Wind Energy Handbook
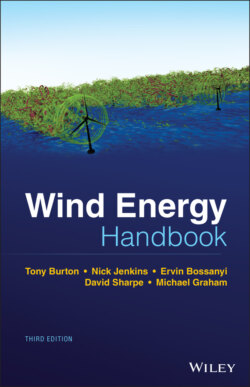
Реклама. ООО «ЛитРес», ИНН: 7719571260.
Оглавление
Michael Barton Graham. Wind Energy Handbook
Table of Contents
List of Tables
List of Illustrations
Guide
Pages
Wind Energy Handbook
About the Authors
Preface to Second Edition
Preface to Third Edition
Acknowledgements for the First Edition
Acknowledgements for the Second Edition
Acknowledgements for the Third Edition
List of Symbols
Greek
Subscripts
Superscripts
Figures C1 and C2 – coordinate systems
1. Introduction. 1.1 Historical development of wind energy
1.2 Modern wind turbines
1.3 Scope of the book
References
Websites
Further Reading
2.1 The nature of the wind
2.2 Geographical variation in the wind resource
2.3 Long‐term wind speed variations
2.4 Annual and seasonal variations
2.5 Synoptic and diurnal variations
2.6 Turbulence. 2.6.1 The nature of turbulence
2.6.2 The boundary layer
2.6.3 Turbulence intensity
2.6.4 Turbulence spectra
2.6.5 Length scales and other parameters
2.6.6 Asymptotic limits
2.6.7 Cross‐spectra and coherence functions
2.6.8 The Mann model of turbulence
2.7 Gust wind speeds
2.8 Extreme wind speeds
2.8.1 Extreme winds in standards
2.9 Wind speed prediction and forecasting
2.9.1 Statistical methods
2.9.2 Meteorological methods
2.9.3 Current methods
2.10 Turbulence in complex terrain
References
3. Aerodynamics of horizontal axis wind turbines. Author's note on aerodynamics
3.1 Introduction
3.2 The actuator disc concept
3.2.1 Simple momentum theory
3.2.2 Power coefficient
3.2.3 The Betz limit
3.2.4 The thrust coefficient
3.3 Rotor disc theory
3.3.1 Wake rotation
3.3.2 Angular momentum theory
3.3.3 Maximum power
3.4 Vortex cylinder model of the actuator disc. 3.4.1 Introduction
3.4.2 Vortex cylinder theory
3.4.3 Relationship between bound circulation and the induced velocity
3.4.4 Root vortex
3.4.5 Torque and power
3.4.6 Axial flow field
3.4.7 Tangential flow field
3.4.8 Axial thrust
3.4.9 Radial flow and the general flow field
3.4.10 Further development of the actuator model
3.4.11 Conclusions
3.5 Rotor blade theory (blade‐element/momentum theory) 3.5.1 Introduction
3.5.2 Blade element theory
3.5.3 The BEM theory
3.5.4 Determination of rotor torque and power
3.6 Actuator line theory, including radial variation
3.7 Breakdown of the momentum theory. 3.7.1 Free‐stream/wake mixing
3.7.2 Modification of rotor thrust caused by wake breakdown
3.7.3 Empirical determination of thrust coefficient
3.8 Blade geometry. 3.8.1 Introduction
3.8.2 Optimal design for variable‐speed operation
3.8.3 A simple blade design
3.8.4 Effects of drag on optimal blade design
3.8.5 Optimal blade design for constant‐speed operation
3.9 The effects of a discrete number of blades. 3.9.1 Introduction
3.9.2 Tip‐losses
3.9.3 Prandtl's approximation for the tip‐loss factor
3.9.4 Blade root losses
3.9.5 Effect of tip‐loss on optimum blade design and power
3.9.6 Incorporation of tip‐loss for non‐optimal operation
3.9.7 Radial effects and an alternative explanation for tip‐loss
3.10 Stall delay
3.11 Calculated results for an actual turbine
3.12 The performance curves. 3.12.1 Introduction
3.12.2 The CP – λ performance curve
3.12.3 The effect of solidity on performance
3.12.4 The CQ – λ curve
3.12.5 The CT – λ curve
3.13 Constant rotational speed operation. 3.13.1 Introduction
3.13.2 The KP−1/λ curve
3.13.3 Stall regulation
3.13.4 Effect of rotational speed change
3.13.5 Effect of blade pitch angle change
3.14 Pitch regulation. 3.14.1 Introduction
3.14.2 Pitching to stall
3.14.3 Pitching to feather
