Amorphous Nanomaterials
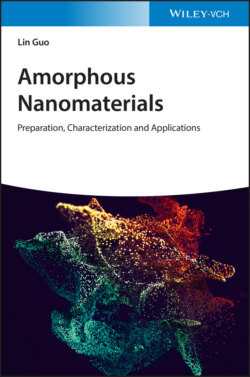
Реклама. ООО «ЛитРес», ИНН: 7719571260.
Оглавление
Lin Guo. Amorphous Nanomaterials
Table of Contents
List of Tables
List of Illustrations
Guide
Pages
Amorphous Nanomaterials
Foreword
Preface
1 Introduction. 1.1 Introduction of Amorphous Materials
1.2 Structural Differences between Amorphous Materials and Crystals
1.2.1 Crystals and Quasicrystals
1.2.2 Amorphous Materials
1.3 History of Amorphous Materials
1.3.1 Establishment of Crystallography
1.3.2 Enlightenment of Amorphous Materials
1.3.3 Modern Amorphous Materials 1-Disordered Elementary Substance
1.3.4 Modern Amorphous Materials 2-Metallic Glass
1.3.5 Modern Amorphous Materials 3-Nontraditional Amorphous Nanomaterials
1.4 Growth Mechanisms of Amorphous Nanomaterials. 1.4.1 Classical Nucleation Theory
1.4.2 Multistep Transformation Mechanism with Amorphous Participation
1.4.3 Complex Growth Process in Solution
1.5 Summary and Outlook
References
2 Local Structure and Electronic State of Amorphous Nanomaterials. 2.1 Spherical Aberration-Corrected Transmission Electron Microscopy. 2.1.1 Introduction
2.1.2 Spherical Aberration-Corrected Transmission Electron Microscopy
2.1.3 Electron Energy Loss Spectroscopy in TEM
2.1.4 Applications in Amorphous Nanomaterial Characterization
2.1.5 Summary and Outlook
2.2 X-ray Absorption Fine Structure Spectrum. 2.2.1 Introduction
2.2.2 Extended X-ray Absorption Fine Structure
2.2.3 X-ray Absorption Near-Edge Structure
2.2.4 Application in Amorphous Nanomaterial Characterization
2.2.5 Summary and Outlook
References
3 Defect Characterization of Amorphous Nanomaterials. 3.1 Introduction
3.2 Positron Annihilation Spectrum
3.3 Electron Paramagnetic Resonance
3.4 Photoluminescence Spectroscopy
3.5 Summary and Outlook
References
4 Synthesis of 0D Amorphous Nanomaterials. 4.1 Introduction
4.2 Bottom-Up Method. 4.2.1 Solution-Based Chemical Method
4.2.2 Thermal Treatment Method
4.2.3 Other Methods
4.3 Top-Down Method
4.4 Summary and Outlook
References
5 Synthesis of 1D Amorphous Nanomaterials. 5.1 Introduction
5.2 Hydrothermal/Solvothermal Method
5.3 Chemical Precipitation Method
5.4 Electrochemical Deposition Method
5.5 Templating Method
5.6 Other Synthetic Methods
5.7 Summary and Outlook
References
6 Synthesis of 2D Amorphous Nanomaterials. 6.1 Introduction
6.2 Thermal Decomposition Method
6.3 Exfoliation Method
6.4 Deposition Method. 6.4.1 Physical Vapor Deposition Method
6.4.2 Electrodeposition Method
6.5 Chemical Precipitation Method
6.6 Templating Method
6.7 Phase Transformation Method
6.8 Sol–Gel Method
6.9 Element Doping Method
6.10 Summary and Outlook
References
7 Synthesis of 3D Amorphous Nanomaterials. 7.1 Introduction
7.2 Template-Engaged Strategies
7.2.1 Coordinating Etching Method
7.2.2 Acid/Alkali Etching Method
7.2.3 Redox Etching Method
7.2.4 Self-Templated Method
7.3 Electrochemical Method
7.4 Hydrothermal/Solvothermal Method
7.5 Common Solution Method
7.6 Laser/Ultrasonic-Assisted Solution Method
7.7 Other Synthetic Methods
7.8 Summary and Outlook
References
8 Synthesis of Amorphous-Coated and Amorphous-Doped Nanomaterials. 8.1 Introduction
8.2 Amorphous Coated Nanomaterials by ALD
8.2.1 Amorphous Metal Oxide Coating
8.2.2 Amorphous Metal Fluoride Coating
8.3 Amorphous-Coated Nanomaterials With Different Dimensions
8.3.1 1D Amorphous-Coated Nanomaterials
8.3.1.1 Homojunction Structure
8.3.1.2. Hetrojuction Structure
8.3.2 2D Amorphous-Coated Nanomaterials
8.3.2.1. Carbon-Based Nanomaterials
8.3.2.2 Ni-Based Nanomaterials
8.3.2.3 Other Metal-based Nanomaterials
8.3.3 3D Amorphous-Coated Nanomaterials
8.3.3.1 Silica Coating
8.3.3.2 Carbon Coating
8.3.3.3 Metal Oxide Coating
8.3.3.4 Metal Sulfide Coating
8.4 Amorphous-Doped or Hybrid Nanomaterials
8.4.1 2D Amorphous-Doped Nanomaterials
8.4.2 3D Amorphous-Doped Nanomaterial
8.5 Summary and Outlook
References
9 Applications of Amorphous Nanomaterials in Electrocatalysis. 9.1 Introduction
9.2 Fundamentals of Electrocatalysis
9.3 Amorphous Nanomaterials as Electrocatalysts for Water Splitting
9.3.1 Amorphous Nanomaterials for HER. 9.3.1.1 Amorphous Single Metallic Nanomaterials for HER
9.3.1.2 Amorphous Binary Metallic Nanomaterials for HER
9.3.1.3 Amorphous Composite Nanomaterials for HER
9.3.2 Amorphous Nanomaterials for OER
9.3.2.1 Amorphous Single Metallic Nanomaterials for OER
