Fundamentals of Heat Engines
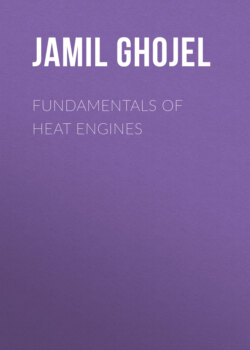
Реклама. ООО «ЛитРес», ИНН: 7719571260.
Оглавление
Jamil Ghojel. Fundamentals of Heat Engines
Table of Contents
List of Tables
List of Illustrations
Guide
Pages
Wiley-ASME Press Series
Fundamentals of Heat Engines
Copyright
Series Preface
Preface
Glossary. Symbols
Greek Symbols
Subscripts
Superscripts
Abbreviations
About the Companion Website
Part I. Fundamentals of Engineering Science. Introduction I: Role of Engineering Science
1 Review of Basic Principles. 1.1 Engineering Mechanics
1.1.1 Definitions
1.1.2 Newton's Laws of Motion
1.1.3 Rectilinear Work and Energy
1.1.4 Circular Motion
1.1.4.1 Uniform Circular Motion of a Particle
1.1.5 Rotating Rigid‐Body Kinetics
1.1.6 Moment, Couple, and Torque
1.1.7 Accelerated and Decelerated Shafts
1.1.8 Angular Momentum (Moment of Momentum)
1.1.9 Rotational Work, Power, and Kinetic Energy
1.2 Fluid Mechanics
1.2.1 Fluid Properties. 1.2.1.1 Mass and Weight
1.2.1.2 Pressure
1.2.1.3 Compressibility
1.2.1.4 Viscosity
1.2.2 Fluid Flow
1.2.2.1 General Energy Equation
1.2.3 Acoustic Velocity (Speed of Sound)
1.2.4 Similitude and Dimensional Analysis
1.2.4.1 Dimensional Analysis
1.2.4.2 Buckingham Pi (π) Theorem
1.3 Thermodynamics
1.3.1 Work and Heat as Different Forms of Energy
1.3.2 Mixture of Gases
Example 1.1
Solution
1.3.2.1 Dalton Model of Gas Mixtures
1.3.3 Processes in Ideal Gas Systems
1.3.3.1 Adiabatic Processes
1.3.3.2 Heat‐Only Process
1.3.3.3 Isothermal Process
1.3.3.4 Isochoric Process
1.3.3.5 Polytropic Process
1.3.4 Cycles
1.3.5 First Law of Thermodynamics
1.3.5.1 Non‐Flow Energy Equation
1.3.5.2 Steady‐Flow Energy Equation
1.3.5.3 Stagnation Properties
1.3.5.4 Isentropic Flow
1.3.5.5 Speed Parameter
1.3.5.6 Mass Flow Parameter
1.3.5.7 Applications of the Energy Equation
1.3.6 Second Law of Thermodynamics
1.3.6.1 Entropy
1.3.7 The Carnot Principle
1.3.8 Zeroth Law of Thermodynamics
1.3.8.1 Thermodynamic Scale of Temperature
1.3.9 Third Law of Thermodynamics
Problems. Engineering Mechanics
Fluid Mechanics
Thermodynamics
2 Thermodynamics of Reactive Mixtures
2.1 Fuels
2.2 Stoichiometry
2.3 Chemical Reactions. 2.3.1 Fuels Having a Single Chemical Formula
2.3.2 Multi‐Component Gaseous Fuels
Example 2.1
2.3.3 Fuels with Known Mass Concentration of the Constituent Elements
2.3.3.1 Air‐Fuel Ratios
2.3.3.2 Products of Complete Combustion (λ ≥ 1)
2.3.3.3 Products of Incomplete Combustion (λ< 1)
Example 2.2
2.4 Thermodynamic Properties of the Combustion Products
2.5 First Law Analysis of Reacting Mixtures
2.5.1 Non‐Flow Process with Chemical Reactions
2.5.2 Steady‐State System with Chemical Reactions. 2.5.2.1 Enthalpy of Formation
2.5.2.2 Enthalpy of Reaction
Example 2.3
2.6 Adiabatic Flame Temperature. 2.6.1 Steady‐State Process
Example 2.4
Solution
2.6.2 Constant‐Volume Combustion Process
2.7 Entropy Change in Reacting Mixtures. 2.7.1 Absolute Entropy
2.8 Second Law Analysis of Reacting Mixtures
Example 2.5
2.9 Chemical and Phase Equilibrium
2.9.1 Gibbs and Helmholtz Functions and Equilibrium
2.9.2 Equilibrium Constant
2.9.2.1 Equilibrium Constant of Formation
