Biodiesel Production
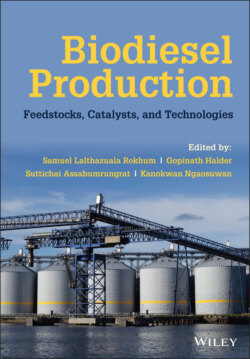
Реклама. ООО «ЛитРес», ИНН: 7719571260.
Оглавление
Группа авторов. Biodiesel Production
Table of Contents
List of Tables
List of Illustrations
Guide
Pages
Biodiesel Production: Feedstocks, Catalysts, and Technologies
Preface
List of Contributors
An Overview of Biodiesel Production
1 Advances in Production of Biodiesel from Vegetable Oils and Animal Fats
1.1 Introduction
1.2 History of the Use of Vegetable Oil in Biodiesel
1.3 Feedstocks for Biodiesel Production
1.3.1 Generations of Biodiesel
1.3.2 First‐Generation Biodiesel
1.3.3 Second‐Generation Biodiesel
1.3.4 Third‐Generation Biodiesel
1.4 Basics of the Transesterification Reaction
1.5 Variables Affecting Transesterification Reaction
1.6 Alkaline‐Catalyzed Transesterification
1.7 Acid‐Catalyzed Transesterification
1.8 Enzymatic‐Catalyzed Transesterification
1.9 Fuel Properties and Quality Specifications for Biodiesel
1.10 Conclusion
References
2 Green Technologies in Valorization of Waste Cooking Oil to Biodiesel
2.1 Introduction. 2.1.1 The Necessity for Biodiesel
2.1.2 Sourcing the Correct Precursor
2.2 Importance of Valorization
2.3 Purification and Characterization
2.4 Transesterification: A Comprehensive Look
2.5 Conversion Techniques
2.5.1 Traditional Conversion Approaches
2.5.1.1 Acid Catalysis
2.5.1.2 Alkali Catalysis
2.5.1.3 Enzyme Catalysis
2.5.1.4 Other Novel Heterogeneous Catalysts
2.5.1.5 Two‐Step Catalyzed Process
2.5.2 Modern Conversion Approaches. 2.5.2.1 Supercritical Fluids
2.5.2.2 Microwave Irradiation
2.5.2.3 Ultrasonication
2.6 Economics and Environmental Impact
2.7 Conclusion and Perspectives
References
3 Non‐edible Oils for Biodiesel Production: State of the Art and Future Perspectives
3.1 Introduction
3.2 Vegetable Non‐edible Oils. 3.2.1 General Cultivation Data
3.2.2 Composition and Chemical–Physical Properties of Biodiesel Obtained from Non‐edible Vegetable Oils
3.2.3 Biodiesel Production from Non‐edible Vegetable Oil
3.2.3.1 Extraction Methods
3.2.3.2 Biodiesel Production
3.2.4 Criticisms Related to Non‐edible Oils
3.3 Future Perspectives of Non‐edible Oils: Oils from Waste
3.4 Conclusion
Acknowledgments
References
4 Algal Oil as a Low‐Cost Feedstock for Biodiesel Production
4.1 Introduction
4.1.1 Microalgae for Biodiesel Production
4.2 Lipid and Biosynthesis of Lipid in Microalgae
4.2.1 Lipid Biosynthesis
4.2.2 Lipid Extraction
4.3 Optimization of Lipid Production in Microalgae
4.3.1 Nitrogen Stress
4.3.2 Phosphorous Stress
4.3.3 pH Stress
4.3.4 Temperature Stress
4.3.5 Light
4.4 Conclusion
References
5 Homogeneous Catalysts Used in Biodiesel Production
5.1 Introduction
5.2 Transesterification in Biodiesel Synthesis
5.3 Homogeneous Catalyst in Biodiesel Synthesis
5.3.1 Homogeneous Acid Catalyst
5.3.2 Homogeneous Base Catalyst
5.4 Properties of Biodiesel Produced by Homogeneous Acid and Base‐Catalyzed Reactions
5.5 Relevance of Homogeneous Acid and Base Catalysts in Biodiesel Synthesis
5.6 Conclusion
References
6 Application of Metal Oxides Catalyst in Production of Biodiesel
6.1 Basic Metal Oxide
6.1.1 Monobasic Metal Oxide. 6.1.1.1 Alkaline Earth Metal Oxide
6.1.1.2 Transition Metal Oxide
6.1.2 Multibasic Metal Oxide
6.1.2.1 Supported on Metal Oxide
6.1.2.2 Supported on Activated Carbon