3.15 Comparison of measured with theoretical performance
3.16 Estimation of energy capture
3.17 Wind turbine aerofoil design. 3.17.1 Introduction
3.17.2 The NREL aerofoils
3.17.3 The Risø aerofoils
3.17.4 The Delft aerofoils
3.17.5 General principles for outboard and inboard blade sections
3.18 Add‐ons (including blade modifications independent of the main structure)
3.18.1 Devices to control separation and stalling
3.18.2 Devices to increase CLmax and lift/drag ratio
3.18.3 Circulation control (jet flaps)
3.19 Aerodynamic noise. 3.19.1 Noise sources
3.19.2 Inflow turbulence‐induced blade noise
3.19.3 Self‐induced blade noise
3.19.4 Interaction between turbulent boundary layers on the blade and the trailing edge
3.19.5 Other blade noise sources
3.19.6 Summary
References
Websites
Further Reading
Appendix A3 Lift and drag of aerofoils
A3.1 Drag
A3.2 The boundary layer
A3.3 Boundary layer separation
A3.4 Laminar and turbulent boundary layers and transition
A3.5 Definition of lift and its relationship to circulation
A3.6 The stalled aerofoil
A3.7 The lift coefficient
A3.8 Aerofoil drag characteristics
A3.8.1 Symmetric aerofoils
A3.8.2 Cambered aerofoils
Note
4. Further aerodynamic topics for wind turbines. 4.1 Introduction
4.2 The aerodynamics of turbines in steady yaw
4.2.1 Momentum theory for a turbine rotor in steady yaw
4.2.2 Glauert's momentum theory for the yawed rotor
4.2.3 Vortex cylinder model of the yawed actuator disc
4.2.4 Flow expansion
4.2.5 Related theories
4.2.6 Wake rotation for a turbine rotor in steady yaw
4.2.7 The blade element theory for a turbine rotor in steady yaw
4.2.8 The blade‐element‐momentum theory for a rotor in steady yaw
4.2.9 Calculated values of induced velocity
4.2.10 Blade forces for a rotor in steady yaw
4.2.11 Yawing and tilting moments in steady yaw
4.3 Circular wing theory applied to a rotor in yaw. 4.3.1 Introduction
4.3.2 The general pressure distribution theory of Kinner
4.3.3 The axisymmetric loading distributions
4.3.4 The anti‐symmetric loading distribution
4.3.5 The Pitt and Peters model
4.3.6 The general acceleration potential method
4.3.7 Comparison of methods
4.4.1 Introduction
4.4.2 The acceleration potential method to analyse unsteady flow
4.4.3 Unsteady yawing and tilting moments
4.5.1 Introduction
4.5.2 Aerodynamic forces caused by aerofoil acceleration
4.5.3 The effect of the shed vortex wake on an aerofoil in unsteady flow
4.6 Dynamic stall. 4.6.1 Introduction
4.6.2 Dynamic stall models
The Leishman–Beddoes model
The ONERA model
The Gangwani model
4.7 Computational fluid dynamics. 4.7.1 Introduction
4.7.2 Inviscid computational methods
4.7.3 RANS and URANS CFD methods
4.7.4 LES and DES methods
4.7.5 Numerical techniques for CFD
Inviscid flow
Viscous flow (primitive variable methods)
4.7.6 Discrete methods of approximating the terms in the Navier–Stokes equations over the flow field
The finite difference method (FDM)
Finite volume method (FVM)
Finite element method (FEM)
4.7.7 Grid construction
4.7.8 Full flow field simulation including ABL and wind turbines. Incident flow field (ABL)
Large‐scale wind farm simulations
References
Further Reading
Note
5. Design loads for HAWTs. 5.1 National and international standards. 5.1.1 Historical development
5.1.2 IEC 61400‐1
5.2 Basis for design loads. 5.2.1 Sources of loading
5.2.2 Ultimate loads
5.2.3 Fatigue loads
5.2.4 Partial safety factors. Partial safety factors for loads
Partial safety factors for the consequences of failure
5.2.5 Functions of the control and safety systems
