The ESD Control Program Handbook
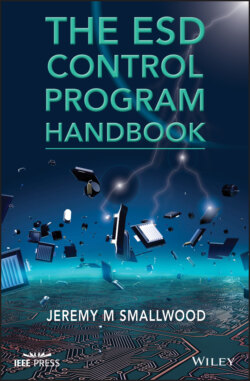
Реклама. ООО «ЛитРес», ИНН: 7719571260.
Оглавление
Jeremy M. Smallwood. The ESD Control Program Handbook
Table of Contents
List of Tables
List of Illustrations
Guide
Pages
The ESD Control Program Handbook
Copyright
Introduction
References
Further Reading
Foreword
Preface
Acknowledgments
1 Definitions and Terminology
1.1 Scientific Notation and SI Unit Prefixes
1.2 Charge, Electrostatic Fields, and Voltage. 1.2.1 Charge
1.2.2 Ions
1.2.3 Dissipation and Neutralization of Electrostatic Charge
1.2.4 Voltage (Potential)
1.2.5 Electric or Electrostatic Field
1.2.6 Gauss's Law
1.2.7 Electrostatic Attraction (ESA)
1.2.8 Permittivity
1.3 Electric Current
1.4 Electrostatic Discharge (ESD)
1.4.1 ESD Models
1.4.2 Electromagnetic Interference (EMI)
1.5 Earthing, Grounding, and Equipotential Bonding
1.6 Power and Energy
1.7 Resistance, Resistivity, and Conductivity
1.7.1 Resistance
1.7.2 Resistivity and Conductivity. 1.7.2.1 Surface Resistivity and Surface Resistance
1.7.2.2 Volume Resistance, Volume Resistivity, and Conductivity
1.7.3 Insulators, Conductors, Conductive, Dissipative, and Antistatic Materials
1.7.4 Point‐to‐Point Resistance
1.7.5 Resistance to Ground
1.7.6 Combination of Resistances
1.8 Capacitance
1.9 Shielding
1.10 Dielectric Breakdown Strength
1.11 Relative Humidity and Dew Point
References
2 The Principles of Static Electricity and Electrostatic Discharge (ESD) Control. 2.1 Overview
2.2 Contact Charge Generation (Triboelectrification)
2.2.1 The Polarity and Magnitude of Charging
2.3 Electrostatic Charge Build‐Up and Dissipation
2.3.1 A Simple Electrical Model of Electrostatic Charge Build‐Up
2.3.2 Capacitance Is Variable
2.3.3 Charge Decay Time
2.3.4 Conductors and Insulators Revisited
2.3.5 The Effect of Relative Humidity
2.4 Conductors in Electrostatic Fields. 2.4.1 Voltage on Conducting and Insulating Bodies and Surfaces
2.4.2 Electrostatic Field in Practical Situations
2.4.3 Faraday Cage
2.4.4 Induction: An Isolated Conductive Object Attains a Voltage When in an Electric Field
2.4.5 Induction Charging: An Object Can Become Charged by Grounding It
2.4.6 Faraday Pail and Shielding of Charges Within a Closed Object
2.5 Electrostatic Discharges
2.5.1 ESD (Sparks) Between Conducting Objects
2.5.2 ESD from Insulating Surfaces
2.5.3 Corona Discharge
2.5.4 Other Types of Discharge
2.6 Common Electrostatic Discharge Sources
2.6.1 ESD from the Human Body
2.6.2 ESD from Charged Conductive Objects
2.6.3 Charged Device ESD
2.6.4 ESD from a Charged Board
2.6.5 ESD from a Charged Module
2.6.6 ESD from Charged Cables
2.7 Electronic Models of ESD
2.8 Electrostatic Attraction (ESA)
2.8.1 ESA and Particle Contamination
2.8.2 Neutralization of Surface Voltages by Air Ions
2.8.3 Ionizers
2.8.4 Rate of Charge Neutralization
2.8.5 The Region of Effective Charge Neutralization Around an Ionizer
2.8.6 Ionizer Balance and Charging of a Surface by an Unbalanced Ionizer
2.9 Electromagnetic Interference (EMI)
2.10 How to Avoid ESD Damage of Components. 2.10.1 The Circumstances Leading to ESD Damage of a Component
2.10.2 Risk of ESD Damage
2.10.3 The Principles of ESD Control
References
Further Reading
3 Electrostatic Discharge–Sensitive (ESDS) Devices. 3.1 What Are ESDS Devices?
