Maintenance, Reliability and Troubleshooting in Rotating Machinery
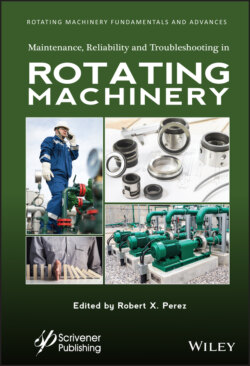
Реклама. ООО «ЛитРес», ИНН: 7719571260.
Оглавление
Группа авторов. Maintenance, Reliability and Troubleshooting in Rotating Machinery
Table of Contents
List of Illustrations
List of Tables
Guide
Pages
Maintenance, Reliability and Troubleshooting in Rotating Machinery
Dedication
Preface
Acknowledgements
1. Machinery Reliability Management in a Nutshell
Criticality
Environmental Consequences
Safety Consequences
Equipment History
Safeguards
Compressor Operating Limits
Compressor Flow Limits
Critical Speeds
Horsepower Limits
Temperatures
Layers of Machinery Protection
Machinery Reliability Assessment Example. Background
History
Safeguards
Conclusion
Closing Remarks
2. Useful Analysis Tools for Tracking Machinery Reliability
Commonly Used Metrics for Spared Machinery: Mean Time to Repair (MTTR)
Mean Time Between Failure (MTBF)
Additional Reliability Assessment Tools for Spared Machines
Pareto Charts & 80-20 Rule
Cumulative Failure Trends
Metrics for Critical Machines
Availability
Critical Machine Events
Process Outage Trends
Process Outage Related to Machinery Outages
Planned Maintenance Percentage (PMP)
Reliability Analysis Capabilities of your CMMS Software
3. Improving the Effectiveness of Plant Operators
Look, Listen and Feel
Applying Look, Listen, and Feel Techniques to Troubleshooting
Why the Operator’s Input is Important to the Troubleshooting Process
Operator Tools
Understanding the Equipment – Pumps, Seals and Sealing Support Systems
Centrifugal Pump Relationships to Remember
Positive Displacement Pump Relationships to Remember
Mechanical Seals
Capital Projects
Writing Quality Work Request
Procedures (Procedures and Decision Trees)
Must Give Operators Feedback
Must be Required to Use their Training
Discipline
Conclusion
Appendix A References
4. Spare Parts Strategies for Optimizing Rotating Machinery Availability
Some Stocking Examples
Capital Spares
Insurance Spares
Analyzing Spare Part Inventories Using Monte Carlo Simulations
Closing
Some Definitions Related to Spare Parts
5. Switch-Over Methodology and Frequency Optimization for Plant Machinery
Machinery Switchover Frequency Optimization Benefits
Time-Dependent Issues Involved in Setting Switchover Frequency for Standby Machines
Frequent Switchover Introduces the Following Negative Impact to Rotating Equipment
Calculation of Start-Stop Damaging Cycles for A, B Configured Equipment: See Definitions Below for More Information
Definitions
Examples of Short Start-Stop Intervals in Process Machinery
Philosophy of Reliability-Centered Switchover Strategy
6. Evaluating Centrifugal Pumps in Petrochemical Applications
Crude Oil Processing
Desalting
Crude Oil Distillation
Properties of Distillation and Fractionator Fractions
Defining NPSHr, NPSH3, and NPSH Margin
Natural Gas Processing: NGL Processing
Centrifugal Pump Design Audits
Design Standards
The Materials of Construction
The Hydraulic Fit
The NPSH Margin [4]
Seal and Seal Flush Design
Challenging Pump Applications
Pumps Operating in Parallel
Pump Liquids with Low Densities
Low NPSH Services
How an Impeller’s Suction Specific Speed Affects the Required NPSH [4]
Pumps Handling a Liquid with Varying Densities
Slurry Pumps [5]
FCC Slurry Pumps
Bottoms Pumps
Hot Pumps with Galling Tendencies
Starting Hot Pumps [6]
High Temperature Concerns
Gaskets [7]
O-Rings
How Processing Issues Can Affect Pump Reliability
Summary
Acknowledgement
References
7. Practical Ways to Improve Mechanical Seal Reliability
Seal Reliability Tracking
MTBR Data from Across the Industry
Reliability Tracking Tools
Bad Actors
Mechanical Seal Best Practices
Improved Mechanical Seal Support System Designs [2]
Reducing Potential Leak Points
Simplifying Operation and Maintenance
Building Better Seal Support Systems
Common Mechanical Sealing Design Challenges. Sealing Light Hydrocarbon Liquids
Sealing Hazardous Organic NESHAP Liquids
Buffer Gas Absorption
Excessive Solids
Seal Cooler Issues in Hot Applications [3]
Piping Plan 21
Advantages
Disadvantages
Piping Plan 23
Advantages
Disadvantages
Common Considerations for Flush Plans
General Seal Piping Plan Recommendations
Ways to Improve Seal Reliability Performance
Seal Failure Analysis [4]
Common Seal Failure Modes
Seal Failure Inspection Notes
Possible Causes
Meeting with Manufacturer
Writing the Seal Failure Report with Recommendations
Post-Analysis Activities
Justifying Seal Upgrades
Closing Thoughts
References
8. Proven Ways to Improve Steam Turbine Reliability
Repairs versus Overhauls
Expected Lifetimes of Steam Turbines and Their Components
Common Failure Modes
Steam Turbine Leaks
Bearing and Lubrication Failures
Governor Failures and Sticking T&T Valves
Improvement Reliability by Design
Acknowledgements
9. General Purpose Steam Turbine Reliability Improvement Case Studies
Governor Valve Packing Gland Leakage: Sealing & Reliability Improvements
Steam Turbines Carbon Seals Upgrade to Mechanical Seals
Typical Benefits of Dry Gas Seal in a 1500 HP Turbine
Modification of GP Turbines for Fast Start without Slow Rolling