5.3 Turbulence and wakes
5.4.1 Operational load cases
Power production load cases – normal machine state
Fault occurrence during power production
Start‐up load cases
Shut‐down load cases
5.4.2 Non‐operational load cases. Normal machine state
Machine fault state
5.4.3 Blade/tower clearance
5.4.4 Constrained stochastic simulation of wind gusts
5.5.1 Synthesis of fatigue load spectrum
5.6 Stationary blade loading. 5.6.1 Lift and drag coefficients
5.6.2 Critical configuration for different machine types
5.6.3 Dynamic response. Tip displacement
Damping
Root bending moment
Spanwise variation of bending moment
5.7.1 Deterministic and stochastic load components
5.7.2 Deterministic aerodynamic loads. Steady, uniform flow perpendicular to plane of rotor
Yawed flow
Shaft tilt
Wind shear
Tower shadow
Wake effects
5.7.3 Gravity loads
5.7.4 Deterministic inertia loads. Centrifugal loads
Gyroscopic loads
Braking loads
Teeter loads
5.7.5 Stochastic aerodynamic loads: analysis in the frequency domain
Rotationally sampled spectrum
Effect of reduced length scale
Rotationally sampled cross‐spectra
Limitations of analysis in the frequency domain
5.7.6 Stochastic aerodynamic loads: analysis in the time domain. Wind simulation
Wind simulation by the harmonic series method
Blade load time histories
5.7.7 Extreme loads
5.8.1 Modal analysis
5.8.2 Mode shapes and frequencies
5.8.3 Centrifugal stiffening
5.8.4 Aerodynamic and structural damping
5.8.5 Response to deterministic loads: step‐by‐step dynamic analysis
Linear acceleration method
Avoidance of resonance: the Campbell diagram
5.8.6 Response to stochastic loads
Power spectrum of generalised blade loading
Power spectrum of tip deflection
Power spectrum of blade root bending moment
5.8.7 Response to simulated loads
5.8.8 Teeter motion
Teeter response to deterministic loads
Teeter response to stochastic loads
5.8.9 Tower coupling
5.8.10 Aeroelastic stability
5.9 Blade fatigue stresses. 5.9.1 Methodology for blade fatigue design
5.9.2 Combination of deterministic and stochastic components
5.9.3 Fatigue prediction in the frequency domain
5.9.4 Wind simulation
5.9.5 Fatigue cycle counting
5.10 Hub and low‐speed shaft loading. 5.10.1 Introduction
5.10.2 Deterministic aerodynamic loads
5.10.3 Stochastic aerodynamic loads
5.10.4 Gravity loading
5.11.1 Loadings from rotor
5.11.2 Nacelle wind loads
5.12 Tower loading. 5.12.1 Extreme loads
5.12.2 Dynamic response to extreme loads
5.12.3 Operational loads due to steady wind (deterministic component)
5.12.4 Operational loads due to turbulence (stochastic component) Analysis in the frequency domain
Analysis in the time domain
5.12.5 Dynamic response to operational loads
5.12.6 Fatigue loads and stresses
5.13 Wind turbine dynamic analysis codes
5.14 Extrapolation of extreme loads from simulations
5.14.1 Derivation of empirical cumulative distribution function of global extremes
5.14.2 Fitting an extreme value distribution to the empirical distribution
5.14.3 Comparison of extreme value distributions
5.14.4 Combination of probability distributions
5.14.5 Extrapolation
5.14.6 Fitting probability distribution after aggregation
5.14.7 Local extremes method
5.14.8 Convergence requirements
References
Appendix A5 Dynamic response of stationary blade in turbulent wind. A5.1 Introduction
A5.2 Frequency response function. A5.2.1 Equation of motion
A5.2.2 Frequency response function
A5.3 Resonant displacement response ignoring wind variations along the blade. A5.3.1 Linearisation of wind loading
A5.3.2 First mode displacement response