3.2 Measuring ESD Susceptibility. 3.2.1 Modeling Electrostatic Discharges
3.2.2 Standard ESD Susceptibility Tests
3.2.3 ESD Withstand Voltage
3.2.4 HBM Component Susceptibility Test
3.2.5 System Level Human Body ESD Susceptibility Test
3.2.6 MM Component Susceptibility Test
3.2.7 CDM Component Susceptibility Test
3.2.8 Comparison of Test Methods
3.2.9 Failure Criteria Used in ESD Susceptibility Tests
3.2.10 Transmission Line Pulse Techniques
3.2.11 The Relation Between ESD Withstand Voltage and ESD Damage
3.2.12 Trends in Component ESD Tests
3.3 ESD Susceptibility of Components. 3.3.1 Introduction
3.3.2 Latent Failures
3.3.3 Built‐in On‐chip ESD Protection and ESD Protection Targets
3.3.4 ESD Sensitivity of Typical Components
3.3.5 Discrete Devices
3.3.6 The Effect of Scaling
3.3.7 Package Effects
3.4 Some Common Types of ESD Damage. 3.4.1 Failure Mechanisms
3.4.2 Breakdown of Thin Dielectric Layers
3.4.3 MOSFETs
3.4.4 Susceptibility to Electrostatic Fields and Breakdown Between Closely Spaced Conductors
3.4.5 Semiconductor Junctions
3.4.6 Field Effect Structures and Nonconductive Device Lids
3.4.7 Piezoelectric Crystals
3.4.8 LEDs and Laser Diodes
3.4.9 Magnetoresistive Heads
3.4.10 MEMS
3.4.11 Burnout of Device Conductors or Resistors
3.4.12 Passive Components
3.4.13 Printed Circuit Boards and Assemblies
3.4.14 Modules and System Components
3.5 System‐Level ESD. 3.5.1 Introduction
3.5.2 The Relationship Between System Level Immunity and Component ESD Withstand
3.5.3 Charged Cable ESD (Cable Discharge Events)
3.5.4 System‐Efficient ESD Design (SEED)
References
Further Reading
4 The Seven Habits of a Highly Effective ESD Program. 4.1 Why Habits?
4.2 The Basis of ESD Protection
4.3 What Is an ESDS Device?
4.4 Habit 1: Always Handle ESDS Components Within an EPA. 4.4.1 What Is an EPA?
4.4.2 Defining the EPA Boundary
4.4.3 Marking the EPA Boundary
4.4.4 What Is an Insignificant Level of ESD Risk?
4.4.5 What Are the Sources of ESD Risk?
4.4.6 What ESD Protection Measures Are Needed in the EPA?
4.4.7 Who Will Decide What ESD Protection Measures Are Required?
4.5 Habit 2: Where Possible, Avoid Use of Insulators Near ESDS. 4.5.1 What Is an Insulator?
4.5.2 Essential and Nonessential Insulators
4.5.3 Remove Nonessential Insulators from the Vicinity of ESDS
4.6 Habit 3: Reduce ESD Risks from Essential Insulators. 4.6.1 What Is an Insulator?
4.6.2 Insulators Cannot Be Grounded
4.6.3 What to Do About ESD Risk from Essential Insulators
4.6.4 Using Ionizers to Reduce Charge Levels on Insulators
4.7 Habit 4: Ground Conductors, Especially People. 4.7.1 What Is a Conductor?
4.7.2 Conductive, Dissipative, or Insulative?
4.7.3 Properties of a Conductor
4.7.4 Charge and Voltage Decay Time
4.7.5 The Importance of Material Contact Resistance in Protecting ESDS. 4.7.5.1 Reduction of Energy Delivered from Conductor in ESD
4.7.5.2 Reduction of Peak Current in a Discharge
4.7.5.3 Specification of a Minimum Material Resistance
4.7.6 Safety Considerations
4.7.7 Elimination of ESD by Grounding and Equipotential Bonding
4.7.8 Understanding the Grounding (Earth) System. 4.7.8.1 Types of Ground
4.7.8.2 The Grounding System
4.7.9 Grounding Personnel Handling ESDS Devices. 4.7.9.1 Basic Requirements for Grounding Personnel Handling ESDS Devices
