The Nature of the Page
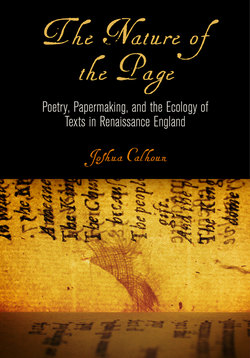
Реклама. ООО «ЛитРес», ИНН: 7719571260.
Оглавление
Joshua Calhoun. The Nature of the Page
Отрывок из книги
THE NATURE OF THE PAGE
Series Editors
.....
In the preface to Papermaking by Hand, Hamady recounts that “a scholar who had written a book on papermaking came to visit one time and when he saw the actual formation of the sheet, loudly exclaimed ‘so that’s how it’s done!’”43 I sympathize with the scholar in Hamady’s anecdote; I only began to appreciate the crucial role of cellulose in the papermaking process while standing in the snow in Portage, Wisconsin, about eleven miles as the crow flies from where Aldo Leopold found the driftwood discussed in the Introduction. I was using a canoe paddle to stir a cauldron in which Robert Possehl was boiling down a herbaceous plant known locally as Lady’s Mantle—identified in Renaissance herbals by the same name or, alternately, “great Sanicle” or “Lyons Foot.”44 We were cooking plants, not retting rags, but our object was the same. “Cellulose is what paper is made from,” Possehl said, and the process of cooking is one way to reduce the plant to pure cellulose. I relate this story, anecdotal as it is, in an attempt to properly cite the sources from which I have borrowed insights. This is a book that could not have been written well by relying solely on other books; rather, it relies on the generosity and insight of scholars and artisans, many of whom, like Possehl, have not published the unique insights they have gained from decades of research and experimentation. Working, however, with someone who excels at making paper directly from plants, I began to understand how the need for more “cheap and reliable” sources of cellulose affected the history of the book in the first place.
Cheap cellulose would be cellulose that is both abundant and easily extractable. All plants contain cellulose, but in varying amounts. For instance, cellulose makes up “about 90 percent of cotton and about 50 percent of wood.”45 Fiber length matters, too. Flax has about 10 percent less cellulose than cotton, but “its fiber was longer and stronger, and its fiber wall was straighter and thicker.”46 In rag form, plant fibers came to papermakers pre-processed: the labor required to convert the plants into textiles had already been done. The labor of further breaking down the fibers through use (as clothing or ship sails, for example) processed the plant fibers even more. So no matter what the plant fiber, much less labor was required to pulp and make paper from linen rags or ship sails than directly from flax and hemp plants. We might visualize the rag shortage crisis as a triangle where the simplest solution would be to cut out the textile phase and make paper directly from plants (see Figure 4). Thus we see so many lists of experimental plants in the history of paper, and so many years passing without a viable paper product. Then Matthias Koops, an immigrant to England at the end of the eighteenth century, claimed the problem of scarce, expensive, imported rags could be solved with a readily available, cheap, local raw material: oat and wheat straw.
.....