A5.3.3 Background and resonant response
A5.4 Effect of across wind turbulence distribution on resonant displacement response
A5.4.1 Formula for normalised co‐spectrum
A5.5 Resonant root bending moment
A5.6 Root bending moment background response
A5.7 Peak response
A5.8 Bending moments at intermediate blade positions. A5.8.1 Background response
A5.8.2 Resonant response
References
6. Conceptual design of horizontal axis wind turbines. 6.1 Introduction
6.2 Rotor diameter
6.2.1 Cost modelling
6.2.2 Simplified cost model for machine size optimisation: an illustration
6.2.3 The NREL cost model
6.2.4 The INNWIND.EU cost model
6.2.5 Machine size growth
6.2.6 Gravity limitations
6.2.7 Variable diameter rotors
6.3 Machine rating
6.3.1 Simplified cost model for optimising machine rating in relation to diameter
6.3.2 Relationship between optimum rated wind speed and annual mean
6.3.3 Specific power of production machines
6.4 Rotational speed
6.4.1 Ideal relationship between rotational speed and solidity
6.4.2 Influence of rotational speed on blade weight
6.4.3 High‐speed rotors
6.4.4 Low induction rotors
6.4.5 Noise constraint on rotational speed
6.4.6 Visual considerations
6.5 Number of blades. 6.5.1 Overview
6.5.2 Ideal relationship between number of blades, rotational speed, and solidity
6.5.3 Effect of number of blades on optimum CP in the presence of tip‐loss and drag
6.5.4 Some performance and cost comparisons
6.5.5 Effect of number of blades on loads
6.5.6 Noise constraint on rotational speed
6.5.7 Visual appearance
6.5.8 Single bladed turbines
6.6 Teetering. 6.6.1 Load relief benefits
6.6.2 Limitation of large excursions
6.6.3 Pitch‐teeter coupling
6.6.4 Teeter stability on stall‐regulated machines
6.7 Power control. 6.7.1 Passive stall control
6.7.2 Active pitch control
6.7.3 Passive pitch control
6.7.4 Active stall control
6.7.5 Yaw control
6.8.1 Independent braking systems: requirements of standards
6.8.2 Aerodynamic brake options
6.8.3 Mechanical brake options
6.8.4 Parking versus idling
6.9 Fixed‐speed, two‐speed, variable‐slip, and variable‐speed operation
6.9.1 Fixed‐speed operation
6.9.2 Two‐speed operation
6.9.3 Variable‐slip operation (see also Section 8.3.8)
6.9.4 Variable‐speed operation
6.9.5 Generator system architectures
6.9.6 Low‐speed direct drive generators
6.9.7 Hybrid gearboxes, medium‐speed generators
6.9.8 Evolution of generator systems
6.10 Other drive trains and generators
6.10.1 Directly connected, fixed‐speed generators
6.10.2 Innovations to allow the use of directly connected generators
6.10.3 Generator and drive train innovations
Superconducting generators
Magnetic gearboxes
Brushless doubly fed induction generators
Direct current power collection
6.11.1 Low‐speed shaft mounting
6.11.2 High‐speed shaft and generator mounting
6.12 Drive train compliance
6.13 Rotor position with respect to tower. 6.13.1 Upwind configuration
6.13.2 Downwind configuration
6.14 Tower stiffness
6.14.1 Stochastic thrust loading at blade passing frequency
6.14.2 Tower top moment fluctuations due to blade pitch errors
6.14.3 Tower top moment fluctuations due to rotor mass imbalance
6.14.4 Tower stiffness categories
6.15 Multiple rotor structures
6.15.1 Space frame support structure
6.15.2 Tubular cantilever arm support structure
6.15.3 Vestas four‐rotor array
6.15.4 Cost comparison based on fundamental scaling rules
6.15.5 Cost comparison based on NREL scaling indices
6.15.6 Discussion
6.16 Augmented flow
6.17 Personnel safety and access issues
References
Note
7.1 Blades. 7.1.1 Introduction