4.7.9.2 Grounding Personnel via a Wrist Strap
4.7.9.3 Grounding Personnel via Footwear and Flooring
4.7.9.4 Grounding Seated Personnel
4.7.10 Grounding ESD Control Equipment. 4.7.10.1 General Considerations
4.7.10.2 Work Surfaces
4.7.10.3 Floors
4.7.10.4 Carts, Racks, and Other Floor Standing Work Surfaces
4.7.10.5 Seats
4.7.10.6 Tools
4.7.10.7 Gloves and Finger Cots
4.7.10.8 ESD Control Garments
4.7.11 What If a Conductor Cannot Be Grounded?
4.8 Habit 5: Protect ESDS Using ESD Packaging. 4.8.1 Don't Take Ordinary Packaging Materials into an EPA
4.8.2 The Basic Functions of ESD Packaging
4.8.3 Open ESD Packaging Only Within an EPA
4.8.4 Don't Put Papers or Other Unsuitable Material in a Package with an ESDS Device
4.9 Habit 6: Train Personnel to Know How to Use ESD Control Equipment and Procedures. 4.9.1 Why Train People?
4.9.2 Who Needs ESD Training?
4.9.3 What Training Do They Need?
4.9.4 Refresher Training
4.10 Habit 7: Check and Test to Make Sure Everything Is Working. 4.10.1 Why Do We Need to Check and Test?
4.10.2 What Needs to Be Tested?
4.10.3 ESD Control Product Qualification
4.10.4 ESD Control Product or System Compliance Verification
4.10.5 Test Methods and Pass Criteria
4.10.6 How Often Should ESD Control Items Be Tested?
4.11 The Seven Habits and ESD Standards
4.12 Handling Very Sensitive Devices
4.13 Controlling Other ESD Sources
References
Further Reading
5 Automated Systems. 5.1 What Makes Automated Handling and Assembly Different?
5.2 Conductive, Static Dissipative, and Insulative Materials
5.3 Safety and AHE
5.4 Understanding the ESD Sources and Risks
5.5 A Strategy for ESD Control. 5.5.1 General Principles of ESD Control in AHE
5.5.2 The Conditions Leading to ESD Damage
5.5.3 Strategies for ESD Control in Automated Equipment
5.5.4 Qualification of ESD Control Measures
5.5.5 Compliance Verification of ESD Control Measures
5.5.6 ESD Training Implications
5.5.7 Modification of Existing AHE
5.6 Determination and Implementation of ESD Control Measures in AHE. 5.6.1 Define the Critical Path of ESDS
5.6.2 Examine the Critical Path and Identify ESD Risks
5.6.3 Determine Appropriate ESD Control Measures. 5.6.3.1 General Control Measures
5.6.4 Include ESD Control in New Equipment Specification
5.6.5 Document the ESD Control Measures Used in the Machine
5.6.6 Implement Maintenance and Compliance Verification of ESD Control Measures
5.7 Materials, Techniques, and Equipment Used for ESD Control in AHE. 5.7.1 Grounding All Conductors That Make Contact with ESDS