2.9.3 Dissociation and Equilibrium Composition
2.10 Multi‐Species Equilibrium Composition of Combustion Products. 2.10.1 Frozen Composition
2.10.2 Equilibrium Composition
2.10.2.1 Six Species in the Products
2.10.2.2 Eleven Species in the Products
2.10.2.3 Eighteen Species in the Products
Problems
Part II. Reciprocating Internal Combustion Engines. Introduction II: History and Classification of Reciprocating Internal Combustion Engines
3 Ideal Cycles for Natural‐Induction Reciprocating Engines
3.1 Generalised Cycle
3.2 Constant‐Volume Cycle (Otto Cycle)
3.3 Constant Pressure (Diesel) Cycle
3.4 Dual Cycle (Pressure‐Limited Cycle)
3.5 Cycle Comparison
Problems
4 Ideal Cycles for Forced‐Induction Reciprocating Engines
4.1 Turbocharged Cycles
4.1.1 Turbocharged Engine with Constant‐Pressure Turbine
4.1.1.1 Thermal Efficiency
4.1.1.2 Mean Effective Pressure
4.1.2 Turbocharged Engine with Variable‐Pressure Turbine
4.1.2.1 Thermal Efficiency
4.1.2.2 Mean Effective Pressure
4.2 Supercharged Cycles
4.2.1 Thermal Efficiency
4.2.2 Mean Effective Pressure
4.3 Forced Induction Cycles with Intercooling
4.3.1 Cycle with Constant‐Pressure Turbine and Intercooling
4.3.1.1 Cooling Process
4.3.1.2 Thermal Efficiency
4.3.1.3 Mean Effective Pressure
4.3.2 Cycle with Variable‐Pressure Turbocharging and Intercooling
4.3.2.1 Cooling Process
4.3.2.2 Thermal Efficiency
4.3.2.3 Mean Effective Pressure
4.3.3 Cycle with Supercharging and Intercooling
4.3.3.1 Cooling Process
4.3.3.2 Thermal Efficiency
4.3.3.3 Mean Effective Pressure
4.4 Comparison of Boosted Cycles
Problems
5 Fuel‐Air Cycles for Reciprocating Engines
5.1 Fuel‐Air Cycle Assumptions
5.2 Compression Process
5.3 Combustion Process
Example 5.1
5.3.1 Constant‐Volume Combustion Cycle (Otto Cycle)
5.3.2 Constant‐Pressure Cycle (Diesel Cycle)
5.4 Expansion Process
5.5 Mean Effective Pressure
5.6 Cycle Comparison
Problems
6 Practical Cycles for Reciprocating Engines
6.1 Four‐Stroke Engine
6.1.1 The Induction Process a − b − c − d − e
6.1.2 The Compression Process e − f
6.1.3 The Combustion and Expansion Processes f − g − h − i
6.1.4 The Exhaust Process i − j − a − b − c
6.2 Two‐Stroke Engine
6.2.1 Compression Processes 5 − 1
6.2.2 Combustion and Expansion Processes 1 − b − c − 2
6.2.3 Exhaust and Induction Processes 2 − 3 − a − 4 − 5
6.3 Practical Cycles for Four‐Stroke Engines
6.3.1 Compression Ignition Engine (CI Engine)
6.3.1.1 Induction Process
6.3.1.2 Compression Process
6.3.1.3 Combustion Process
6.3.1.4 The Expansion Process
6.3.1.5 Cycle Work and Mean Effective Pressure
6.3.2 Spark Ignition Engine (SI Engine)
6.3.2.1 Combustion Process
6.3.2.2 Expansion Process
6.3.2.3 Cycle Work and Mean Effective Pressure
6.3.3 Constant‐Pressure Combustion Engine
6.3.3.1 Combustion Process
6.3.3.2 Expansion Process
6.3.3.3 Cycle Work and Mean Effective Pressure
6.4 Cycle Comparison
6.5 Cycles Based on Combustion Modelling (Wiebe Function)
6.5.1 The Wiebe Function
6.5.2 Cycle Calculation Using Wiebe Function
6.6 Example of Wiebe Function Application
6.6.1 SI Engine
6.6.2 CI Engine
6.7 Double Wiebe Models