7.1.2 Aerodynamic design
7.1.3 Practical modifications to optimum aerodynamic design
7.1.4 Structural design criteria
7.1.5 Form of blade structure
7.1.6 Blade materials and properties
7.1.7 Static properties of glass/polyester and glass/epoxy composites
Glass fibre properties
Matrix properties
Uniaxial plies
Biaxial plies
Triaxial laminate
7.1.8 Fatigue properties of glass/polyester and glass/epoxy composites
S‐N curves
Influences of fibre content, matrix, and fabric
Constant life diagrams
Linear Goodman diagram
Miner's damage sum
Load sequence effects
Strength degradation models
Fatigue at structural details
7.1.9 Carbon fibre composites. Carbon fibre properties
Carbon fibre composite properties
Pultrusion
Benefits versus cost
7.1.10 Properties of wood laminates
Static properties
Fatigue properties
7.1.11 Material safety factors
7.1.12 Manufacture of composite blades
Mould lay‐up
Resin application
Vacuum resin infusion
Pre‐pregs
Assembly of half shells
Segmental construction
Filament winding
7.1.13 Blade loading overview
Extreme loading during operation: stall‐regulated machines
Extreme loading during operation: pitch‐regulated machines
Fatigue loading
Behaviour of stall‐regulated machines in fatigue
Behaviour of pitch‐regulated machines in fatigue
Factors affecting fatigue criticality
Other sources of variability
Fatigue due to gravity loading
Tip deflection
7.1.14 Simplified fatigue design example
Blade geometry
Blade structure description
Operating regime
Deterministic loading
Stochastic loading
Combination of deterministic and stochastic stresses
Very low frequency cycles
Spar cap thickness profile
Variation of fatigue stresses and damage with wind speed
Fatigue criticality at root
Tip clearance
Scaling the fatigue design to 160 m diameter
7.1.15 Blade resonance
Vibrations in stall
Effect of blade twist
Coupling of edgewise blade mode and rotor whirl modes
Mechanical damping
7.1.16 Design against buckling
Critical buckling stress
Allowance for imperfections
7.1.17 Blade root fixings
7.1.18 Blade testing
Static testing
Fatigue testing
7.1.19 Leading edge erosion
Energy loss
Rain drop impact
Protection against erosion
7.1.20 Bend‐twist coupling
Off‐axis fibres
Ratio of twisting and bending rotations under the action of applied moment
Coupling coefficient
Bending moment reduction
Blade pitch correction
Tower clearance
Swept‐back blades
Commercial application
7.2 Pitch bearings
7.3 Rotor hub
7.4 Gearbox. 7.4.1 Introduction
7.4.2 Variable loads during operation
7.4.3 Drive train dynamics
7.4.4 Braking loads
7.4.5 Effect of variable loading on fatigue design of gear teeth
7.4.6 Effect of variable loading on fatigue design of bearings and shafts
7.4.7 Gear arrangements
7.4.8 Gearbox noise
7.4.9 Integrated gearboxes
7.4.10 Lubrication and cooling
7.4.11 Gearbox efficiency
7.5.1 Fixed‐speed induction generators
7.5.2 Variable‐slip induction generators
7.5.3 Variable‐speed operation
7.5.4 Variable‐speed operation using a DFIG
7.5.5 Variable‐speed operation using a full power converter
7.6 Mechanical brake. 7.6.1 Brake duty
7.6.2 Factors governing brake design
7.6.3 Calculation of brake disc temperature rise
7.6.4 High‐speed shaft brake design
7.6.5 Two‐level braking
7.6.6 Low‐speed shaft brake design
7.7 Nacelle bedplate
7.8 Yaw drive
7.9 Tower. 7.9.1 Introduction
7.9.2 Constraints on first mode natural frequency
7.9.3 Steel tubular towers
Design against buckling
Fatigue design
Relative criticality of extreme and fatigue loads
Tuning of tower natural frequency
Joints between tower sections