5.7.2 Isolated Conductors
5.7.3 Preventing Induced Voltages on ESDS Devices
5.7.4 Reducing Tribocharging of ESDS Devices
5.7.5 Using Resistive Contact Materials to Limit Charged Device ESD Current
5.7.6 Anodization
5.7.7 Bearings
5.7.8 Conveyor Belts
5.7.9 Using Ionizers to Reduce Charge Levels on ESDS Devices, Essential Insulators, and Isolated Conductors
5.7.10 Vacuum Pickers
5.8 ESD Protective Packaging
5.9 Measurements in AHE. 5.9.1 Overview of Measurements in AHE
5.9.2 Resistance Measurements. 5.9.2.1 Overview of Resistance Measurements in AHE
5.9.2.2 Resistance Meters
5.9.2.3 Point‐to‐Point Resistance of Surfaces
5.9.2.4 Resistance to Ground from Surfaces and Machine Parts
5.9.2.5 Resistance to Ground of a Potentially Isolated Conductor
5.9.2.6 Measurements on ESD Protective Packaging
5.9.3 Electrostatic Field and Voltage Measurements. 5.9.3.1 Voltage Measurement Instruments
5.9.3.2 Voltages on Small Conductors or ESDS Devices
5.9.3.3 Voltages on ESDS Devices
5.9.4 Charge Measurements
5.9.5 Measurement of the Voltage Decay Time and Offset Voltage Due to Neutralization by an Ionizer
5.9.6 ESD Current Measurements
5.9.7 Detection of ESD Using EMI Detectors
5.10 Handling Very Sensitive Components
References
Further Reading
6 ESD Control Standards. 6.1 Introduction
6.2 The Development of ESD Control Standards
6.3 Who Writes the Standards?
6.4 The IEC and ESDA Standards. 6.4.1 Standards Numbering
6.4.2 The Language of Standards
6.4.3 Definitions Used in Standards
6.5 Requirements of IEC 61340‐5‐1 and ANSI/ESD S20.20 Standards. 6.5.1 Background
6.5.2 Documentation and Planning
6.5.3 Technical Basis of the ESD Control Program
6.5.4 Personal Safety
6.5.5 ESD Coordinator
6.5.6 Tailoring the ESD Program
6.5.7 The ESD Control Program Plan
6.5.8 Training Plan
6.5.9 Product Qualification Plan
6.5.10 Compliance Verification Plan
6.5.11 Test Methods
6.5.12 ESD Control Program Plan Technical Requirements. 6.5.12.1 Safety
6.5.12.2 Grounding and Bonding Systems
6.5.12.3 Personnel Grounding
6.5.12.4 ESD‐Protected Areas (EPAs)
6.5.12.5 Equipment Used in the EPA
6.5.12.6 Insulators
6.5.12.7 Isolated Conductors
6.5.12.8 Hand Electrical Soldering and Desoldering Tools
6.5.13 ESD Packaging
6.5.14 Marking
References
Further Reading
7 Selection, Use, Care, and Maintenance of Equipment and Materials for ESD Control. 7.1 Introduction
7.1.1 Selection and Qualification of Equipment
7.1.2 Use
7.1.3 Cleaning, Care, and Maintenance of Equipment
7.1.4 Compliance Verification
7.2 ESD Control Earth (Ground) 7.2.1 What Does the ESD Control Earth Do?
7.2.2 Choosing an ESD Control Earth
7.2.3 Qualification of ESD Control Earth
7.2.4 Compliance Verification of ESD Control Earth
7.2.5 Common Problems with Ground Connections
7.3 The ESD Control Floor. 7.3.1 What Does an ESD Control Floor Do?
7.3.2 Permanent ESD Control Floor Material
7.3.3 Semipermanent or Nonpermanent ESD Control Floor Materials
7.3.4 Selection of Floor Materials
7.3.5 Floor Material Qualification Test
7.3.6 Acceptance of a Floor Installation
7.3.7 Use of Floor Materials
7.3.8 Care and Maintenance of Floors
7.3.9 Compliance Verification Test
7.3.10 Common Problems
7.4 Earth Bonding. 7.4.1 The Role of Earth Bonding Points
7.4.2 Selection of Earth Bonding Points
7.4.3 Qualification of Earth Bonding Points
7.4.4 Use of Earth Bonding Points
7.4.5 Compliance Verification of Earth Bonding Points
7.5 Personal Grounding. 7.5.1 What Is the Purpose of Personal Grounding?
7.5.2 Personal Grounding and Electrical Safety
7.5.3 Wrist Straps. 7.5.3.1 Conventional Wrist Strap Systems
7.5.3.2 Constant (Continuous) Monitor Wrist Strap Systems
7.5.3.3 Cordless Wrist Straps
7.5.3.4 Wrist Strap System Selection
7.5.3.5 Wrist Strap System Use
7.5.3.6 Wrist Strap Qualification
7.5.3.7 Wrist Strap Cleaning and Maintenance
7.5.3.8 Wrist Strap System Compliance Verification Test