6.7.1 Rapid Combustion Phase
6.7.2 Diffusion Phase
6.8 Computer‐Aided Engine Simulation
Problems
7 Work‐Transfer System in Reciprocating Engines
7.1 Kinematics of the Piston‐Crank Mechanism
7.2 Dynamics of the Reciprocating Mechanism
7.2.1 Mass‐Distribution Scheme
7.2.1.1 Masses at the Piston Pin
7.2.1.2 Masses at the Crank Pin
7.2.2 Forces Acting on the Reciprocating Mechanism
7.2.2.1 Forces Acting on the Piston Pin
7.2.2.2 Forces Acting on the Crank Pin
7.2.2.3 Forces and Moments Acting on the Crankshaft Supports at Point O
7.2.2.4 Resultant Forces Acting on the Crank Pin
7.2.2.5 Polar Diagram
7.2.2.6 Resultant Forces Acting on the Crankshaft Bearing Journals
7.3 Multi‐Cylinder Engines
7.3.1 Torque in Multi‐Cylinder Engines
7.3.1.1 Torque Uniformity Factor (TUF)
7.3.2 Engine‐Speed Fluctuations
7.4 Engine Balancing
7.4.1 Single‐Cylinder Engine
7.4.2 Multi‐Cylinder Engines
7.4.2.1 Two‐Cylinder Inline Engine
7.4.2.2 Two‐Cylinder V‐Engine
7.4.2.3 Balancing an Eight‐Cylinder V‐Engine
7.4.2.3.1 Second‐Order Inertial Forces
7.4.2.3.2 First Order Inertial Forces
7.4.2.3.3 Rotating (Centrifugal) Inertial Forces
7.4.2.4 Other Engine Configurations
Problems
8 Reciprocating Engine Performance Characteristics. 8.1 Indicator Diagrams
8.2 Indicated Parameters
8.2.1 Indicated Work
8.2.2 Indicated Power
8.2.3 Indicated Specific Fuel Consumption
8.2.4 Indicated Efficiency
8.2.5 Indicated Mean Effective Pressure
8.2.6 Indicated Power
8.3 Brake Parameters
8.3.1 Brake‐Specific Fuel Consumption
8.3.2 Brake Efficiency
8.3.3 Brake Mean Effective Pressure
8.3.4 Brake Power
8.4 Engine Design Point and Performance
8.4.1 Design Point Calculations
8.4.2 Engine Performance Characteristics
8.5 Off‐Design Performance
8.5.1 Speed Characteristics
8.5.2 Load Characteristics
8.5.2.1 SI Engines
8.5.2.2 CI Engines
Problems
Part III. Gas Turbine Internal Combustion Engines. Introduction III: History and Classification of Gas Turbines
9 Air‐Standard Gas Turbine Cycles
9.1 Joule‐Brayton Ideal Cycle
9.2 Cycle with Heat Exchange (Regeneration)
9.3 Cycle with Reheat
9.4 Cycle with Intercooling
9.5 Cycle with Heat Exchange and Reheat
9.6 Cycle with Heat Exchange and Intercooling
9.7 Cycle with Heat Exchange, Reheat, and Intercooling
9.8 Cycle Comparison
Problems
10 Irreversible Air‐Standard Gas Turbine Cycles
10.1 Component Efficiencies. 10.1.1 Compressor Isentropic Efficiency
10.1.2 Turbine Isentropic Efficiency
10.1.3 Polytropic (Small‐Stage) Compressor Efficiency
10.1.4 Polytropic (Small‐Stage) Turbine Efficiency
10.2 Simple Irreversible Cycle
10.3 Irreversible Cycle with Heat Exchange (Regenerative Irreversible Cycle)
10.4 Irreversible Cycle with Reheat
10.5 Irreversible Cycle with Intercooling
10.6 Irreversible Cycle with Heat Exchange and Reheat
10.7 Irreversible Cycle with Heat Exchange and Intercooling
10.8 Irreversible Cycle with Heat Exchange, Reheat, and Intercooling
10.9 Comparison of Irreversible Cycles
Problems
11 Practical Gas Turbine Cycles
11.1 Simple Single‐Shaft Gas Turbine
11.2 Thermodynamic Properties of Air
11.3 Compression Process in the Compressor
11.3.1 Power to Drive the Compressor