Bolted flange joints
Bolted lap joints
Tower tie‐down
Tower doorways
7.9.4 Steel lattice towers
7.9.5 Hybrid towers
7.10 Foundations
7.10.1 Slab foundations
7.10.2 Multi‐pile foundations
7.10.3 Concrete monopile foundations
7.10.4 Foundations for steel lattice towers
7.10.5 Foundation rotational stiffness
References
8 The controller
8.1 Functions of the wind turbine controller. 8.1.1 Supervisory control
8.1.2 Closed‐loop control
8.1.3 The safety system
8.2.1 Pitch control
8.2.2 Stall control
8.2.3 Generator torque control
8.2.4 Yaw control
8.2.5 Influence of the controller on loads
8.2.6 Defining controller objectives
8.2.7 PI and PID controllers
8.3 Closed‐loop control: general techniques
8.3.1 Control of fixed‐speed, pitch‐regulated turbines
8.3.2 Control of variable‐speed, pitch‐regulated turbines
8.3.3 Pitch control for variable‐speed turbines
8.3.4 Switching between torque and pitch control
8.3.5 Control of tower vibration
8.3.6 Control of drive train torsional vibration
8.3.7 Variable‐speed stall regulation
8.3.8 Control of variable‐slip turbines
8.3.9 Individual pitch control
8.3.10 Multivariable control – decoupling the wind turbine control loops
8.3.11 Two axis decoupling for individual pitch control
8.3.12 Load reduction with individual pitch control
8.3.13 Individual pitch control implementation
8.3.14 Further extensions to individual pitch control
8.3.15 Commercial use of individual pitch control
8.3.16 Estimation of rotor average wind speed
8.3.17 LiDAR‐assisted control
8.3.18 LiDAR signal processing
8.4 Closed‐loop control: analytical design methods
8.4.1 Classical design methods
8.4.2 Gain scheduling for pitch controllers
8.4.3 Adding more terms to the controller
8.4.4 Other extensions to classical controllers
8.4.5 Optimal feedback methods
8.4.6 Pros and cons of model based control methods
8.4.7 Other methods
8.5 Pitch actuators
8.6 Control system implementation
8.6.1 Discretisation
8.6.2 Integrator desaturation
References
9 Wake effects and wind farm control. 9.1 Introduction
9.2 Wake characteristics
9.2.1 Modelling wake effects
9.2.2 Wake turbulence in the IEC standard
9.2.3 CFD models
9.2.4 Simplified or ‘engineering’ wake models
Velocity deficit
Wake turbulence
Wake deflection due to yaw
Wake superposition
Wake meandering and advection
9.2.5 Wind farm models
9.3 Active wake control methods
9.3.1 Wake control options
Conventional sector management
Axial induction control
Wake steering control
Combining axial induction and wake steering control
Other possibilities
9.3.2 Control objectives
Higher energy capture
Management of fatigue loading
Better management of grid ancillary services provision
9.3.3 Control design methods for active wake control
Quasi‐static open‐loop or feedforward control
Dynamic closed‐loop feedback control
Machine learning
9.3.4 Field testing for active wake control
9.4 Wind farm control and the grid system
9.4.1 Curtailment and delta control
9.4.2 Fast frequency response
References
10 Onshore wind turbine installations and wind farms
10.1 Project development
10.1.1 Initial site selection
10.1.2 Project feasibility assessment
10.1.3 Measure–correlate–predict
10.1.4 Micrositing
10.1.5 Site investigations
10.1.6 Public consultation
10.1.7 Preparation of the planning application and environmental statement
10.1.8 Planning requirements in the UK
10.1.9 Procurement of wind farms
10.1.10 Financing of wind farms
10.2 Landscape and visual impact assessment
10.2.1 Landscape character assessment
10.2.2 Turbine and wind farm design for minimum visual impact