7.5.3.9 Common Problems
7.5.4 Footwear and Flooring Grounding. 7.5.4.1 The Importance of Footwear and Flooring in ESD Control
7.5.4.2 Types of Footwear
7.5.4.3 Footwear and Safety
7.5.4.4 Selection of Footwear
7.5.4.5 Qualification of Footwear
7.5.4.6 Use of Footwear
7.5.4.7 Compliance Verification of Footwear
7.5.4.8 Common Problems
7.5.5 Grounding via ESD Control Seating
7.5.6 Personal Grounding via an ESD Garment
7.5.6.1 Qualification of a Groundable Static Control Garment
7.5.6.2 Compliance Verification of ESD Control Garments
7.6 Work Surfaces. 7.6.1 What Does a Work Surface Do?
7.6.2 Types of Work Surfaces
7.6.3 Selection of a Work Surface
7.6.4 Workstation Qualification Test
7.6.5 Acceptance of Work Surfaces
7.6.6 Cleaning and Maintenance of Work Surfaces
7.6.7 Compliance Verification Test of Work Surfaces
7.6.8 Common Problems
7.7 Storage Racks and Shelves. 7.7.1 Should It be an EPA Rack or Shelf?
7.7.2 Selection, Care, and Maintenance of Racks, and Shelves
7.7.3 Qualification Test of EPA Shelves and Racks
7.7.4 Acceptance of Shelves and Racks
7.7.5 Cleaning and Maintenance of Shelves and Racks
7.7.6 Compliance Verification Test of Shelves and Racks
7.7.7 Common Problems
7.8 Trolleys, Carts, and Mobile Equipment. 7.8.1 Types of Trolleys, Carts and Mobile Equipment
7.8.2 Selection, Care, and Maintenance of Trolleys, Carts, and Mobile Equipment
7.8.3 Qualification of Trolleys, Carts, and Mobile Equipment
7.8.4 Compliance Verification of Trolleys, Carts and Mobile Equipment
7.8.5 Common Problems
7.9 Seats. 7.9.1 What Is an ESD Control Seat for?
7.9.2 Types of ESD Seating
7.9.3 Selection of Seating
7.9.4 Qualification Test of Seating
7.9.5 Cleaning and Maintenance of Seating
7.9.6 Compliance Verification Test of Seating
7.9.7 Common Problems
7.9.8 Personal Grounding via ESD Control Seating
7.10 Ionizers. 7.10.1 What Does an Ionizer Do?
7.10.2 Ion Sources
7.10.3 Types of Ionizer System
7.10.4 Selection of Ionizers
7.10.5 Qualification Test of Ionizers
7.10.6 Cleaning and Maintenance of Ionizers
7.10.7 Compliance Verification Test of Ionizers
7.10.8 Common Problems
7.11 ESD Control Garments. 7.11.1 What Does an ESD Control Garment Do?
7.11.2 Types of ESD Control Garments
7.11.3 Selection of ESD Control Garments
7.11.4 Qualification Test of ESD Control Garments
7.11.5 Use of ESD Control Garments
7.11.6 Cleaning and Maintenance of ESD Control Garments
7.11.7 Compliance Verification of ESD Control Garments
7.11.8 Personal Grounding via an ESD Garment
7.12 Hand Tools. 7.12.1 Why Have ESD Hand Tools?
7.12.2 Types of Hand Tool
7.12.3 Qualification Test of Hand Tools
7.12.4 Use of Hand Tools
7.12.5 Compliance Verification Test of Hand Tools
7.12.6 Common Problems with ESD Control Hand Tools
7.13 Soldering or Desoldering Irons. 7.13.1 ESD Control Issues with Soldering or Desoldering Irons
7.13.2 Qualification of Soldering Irons
7.13.3 Compliance Verification of Soldering Irons
7.14 Gloves and Finger Cots. 7.14.1 Why Have Gloves and Finger Cots?
7.14.2 Types of Gloves and Finger Cots
7.14.3 Selection of Gloves or Finger Cots for ESD Control
7.14.4 Qualification Test of Gloves and Finger Cots
7.14.5 Cleaning and Maintenance of Gloves
7.14.6 Compliance Verification Test of Gloves and Finger Cots
7.14.7 Common Problems with Gloves and Finger Cots
7.15 Marking of ESD Control Equipment
References
Further Reading
8 ESD Control Packaging. 8.1 Why Is Packaging Important in ESD Control?
8.2 Packaging Functions
8.3 ESD Control Packaging Terminology
8.3.1 Terminology in General Usage
8.4 ESD Packaging Properties
8.4.1 Triboelectric Charging
8.4.2 Surface Resistance
8.4.3 Volume Resistance
8.4.4 Electrostatic Field Shielding
8.4.5 ESD Shielding
8.5 Use of ESD Protective Packaging. 8.5.1 The Importance of ESD Packaging Properties. 8.5.1.1 Charge Generation and Retention