6.1.2.3 Supported on Metal Organic Framework
6.1.3 Active Site‐Doped Basic Metal Oxide
6.1.3.1 Alkali Metal Doped
6.1.3.2 Active Metal Oxide Doped
6.1.4 Mechanism of Transesterification Catalyzed by Basic Metal Oxide
6.2 Acid Metal Oxide
6.2.1 Monoacid Metal Oxide
6.2.2 Multiacid Metal Oxide
6.2.3 Supported on Metal Organic Framework
6.2.4 Mechanism of Transesterification/Esterification Catalyzed by Acid Metal Oxide
6.3 Deactivation of Metal Oxide
References
7 Supported Metal/Metal Oxide Catalysts in Biodiesel Production: An Overview
7.1 Introduction
7.2 Supported Catalyst
7.3 Metals and Metal Oxide Supported on Alumina
7.4 Metals and Metal Oxide Supported on Zeolite
7.5 Metals and Metal Oxide Supported on ZnO
7.6 Metals and Metal Oxide Supported on Silica
7.7 Metals and Metal Oxide Supported on Biochar
7.7.1 Solid Acid Catalysts
7.7.2 Solid Alkali Catalysts
7.8 Metals and Metal Oxide Supported on Metal Organic Frameworks
7.9 Metal/Metal Oxide Supported on Magnetic Nanoparticles
7.10 Summary
References
8 Mixed Metal Oxide Catalysts in Biodiesel Production
8.1 Introduction
8.2 Previous Research
8.3 State of the Art
8.3.1 Solid Acid MMO Catalysts
8.3.2 Solid Base MMO Catalysts
8.3.3 Solid Bifunctional MMO Catalysts
8.4 Discussion
8.5 Conclusion
8.6 Symbols and Nomenclature
References
9 Nanocatalysts in Biodiesel Production
9.1 Introduction
9.2 Transesterification of Vegetable Oils
9.3 Conventional Catalysts Used in Biodiesel Production: Advantages and Limitations
9.3.1 Homogeneous Catalysts
9.3.2 Heterogeneous Catalysts
9.3.3 Biocatalysts
9.4 Role of Nanotechnology in Biodiesel Production
9.5 Different Nanocatalysts in Biodiesel Production
9.5.1 Metal‐Based Nanocatalysts
9.5.2 Carbon‐Based Nanocatalysts
9.5.3 Zeolites/Nanozeolites
9.5.4 Magnetic Nanocatalysts
9.5.5 Nanoclays
9.5.6 Other Nanocatalysts
9.6 Conclusion
Acknowledgment
References
10 Sustainable Production of Biodiesel Using Ion‐Exchange Resin Catalysts
10.1 Introduction
10.2 Features of Ion‐Exchange Resin Catalysts
10.3 Cation‐Exchange Resin Catalyst. 10.3.1 Notes of Caution When Comparing the Activity of Resins with Different Properties
10.3.2 Reversible Reduction of Resin Catalytic Activity by Water
10.3.3 Search for Operating Conditions for Maximum Productivity Rather than Maximum Catalytic Activity
10.3.4 Challenges Regarding One‐Step Reaction with Simultaneous Esterification and Transesterification Catalyzed by Cation‐Exchange Resin
10.4 Anion‐Exchange Resin Catalysts. 10.4.1 Requirements for High Catalytic Activity in the Transesterification of Triglycerides
10.4.2 Analysis of Previous Studies
10.4.3 Decreased Catalytic Activity and Regeneration Method
10.4.4 Additional Functions Unique to Anion‐Exchange Resins
10.5 Summary
References
11 Advances in Bifunctional Solid Catalysts for Biodiesel Production
11.1 Introduction
11.2 Application of Solid Bifunctional Catalyst in Biodiesel Production. 11.2.1 Acid–Base Bifunctional Catalysts
11.2.1.1 Oxides of Acid–Base
11.2.1.2 Acid–Base Hydrides
11.2.2 Bifunctional Acid Catalyst
11.2.2.1 Bifunctional Brønsted–Lewis Acid Oxides
11.2.2.2 Heteropolyacid‐Based Bifunctional Catalyst
11.2.3 Biowaste‐Derived Bifunctional Catalyst
11.3 Summary and Concluding Remarks
Acknowledgment
References
12 Application of Catalysts Derived from Renewable Resources in Production of Biodiesel