10.2.3 Assessment of visual impact
10.2.4 Shadow flicker
10.3 Noise
10.3.1 Terminology and basic concepts
10.3.2 Wind turbine noise
10.3.3 Measurement of wind turbine noise
10.3.4 Prediction and assessment of wind farm noise
10.3.5 Low frequency noise
10.4 Electromagnetic interference
10.4.1 Impact of wind turbines on communication systems
10.4.2 Impact of wind turbines on aviation radar
10.5 Ecological assessment
10.5.1 Impact on birds
10.5.2 Impact on bats
References
Software
Notes
11 Wind energy and the electric power system. 11.1 Introduction
11.1.1 The electric power system
11.1.2 Electrical distribution networks
11.1.3 Electrical transmission systems
11.2 Wind turbine electrical systems
11.2.1 Wind turbine transformers
11.2.2 Protection of wind turbine electrical systems
11.2.3 Lightning protection of wind turbines
11.3 Wind farm electrical systems. 11.3.1 Power collection system
11.3.2 Earthing (grounding) of wind farms
11.4 Connection of wind farms to distribution networks
11.4.1 Power system studies
11.4.2 Electrical protection of a wind farm
11.4.3 Islanding and anti‐islanding protection
11.4.4 Utility protection of a wind farm
11.5 Grid codes and the connection of large wind farms to transmission networks
11.5.1 Continuous operation capability
11.5.2 Reactive power capability
11.5.3 Frequency response
11.5.4 Fault ride through
11.5.5 Fast fault current injection
11.5.6 Synthetic inertia
11.6 Wind energy and the generation system
11.6.1 Development (planning) of a generation system including wind energy
11.6.2 Operation of a generation system including wind energy
11.6.3 Wind power forecasting
11.7 Power quality
11.7.1 Voltage flicker perception
11.7.2 Measurement and assessment of power quality characteristics of grid connected wind turbines
11.7.3 Harmonics
References
Appendix A11 Simple calculations for the connection of wind turbines. A11.1 The per‐unit system
A11.2 Power flows, slow voltage variations, and network losses
Notes
12 Offshore wind turbines and wind farms. 12.1 Offshore wind farms
12.2 The offshore wind resource. 12.2.1 Winds offshore
12.2.2 Site wind speed assessment
12.2.3 Wakes in offshore wind farms
12.3 Design loads. 12.3.1 International standards
12.3.2 Wind conditions
12.3.3 Marine conditions
12.3.4 Wave spectra
12.3.5 Ultimate loads: operational load cases and accompanying wave climates
Normal sea state
Severe sea state
Embedded extreme regular wave
Environmental contours
12.3.6 Ultimate loads: non‐operational load cases and accompanying wave climates
Extreme sea state
Embedded extreme regular wave
Modification of wave climate in shallow water
12.3.7 Fatigue loads
12.3.8 Wave theories
Airy wave theory
Dean's stream function theory
12.3.9 Wave loading on support structure
Morison's equation
Values of drag and inertia coefficients
Ratio of drag force to inertia force
Airy wave loading on cylinder
Cylinder loading for non‐linear waves
Diffraction
Breaking waves
12.3.10 Constrained waves
12.3.11 Analysis of support structure loads
Extreme loads
Fatigue loads
12.4 Machine size optimisation
12.5 Reliability of offshore wind turbines
12.5.1 Machine architecture
12.5.2 Redundancy
12.5.3 Component quality
12.5.4 Protection against corrosion
12.5.5 Condition monitoring
Drive train vibration monitoring
Lubricant oil debris detection
Nacelle vibration monitoring
Pitch bearing resistance
Added value
12.6 Fixed support structures – overview
12.7 Fixed support structures. 12.7.1 Monopiles – introduction
12.7.2 Monopiles – geotechnical design
The PISA project