8.5.1.2 Electrostatic Field Shielding
8.5.1.3 Electrostatic Discharge Shielding
8.5.2 Packaging Used Within the EPA
8.5.3 Packaging Used to Protect ESDS Outside the EPA
8.5.4 Packaging Used for Non‐ESD Susceptible Items
8.5.5 Avoiding Charged Cables and Modules
8.6 Materials and Processes Used in ESD Protective Packaging. 8.6.1 Introduction
8.6.2 Antistats, Pink Polythene, and Low‐Charging Materials
8.6.3 Static Dissipative and Conductive Polymers
8.6.4 Intrinsically Conductive or Dissipative Polymers
8.6.5 Metallized Film
8.6.6 Anodized Aluminum
8.6.7 Vacuum Forming of Filled Polymers
8.6.8 Injection Molding
8.6.9 Embossing
8.6.10 Vapor Deposition
8.6.11 Surface Coating
8.6.12 Lamination
8.7 Types and Forms of ESD Protective Packaging
8.7.1 Bags
8.7.1.1 Pink Polythene Bags
8.7.1.2 Conductive (Black Polythene) Bags
8.7.1.3 Metalized ESD Shielding Bags
8.7.1.4 Moisture Barrier Bags
8.7.2 Bubble Wrap
8.7.3 Foam
8.7.4 Boxes, Trays, and PCB Racks
8.7.5 Tape and Reel
8.7.6 Sticks (Tubes)
8.7.7 Self‐Adhesive Tapes and Labels
8.8 Packaging Standards. 8.8.1 ESD Control and Protection Packaging Standards
8.8.2 Moisture Barrier Packaging Standards. 8.8.2.1 Handling, Packing, Transport, and Use of Moisture‐Sensitive Devices
8.8.2.2 MIL‐PRF‐81705
8.8.2.3 ESD Association ANSI/ESD S11.4
8.8.3 ESD Control Packaging Measurements
8.9 How to Select an Appropriate Packaging System. 8.9.1 Introduction
8.9.2 Customer Requirements
8.9.3 What Is the Form of the ESDS Device?
8.9.4 ESD Threats and ESD Susceptibility
8.9.5 The Intended Packaging Tasks
8.9.6 Evaluate the Operational Environment for the Packaging
8.9.7 Selecting the ESD Packaging Type and ESD Protective Functions. 8.9.7.1 Intimate Packaging
8.9.7.2 Proximity Packaging
8.9.7.3 Packaging Systems
8.9.8 Testing the Packaging System
8.10 Marking of ESD Protective Packaging
References
Further Reading
9 How to Evaluate an ESD Control Program. 9.1 Introduction
9.2 Evaluation of ESD Risks. 9.2.1 Sources of ESD Risk
9.2.2 Evaluation of ESD Susceptibility of Components and Assemblies
9.3 Evaluating Process Capability Based on HBM, MM, and CDM Data
9.3.1 Process Capability Evaluation
9.3.1.1 A Structured Approach to Process Evaluation
9.3.1.2 Evaluate the Critical ESDS Path Through the Process
9.3.1.3 Use of ESD Withstand Data in Process Evaluation
9.3.2 Human Body ESD and Manual Handling Processes
9.3.3 ESD Risk Due to Isolated Conductors
9.3.3.1 What Is an Isolated Conductor?
9.3.3.2 How to Deal with Isolated Conductors
9.3.4 Charged Device ESD Risks
9.3.5 Damage to Voltage‐Sensitive Structures Such as a Capacitor or a MOSFET Gate
9.3.6 Evaluating ESD Risk from Electrostatic Fields
9.3.6.1 Risk to ESDS Devices Due to Electrostatic Fields
9.3.7 Troubleshooting
9.4 Evaluating ESD Protection Needs. 9.4.1 Standard ESD Control Precautions Do Not Necessarily Address all ESD Risks
9.4.2 Evaluating Return on Investment for ESD Protection Measures
9.4.3 What Is the Maximum Acceptable Resistance to Ground?
9.4.3.1 Charging Current in a Quasicontinuous Process
9.4.3.2 Maximum Decay Time
9.4.4 Should There Be a Minimum Resistance to Ground?
9.4.5 ESD from Charged Tools
9.4.6 Use of Gloves or Finger Cots
9.4.7 Charged Cable ESD
9.4.8 Charged Board ESD
9.4.9 Charged Module or Assembly ESD
9.5 Evaluation of Cost Effectiveness of the ESD Control Program. 9.5.1 The Cost of an Inadequate ESD Control Program
9.5.2 The Benefit Arising from of the ESD Control Program
9.5.3 Evaluation of the Cost of an ESD Control Program
9.5.4 ROI in ESD Control
9.5.5 Optimizing an ESD Control Program
9.6 Evaluation of Compliance of an ESD Control Program with a Standard. 9.6.1 Two Steps to Compliance Evaluation
9.6.2 Using Checklists to Evaluate Compliance of Documentation with a Standard
9.6.3 Evaluation of Compliance of a Facility with the ESD Control Program
9.6.4 Common Problems
References
10 How to Develop an ESD Control Program. 10.1 What Do We Need for a Successful ESD Control Program? 10.1.1 The ESD Control Strategy
10.1.2 How to Develop an ESD Control Program
10.1.3 Safety and ESD Control
10.2 The EPA. 10.2.1 Where Do I Need an EPA?
10.2.2 Boundaries and Signage
10.3 What Are the Sources of ESD Risk in the EPA?
10.4 How to Determine Appropriate ESD Measures. 10.4.1 ESD Control Principles
10.4.2 Select Convenient Ways of Working
10.5 Documentation of ESD Procedures. 10.5.1 What Should the Documentation Cover?
10.5.2 Writing an ESD Control Program Plan That Is Compliant with a Standard
10.5.3 Introduction Section
10.5.4 Scope
10.5.5 Terms and Definitions
10.5.6 Personal Safety
10.5.7 ESD Control Program. 10.5.7.1 ESD Coordinator
10.5.7.2 Tailoring ESD Control Requirements
10.5.8 ESD Control Program Plan
10.5.9 ESD Training Plan
10.5.10 ESD Control Product Qualification
10.5.11 Compliance Verification Plan
10.5.12 ESD Program Technical Requirements. 10.5.12.1 Documenting Technical Requirements
10.5.12.2 ESD Ground
10.5.12.3 Personal Grounding. 10 Personal Grounding Equipment
Occasional Verification of ESD Control Footwear Worn on ESD Control Flooring
Personal Grounding Testers
10.5.13 ESD Protected Areas. 10.5.13.1 Handling ESDS Devices and Access to the EPA
10.5.13.2 Insulators
10.5.13.3 Isolated Conductors
10.5.13.4 ESD Control Equipment. How to Specify ESD Control Equipment
Bench Mats and Other Surfaces on Which ESDS Devices Are Placed
ESD Control Flooring
Seating
Tools
Gloves and Finger Cots
Ionizers
ESD Control Garments (Coats)