9.3.2.2 Amorphous Binary Metallic Nanomaterials for OER
9.3.2.3 Amorphous Polynary Metal Nanomaterials for OER
9.3.2.4 Amorphous Composites for OER
9.3.3 Amorphous Nanomaterials for ORR
9.3.3.1 Amorphous Noble Metal-based Nanomaterials for ORR
9.3.3.2 Amorphous 3d Metal-based Nanomaterials for ORR
9.3.4 Amorphous Nanomaterials for CRR
9.3.5 Amorphous Nanomaterials for NRR
9.3.6 Amorphous Nanomaterials as Bifunctional Electrocatalysts
9.3.6.1 Amorphous Nanomaterials as Bifunctional Electrocatalysts of HER and OER
9.3.6.2 Amorphous Nanomaterials as Bifunctional Electrocatalysts of ORR and OER
9.4 Summary and Outlook
References
10 Applications of Amorphous Nanomaterials in Batteries. 10.1 Introduction
10.2 Negative Electrodes in Batteries. 10.2.1 Amorphous Phosphorus Compounds
10.2.2 Amorphous Silicon Compounds
10.2.3 Amorphous Transition Metal Oxides
10.2.3.1 Amorphous Iron Oxides
10.2.3.2 Amorphous Titanium Oxides
10.2.3.3 Amorphous Vanadium-Based Oxides
10.2.3.4 Amorphous Tin-Based Oxides
10.2.4 Amorphous Carbon
10.3 Positive Electrodes in Batteries. 10.3.1 Amorphous Ferric Phosphate
10.3.2 Amorphous Vanadium-Based Oxides
10.3.3 Amorphous Metal Polysulfides
10.4 Summary and Outlook
References
11 Applications of Amorphous Nanomaterials in Supercapacitors. 11.1 Introduction
11.2 Applications in Electric Double-Layer Capacitors
11.3 Applications in Pseudocapacitors
11.3.1 Amorphous Metal Oxides
11.3.2 Amorphous Metal Sulfides
11.3.3 Other Amorphous Nanomaterials
11.4 Summary and Outlook
References
12 Applications of Amorphous Nanomaterials in Photocatalysis. 12.1 Introduction
12.2 Photocatalytic Degradation
12.3 Photocatalytic Decomposition of Water
12.4 Photo-Electrocatalysis
12.5 Amorphous Nanomaterial as Cocatalyst in Photocatalysis
12.6 Other Applications in Photocatalysis
12.7 Summary and Outlook
References
13 Engineering Applications of Amorphous Nanomaterials. 13.1 Introduction
13.2 Mechanical Properties of Amorphous Nanomaterials
13.2.1 Amorphous Alloys/Metals
13.2.2 Amorphous Nonmetallic Materials
13.3 Strategy for Enhancing the Mechanical Performance
13.3.1 Introduction of Micro/Nanosecond Phase
13.3.2 Introduction of Micro/Nano-Inhomogeneity
13.3.3 Surface Modification
13.3.4 Amorphous Based Composite Materials
13.4 Summary and Outlook
References
Index
WILEY END USER LICENSE AGREEMENT
Отрывок из книги
Preparation, Characterization and Applications
Lin Guo
.....
Metallic glass showes a unique disordered structure, without defects such as dislocations and grain boundaries in the crystal, endowing them with many unique superior properties. For example, in terms of mechanical properties, metallic glasses exhibit high strength, high hardness, high wear resistance and corrosion resistance, high fatigue resistance, low elastic modulus, large elastic strain limit, etc. Thus, metallic glass possesses broad potential applications in the fields of engineering mechanics, biological sciences, and aerospace. For example, the amorphous alloys in almost every alloy system have achieved several times higher strength than the crystalline material. In 2011, Zhang Tao et al. [17] developed a CoTaB ternary alloy with a compressive strength of 6.0 GPa and a specific strength of 650 Nm g−1, which reached the highest record for the strength of metal materials.
At the same time, the introduction of micro/nanoscale heterogeneous structures or the second phase in bulk amorphous materials could significantly improve the toughness of amorphous materials. In 2007, according to Poisson’s ratio criterion, Wang Weihua et al. [18] adjusted the composition of the Zr–Cu–Ni–Al metallic alloy and prepared an amorphous alloy system with a multilevel microscale heterogeneous structure, which showed high strength (1.7 GPa) and very large compressive plasticity (strain > 150%). These amorphous alloys can even be bent to 90° at room temperature (Figure 1.6a–d). In 2008, WL Johnson et al. [19] improved the composition of the amorphous alloy and controlled the content of each component to synthesize the Zr–Ti–Nb–Cu–Be metallic alloy with a micron-scale precipitated second phase. For the first time, the fracture deformation has been increased to more than 10%, and up to 14%. At the same time, the fracture toughness of the amorphous alloy reached 170 MPa m0.5, indicating an excellent toughness (Figure 1.6e–g).
.....