Lean Six Sigma For Dummies
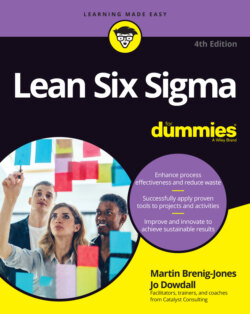
Реклама. ООО «ЛитРес», ИНН: 7719571260.
Оглавление
Martin Brenig-Jones. Lean Six Sigma For Dummies
Lean Six Sigma For Dummies® To view this book's Cheat Sheet, simply go to www.dummies.com and search for “Lean Six Sigma For Dummies Cheat Sheet” in the Search box. Table of Contents
List of Tables
List of Illustrations
Guide
Pages
Introduction
About This Book
Foolish Assumptions
Icons Used In This Book
Beyond This Book
Where to Go From Here
Understanding Lean Six Sigma
Defining Lean Six Sigma
Introducing Lean Thinking
Bringing on the basics of Lean
Building people first
Looking at the lingo
Taking the strain out of constraints
Considering the customer
Perusing the principles of Lean thinking
Sussing Six Sigma
Considering the key elements of Six Sigma
Getting to grips with variation
Introducing a simple example
Considering customer requirements
Calculating Process Sigma values
Bringing Lean and Six Sigma together
Adding More to the Mix
Managing change
Applying Agility
Employing innovation
Practicing Project Management
Understanding the Principles of Lean Six Sigma
Considering the Key Principles of Lean Six Sigma
Focus on the customer
Identify and understand how the work gets done
Manage, improve and smooth the process flow
Remove non-value-adding steps and waste
Manage by fact and reduce variation
Involve and equip the people in the process
Undertake improvement activity in a systematic way
Improving Existing Processes: Introducing DMAIC
Defining your project
Outlining the problem
Framing the scope
Measuring how the work is done
Analyzing your process
Improving your process
Coming up with a control plan
Reviewing Your DMAIC Phases
Taking a Pragmatic Approach
WAX ON, WAX OFF: LEAN SIX SIGMA AND MARTIAL ARTS
Lean Six Sigma Foundations
Identifying Your Process Customers
Understanding the Process Basics
Pinpointing the elements of a process
Identifying internal and external customers
Getting a High-Level Picture
Drawing a high-level process map
Segmenting customers
Understanding Your Customers’ Needs
Considering Kano
Obtaining the Voice of the Customer
Taking an outside-in view
Seeing customer segments
Prioritizing your customers
Researching the Requirements
Interviewing your customers
Focusing on focus groups
Considering customer surveys
Using observations
Avoiding Bias
Considering Critical To Quality Customer Requirements
Establishing the Real CTQs
Prioritizing the requirements
Measuring performance using customer-focused measures
Understanding the Process
Finding Out How the Work Gets Done
GOING TO THE GEMBA
Practicing Process Stapling
PROCESS STAPLING IN ACTION
Drawing spaghetti diagrams
Painting a Picture of the Process
Keeping things simple
Developing a deployment flowchart
Constructing a Value Stream Map
Identifying moments of truth
Managing People and Change
Getting into the Grey Matter
Gaining Acceptance
Sizing Up the Status Quo
Using a forcefield diagram
Analyzing your stakeholders
Coping with Change
Creating the Vision
Busting Assumptions
Understanding Performance and Analyzing the Process
Gathering Data
Managing by Fact
Realizing the importance of good data
Reviewing what you currently measure
Deciding what to measure
Developing a Data Collection Plan
Step 1: Agreeing on the measures
Getting a balance of measures
Connecting things up
Step 2: Creating clear operational definitions
Step 3: Validating your measurement system
Step 4: Developing the Sampling Plan
Population sampling
Process sampling
Determining the sample size
Sampling from a finite population
Step 5: Collecting the data
Identifying ways to improve your approach
Presenting Your Data
Delving into Different Types of Variation
Understanding natural variation
Spotlighting special cause variation
Distinguishing between variation types
Avoiding tampering
Displaying data differently
Recognizing the Importance of Control Charts
Creating a control chart
Spotting special causes
Choosing the right control chart
Examining the state of your processes
Considering the capability of your processes
Handling a histogram
Using Pareto charts
Identifying Root Causes
Unearthing the Suspects
Generating Your List of Suspects
Creating a cause and effect diagram
Applying affinity mapping
Digging deeper with the Five Whys
Understanding the key drivers
Confirming the Causes
Investigating the suspects and getting the facts
Succeeding with scatter plots
Measuring the relationship between X and Y
Handling hypothesis tests
Moving on
Identifying Non-Value-Adding Steps and Waste
Defining Value-Adding
Providing a common definition
Carrying out a value-add/non-value-add analysis
Assessing opportunity
Looking at the Eight Wastes
Troubling over transportation
Investigating inventory
Moving in on motion
Playing the waiting game
Owning up to overproduction
Picking on overprocessing
Dealing with defects
Realizing the potential in people
Going greener with Lean Six Sigma
Considering customer perspectives
Going for a Waste Walk
Getting the Process to Flow
Applying the Theory of Constraints
Identifying the weakest link
Improving the process flow
Building a buffer
Managing the Production Cycle
Using pull rather than push production
Moving to single piece flow
Recognizing the problem with batches
Looking at Your Layout
Identifying wasted movement
Using cell manufacturing (a.k.a. autonomous working)
Applying cell manufacturing in the office
Identifying product families
Taking takt time into account
Improving and Innovating
Thinking Differently and Generating Solutions
Getting Immersed in Ideas
Showering and storming
Negative brainstorming
Using words and pictures
Brainwriting
Identifying the attributes
Additional tools for idea generation
TEN TOP TIPS FOR BOOSTING CREATIVITY