10.5.14 ESD Protective Packaging
10.5.15 Marking of ESD‐Related Items
10.5.16 References
10.6 Evaluating ESD Protection Needs
10.7 Optimizing the ESD Control Program. 10.7.1 Costs and Benefits of ESD Control
10.7.2 Strategies for Optimization. 10.7.2.1 Minimization of the EPA
10.7.2.2 Choice of EPA Boundary
10.7.2.3 Minimizing Variation of the ESD Control Program
10.7.2.4 Standard or Tailored ESD Control
10.7.2.5 Design for Convenience
10.7.2.6 Who Audits the ESD Control Program?
10.8 Considerations for Specific Areas of the Facility. 10.8.1 The Varying ESD Control Requirements of Different Areas
10.8.2 Goods In and Stores
10.8.3 Kitting
10.8.4 Dispatch
10.8.5 Test
10.8.6 Research & Development
10.9 Update and Improvement
References
11 ESD Measurements. 11.1 Introduction
11.2 Standard Measurements
11.3 Product Qualification or Compliance Verification?
11.3.1 Measurement Methods for Product Qualification
11.3.1.1 Product Qualification of a Bench Mat
11.3.1.2 Example: Product Qualification of a Footwear and Floor Combination
11.3.2 Measurement Methods for Compliance Verification
11.3.2.1 Example: Compliance Verification Test of a Bench Mat
11.3.2.2 Example: Compliance Verification of Footwear and Flooring
11.4 Environmental Conditions
11.5 Summary of the Standard Test Methods and Their Applications
11.6 Measurement Equipment. 11.6.1 Choosing a Resistance Meter for High‐Resistance Measurements
11.6.2 Low‐Resistance Meter for Soldering Iron Grounding Test
11.6.3 Resistance Measurement Electrodes
11.6.4 Concentric Ring Electrodes for Packaging Surface and Volume Resistance Measurement
11.6.4.1 Conversion of Surface Resistance to Surface Resistivity for a Concentric Ring Electrode
11.6.4.2 Conversion of Volume Resistance to Volume Resistivity
11.6.5 Two‐Point Probe for Packaging Surface Resistance Measurements
11.6.6 Footwear Test Electrode
11.6.7 Handheld Electrode
11.6.8 Tool Test Electrode
11.6.9 Metal Plate Electrode for Volume Resistance Measurements
11.6.10 Insulating Supports
11.6.11 ESD Ground Connectors
11.6.12 Electrostatic Field Meters and Voltmeters
11.6.12.1 Electrostatic Field Meter–Based Instruments
11.6.12.2 Noncontact Electrostatic Voltmeters
11.6.12.3 Contact Electrostatic Voltmeters
11.6.13 Charge Plate Monitors (CPM)
11.7 Common Problems with Measurements. 11.7.1 Humidity
11.7.2 Accidental Measurement of Parallel Paths
11.8 Standard Measurements Specified by IEC 61340‐5‐1 and ANSI/ESD S20.20
11.8.1 Resistance to Ground
11.8.1.1 Resistance to Ground from a Work Surface or Floor
Common Problems
11.8.1.2 Compliance Verification of Seating in the EPA
11.8.1.3 Qualification of Seating
Common Problems
11.8.2 Point‐to‐Point Resistance
11.8.2.1 Point‐to‐Point Resistance of Work Surface
11.8.2.2 Point‐to‐Point Resistance Measurements on ESD Garments
11.8.2.3 Simple Point‐to‐Point Measurement on the Garment Fabric
Common Problems
Measurement from Garment Cuff to Cuff
Measurement of Sleeve‐to‐Sleeve Resistance of a Garment Using Hanging Clamps
Measurement of Resistance to Groundable Point of a Garment
11.8.3 Personal Grounding Equipment Tests. 11.8.3.1 End‐to‐End Resistance of a Ground Cord
Common Problems
11.8.3.2 Measurement of Wrist Straps and Cords as Worn
Common Problems
11.8.3.3 Measurement of Personnel Grounding Through Footwear to Foot Plate Electrode
Common Problems
11.8.3.4 Measurement of Resistance from Person to Ground
Common Problems
11.8.3.5 Resistance to Ground of an Earth Bonding Point
Common Problems
11.8.4 Surface Resistance of Packaging Materials
11.8.4.1 Surface Resistance of Packaging Measured Using a Concentric Ring Electrode
Common Problems
11.8.4.2 Point‐to‐Point Resistance of Small Packaging Items
Common Problems
11.8.4.3 Point‐to‐Point Resistance of Packaging Using 2.5 kg Resistance Measurement Electrodes
Common Problems
11.8.5 Volume Resistance of Packaging Materials
Common Problems
11.8.6 ESD Shielding of Bags
11.8.7 Evaluation of ESD Shielding of Packaging Systems
11.8.8 Measurement of Ionizer Decay Time and Offset Voltage
11.8.8.1 Common Problems
11.8.9 Walk Test of Footwear and Flooring
11.8.9.1 Common Problems
11.9 Useful Measurements Not Specified by IEC 61340‐5‐1 and ESD S20.20
11.9.1 Electrostatic Fields and Voltages
11.9.2 Measurement of Electric Fields at the Position of the ESDS
11.9.2.1 Common Problems
11.9.3 Measurement of Surface Voltages on Large Objects Using an Electrostatic Field Meter Calibrated as a Surface Voltmeter
