Control Theory Applications for Dynamic Production Systems
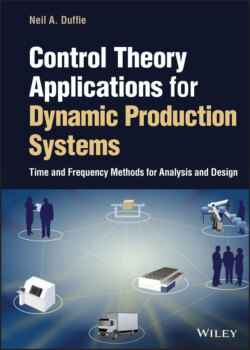
Реклама. ООО «ЛитРес», ИНН: 7719571260.
Оглавление
Neil A. Duffie. Control Theory Applications for Dynamic Production Systems
Control Theory Applications for Dynamic Production Systems. Time and Frequency Methods for Analysis and Design
Contents
List of Figures
List of Tables
Guide
Pages
Preface
Acknowledgments
1 Introduction
1.1 Control System Engineering Software
References
Notes
2 Continuous-Time and Discrete-Time Modeling of Production Systems
2.1 Continuous-Time Models of Components of Production Systems
Example 2.1 Continuous-Time Model of a Production Work System with Disturbances
Program 2.1 WIP response calculated using solution of differential equation
Example 2.2 Continuous-Time Model of Backlog Regulation in the Presence of Rush Orders and Canceled Orders
Example 2.3 Continuous-Time Model of Mixture Temperature Regulation using a Heater
2.2 Discrete-Time Models of Components of Production Systems
Example 2.4 Discrete-Time Model of a Production Work System with Disturbances
Program 2.2 WIP Response calculated recursively using difference equation
Example 2.5 Discrete-Time Model of Planned Lead Time Decision-Making
Example 2.6 Exponential Filter for Number of Production Workers to Assign to a Product
2.3 Delay
Example 2.7 Continuous-Time Model of Delay in a Production System
Example 2.8 Discrete-Time Model of Assignment of Production Workers with Delay
2.4 Model Linearization
2.4.1 Linearization Using Taylor Series Expansion – One Independent Variable
Example 2.9 Production System Lead Time when WIP Is Constant and Capacity Is Variable
2.4.2 Linearization Using Taylor Series Expansion – Multiple Independent Variables
Example 2.10 Production System Lead Time when WIP and Capacity are Variable
2.4.3 Piecewise Approximation
Example 2.11 Piecewise Approximation of a Logistic Operating Curve
2.5 Summary
Notes
3 Transfer Functions and Block Diagrams
3.1 Laplace Transform
Example 3.1 Laplace Transform of a Unit Step Function
Example 3.2 Laplace Transform of an Exponential Function of Time
Example 3.3 Laplace Transform of a Decaying Sinusoidal Function
3.2 Properties of the Laplace Transform
3.2.1 Laplace Transform of a Function of Time Multiplied by a Constant
3.2.2 Laplace Transform of the Sum of Two Functions of Time
3.2.3 Laplace Transform of the First Derivative of a Function of Time
3.2.4 Laplace Transform of Higher Derivatives of a Function of Time Function
3.2.5 Laplace Transform of Function with Time Delay
3.3 Continuous-Time Transfer Functions
Example 3.4 Continuous-Time Transfer Function for WIP in a Production System
Example 3.5 Continuous-Time Transfer Function for Order Release Rate Decision-Making
Example 3.6 Continuous-Time Transfer Function for Two-company Production System with Delays
Example 3.7 Transfer Function of First-Order Continuous-Time Mixture Heating with Delay
Program 3.1 Creating a continuous-time transfer function variable with delay
Program 3.2 Alternative method for creating a continuous-time transfer function variable
3.4 Z Transform
Example 3.8 Z Transform of a Unit Step Sequence
Example 3.9 Z Transform of an Exponential Sequence
Example 3.10 Z Transform of a Decaying Sinusoidal Sequence
3.5 Properties of the Z Transform
3.5.1 Z Transform of a Sequence Multiplied by a Constant
3.5.2 Z Transform of the Sum of Two Sequences
3.5.3 Z Transform of Time Delay dT
3.5.4 Z Transform of a Difference Equation
3.6 Discrete-Time Transfer Functions
Example 3.11 Positive and Negative Powers of z
Example 3.12 Discrete-Time Transfer Function Relating WIP to Work Input Rate
Example 3.13 Discrete-Time Transfer Function with Delay Relating Permanent Worker Capacity to Demand
Program 3.3 Creating a discrete-time transfer function variable
Program 3.4 Alternative method for creating a discrete-time transfer function variable
3.7 Block Diagrams
Example 3.14 Block Diagram for Work In Progress in a Production Work System
Example 3.15 Block Diagram for Adjusting Capacity of Cross-Trained and Permanent Workers
3.8 Transfer Function Algebra
3.8.1 Series Relationships
Example 3.16 Discrete-Time Transfer Functions in Series
Program 3.5 Combining discrete-time transfer functions in series
3.8.2 Parallel Relationships
Example 3.17 Continuous-Time Transfer Functions in Parallel
Program 3.6 Combining continuous-time transfer functions in parallel
3.8.3 Closed-Loop Relationships
Example 3.18 Closed-Loop Transfer Function for Continuous-Time Capacity Adjustment
Example 3.19 Closed-Loop Transfer Function for Discrete-Time Control of Actuator Position
