Ferroic Materials for Smart Systems
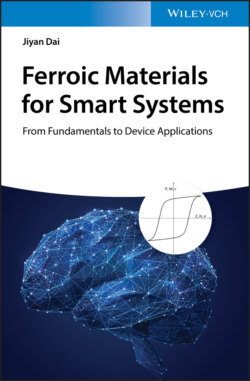
Реклама. ООО «ЛитРес», ИНН: 7719571260.
Оглавление
Jiyan Dai. Ferroic Materials for Smart Systems
Table of Contents
List of Tables
List of Illustrations
Guide
Pages
Ferroic Materials for Smart Systems. From Fundamentals to Device Applications
Copyright
1 General Introduction: Smart Materials, Sensors, and Actuators
1.1 Smart System
1.2 Device Application of Ferroelectric Materials
1.2.1 Piezoelectric Device Applications
1.2.2 Infrared Sensor
1.2.3 Ferroelectric RAM (FeRAM)
1.3 Device Application of Ferromagnetic Materials
1.3.1 Spin‐Transfer Torque Memory
1.3.2 Magnetic Field Sensor Based on Multiferroic Device
1.4 Ferroelastic Material and Device Application
1.5 Scope of This Book
References
2 Introduction to Ferroelectrics. 2.1 What Is Ferroelectrics?
2.1.1 P–E Loop
2.1.2 Relationships Between Dielectric, Piezoelectric, Pyroelectric, and Ferroelectric. 2.1.2.1 Ferroelectric–Dielectric
2.1.2.2 Ferroelectric–Piezoelectric
2.1.2.3 Ferroelectric–Pyroelectric
2.2 Origin of Ferroelectrics. 2.2.1 Structure‐Induced Phase Change from Paraelectric to Ferroelectric
2.2.2 Soft Phonon Mode
2.3 Theory of Ferroelectric Phase Transition. 2.3.1 Landau Free Energy and Curie–Weiss Law
2.3.2 Landau Theory of First‐Order Phase Transition
2.3.3 Landau Theory of a Second‐Order Phase Transition
2.4 Ferroelectric Domains and Domain Switching. 2.4.1 Domain Structure
2.4.2 Ferroelectric Switching
2.5 Ferroelectric Materials
2.5.1 From BaTiO3 to SrTiO3
2.5.2 From PbTiO3 to PbZrO3
2.5.3 Antiferroelectric PbZrO3
2.5.3.1 Pb(Zrx Ti1−x)O3 (PZT)
2.5.4 Relaxor Ferroelectrics
2.5.4.1 Relaxor Ferroelectrics: PMN‐xPT Single Crystal
2.5.4.2 Polar Nano Regions
2.5.4.3 Morphotropic Phase Boundary (MPB) of PMN‐PT Crystal
2.6 Ferroelectric Domain and Phase Field Calculation
References
3 Device Applications of Ferroelectrics
3.1 Ferroelectric Random‐Access Memory
3.2 Ferroelectric Tunneling Non‐volatile Memory
3.2.1 Tunneling Models
3.2.2 Metal–Ferroelectric–Semiconductor Tunnel Junction
3.2.3 Ferroelectric Tunneling Memristor
3.2.4 Strain Modulation to Ferroelectric Memory
3.3 Pyroelectric Effect and Infrared Sensor Application. 3.3.1 Pyroelectric Coefficient
3.3.2 Pyroelectric Infrared Sensor
3.3.3 Pyroelectric Figures of Merit
3.4 Application in Microwave Device
3.5 Ferroelectric Photovoltaics
3.6 Electrocaloric Effect
References
4. Ferroelectric Characterizations
4.1 P–E Loop Measurement
4.2 Temperature‐Dependent Dielectric Permittivity Measurement
4.3 Piezoresponse Force Microscopy (PFM)
4.3.1 Imaging Mechanism of PFM
4.3.2 Out‐of‐plane Polarization (OPP) and In‐plane Polarization (IPP) PFM
4.3.2.1 Electrostatic Force in PFM
4.3.2.2 Perspectives of PFM Technique
4.4 Structural Characterization
4.5 Domain Imaging and Polarization Mapping by Transmission Electron Microscopy
4.5.1 Selected Area Electron Diffraction (SAED)
4.5.2 Convergent Beam Electron Diffraction (CBED) for Tetragonality Measurement
References
5 Recent Advances in Ferroelectric Research
5.1 Size Limit of Ferroelectricity
5.2 Ferroelectricity in Emerging 2D Materials
5.3 Ferroelectric Vortex
5.4 Molecular Ferroelectrics
5.5 Ferroelectricity in HfO2 and ZrO2 Fluorite Oxide Thin Films
5.6 Ferroic Properties in Hybrid Perovskites
References
6 Piezoelectric Effect: Basic Theory. 6.1 General Introduction to Piezoelectric Effect
6.2 Piezoelectric Constant Measurement
6.2.1 Piezoelectric Charge Constant
6.2.2 Piezoelectric Voltage Constant
6.2.3 Dielectric Permittivity
6.2.4 Young's Modulus (Elastic Stiffness)
6.2.5 Elastic Compliance
6.2.6 Electromechanical Coupling Factor
6.2.6.1 How to Measure Electromechanical Coupling Factor?
Under Static or Low Frequency
High‐Frequency Resonance Measurement
6.3 Equivalent Circuit
6.4 Characterization of Piezoelectric Resonator Based on a Resonance Technique
6.4.1 Length Extensional Mode of a Rod
6.4.2 Extensional Vibration Mode of a Long Plate
6.4.3 Thickness Shear Mode of a Thin Plate