11.4 Combustion Process
11.4.1 Combustion Chamber Design
11.4.2 Thermodynamic Properties of the Combustion Products
11.4.3 Combustion Temperature
11.4.3.1 Method 1
11.4.3.2 Method 2
11.4.3.3 Method 3
11.4.3.4 Method 4
11.4.4 Effect of Dissociation on the Combustion Temperature
11.5 Expansion Process in the Turbine
11.5.1 Total Turbine Power
11.5.2 Specific Fuel Consumption
11.5.3 Cycle Thermodynamic Efficiency
Problems
12 Design‐Point Calculations of Aviation Gas Turbines
12.1 Properties of Air
12.1.1 International Standard Atmosphere (ISA)
12.1.2 Stagnation Properties
12.2 Simple Turbojet Engine
12.2.1 Intake (Diffuser)
12.2.2 Compressor
12.2.3 Combustion Chamber
12.2.4 Turbine
12.2.5 Nozzle
12.2.5.1 Sonic Flow
12.2.5.2 Subsonic Flow
12.2.6 Engine Performance
12.3 Performance of Turbojet Engine – Case Study
12.3.1 Performance Maps
12.3.2 Effect of Flight Mach Number
12.3.3 Effect of Flight Altitude
12.4 Two‐Spool Unmixed‐Flow Turbofan Engine
12.4.1 Design‐Point Calculations of the Core Engine
12.4.1.1 Bypass Ratio
12.4.1.2 Intake
12.4.1.3 Fan
12.4.1.4 Compressor
12.4.1.5 Combustion Chamber
12.4.1.6 Compressor Turbine (High‐Pressure Turbine)
12.4.1.7 Low‐Pressure Turbine
12.4.1.8 Hot Nozzle
12.4.1.9 Sonic Flow in the Hot Nozzle (Nozzle Choked)
12.4.1.10 Subsonic Flow in the Hot Nozzle (Nozzle Unchoked)
12.4.2 Design‐Point Calculations of the Engine Bypass Section
12.4.2.1 Intake and Fan
12.4.2.2 Cold Nozzle
12.5 Performance of Two‐Spool Unmixed‐Flow Turbofan Engine – Case Study
12.6 Two‐Spool Mixed‐Flow Turbofan Engine
12.6.1 Design‐Point Calculations of Engine Core
12.6.1.1 Intake
12.6.1.2 Fan
12.6.1.3 Compressor
12.6.1.4 Combustion Chamber
12.6.1.5 Compressor Turbine (High‐Pressure Turbine)
12.6.1.6 Low‐Pressure Turbine
12.6.2 Design‐Point Calculations of Bypass Section
12.6.2.1 Intake
12.6.2.2 Fan
12.6.2.3 Bypass Duct (Cold Jet Tube)
12.6.3 Mixer. 12.6.3.1 Assumptions
12.6.3.2 Governing Equations
12.6.3.3 Computational Procedure
12.6.4 Propelling Nozzle
12.6.4.1 Sonic Flow in the Propelling Nozzle (Nozzle Choked)
12.6.4.2 Subsonic Flow in the Hot Nozzle (Nozzle Unchoked)
12.7 Performance of Two‐Spool Mixed‐Flow Turbofan Engine – Case Study
Problems
13 Design‐Point Calculations of Industrial Gas Turbines
13.1 Single‐Shaft Gas Turbine Engine
13.1.1 Design‐Point Calculations
13.1.1.1 Compressor
13.1.1.2 Combustion Chamber
13.1.1.3 Turbine
13.1.1.4 Specific Fuel Consumption
13.1.1.5 Cycle Thermodynamic Efficiency
13.2 Performance of Single‐Shaft Gas Turbine Engine – Case Study
13.2.1 In Terms of Relative Air‐Fuel Ratio λ
13.2.2 In Terms of Cycle Maximum Temperature T3
13.2.3 Comparison with Practical Cycles
13.3 Two‐Shaft Gas Turbine Engine
13.3.1 Design‐Point Calculations
13.3.1.1 Mechanical Efficiency of the Gas Generator
13.3.1.2 Temperature Equivalents of the Compressor Work
13.3.1.3 Pressure Losses
13.3.1.4 Temperature Drop in the Compressor Turbine
13.3.1.5 Temperature Equivalent of the Power‐Turbine Work
13.3.1.6 Specific Fuel Consumption
13.3.1.7 Cycle Thermal Efficiency
13.4 Performance of Two‐Shaft Gas Turbine Engine – Case Study