Layered soils
Potential benefits of PISA approach
Cyclic loading
Scour
12.7.3 Monopiles – steel design
Transition piece
Cable ducts
Corrosion protection
Grouted joint design
Monopiles in deeper water
12.7.4 Monopiles – fatigue analysis in the frequency domain
Wave loading in the frequency domain
Bending moment and stress transfer functions for a monopile
Example mudline bending moment transfer functions
Effect of diffraction
Aerodynamic damping
Wind wave mis‐alignment
Structural damping
Soil damping
Damping during turbine shut‐down
Monopile bending moment spectra
Approximate treatment of moment response for fatigue analysis purposes
Derivation of fatigue damage
Wind loading in the frequency domain
Wind loading in the time domain
Combination of wind and wave loading fatigue spectra
12.7.5 Gravity bases
Gravity bases in the Southern Baltic
Gravity bases in the North Sea off Belgium
Gravity bases in the North Sea off Blyth, United Kingdom
12.7.6 Jacket structures
Transition section
Three legged jackets
Simplified jacket models for turbine dynamic response analysis
Piling
Suction buckets
Installation methods
Jacket weights
Comparison with monopile weights
Integrated jacket structure and tower
12.7.7 Tripod structures
Alpha Ventus tripod structures
Borkum West 2 tripod structures
12.7.8 Tripile structures
12.7.9 S‐N curves for fatigue design. Derivation of S‐N curve
12.8 Floating support structures. 12.8.1 Introduction
12.8.2 Floater concepts
Spar buoys
Barges
Semi‐submersibles
Tension leg platforms
Additional loads on turbine
12.8.3 Design standards
12.8.4 Design considerations
Initial design objectives
Design space
Response to regular waves
Aero‐servo‐hydro‐elastic software tools
Pitch control adaptation
Critical load case selection
12.8.5 Spar buoy design space
12.8.6 Semi‐submersible design space
Four column semi‐submersible with central wind turbine generator tower
12 Benefit of heave plates
Three column semi‐submersible with wind turbine generator tower coaxial with one of the columns
Natural frequency considerations
12.8.7 Station keeping
12.8.8 Spar buoy case study – Hywind Scotland
12.8.9 Three column semi‐submersible case study – WindFloat Atlantic
WindFloat 1
12.8.10 Ring shaped floating platform – Floatgen, France
12.9 Environmental assessment of offshore wind farms. 12.9.1 Environmental impact assessment
12.9.2 Contents of the environmental statement of an offshore wind farm
12.9.3 Environmental monitoring of wind farms in operation
12.10 Offshore power collection and transmission systems
12.10.1 Offshore wind farm transmission systems
12.10.2 Submarine AC cable systems
12.10.3 HVdc transmission
References
Appendix A12 Costs of electricity
A12.1 Levelised cost of electricity
A12.2 Strike price and contract for difference
Note
Index
WILEY END USER LICENSE AGREEMENT
Отрывок из книги
Third Edition
Tony Burton
.....
The mathematical detail of Prandtl's analysis is given in Glauert (1935a), and because it is based on a somewhat strangely simplified model of the wake will not be repeated here. It has, however, remained the most commonly used tip‐loss correction because it is reasonably accurate and, unlike Goldstein's theory, the result can be expressed in closed solution form. The Prandtl tip‐loss factor is given by
Rw − r is a distance measured from the wake edge. Distance d between the discs should be that of the distance travelled by the flow between successive vortex sheets. Glauert (1935a), takes d as being the normal distance between successive helicoidal vortex sheets.
.....