Interface of Ceramic-Matrix Composites
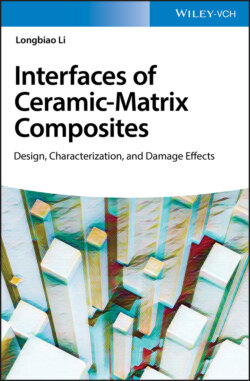
Реклама. ООО «ЛитРес», ИНН: 7719571260.
Оглавление
Longbiao Li. Interface of Ceramic-Matrix Composites
Table of Contents
List of Tables
List of Illustrations
Guide
Pages
Interfaces of Ceramic-Matrix Composites. Design, Characterization and Damage Effects
Preface
Acknowledgments
1 Definition, Function, and Design of Interface in Ceramic‐Matrix Composites. 1.1 Introduction
1.2 The Definition of Interface in Ceramic‐Matrix Composites
1.2.1 Non‐oxide CMCs
1.2.2 Oxide/Oxide CMCs
1.3 The Function of Interface in Ceramic‐Matrix Composites
1.3.1 Effect of Interphase on Sliding Resistance
1.3.2 Effect of Interphase on Thermal Misfit Stress
1.4 The Design of Interface in Ceramic‐Matrix Composites
1.4.1 PyC Interphase
1.4.2 BN Interphase
1.5 Conclusion
References
2 Interface Characterization of Ceramic‐Matrix Composites. 2.1 Introduction
2.2 Effect of Interface Properties on Tensile and Fatigue Behavior of Ceramic‐Matrix Composites
2.2.1 Theoretical Analysis
2.2.1.1 First Matrix Cracking Stress
2.2.1.2 Matrix Cracking Density
2.2.1.3 Fatigue Hysteresis‐Based Damage Parameters
2.2.2 Results and Discussion
2.2.2.1 Effect of the Interface Properties on First Matrix Cracking Stress
2.2.2.2 Effect of the Interface Properties on Matrix Cracking Density
2.2.2.3 Effect of the Interface Properties on the Fatigue Hysteresis‐Based Damage Parameters
2.2.3 Experimental Comparisons
2.2.3.1 First Matrix Cracking Stress
2.2.3.2 Matrix Cracking Density
2.2.3.3 Fatigue Hysteresis‐Based Damage Parameters
2.3 Effect of Pre‐exposure on Tensile Damage and Fracture of Ceramic‐Matrix Composites
2.3.1 Theoretical Analysis
2.3.1.1 Stress Analysis Considering Interface Oxidation and Fiber Failure
2.3.1.2 Matrix Multicracking Considering Interface Oxidation
2.3.1.3 Interface Debonding Considering Interface Oxidation
2.3.1.4 Fiber Failure Considering Interface and Fiber Oxidation
2.3.1.5 Tensile Stress–Strain Curves Considering Effect of Pre‐exposure
2.3.2 Results and Discussion
2.3.2.1 Effect of Pre‐exposure Temperature on Tensile and Damage Process
2.3.2.2 Effect of Pre‐exposure Time on Tensile and Damage Processes
2.3.2.3 Effect of Interface Shear Stress on Tensile and Damage Processes
2.3.2.4 Effect of Fiber Strength on Tensile and Damage Processes
2.3.2.5 Effect of Fiber Weibull Modulus on Tensile and Damage Processes
2.3.3 Experimental Comparisons
2.4 Effect of Interface Properties on Lifetime of Ceramic‐Matrix Composites
2.4.1 Theoretical Analysis
2.4.1.1 Life Prediction Model at Room Temperature
2.4.1.2 Life Prediction Model at Elevated Temperatures in the Oxidative Environment
2.4.2 Experimental Comparisons
2.4.2.1 Life Prediction at Room Temperature
2.4.2.2 Life Prediction at Elevated Temperature
2.5 Conclusion
References
3 Interface Assessment of Ceramic‐Matrix Composites. 3.1 Introduction
3.2 Relationships Between Interface Slip and Temperature Rising in CMCs
3.2.1 Hysteresis Theories
3.2.1.1 Case I
3.2.1.2 Case II
3.2.1.3 Case III
3.2.1.4 Case IV
3.2.2 Experimental Comparisons
3.2.2.1 Unidirectional CMCs
3.2.2.2 Cross‐Ply CMCs
3.2.2.3 2D CMCs
3.3 Interface Assessment of CMCs from Hysteresis Loops
3.3.1 Results and Discussion
3.3.1.1 Unidirectional C/SiC Composite
3.3.1.2 Cross‐Ply C/SiC Composite
3.3.1.3 2.5D C/SiC Composite
3.3.2 Experimental Comparisons
3.3.2.1 Unidirectional C/SiC Composite
3.3.2.2 Unidirectional SiC/CAS Composite
3.3.2.3 Unidirectional SiC/CAS‐II Composite
3.3.2.4 Cross‐Ply C/SiC Composite
3.3.2.5 2.5D C/SiC Composite
3.4 Conclusion
References
4 Interface Damage Law of Ceramic‐Matrix Composites. 4.1 Introduction
4.2 Interface Damage Law at Room Temperature
4.3 Interface Damage Law at Elevated Temperature in Inert Atmosphere
4.4 Interface Damage Law at Elevated Temperature in Air Atmosphere. 4.4.1 1000 °C
4.4.2 1200 °C
4.4.3 1300 °C
4.5 Interface Damage Law at Elevated Temperature in Steam Atmosphere. 4.5.1 1000 °C
4.5.2 1200 °C
4.6 Results and Discussion. 4.6.1 Effect of Temperature, Oxidation, and Fiber Preforms on Interface Damage of CMCs
4.6.2 Comparisons of Interface Damage Between C/SiC and SiC/SiC Composites
4.7 Conclusion
References
Index
WILEY END USER LICENSE AGREEMENT
Отрывок из книги
Longbiao Li
For a monolithic ceramic material, when it is subjected to tensile stress, it appears as elastic deformation at low stress level; as the stress increases, cracks occur in the defect region of the material, and the cracks rapidly expand, causing the material to undergo brittle fracture. When the CMC material is subjected to tensile stress, it is elastically deformed before matrix cracks; as the tensile stress increases, the matrix begins to crack, and the fibers begin to debond and play a role of crack bridging; as the tensile stress increases further, the cracks become saturated, and the bridging fibers begin to pull out; as the tensile stress continues to increase, the fibers begin to break until the material reaches the highest strength. The fracture modes of monolithic ceramics and CMCs are different, mainly because the interface plays a role in the fracture process of CMCs. The interface is a special domain between the matrix and the reinforcement. It is the link between the fiber and the matrix, and also a bridge for load transfer. The structure and properties of interphase directly affect the strength and toughness of CMCs. This book focuses on the time‐dependent mechanical behavior of CMCs at elevated temperatures, as the following:
.....
I hope this book can help the material scientists and engineering designers to understand and master the interface of CMCs.
26 January 2020
.....