13.4.1 In Terms of Relative Air‐Fuel Ratio λ
13.4.2 In Terms of Cycle Maximum Temperature T3
Problems
14 Work‐Transfer System in Gas Turbines
14.1 Axial‐Flow Compressors
14.1.1 Input Power
14.1.2 Degree of Reaction D
14.1.3 Compressor Performance Characteristics
14.2 Radial‐Flow Compressors
14.2.1 Radial‐Flow Compressor Characteristics
14.3 Axial‐Flow Turbines
14.3.1 Velocity Diagrams
14.3.2 Stage Output Power
14.3.3 Multistage Turbine Output Power
14.3.4 Blade Profile
14.3.5 Degree of Reaction
14.3.5.1 Degree of Reaction in Terms of Fluid Velocities
14.3.5.2 Degree of Reaction in Terms of Blade Characteristics
14.3.6 Utilisation Factor (Diagram Efficiency)
14.3.7 Axial Turbine Coefficients
14.3.8 Axial‐Flow Turbine Performance Characteristics
14.4 Radial‐Flow Turbines
14.4.1 Turbine Design
14.4.2 Turbine Characteristics
Problems
15 Off‐Design Performance of Gas Turbines
15.1 Component‐Matching Method
15.1.1 Off‐Design Performance of Single‐Shaft Gas Turbine
15.1.1.1 Calculation Procedure
15.1.1.2 Propeller Load
15.1.1.3 Electric Generator
15.1.2 Off‐Design Performance of Two‐Shaft Gas Turbine (Free‐Turbine Engine)
15.1.2.1 Power Turbine Output
15.1.3 Off‐Design Performance of Turbojet Engine
15.1.3.1 Converging Nozzle
15.1.3.2 Intake Duct
15.1.3.3 Matching the Gas Generator and Nozzle
15.1.3.4 Thrust Calculation
15.2 Thermo‐Gas‐Dynamic Matching Method
15.2.1 Single‐Shaft Gas Turbine
15.2.1.1 Compressor
15.2.1.2 Combustion Chamber
15.2.1.3 Compressor Turbine
15.2.1.4 Flow Compatibility
15.2.1.5 Solution Procedure
15.2.1.6 Procedure
15.2.2 Two‐Shaft Gas Turbine
15.2.2.1 Gas Generator
15.2.2.2 Matching the Compressor and Compressor Turbine
15.2.2.3 Power Turbine
15.2.2.4 Matching Mass Flow of the Compressor Turbine and Power Turbine
15.2.2.5 Off‐Design Calculation Procedure
15.2.2.6 Off‐Design Prediction Results
15.2.3 Turbojet Engine
15.2.3.1 Compressor
15.2.3.2 Combustion Chamber
15.2.3.3 Compressor Turbine
15.2.3.4 Gas Generator
15.2.3.5 Matching the Compressor and Compressor Turbine
15.2.3.6 Matching Mass Flow of the Compressor Turbine and Nozzle
15.2.3.7 Off‐Design Calculation Procedure
15.2.3.8 Off‐Design Prediction Results
Problems
Bibliography
Appendix A Thermodynamic Tables
Appendix B Dynamics of the Reciprocating Mechanism
Appendix C Design Point Calculations – Reciprocating Engines
C.1. Engine Processes
C.1.1 Induction Process
C.1.2 Compression Process
C.1.3 Combustion Process
C.1.4 Expansion Process
C.1.5 Performance Parameters
Appendix D Equations for the Thermal Efficiency and Specific Work of Theoretical Gas Turbine Cycles
Nomenclature
Index
WILEY END USER LICENSE AGREEMENT
Отрывок из книги
Corrosion and Materials in Hydrocarbon Production: A Compendium of Operational and Engineering Aspects
Bijan Kermani, Don Harrop
.....
Determine the molar composition of the mixture.
If a gas mixture of two components A and B is at pressure p and temperature T in a container with volume V, each gas in the mixture exists separately and independently at the temperature and volume of the mixture, and their respective pressures are pA and pB. For the mixture
.....