Common Problems
11.9.4 Measurement of Voltage on Devices or Small Conductors
11.9.4.1 Measurement Using a Non‐contact Voltmeter
11.9.4.2 Measurement Using a Contact Voltmeter
11.9.5 Resistance of Tools. 11.9.5.1 Resistance from Tool Tip to Handle
Common Problems
11.9.5.2 Resistance to Ground of Handheld Tool
Common Problems
11.9.6 Resistance of Soldering Irons. 11.9.6.1 Resistance to Groundable Point of Soldering Iron Tip
Common Problems
11.9.6.2 Resistance to Ground of a Soldering Iron Tip
Common Problems
11.9.7 Resistance of Gloves or Finger Cots
11.9.7.1 Measurement of Resistance Through a Glove Using a Handheld Electrode
11.9.7.2 Testing Resistance Through a Glove Using a Wrist Strap Tester
Common Problems
11.9.7.3 Measurement of Resistance to Ground Through a Glove Using a Handheld Electrode
11.9.8 Charge Decay Measurements
11.9.8.1 CPM Charge Decay for Tools
Common Problems
11.9.8.2 Charge Decay of Gloves and Finger Cots
Common Problems
11.9.8.3 System Test of Glove and Handheld Tool
Common Problems
11.9.9 Faraday Pail Measurement of Charge on an Object
11.9.9.1 The Faraday Pail
11.9.9.2 Measurement of Electrostatic Charging of Items Handled with Gloves or Finger Cots Using a Faraday Pail
Common Problems
11.9.9.3 Evaluation of Charging of an Item Using a CPM Plate
Common Problems
11.9.10 ESD Event Detection
Common Problems
References
Further Reading
12 ESD Training. 12.1 Why Do We Need ESD Training?
12.2 Training Planning
12.3 Who Needs Training?
12.4 Training Form and Content. 12.4.1 Training Goals
12.4.2 Initial Training
12.4.3 Refresher Training
12.4.4 Training Methods
12.4.4.1 Video, Computer or Internet‐Based Training
12.4.4.2 Instructor‐Led Training
12.4.5 Supporting Information
12.4.6 Training Considerations
12.4.6.1 Preparing a Presentation
12.4.6.2 Presentation and Attendee Participation
12.4.6.3 Hands‐On Learning
12.4.6.4 Follow‐Up Assessment and Training
12.4.7 Public Tutorials and Courses
12.4.8 Qualifications and Certification
12.4.9 National and International ESD Groups and Electrostatics Interest Organizations
12.4.10 Conferences
12.4.11 Books, Articles, and Online Resources
12.5 Electrostatic and ESD Theory. 12.5.1 The Pros and Cons of Theory
12.5.2 A Technical and Nontechnical Explanation of Electrostatic Charging
12.6 Demonstrations of ESD Control–Related Issues. 12.6.1 The Role of Demonstrations
12.6.2 Demonstrating Real ESD Damage
12.6.3 The Cost of ESD Damage
12.7 Electrostatic Demonstrations. 12.7.1 The Value of Electrostatic Demonstrations
12.7.2 The Pros and Cons of Demonstrations
12.7.3 Useful Equipment for Demonstrations
12.7.4 Showing How Easy It is to Generate Electrostatic Charge
12.7.5 Understanding Electrostatic Fields
12.7.6 Understanding Charge and Voltage
12.7.7 Tribocharging
12.7.8 Production of ESD
12.7.9 Equipotential Bonding and Grounding
12.7.10 Induction Charging
12.7.11 ESD on Demand – The “Perpetual ESD Generator”
12.7.12 Body Voltage and Personal Grounding
12.7.13 Charge Generation and Electrostatic Field Shielding of Bags
12.7.14 Insulators Cannot Be Grounded
12.7.15 Neutralizing Charge – Charge Decay and Voltage Offset of Ionizers
12.8 Evaluation. 12.8.1 The Need for Evaluation
12.8.2 Practical Test
12.8.3 Written Tests
12.8.4 Pass Criteria
References
Further Reading
13 The Future. 13.1 General Trends
13.2 ESD Withstand Voltage Trends. 13.2.1 Integrated Circuit ESD Withstand Voltage Trends
13.2.2 Other Component ESD Withstand Voltage Trends
13.2.3 Availability of ESD Withstand Voltage Data
13.2.4 Device ESD Withstand Test
13.3 ESD Control Programs and Process Control. 13.3.1 ESD Control Program Development Strategies
13.3.2 A Basic ESD Control Program
13.3.3 Detailed ESD Control Program
13.3.4 Human Body ESD
13.3.5 ESD Between ESDS and Conductive Items
13.3.6 “Two‐Pin” ESD From Charged Ungrounded Conductive Items
13.3.7 “One‐Pin” ESD Between the ESDS and Another Conductive Part
13.3.8 Charged Board, Module, and Cable Discharge Events
13.3.9 Optimization
13.4 Standards
13.4.1 Impact on Future Standards
13.4.2 ESD Control in Automated Handling
13.5 ESD Control Equipment and Materials. 13.5.1 ESD Control Materials
13.5.2 ESD Protective Packaging
13.6 ESD‐Related Measurements. 13.6.1 ESD Protective Packaging Measurements
13.6.2 Voltage Measurement on ESDS Devices and Ungrounded Conductors
13.6.3 Measurements Related to ESD Risk in Automated Handling Equipment
13.7 System ESD Immunity
13.8 Education and Training
References
Further Reading
A Appendix A: An Example Draft ESD Control Program. A.1 About This Plan
A.2 Description of the Example Facility
A.3 Test and Qualification Procedures
A.4 ESD Control Program Plan at XXX Ltd. A.4.1 Introduction
A.4.2 Scope
A.4.3 Terms and Definitions
A.5 Personal Safety
A.6 ESD Control Program. A.6.1 ESD Control Program Requirements
A.6.2 ESD Coordinator
A.6.3 Tailoring ESD Control Requirements
A.7 ESD Control Program Technical Requirements. A.7.1 ESD Ground
A.7.2 Personal Grounding
A.7.3 ESD Protected Areas (EPA) A.7.3.1 General EPA Requirements
A.7.3.2 Insulators
Tailored Requirement for Essential Papers
Electrostatic Fields and Voltages
A.7.3.3 Isolated Conductors
A.7.3.4 ESD Control Equipment
A.7.4 ESD Protective Packaging
A.7.5 Marking of ESD‐Related Items. A.7.5.1 General
A.7.5.2 Marking of ESD Protective Packaging
A.7.5.3 Marking of ESD Control Equipment Used in EPAs
A.8 Compliance Verification Plan
A.9 ESD Training Plan. A.9.1 General Requirements of the ESD Training Plan
A.9.2 Training Records
A.9.3 Training Content and Frequency. A.9.3.1 ESD Awareness Training
A.9.3.2 ESD Audit and Measurements Training
A.9.3.3 EPA Cleaning Training
A.9.3.4 Principles and Practice of ESD Control Training
A.10 ESD Control Product Qualification
References
Index
WILEY END USER LICENSE AGREEMENT
Отрывок из книги
Jeremy M Smallwood
Electrostatic Solutions Ltd
.....
Table 1.2 shows how the terms insulating, dissipative, conductive, and antistatic are widely used in ESD control. Take care when using these terms, because they may be defined differently in different contexts and may mean different things to different people. When defined in the standards, the precise definition can change as the standards evolve into new editions.
The situation becomes worse if usage of these terms in other industries and for specific products is considered (Table 1.3). In general, these words should be considered unreliable in meaning unless specified by standards as part of an ESD control system.
.....