding Specifications, and Other Useful Information. 7.1 Introduction
7.2 Structural Welding Codes
7.3 Useful Engineering Information
Index
Also of Interest. By the same Author. ARC WELDING PROCESSES HANDBOOK. 2021, 416 pages, ISBN 978-1-119-81905-9
WILEY END USER LICENSE AGREEMENT
Отрывок из книги
Scrivener Publishing
.....
The transition temperature provides somewhat similar criteria for analyzing Cv test results. This method requires Cv test over a range of temperatures from a relatively high temperature where the metal exhibits its best toughness down to a low temperature at which cleavage can initiate. The obtained energy levels are then plotted against temperature. Metal with bcc crystalline structures undergo a precipitous drop in energy over a relatively narrow mid-range span of temperature. The drop in energy coincides with the occurrence of cleavage during the fracture.
The extent of plastic deformation that occurs in the Cv specimen’s cross section during testing also is a quantifiable value, and this feature undergoes a marked transition in the bcc metals with the lowering of test temperature. When a Cv specimen is broken, a small amount of lateral contraction ordinarily occurs across the width, close to and parallel with the root of the notch, conversely expansion should occur across the width opposite the notch. Both changes in dimension from original 10 mm (0.394 inch) width of the specimen are easily measured, and both dimensional changes are indicators of ductility in the presence of a notch. The extent of lateral expansion opposite the notch is the value presently favored for appraising the capacity of metal flow plastically during fracture under impact load.
.....