Photovoltaic Module Reliability
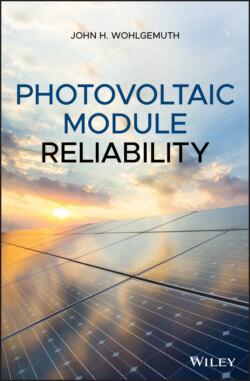
Реклама. ООО «ЛитРес», ИНН: 7719571260.
Оглавление
John H. Wohlgemuth. Photovoltaic Module Reliability
Table of Contents
List of Tables
List of Illustrations
Guide
Pages
Photovoltaic Module Reliability
Acknowledgments
1 Introduction
1.1 Brief History of PVs
1.2 Types of PV Cells
1.3 Module Packaging – Purpose and Types
1.4 What Does Reliability Mean for PV Modules?
1.5 Preview of the Book
References
2 Module Failure Modes
2.1 Broken Interconnects
2.2 Broken/Cracked Cells and Snail Trails
2.3 Delamination
2.4 Corrosion of Cell Metallization
2.5 Encapsulant Discoloration
2.6 Failure of Electrical Bonds Particularly Solder Bonds
2.7 Glass Breakage
2.8 Junction Box Problems
2.9 Loss of Elastomeric Properties of Back Sheets
2.10 Reverse Bias Hot Spots
2.11 By‐Pass Diodes
2.12 Structural Failures
2.13 Ground Faults and Open Circuits Leading to Arcing
2.14 Potential Induced Degradation
2.15 Thin‐Film Specific Defects
2.15.1 Light‐Induced Degradation
2.15.2 Inadequate Edge Deletion
2.15.3 Shunts at Laser Scribes and Impurities in Thin Film
2.15.4 Failure of Edge Seals
References
3 Development of Accelerated Stress Tests
3.1 Thermal Cycling or Change in Temperature
3.2 Damp Heat
3.3 Humidity Freeze
3.4 Ultraviolet (UV) Light Exposure
3.5 Static Mechanical Load
3.6 Cyclic (Dynamic) Mechanical Load
3.7 Reverse Bias Hot Spot Test
3.8 Bypass Diode Thermal Test
3.9 Hail Test
References
4 Qualification Testing
4.1 JPL Block Buy Program
4.2 Evolution of IEC 61215 Qualification Test Sequence
4.3 IEC 61215 Test Protocol
4.3.1 MQT 01 – Visual Inspection
4.3.2 MQT 02 – Maximum Power Determination
4.3.3 MQT 03 – Insulation Test
4.3.4 MQT 04 – Measurement of Temperature Coefficients
4.3.5 MQT 05 – Measurement of NMOT
4.3.6 MQT 06 – Performance at STC and NMOT
4.3.7 MQT 07 – Performance at Low Irradiance
4.3.8 MQT 08 – Outdoor Exposure Test
4.3.9 MQT 09 – Hot Spot Endurance Test
4.3.10 MQT 10 – UV Preconditioning Test
4.3.11 MQT 11 – Thermal Cycling Test
4.3.12 MQT 12 – Humidity‐Freeze Test
4.3.13 MQT 13 – Damp‐Heat Test
4.3.14 MQT 14 – Robustness of Termination
4.3.15 MQT 15 – Wet Leakage Current Test
4.3.16 MQT 16 – Static Mechanical Load Test
4.3.17 MQT 17 – Hail Test
4.3.18 MQT 18 – Bypass Diode Test
4.3.19 MQT 19 – Stabilization
4.4 How Qualification Tests have been Critical to Improving the Reliability and Durability of PV Modules
4.5 Limitations of the Qualification Tests
4.6 PV Module Safety Certification
4.6.1 Construction Requirements: IEC 61730‐1
4.6.1.1 Components
4.6.1.2 Mechanical and Electromechanical Connections
4.6.1.3 Materials
4.6.1.3.1 Polymeric Materials
4.6.1.3.2 Metallic Materials
4.6.1.4 Protection Against Electric Shock
4.6.2 Requirements of Testing IEC 61730‐2
4.6.2.1 MST 01 – Visual Inspection
4.6.2.2 MST 02 – Performance at STC
4.6.2.3 MST 03 – Maximum Power Determination
4.6.2.4 MST 04 – Insulation Thickness Test
4.6.2.5 MST 05 – Durability of Markings Test
4.6.2.6 MST 06 – Sharp Edge Test
4.6.2.7 MST 07 – Bypass Diode Functionality Test
4.6.2.8 MST 11 – Accessibility Test
4.6.2.9 MST 12 – Cut Susceptibility Test
4.6.2.10 MST 13 – Continuity Test of Equipotential Bonding
4.6.2.11 MST 14 – Impulse Voltage Test
4.6.2.12 MST 16 – Insulation Test
4.6.2.13 MST 17 – Wet Leakage Current Test
4.6.2.14 MST 21 – Temperature Test
4.6.2.15 MST 22 – Hot Spot Endurance Test
4.6.2.16 MST 24 – Ignitability Test
4.6.2.17 MST 25 – Bypass Diode Thermal Test
4.6.2.18 MST 26 – Reverse Current Overload Test
4.6.2.19 MST 32 – Mechanical Breakage Test
4.6.2.20 MST 33 – Screw Connections Test – Test for General Screw Connections MST 33a
4.6.2.21 MST 33 – Screw Connections Test – Test for Locking Screws MST 33b
4.6.2.22 MST 34 – Static Mechanical Load Test
4.6.2.23 MST 35 – Peel Test
4.6.2.24 MST 36 – Lap Shear Strength Test
4.6.2.25 MST 37 – Materials Creep Test
4.6.2.26 MST 42 – Robustness of Termination Test
4.6.2.27 MST 51 – Thermal Cycling Test
4.6.2.28 MST 52 – Humidity Freeze Test
4.6.2.29 MST 53 – Damp Heat Test
4.6.2.30 MST 54 – UV Test
4.6.2.31 MST 55 – Cold Conditioning
4.6.2.32 MST 56 – Dry Heat Conditioning
4.6.2.33 Recommendations for Testing of PV Modules from Production
References
5 Failure Analysis Tools