Program 3.7 Calculation of closed-loop transfer function
3.8.4 Transfer Functions of Production Systems with Multiple Inputs and Outputs
Example 3.20 Closed-Loop Continuous-Time Transfer Functions for Backlog Regulation
Example 3.21 Closed-Loop Discrete-Time Transfer Functions for Pressing Operation Control
3.8.5 Matrices of Transfer Functions
Example 3.22 Matrix of Continuous-Time Transfer Functions Modeling Warehouse with Two Inputs and One Output
Program 3.8 Creation of continuous-time transfer function matrix
Example 3.23 Matrix of Discrete-Time Transfer Functions Modeling Closed-Loop Control of a Pressing Operation
3.8.6 Factors of Transfer Function Numerator and Denominator
Example 3.24 Factored Continuous-Time Transfer Function
Example 3.25 Factored Discrete-Time Transfer Function
Program 3.9 Factoring a discrete-time transfer function
3.8.7 Canceling Common Factors in a Transfer Function
Example 3.26 Common Factors in a Continuous-Time Transfer Function
Program 3.10 Canceling common factors in a continuous-time transfer function
3.8.8 Padé Approximation of Continuous-Time Delay
Example 3.27 Substitution of Padé Approximation for Continuous-Time Delay
Program 3.11 Padé approximation of continuous-time delay
3.8.9 Absorption of Discrete Time Delay
Example 3.28 Absorption of Delay in a Discrete-Time Transfer Function
Program 3.12 Absorption of delay in a discrete-time transfer function
3.9 Production Systems with Continuous-Time and Discrete-Time Components
3.9.1 Transfer Function of a Zero-Order Hold (ZOH)
3.9.2 Discrete-Time Transfer Function Representing Continuous-Time Components Preceded by a Hold and Followed by a Sampler
Example 3.29 Discrete-Time Model of WIP Reported after Delay
Program 3.13 Discrete-time transfer function representing ZOH, accumulation of work, delay and WIP sampler
Example 3.30 Discrete-Time Model of Mixture Temperature Regulation
Program 3.14 Discrete-time transfer function representing ZOH, amplifier, mixture heating, and temperature measurement
3.10 Potential Problems in Numerical Computations Using Transfer Functions
Example 3.31 Numerical Inaccuracies in Addition of Transfer Functions
Program 3.15 Approaches for summing transfer function variables
3.11 Summary
Notes
4 Fundamental Dynamic Characteristics and Time Response
4.1 Obtaining Fundamental Dynamic Characteristics from Transfer Functions
4.1.1 Characteristic Equation
4.1.2 Fundamental Continuous-Time Dynamic Characteristics
Example 4.1 Effect of Time Constant on Step Response of a First-Order Continuous-Time Production System or Component
Example 4.2 Effect of Damping Ratio and Natural Frequency on Step Response of a Second-Order Continuous-Time Production System or Component
4.1.3 Continuous-Time Stability Criterion
Example 4.3 Relationship Between Proportional Decision-Rule Parameter and Stability of a Continuous-Time First-Order Production System
Example 4.4 Relationship Between Proportional Decision-Rule Parameter and Stability of a Continuous-Time Second-Order Production System
Example 4.5 Stability of a Production System with Continuous-Time Capacity Adjustment with Delay
Program 4.1 Calculation of fundamental dynamic characteristics of production system with continuous-time capacity adjustment and delay
4.1.4 Fundamental Discrete-Time Dynamic Characteristics
Example 4.6 Effect of Time Constant on Step Response of a First-Order Discrete-Time Production System or Component
Example 4.7 Effect of Damping Ratio and Natural Frequency on Step Response of a Second-Order Discrete-Time Production System or Component
4.1.5 Discrete-Time Stability Criterion
Example 4.8 Relationship Between Proportional Decision-Rule Parameter and Stability of a Discrete-Time First-Order Production System
Example 4.9 Stability of Discrete-Time Actuator Position Control
Program 4.2 Calculation of discrete-time dynamic characteristics
4.2 Characteristics of Time Response
4.2.1 Calculation of Time Response
Example 4.10 Response of Continuous-Time Capacity Adjustment to a Unit Step in Work Input
Program 4.3 Calculation of continuous-time step response
Example 4.11 Response of Discrete-Time Capacity Adjustment to a Unit Step in Work Input
Program 4.4 Calculation of discrete-time step response
Example 4.12 Response of Discrete-Time Actuator Position Control to Constant Velocity Command
Program 4.5 Calculation of response to given input function of time
4.2.2 Step Response Characteristics
Example 4.13 Characteristics of Step Response of Continuous-Time Capacity Adjustment
Program 4.6 Calculation of step response characteristics