12.1 Introduction
12.2 Potential Renewable Resources for Production of Biodiesel Catalysts
12.2.1 Animal Resources
12.2.1.1 Eggshells (Chicken and Ostrich)
12.2.1.2 Seashells (Snail, Mussel, Oyster, and Capiz)
12.2.1.3 Bones
12.2.2 Plant Resources
12.2.2.1 Carbon‐Supported Catalysts
12.2.2.2 Silica‐Supported Catalysts
12.2.2.3 Other Potential Elements from Plant Residues
12.2.3 Natural Resources. 12.2.3.1 Dolomitic Rock (Calcined Dolomite and Modified Dolomite)
12.2.3.2 Lime
12.2.3.3 Natural Clays
12.2.3.4 Zeolites
12.2.4 Industrial Waste Resources
12.2.4.1 Food Industry Wastes
12.2.4.2 Mining Industry Wastes
12.3 Advantages, Disadvantages, and Challenges of These Types of Catalyst for Biodiesel Production
Acknowledgment
References
13 Biodiesel Production Using Ionic Liquid‐Based Catalysts
13.1 Introduction
13.2 Mechanism of IL‐Catalyzed Biodiesel Production
13.3 Acidic and Basic Ionic Liquids (AILs/BILs) as Catalyst in Biodiesel Production
13.4 Supported Ionic Liquids in Biodiesel Production
13.5 IL Lipase Cocatalysts
13.6 Optimization and Novel Biodiesel Production Technologies Using ILs
13.7 Recyclability of the Ionic Liquids on Biodiesel Production
13.7.1 Recovery of ILs
13.7.2 Reuse of Ionic Liquids
13.8 Kinetics of IL‐Catalyzed Biodiesel Production
13.9 Techno‐Economic Analysis and Environmental Impact Analysis of Biodiesel Production Using Ionic Liquid as Catalyst
13.10 Conclusion
Abbreviations
References
14 Metal–Organic Frameworks (MOFs) as Versatile Catalysts for Biodiesel Synthesis
14.1 Introduction
14.1.1 Metal‐Containing Secondary Building Units
14.1.2 Organic Linker
14.1.3 Pore Volume
14.2 Biodiesel Synthesis Over MOF Catalysts
14.2.1 Transesterification Reaction
14.2.1.1 Transesterification at SBUs of MOFs
14.2.1.2 Transesterification at Linker Active Sites
14.2.2 Esterification of Carboxylic Acids
14.2.2.1 Esterification of Carboxylic Acids at SBUs of MOFs
14.2.2.2 Esterification of Carboxylic Acids at Linker Active Sites
14.2.2.3 Esterification at Pore Volume (Guest Incorporation)
14.3 Conclusion
References
15 Upstream Strategies (Waste Oil Feedstocks, Nonedible Oils, and Unicellular Oil Feedstocks like Microalgae)
15.1 Introduction
15.1.1 Classification of Biodiesel
15.1.2 Commercial Production of Biodiesel
15.2 Biodiesel Feedstocks
15.2.1 Edible Oils as Feedstock for Biodiesel Production
15.2.2 Nonedible Oils as Feedstocks for Biodiesel Production
15.2.3 Waste Feedstocks (Waste Cooking Oils, Waste Animal Fats, Waste Coffee Ground Oil, Olive Pomace)
15.2.4 Unicellular Oil Feedstocks (Microalgae, Yeasts, Cyanobacteria)
15.3 Composition of Oils and Fats
15.4 Methods for Oil Extraction
15.4.1 Mechanical Extraction
15.4.2 Solvent Extraction
15.4.3 Enzymatic Extraction
15.5 Purification of Oils and Fats
15.5.1 Deacidification
15.5.2 Winterization
15.5.3 Demetallization
15.5.4 Degumming
15.6 Production of Biodiesel
15.6.1 Catalysts for Biodiesel Production
15.6.2 Homogeneous Catalysts
15.6.3 Heterogeneous Catalysts
15.7 Future Prospects
References
16 Mainstream Strategies for Biodiesel Production
16.1 Introduction
16.2 Mainstream Strategies and Technology for Biodiesel Production. 16.2.1 Current Mainstream Operation. 16.2.1.1 Batch Mode
16.2.1.2 Continuous Mode
16.2.2 Process Mainstream for Biodiesel Production Based on the Reactor Types. 16.2.2.1 Rotating Reactor