5.1 PV Performance – Analysis of Light I–V Curves
5.2 Performance as a Function of Irradiance
5.3 Dark I–V Curves
5.4 Visual Inspection
5.5 Infrared (IR) Inspection
5.6 Electroluminescence (EL)
5.7 Adhesion of Layers, Boxes, Frames, etc
References
6 Using Quality Management Systems to Manufacture PV Modules
6.1 Quality Management Systems
6.2 Using ISO 9000 and IEC 61215
6.3 Why just Using IEC 61215 and ISO 9000 is No Longer Considered Adequate?
6.4 Customer Defined “Do It Yourself” Quality Management and Qualification Systems (IEC 61215 on Steroids)
6.5 Problems with the “Do It Yourself” System
References
7 The PVQAT Effort
7.1 Task Group 1: PV QA Guidelines for Module Manufacturing
7.2 Task Group 2: Testing for Thermal and Mechanical Fatigue
7.3 Task Group 3: Testing for Humidity, Temperature and Voltage
7.3.1 Corrosion
7.3.2 Delamination
7.3.3 PID
7.3.4 Delamination Due to Voltage Stress
7.4 Task Group 4: Testing for Diodes, Shading and Reverse Bias
7.5 Task Group 5: Testing for UV, Temperature and Humidity
7.6 Task Group 6: Communications of Rating Information
7.7 Task Group 7: Testing for Snow and Wind Load
7.8 Task Group 8: Testing for Thin‐Film Modules
7.9 Task Group 9: Testing for Concentrator Photovoltaic (CPV)
7.10 Task Group 10: Testing for Connectors
7.11 Task Group 11: QA for PV Systems
7.12 Task Group 12: Soiling and Dust
7.13 Task Group 13: Cells
References
8 Conformity Assessment and IECRE
8.1 Module Conformity Assessment – PowerMark, IECQ, PVGAP, and IECEE
8.1.1 PV‐1: “Criteria for a Model Quality System for Laboratories Engaged in Testing PV Modules”
8.1.2 PV‐2: Model for a Third‐Party Certification and Labeling Program for PV Modules
8.1.3 PV‐3: Testing Requirements for a Certification and Labeling Program for PV Modules
8.1.4 PV‐4: Operational Procedures Manual for the Certification Body of the PV Module Certification Program
8.1.5 PV‐5: Application and Certification Procedures for the PV Module Certification Program
8.2 IECRE – Conformity Assessment for PV Systems
References
9 Predicting PV Module Service Life
9.1 Determining Acceleration Factors
9.1.1 Thermal Cycling
9.1.2 Discoloration of the Encapsulant
9.1.3 PET Hydrolysis
9.2 Impact of Design and Manufacturing on Failure or Degradation Rates for PV Modules
9.3 Impact of Location and Type of Mounting on Failure or Degradation Rates for PV Modules
9.4 Extended Stress Testing of PV Modules
9.5 Setting Up a True Service Life Prediction Program
References
10 What does the Future Hold for PV and a Brief Summary
10.1 Current Work on Updating Standards
10.1.1 Second Edition of IEC 61215 Series
10.1.2 Amendment 1 to Second Edition of IEC 61730‐1 and IEC 61730‐1
10.1.3 IEC TS 63126 – Guidelines for Qualifying PV Modules, Components and Materials for Operation at High Temperatures
10.2 Looking to the Future
10.2.1 Degradation Rates
10.2.2 Module Lifetime
10.3 Brief Summary
10.3.1 Personal Reflections
References
Index. a
b
c
d
e
f
g
h
i
j
k
l
m
n
o
p
q
r
s
t
u
v
w
x
y
z
WILEY END USER LICENSE AGREEMENT
Отрывок из книги
John H. Wohlgemuth
.....
Thin film cells are deposited onto a foreign substrate. These substrates can be glass where the cells are deposited right side up or upside down depending on the technology of the particular thin film material being used. Figures 1.4a and 1.4b show the cross section of these two types of module constructions. In Figure 1.4a, the thin film is deposited on the backside of the front glass. This is typical of how CdTe and a‐Si modules are fabricated. Figure 1.4a has been drawn with edge seals as this is typically how CdTe modules are fabricated today. The edge seals are designed to keep moisture from reaching the active cell area for the lifetime of the product (typically warrantied by the manufacturer for 25 years). In Figure 1.4b, the thin film is deposited on the front side of the back glass. This is typical of how CIS and CIGS modules are fabricated. Figure 1.4b has also been drawn with edge seals, but edge seals are not as prevalent in these types of modules. In this case, the superstrate can also be made of glass though other materials are often used.
Figure 1.3a Cross‐sectional drawing of glass/encapsulant/cry‐Si cells/encapsulant/backsheet module.
.....