6.4.4 Thickness Mode of a Thin Disc/Plate
6.4.5 Radial Mode in a Thin Disc
6.4.6 Mechanical Quality Factor
References
7 Piezoelectric Devices
7.1 Piezoelectric Ultrasonic Transducers
7.1.1 Structure of Ultrasonic Transducers
7.1.2 Theoretical Models of Ultrasonic Transducer (KLM Model)
7.1.3 Characterization of Ultrasonic Transducers
7.1.3.1 Bandwidth (BW)
7.1.3.2 Sensitivity of the Transducer
7.1.3.3 Resolution
7.1.4 Types of Ultrasonic Transducers. 7.1.4.1 Medical Application
7.1.5 Piezoelectric Film Application in Ultrasound Transducers
7.1.6 Challenges and Trend of Developing New Advanced Ultrasound Transducers
7.2 Ultrasonic Motor
7.2.1 Terminologies
7.2.2 Design of USM
7.3 Surface Acoustics Wave Devices
7.3.1 Interdigital Electrode in SAW Device
7.3.2 Acoustic Wave
7.3.3 Piezoelectric Property Considerations for SAW Devices
7.3.4 Characterization of SAW Devices
7.3.5 Lead‐Free Piezoelectric Materials
References
8 Ferromagnetics: From Material to Device
8.1 General Introduction to Ferromagnetics
8.2 Ferromagnetic Phase Transition: Landau Free‐Energy Theory
8.3 Domain and Domain Wall
8.4 Magnetoresistance Effect and Device
8.4.1 Anisotropic Magnetoresistance (AMR)
8.4.2 Giant Magnetoresistance (GMR)
8.4.3 Colossal Magnetoresistance (CMR)
8.4.4 Tunneling Magnetoresistance (TMR)
8.4.4.1 Spin‐Transfer Torque Random‐Access Memory (STT‐RAM)
8.5 Magnetostrictive Effect and Device Applications
8.5.1 Magnetostrictive Properties of Terfenol‐D
8.5.2 Magnetostrictive Ultrasonic Transducer
8.5.3 Magnetoelastic Effect
8.5.3.1 Magnetomechanical Strain Gauge
8.6 Characterizations of Ferromagnetism
8.6.1 Vibrating Sample Magnetometer (VSM)
8.6.2 Superconducting Quantum Interference Device (SQUID)
8.6.3 Magnetic Force Microscopy (MFM)
8.6.4 Magneto‐Optical Kerr Effect (MOKE)
8.7 Hall Effect. 8.7.1 Ordinary Hall Effect
8.7.2 Anomalous Hall Effect
8.7.3 Spin Hall Effect
References
9 Multiferroics: Single Phase and Composites. 9.1 Introduction on Multiferroic
9.2 Magnetoelectric Effect
9.3 Why Are There so Few Magnetic Ferroelectrics?
9.4 Single Phase Multiferroic Materials
9.4.1 Switching Mechanism in BFO Films
9.5 ME Composite Materials
9.6 Modeling the Interfacial Coupling in Multilayered ME Thin Film
9.6.1 PZT/CFO Multilayered Heterostructures
9.6.2 Ferroelectric Properties of PZT/CFO Multilayers
References
10 Device Application of Multiferroics
10.1 ME Composite Devices
10.1.1 Effect of Preload Stress
10.2 Memory Devices Based on Multiferroic Thin Films
10.3 Memory Devices Based on Multiferroic Tunneling
References
11 Ferroelasticity and Shape Memory Alloy
11.1 Shape Memory Alloy
11.1.1 SMA Phase Change Mechanism
11.1.2 Nonlinearity in SMA
11.1.3 One‐Way and Two‐Way Shape Memory Effect
11.1.4 Superelastic Effect (SE)
11.1.5 Application Examples of SMAs
11.2 Ferromagnetic Shape Memory Alloys
11.2.1 Formation of Twin Variants
11.2.2 Challenges for Ni–Mn–Ga SMA
11.2.3 Device Application of MSMA
References
Index
WILEY END USER LICENSE AGREEMENT
Отрывок из книги
Jiyan Dai
Figure 1.1 AI beats human chess player.
.....
A very new application example is piezoelectric‐based fingerprint ID system in mobile phone. The currently used finger identification system is based on capacitance measurement to obtain two‐dimensional (2D) information of fingerprint, but it faces the problem of difficulty to identify the fingerprint when the finger is dirty or wet. Ultrasound fingerprint identification system based on piezoelectric ultrasonic transducer and imaging system can obtain a three‐dimensional image of fingerprint with a certain depth. This can overcome the problems of the current fingerprint identification system in most mobile phones. InvenSense, Inc. is one of the main suppliers of this solution, and Figure 1.8 is an illustration of the ultrasonic fingerprint system.
Figure 1.8 Illustration of concept of a ultrasonic transducer‐based fingerprint ID system based on complementary metal‐oxide‐semiconductor micro‐electro‐mechanical systems (CMOS‐MEMS) technology.
.....