Example 4.14 Step Response Characteristics of Discrete-Time Temperature Regulation
Program 4.7 Calculation of step response characteristics of discrete-time temperature regulation
Example 4.15 Step Response Characteristics of a System with Two Time Constants
4.3 Summary
Notes
5 Frequency Response
5.1 Frequency Response of Continuous-Time Systems
5.1.1 Frequency Response of Integrating Continuous-Time Production Systems or Components
Example 5.1 Frequency Response of Backlog in a Production System
Program 5.1 Calculation of frequency response of backlog
5.1.2 Frequency Response of 1st-order Continuous-Time Production Systems or Components
Example 5.2 Frequency Response of Continuous-Time Capacity Adjustment
Program 5.2 Calculation of capacity adjustment frequency response
5.1.3 Frequency Response of 2nd-order Continuous-Time Production Systems or Components
Example 5.3 Frequency Response of Mixture Temperature Regulation
Program 5.3 Frequency response of mixture temperature regulation
5.1.4 Frequency Response of Delay in Continuous-Time Production Systems or Components
Example 5.4 Frequency Response of Delay in a 2-Company Production System
Program 5.4 Calculation of frequency response of delay
5.2 Frequency Response of Discrete-Time Systems
5.2.1 Frequency Response of Discrete-Time Integrating Production Systems or Components
Example 5.5 Frequency Response of Warehouse Inventory
Program 5.5 Frequency response of discrete-time warehouse inventory
5.2.2 Frequency Response of Discrete-Time 1st-Order Production Systems or Components
Example 5.6 Discrete-Time Frequency Response of Capacity Provided by Permanent Workers
Program 5.6 Calculation of frequency response of permanent and cross-trained worker capacity adjustments
5.2.3 Aliasing Errors
5.3 Frequency Response Characteristics
5.3.1 Zero-Frequency Magnitude (DC Gain) and Bandwidth
Example 5.7 Zero-Frequency Magnitude and Bandwidth
Program 5.7 Calculation of zero-frequency magnitude and bandwidth
5.3.2 Magnitude (Gain) Margin and Phase Margin
Example 5.8 Open-Loop Magnitude Margin and Phase Margin of Capacity Adjustment
Program 5.8 Calculation of magnitude margin and phase margin
5.4 Summary
Notes
6 Design of Decision-Making for Closed-Loop Production Systems
6.1 Basic Types of Continuous-Time Control
6.1.1 Continuous-Time Proportional Control
6.1.2 Continuous-Time Proportional Plus Derivative Control
6.1.3 Continuous-Time Integral Control
6.1.4 Continuous-Time Proportional Plus Integral Control
6.2 Basic Types of Discrete-Time Control
6.2.1 Discrete-Time Proportional Control
6.2.2 Discrete-Time Proportional Plus Derivative Control
6.2.3 Discrete-Time Integral Control
6.2.4 Discrete-Time Proportional Plus Integral Control
6.3 Control Design Using Time Response
Example 6.1 Time Response Design of Continuous-Time Integral Control of Production Using Metal Forming
Program 6.1 Calculation of settling times and step response for continuous-time integral control of production using metal forming
Example 6.2 Time Response Design of Discrete-Time Proportional Control of Actuator Position
Program 6.2 Proportional discrete-time control of actuator position
Example 6.3 Time Response Design of Discrete-Time Proportional Plus Derivative Control of Actuator Position
Program 6.3 Calculation of settling time for proportional plus derivative discrete-time control of actuator position
6.4 Direct Design of Decision-Making
Example 6.4 Direct Design for Settling Time of Discrete-Time Integral Control of Production Using Metal Forming
Program 6.4 Calculation of parameter Ki for discrete-time integral control of production using metal forming
Example 6.5 Direct Design for Dead-Beat Response of Discrete-Time Integral Control of Production Using Metal Forming
Example 6.6 Direct Design of Damping Ratio and Settling Time for Continuous-Time Proportional Plus Integral Regulation of Mixture Temperature
Example 6.7 Direct Design of Time Constant Cancellation for Continuous-Time Integral-Lead Regulation of Mixture Temperature
6.4.1 Model Simplification by Eliminating Small Time Constants and Delays
Example 6.8 Simplified Design of Closed-loop Production System with WIP and Backlog Regulation
Program 6.5 Calculation of proportional control parameter for backlog regulation using simplified model
6.5 Design Using Frequency Response
Design Guideline 1 High Open-Loop Frequency Response Magnitude at Relatively Low Frequencies
Design Guideline 2 Low Open-Loop Frequency Response Magnitude at Relatively High Frequencies
Design Guideline 3 Relationship Between Open-Loop Phase Margin and Closed-Loop Damping Ratio