16.2.2.1.1 Spinning Disk Reactor (SDR)
16.2.2.1.2 Rotating Tube Reactor (RTR)
16.2.2.2 Tubular Flow Reactor
16.2.2.2.1 Packed Bed Reactor
16.2.2.2.2 Oscillatory Flow Reactor
16.2.2.2.3 Microchannel Reactor
16.2.2.2.4 Static Mixer Reactor
16.2.2.3 Cavitational Reactor
16.2.2.3.1 Acoustic Cavitation Reactor/Ultrasonic Cavitation Reactor
16.2.2.3.2 Hydrodynamic Cavitation Reactor
16.2.2.3.3 Shockwave Power Reactor
16.2.2.4 Microwave Reactor
16.2.2.5 Multifunctional Reactor (Reactive Distillation, Membrane, Centrifugal Reactors) 16.2.2.5.1 Reactive Distillation
16.2.2.5.2 Membrane Reactor
16.2.2.5.3 Centrifugal Reactor
16.2.2.6 Other Process Intensification
16.3 Future Prospects and Challenges
Acknowledgment
References
17 Downstream Strategies for Separation, Washing, Purification, and Alcohol Recovery in Biodiesel Production
17.1 Introduction
17.1.1 Factors Affecting Biodiesel Yield
17.1.2 Transesterification Reaction Conditions
17.1.3 Separation After FAME Conversion
17.1.4 Washing
17.2 Glycerol Separation and Refining
17.3 Membrane Reactors
17.4 Methanol Recovery
17.5 Additization
17.6 Conclusion
References
18 Heterogeneous Catalytic Routes for Bio‐glycerol‐Based Acrylic Acid Synthesis
18.1 Introduction
18.2 Acrylic Acid Synthesis from Propylene
18.3 Acrylic Acid Synthesis from Glycerol
18.3.1 Glycerol Dehydration to Acrolein
18.3.2 Acrylic Acid Synthesis from Glycerol
18.4 Conclusion
Acknowledgments
References
19 Sustainability, Commercialization, and Future Prospects of Biodiesel Production
19.1 Introduction
19.2 Biodiesel as a Promising Renewable Energy Carrier
19.3 Overview of the Biodiesel Production Process
19.4 Evolution in the Feedstocks Used for the Sustainable Production of Biodiesel
19.5 First‐Generation Biodiesel and the Challenges in Its Sustainability
19.6 Development of Second‐Generation Biodiesel to Address the Sustainability
19.7 Algae‐Based Biodiesel
19.8 Waste Oils, Grease, and Animal Fats in Biodiesel Production
19.9 Technical Impact by the Biodiesel Usage
19.10 Socioeconomic Impacts
19.11 Toxicological Impact
19.12 Sustainability Challenges in the Biodiesel Production and Use
19.13 Concluding Remarks
References
20 Advanced Practices in Biodiesel Production
20.1 Introduction
20.2 Mechanism of Transesterification
20.3 Advanced Biodiesel Production Technologies. 20.3.1 Production of Biodiesel Using Membrane Reactor. 20.3.1.1 Principle
20.3.2 Microwave‐Assisted Transesterification Technology. 20.3.2.1 Principle
20.3.3 Ultrasonic‐Assisted Transesterification Techniques
20.3.4 Production of Biodiesel Using Cosolvent Method. 20.3.4.1 Principle
20.3.5 In Situ Biodiesel Production Technology. 20.3.5.1 Principle
20.3.6 Production of Biodiesel Through Reactive Distillation Process. 20.3.6.1 Principle
20.4 Conclusion
20.5 Future Perspectives
References
Index. a
b
c
d
e
f
g
h
i
j
k
l
m
n
o
p
r
s
t
u
v
w
y
z
WILEY END USER LICENSE AGREEMENT
Отрывок из книги
Edited by
Dr. Samuel Lalthazuala Rokhum
.....
Armando T. Quitain Faculty of Advanced Science and Technology, Kumamoto University Kumamoto, Japan Center for International Education Kumamoto University, Kumamoto, Japan
Umer Rashid Institute of Nanoscience and Nanotechnology (ION2), Universiti Putra Malaysia, Serdang Selangor, Malaysia
.....