Delivering Safety Excellence
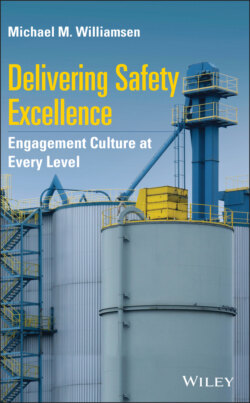
Реклама. ООО «ЛитРес», ИНН: 7719571260.
Оглавление
Michael M. Williamsen. Delivering Safety Excellence
Table of Contents
List of Tables
List of Illustrations
Guide
Pages
Delivering Safety Excellence. Engagement Culture at Every Level
Acknowledgements
Author Biography
List of Figures
Preface
Prologue
Note
Introduction
1 The Funeral
Notes
2 No Support for Safety
3 The Tyranny of the Urgent
4 No Pay for Safety
Note
5 Weak Culture Miseries
6 Injury Plateau
Limitations of Safety Observation Sampling
Note
7 A Brief Safety History
8 Beyond Accident Reaction
Note
9 Safety Culture Beginnings
Notes
10 More Safety Culture
10.1 Background for Culture Improvement
10.2 Human Interaction Realities
11 Active Resistance
12 Zero Injuries
13 How Long?
13.1 POP Statement
13.2 Action Item Matrix (AIM)
13.3 Workers' Compensation Carrier Claim Processing Procedure
14 World‐Class Safety
Note
15 Watch Out
15.1 Setting Priorities
15.2 Management Reluctance to Be Involved
15.3 Regulatory Audits
15.4 Team Inclusiveness
15.5 The Importance of Good Data and a Solid Improvement Process
15.6 The Need for a Challenging Time Line
15.7 Urgency Followed by Complacency
15.8 Series or Parallel Problem Attack Process
15.9 The Importance of Viable Metrics
Note
16 Moving Forward to Safety Culture Excellence
Note
17 The Critical Safety Steering Team
18 The RIW Process
18.1 Rapid Improvement Workshop Teams
18.2 Delivering a Better Safety Performance
19 Fundamentals That Are a Result of Developing a Culture of Safety Excellence
Note
20 Communication and Recognition
20.1 Encouraging Positive Behavior
Notes
21 Hazard Recognition Is Different than Hazard Control
21.1 The Common Threads
21.2 Overestimating Personal Capabilities
21.3 Complacency – Familiarity with the Task
21.4 Safety Warnings – the Severity of the Outcome
21.5 Voluntary Actions and Being in Control of Them
21.6 Personal Experience with an Outcome
21.7 Cost of Noncompliance
21.8 Overconfidence in the Equipment
21.9 Overconfidence in Protection and Rescue
21.10 Potential Profit and Gain from Action
21.11 Role Models Accepting Risk
Note
22 The Trap of Complacency
Epilogue
A The History of the Continuous Excellence Performance (CEP)/Zero Incident Performance (ZIP) Process
B The Railroad Study by Petersen and Bailey
Using Behavioral Techniques to Improve Safety Program Effectiveness
B.1 MR Study of Safety Program Effectiveness. B.1.1 Phase I – 1979–1983
B.1.2 PHASE II – 1985–1988
B.1.2.1 Study Overview
B.1.2.2 Participants in Study
B.1.2.3 History – Need for Study
B.1.2.4 Three Management Approaches to Safety Programming
B.1.2.5 Philosophies Underlying Three Approaches to Safety Programming
B.1.2.6 Development of the Study Format
B.1.2.7 Assumptions to be Tested
B.1.2.8 Safety Program Activities Survey
B.1.2.9 Involvement of Top Railroad Safety Officers
B.1.2.10 Pilot Survey – Railroads I and II
B.1.2.11 AAR Study Group Analysis
B.1.2.12 Aberdeen Study Group Analysis
B.1.2.13 Further Refinement of the Survey Process
B.1.2.14 Survey Verification Study – Railroads III and IV
B.1.2.15 Description of Analysis Program
B.1.2.16 Analysis and Use of Survey Data by Managements
B.1.2.17 Testing a Human Behavioral Factors Approach
B.1.2.18 Technique to Measure the Effects of the Experimental Program
B.1.2.19 Training Format – Railroads I and II
B.1.2.20 Results of Positive Reinforcement – Railroads I and II
B.1.2.21 Verification of Results on Railroads III and IV
B.1.2.22 Reductions in Unsafe Behaviors
B.1.2.23 Summary of Positive Reinforcement Experimental Results
Impact of Study – Four Railroads. B.2 Railroad I. B.2.1 Background
B.2.2 Impact of Study
B.3 Railroad II. B.3.1 Background
B.3.2 Impact of Study
B.4 Railroad III. B.4.1 Background
B.4.2 Impact of Study
B.5 Railroad IV. B.5.1 Background
B.5.2 Impact of Study
B.5.2.1 Longer Term Use of Positive Reinforcement
B.5.2.2 Study Conclusions and Outcomes
B.5.2.3 A Final Word
Appendix 1: Sample – Chart Used for Analysis on One of the Study Railroads
Appendix 2: Sample – Chart Used for Analysis on One of the Study Railroads
Appendix 3: Sample – Chart Used for Analysis on One of the Study Railroads
Appendix 4: Sample – Chart Used for Analysis on One of the Study Railroads
Appendix 5: Sample – Chart Used for Analysis on One of the Study Railroads
Appendix 6: Total Response – 20 Categories – 4 Railroads
Appendix 7: Comparison of Positive Responses by Category – 4 Railroads
Appendix 8: Comparison of Training Results – 4 Railroads
Appendix 9: Positive Recognition Training Outline
Appendix 10: Assessment Questions Used by Supervisors
Appendix 11: Analysis of Responses to Pilot Survey Questionnaires for Railroads I and II. Source: Based on American association of railroads
C The Charter Document
C.1 Process and Objectives (Outcomes)
C.2 Scope and Authority
C.3 Roles and Responsibilities
C.4 Team Member Representation
C.5 Team Safety Department Representative
C.6 Voting and Quorum
C.7 Team Member Service
C.8 Team Leader Service
C.9 Selection of Team Leader
C.10 Meeting Frequency
C.11 Recordkeeping
C.12 Communication
C.13 Team Learning Plan
C.14 Annual Review of POP Statement (Purpose Objective Process) and Team Charter
C.15 Measurables
C.16 Effective Team Norms
C.17 Steering Team Member Training
C.17.1 CIT Facilitator
C.18 Continuous Improvement Team Management
C.19 Continuous Improvement Topics
C.19.1 Continuous Improvement Process Implementation and Sustainability
Index
WILEY END USER LICENSE AGREEMENT
Отрывок из книги
Michael M. Williamsen, PhD
Cobden, IL, USA
.....
Since the 1970s' Occupational Safety and Health Act (OSHA) became law, OSHA has tried a number of approaches in an effort to improve safety in the United States:
Untold billions of dollars spent on OSHA have resulted in minimal improvement in personnel safety numbers. The plateau in safety performance is not improving with a “trouble equals government/business leadership punishment” model. A number of safety professionals and managers committed to safety excellence, who have experiences in various industries in multiple countries and cultures, have settled on a better working model. This approach is more along the lines of a safety culture where “trouble equals value added assistance.” Subsequently, if the leadership cannot improve performance when given such assistance, their poor performance leads to a change in leadership.
.....