Design Guideline 4 Open-Loop Frequency Response Magnitude in the Vicinity of Frequency ωcp
Design Guideline 5 Relationship Between Closed-Loop Bandwidth, Open-Loop Phase Margin, and Frequency ωcp
6.5.1 Using the Frequency Response Guidelines to Design Decision-Making
Example 6.9 Frequency Response Design of Continuous-Time Control of Production Using Metal Forming
Program 6.6 Calculation of continuous-time integral control parameter for production using metal forming
Example 6.10 Frequency Response Design of Proportional Control for Discrete-Time Production System with Delay Using Phase Margin
Program 6.7 Calculate proportional control parameter using phase margin for discrete-time production system with delay
Example 6.11 Frequency Response Design of Discrete-Time Integral-Lead Control for Mixture Heating with Delay
Program 6.8 Calculation of discrete-time integral-lead control for mixture heating with delay
6.6 Closed-Loop Decision-Making Topologies
6.6.1 PID Control
Example 6.12 Equivalent Discrete-Time PID Control
6.6.2 Decision-Making Components in the Feedback Path
Example 6.13 Discrete-Time Lead Control in the Feedback Path
Program 6.9 Calculation of response with lead control in forward and feedback paths
6.6.3 Cascade Control
Example 6.14 Cascade Discrete-Time Control of Force in a Pressing Operation
Program 6.10 Calculate force and position for pressing operation with cascade control
6.6.4 Feedforward Control
Example 6.15 Discrete-Time Regulation of Lead Time With Feedforward Decision-Making
Example 6.16 Discrete-Time Feedforward Control of Force in a Pressing Operation
Program 6.11 Calculation of pressing force with discrete-time feedforward control
6.6.5 Circumventing Time Delay Using a Smith Predictor Topology
Example 6.17 Circumventing Delay in Discrete-Time Regulation of Lead Time Using Work Output Error and a Smith Predictor Topology
Program 6.12 Calculation of response of discrete-time integral-lead control with Smith Predictor topology
6.7 Sensitivity to Parameter Variations
Example 6.18 Sensitivity of Closed-Loop Time Constant to Variation in Production Using Metal Forming Parameter K m
Program 6.13 Calculation of sensitivity of closed-loop time contant to production parameter Km
6.8 Summary
Notes
7 Application Examples
7.1 Potential Impact of Digitalization on Improving Recovery Time in Replanning by Reducing Delays
Program 7.1 Calculation of result of reducing delays in replanning cycle
7.2 Adjustment of Steel Coil Deliveries in a Production Network with Inventory Information Sharing
Program 7.2 Calculation of galvanizing line inventory frequency response
7.3 Effect of Order Flow Information Sharing on the Dynamic Behavior of a Production Network
Program 7.3 Calculation of fundamental dynamic characteristics and time response of a production network without and with order flow information sharing
7.4 Adjustment of Cross-Trained and Permanent Worker Capacity
Program 7.4 Adjustment of permanent and cross-trained worker capacity
7.5 Closed-Loop, Multi-Rate Production System with Different Adjustment Periods for WIP and Backlog Regulation
Program 7.5 Calculation of fundamental dynamic properties and time response for a production system with backlog and WIP Regulation and two different adjustment periods
7.6 Summary
References
Notes
Bibliography
Index
WILEY END USER LICENSE AGREEMENT
Отрывок из книги
Neil A. DuffieUniversity of WisconsinMadison, Wisconsin
This book was written for a course entitled Smart Manufacturing at the University of Wisconsin-Madison, taught for graduate students working in industry. It has been heavily influenced by two decades of industry-oriented research, mainly in collaboration with colleagues in Germany, on control theory applications in analysis and design of the dynamic behavior of production systems. Motivated by this experience, the material in this book has been selected to
.....
Figure 2.9 Response of change in planned lead time to lateness in order completion.
The exponential filter shown in shown in Figure 2.10 is used in a component of a production system to make periodic decisions regarding the workforce that should be assigned to a product when there are fluctuations in demand for the product. The exponential filter has a weighting parameter 0 < α ≤ 1 that determines how significantly the amplitudes of higher-frequency fluctuations in number of workers are reduced with respect to the amplitudes of fluctuations in demand. This reduction is important because making rapid, larger amplitude changes in the number of workers is likely to be costly and logistically difficult.
.....