How the GP Turbine Fast Startup Modification Works
Dry Flexible Metal Coupling Upgrade with Split Spacer, for Short Coupled Turbines with Insufficient Length Coupling Spacers
General Purpose Lube Oil System Upgrade for Self-Contained Bearing Housings to Eliminate Overheating & Bearing Failures
Governor and Trip System Upgrade from Hydraulic to Electronic-Pneumatic
Governor Requirements:
Electronic Governor with Pneumatic Actuator & Pneumatic Trip System
Governor and Trip System Requirements
Overview of All-Electronic Trip and Overspeed Protection System
Outboard Bearing Improved Flex Foot: Higher Turbine Reliability & Lower Vibration
Results
10. Rotating Machinery Repair Best Practices
World-Class Reliability Performance Should be the Goal of Every Repair Facility
Cutting Corners = Unreliability
The Importance of Alignment
Alignment Tolerances [2]
Alternative Alignment Guidelines
Alignment Calculation Example
Rotor Balance
Imperial Units
Metric Units
Static Unbalance
Dynamic Unbalance
Balancing
Common Causes of Rotor Unbalance [3]
Balancing Grades
The Importance of Fit, Clearance & Tolerance
Fits, Clearances and Tolerances [5]
Tolerance
Clearance
Coupling Hub Fits
Keyed Interference Fits [6]
Keyless Interference Fits
Effects of Excessive Looseness
Rotating Element Looseness
Effects of Internal Looseness
Structural Looseness
As Found and As Left Measurements
Closing Thoughts
References
11. Procedures + Precision = Reliability
12. The Top 10 Behaviors of Precision-Maintenance Technicians
13. Optimizing Machinery Life Cycle Costs through Precision and Proactive Maintenance
Precision Maintenance 101
Life-Extension Equations
Worked Example
Life Cycle Costs
Considering Energy Consumption
Life Cycle Inventory Analysis
Justifying Precision Maintenance. Estimating the Benefits
Now for the Cost-Benefit Analysis
14. Optimum Reference States for Precision Maintenance
Fasteners
Lubrication
Alignment
Balance
Flab Management
Conclusion
15. Writing Effective Machinery Work Order Requests
16. Improving Machinery Reliability by Using Root Cause Failure Analysis Methods
Introduction
What Is a Root Cause Failure Analysis?
Root Cause Failure Analysis Example #1: Ill-Advised Bearing Replacement. History
Corrective Measures
Comments
Root Cause Failure Analysis Example #2: Reciprocating Compressor Rod Failure [1] Background
Physical root cause
Latent root causes
Comments
RCFA Steps
Step 1: Define the Problem
Step 2: Gather Data/Evidence
Identifying the Physical Root Cause of the Primary Failure
Fatigue Example: Fin-Fan Cooler Shaft Failures
Preserving Machine Data
Step 3: Ask Why and Identify the Causal Relationships Associated with the Defined Problem
Causal Chains
Bearing Failure Sequence of Events with Descriptions
Five Why RCFA Example
Cause Mapping [2]
Cause Map Example #2
Single Root Cause versus Multiple Causes
Cause Mapping Steps
Inhibitors to Effective Problem Solving [3]
When Is a Root Cause Failure Analysis Justified?
RCFA Levels
Closing Thoughts
Appendix A. No Magic Allowed. Identifying Sequence of Events and Causal Chains
5-Why Method of Investigation
Advice on Failure Sequences
Appendix B. Analyzing Component Failure Mechanisms
Common Mechanical Failure Modes. Foreign Object Damage (FOD)
Stress Corrosion Cracking
Erosion
Cavitation
Hydrogen Embrittlement
Galling
Fretting
Hot Corrosion (Gas Turbines) [4]
Common Hydrodynamic Bearing Failure Modes [5]
Rolling Element Bearing Failure Characteristics [6]
Tips for Analyzing Mechanical Seal Failures [7]
Common Seal Failure Modes
Appendix C. Common Machinery Failure Modes [8]
Pluggage
Erosive Wear
Fatigue
Compressor Blade Fatigue Example
Hydrodynamic Bearing Failure Examples
Rubbing
Unique Failure Modes
References
17. Investigation and Resolution of Repetitive Fractionator Bottom Pump Failures
Introduction
List of Additional Failure Inherent Causes to Be Rectified
Key Shop and Field Pump Measurements
Conclusion [1]
Actual Findings
Effect of Improvements on Pump Radial Shaft Vibration
Reference
18. Reliability Improvements Made to 6000 KW Water Injection Pumps Experiencing Wear Ring Failures
Summary
Sequence of Events
New Design Proposal of Eliminating Grub Screws or Flash Butt Welding. Example: Wear ring ID = 8.0 inches. Apply Taper Fit Principle
Upgrade Options
Detailed Analysis of Problem & Solution Related to All Pump Wear Rings
Discussion on Reliability Improvements Added to Achieve High Reliability
The Five Root Causes of Machinery Failure
Design Errors
Manufacturing Errors: None Found. User Specification Errors
User Maintenance Errors: None Found
About the Editor
About the Contributors
Index
Also of Interest. Other books by the same editor
Check out these other titles from Scrivener Publishing
WILEY END USER LICENSE AGREEMENT
Отрывок из книги
Scrivener Publishing
.....
A possible reliability strategy for a critical compressor might look like this:
There is no generic maintenance strategy for all the different types of rotating machinery. Each situation must be evaluated based on the historical failure mode, their consequences, and your maintenance budget. Some trial and error may be needed to identify the right mix of maintenance strategies.
.....