Prioritizing the Ideas
Feeling dotty with n/3
Using a criteria selection matrix
Testing the Ideas to See What Will Fly
Discovering the Opportunity for Prevention
Looking at Prevention Tools and Techniques
Introducing Jidoka
Recognizing risk with Failure Mode and Effects Analysis
Error proofing your processes
Workplace Organization
Introducing the Five Ss
Carrying out a red-tag exercise
Using Visual Management
Profiting from Preventive Maintenance
Avoiding Peaks and Troughs
Introducing Heijunka
Spreading the load
Carrying out work in a standard way
Building in Business Process Robotics
Introducing Design for Six Sigma
Introducing DfSS
Introducing DMADV
Defining What Needs Designing
Getting the measure of needs
Analyzing for design
Developing the detailed design
Verifying that the design works
Choosing between DMAIC and DMADV
Considering Quality Function Deployment (QFD)
Clarifying the floorplan
Room 1: Customer needs
Room 2: Prioritizing needs and looking at the competition
Room 3: Characteristics and measures
Room 4: Relationships
Room 5: Competitive benchmarking
Room 6: Targets and limits
Room 7: Correlation
Undertaking a QFD drill-down
Making Decisions
Discovering Design Thinking
The Principles of Design Thinking
Comparing DMADV and Design Thinking
Walking through the Design Thinking Steps
Understanding the task
Empathizing and observing
Redefining the problem
Finding ideas (ideation)
Designing prototypes
Testing ideas and assumptions
Deciding on Design Thinking
Applying Agile to Lean Six Sigma Projects
Understanding Agile Principles
Embracing an Agile Mindset
Succeeding in the Scrum
Understanding Agile roles
Scrum Master
Product Owner
Team members
Concentrating on customer requirements
Capitalizing on Kanbans
Combining Agile and Lean Six Sigma
Deploying Lean Six Sigma and Making Change Happen
Running Rapid Improvement Events and Solving Problems with DMAIC
Raving about Rapid Improvement
Understanding the Facilitator’s Role
Planning and preparation
Running the event
Following up and action planning
Creating a Checklist for Running Successful Events
Practicing Problem Solving
Ensuring Everyday Operational Excellence
Standardizing the Process
Perfecting the process handover
Populating the Process Management Chart
Making Everyday Operational Excellence a Reality
Embracing Leader Standard Work
Engaging the team
Using the right methodology
Creating a culture of Continuous Improvement
Understanding Organizational Culture
Leading the Deployment and Selecting the Right Projects
Considering Key Factors for Successful Deployment
Understanding Executive Sponsorship
Considering Size and Sector
Recognizing the Important Role of Managers
Introducing the Deployment Program Manager
Starting Your Lean Six Sigma Program
Understanding What Project Sponsors Do
Driving Strategy Deployment with Lean Six Sigma
Generating a List of Candidate Improvement Projects
Deciding Whether Lean Six Sigma Is the Right Approach
Prioritizing projects
Deciding on which approach fits which project
Setting Up a DMAIC Project
Putting It All Together: Checklists to Support Your DMAIC Project
Defining the Project
Delivering the Define phase
Getting through the Define phase tollgate
Moving into the Measure Phase
Making good on Measure phase deliverables
Getting through the Measure phase tollgate
Analyzing to Identify Root Causes
Acing the Analyze phase
Getting through the Analyze phase tollgate
Quantifying the Opportunity
Identifying and Planning the Improvements
Executing the Improve phase
Getting through the Improve phase tollgate
Confirming the Customer and Business Benefits
Implementing the Solutions and Controlling the Process
Completing the Control phase
Getting through the Control phase tollgate
Conducting the Final Benefit Review
The Part of Tens
Ten Tips for Best-Practice Project Storyboards
Keep It Brief
Make It Visual
Make It Flow
Weave the Story Together with a Golden Thread
Keep It Up to Date as You Go Along
Don't Forget the “Happily Ever After” Part
Keep It Simple
Develop a One-Page Summary
Reflect on the Lessons Learned
Share, Share, Share!
Ten Pitfalls to Avoid
Jumping to Solutions
Coming Down with Analysis Paralysis
Falling into Common Project Traps
Stifling the Program Before You’ve Started
Ignoring Change Management
Getting Complacent
Thinking That You’re Already Doing It
Believing the Myths
Doing the Wrong Things Right
Overtraining
Ten (Plus One) Places to Go for Help
Your Colleagues
Your Sponsor
Other Organizations
The Internet
Social Media
Networks and Associations
Conferences
Books
Periodicals
Software
Statistical analysis
Simulation
Deployment management
Online collaboration tools
Training and Consulting Companies
Index. A
B
C
D
E
F
G
H
I
J
K
L
M
N
O
P
Q
R
S
T
U
V
W
X
Y
About the Authors
Authors' Acknowledgments
WILEY END USER LICENSE AGREEMENT
Отрывок из книги
Lean Six Sigma provides a rigorous and structured approach to help manage and improve quality and performance, and to solve potentially complex problems. It helps you use the right tools, in the right place and in the right way, not just in process improvement projects but also in your day-to-day work. Lean Six Sigma really is about getting key principles and concepts into the DNA and lifeblood of your organization so that it becomes a natural part of how you do things.
This book is for practitioners using Lean Six Sigma as well as those who are seeking to “lead and live” Lean Six Sigma in their organizations.
.....
Throughout the book, you’ll see small symbols called icons in the margins; these highlight special types of information. We use these to help you better understand and apply the material. Look out for the following icons:
Keep your eyes on the target to find tips and tricks we share to help you make the most of Lean Six Sigma.
.....