Engineering Physics of High-Temperature Materials
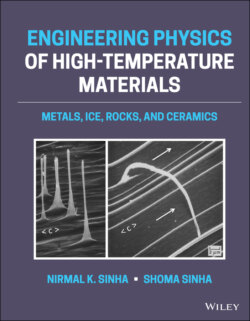
Реклама. ООО «ЛитРес», ИНН: 7719571260.
Оглавление
Nirmal K. Sinha. Engineering Physics of High-Temperature Materials
Table of Contents
List of Tables
List of Illustrations
Guide
Pages
Engineering Physics of High‐Temperature Materials. Metals, Ice, Rocks, and Ceramics
Acknowledgments
Engineering Physics of High‐Temperature Materials. Preface
1 Importance of a Unified Model of High‐Temperature Material Behavior. CHAPTER MENU
1.1 The World's Kitchens – The Innovation Centers for Materials Development
Trinity of Fire
Trinity of Civilization
1.1.1 Defining High Temperature Based on Cracking Characteristics
Trinity of Cracks
1.2 Trinities of Earth's Structure and Cryosphere
1.2.1 Trinity of Earth's Structure. Trinity of Earth's Structure
1.2.2 Trinity of Earth's Cryospheric Regions
Trinity of Earth's Cryosphere
1.3 Earth's Natural Materials (Rocks and Ice)
1.3.1 Ice: A High‐Temperature Material
1.3.2 Ice: An Analog to Understand High‐Temperature Properties of Solids
1.4 Rationalization of Temperature: Low and High
1.5 Deglaciation and Earth's Response
Sea‐Level Change
Uses of Sea‐Level Changes
1.6 High‐Temperature Deformation: Time Dependency. 1.6.1 Issues with Terminology: Elastic, Plastic, and Viscous Deformation
1.6.2 Elastic, Delayed Elastic, and Viscous Deformation
Trinity of Strain
Creep Trinity
1.7 Strength of Materials
1.8 Paradigm Shifts
1.8.1 Paradigm Shift in Experimental Approach
1.8.2 Breaking Tradition for Creep Testing
1.8.3 Exemplification of the Novel Approach
1.8.4 Romanticism for a Constant‐Structure Creep Test
References
2 Nature of Crystalline Substances for Engineering Applications. CHAPTER MENU
Trinity of Properties
2.1 Basic Materials Classification. Trinity of Classification
Trinity of States
2.2 Solid‐state Materials
2.2.1 Structure of Crystalline Solids
Trinity of Crystal Structure
2.2.2 Structure of Amorphous Solids
Trinity of Glass Structure Models
2.3 General Physical Principles. 2.3.1 Solidification of Materials
2.3.2 Phase Diagrams
2.3.3 Crystal Imperfections
2.3.3.1 Point Defects
2.3.3.2 Line Defects/Dislocations
2.3.3.3 Planar Defects
2.3.3.4 Intragranular Precipitates
Trinity of Precipitate Classification
2.3.3.5 Boundary Defects
2.3.3.6 Bulk or Volume Defects
2.4 Glass and Glassy Phase
2.4.1 Glass Transition
2.4.2 Structure of Real Glass
2.4.3 Composition of Standard Glass
2.4.4 Thermal Tempering
2.4.5 Material Characteristics
2.5 Rocks: The Most Abundant Natural Polycrystalline Material. Trinity of Rocks
2.5.1 Sedimentary Rocks
2.5.2 Metamorphic Rocks
2.5.3 Igneous Rocks
2.6 Ice: The Second Most Abundant Natural Polycrystalline Material
2.7 Ceramics
2.8 Metals and Alloys
2.8.1 Iron‐base Alloys
Trinity of Iron Phases
2.8.2 Nickel‐base Alloys
2.8.3 Titanium‐base Alloys
2.8.4 Mechanical Metallurgy
2.9 Classification of Solids Based on Mechanical Response at High Temperatures
Trinity of High‐Temperature Deformation Mechanisms
References
3 Forensic Physical Materialogy
3.1 Introduction
3.1.1 Material Characterization
3.2 Polycrystalline Solids and Crystal Defects
3.2.1 Etch‐Pitting Technique – A Powerful Tool
3.3 Structure and Texture of Natural Hexagonal Ice, Ih
3.4 Section Preparation for Microstructural Analysis
3.4.1 Thin Sectioning of Ice
3.4.2 Large 300 mm Diameter Polariscope
3.4.3 Sectioning for Forensic Analysis of Compression Failure
3.5 Etching of Prepared Section Surfaces
3.5.1 Surface Etching
3.6 Sublimation Etch Pits in Ice, Ih
3.7 Etch‐Pitting Technique for Dislocations
3.7.1 Simultaneous Etching and Replicating
3.7.2 Etching Processes and Their Applications
3.8 Chemical Etching and Replicating of Ice Surfaces
3.9 Displaying Dislocation Climb by Etching
3.10 Thermal Etching: An Unexploited Materialogy Tool
References
4 Test Techniques and Test Systems. CHAPTER MENU
4.1 On the Strength of Materials and Test Techniques
4.1.1 Issues with Stress–Strain (σ–ε) Diagrams at High Temperatures
4.1.2 Fundamentals of Displacement Rate, Strain Rate, and Stress Rate Tests
4.1.3 Time – An Important Parameter at High Temperatures
4.2 Static Modulus and Dynamic Elastic Modulus
4.3 Thermal Expansion Over a Wide Range of Temperature
4.4 Creep and Fracture Strength
4.5 Bending Tests
4.5.1 Three‐Point Bending
4.5.2 Four‐Point Bending
4.5.3 Cantilever Beam Bending
4.6 Compression Tests – Uniaxial, Biaxial, and Triaxial
4.6.1 Uniaxial Compression Tests
4.6.2 Biaxial or Confined Compression Tests
4.6.3 Triaxial or Multiaxial Compression and Tension Tests
4.7 Tensile and/or Compression Test System
4.7.1 Tests with Single Top‐Lever Loading Frame
4.7.2 Universal Testing Machine and Systems: Introduction to SRRT Methodology
Box
4.8 Stress Relaxation Tests (SRTs)
4.8.1 Necessity for Stress Relaxation Properties
4.8.2 Basic Principle of SRTs
4.9 Cyclic Fatigue
4.9.1 Low‐Cycle Fatigue (LCF) and High‐Cycle Fatigue (HCF Tests)
4.9.2 Uncharted Characteristics of Delayed Elasticity in Cyclic Loading
4.9.3 Cyclic Loading of Snow and Thermal Cycling on Asphalt Concrete
4.10 Acoustic Emission (AE) and/or Microseismic Activity (MA)
4.11 Tempering of Structural and Automotive Glasses
4.12 Specimen Size and Geometry: Depending on Material Grain Structure
4.13 In Situ Borehole Tests: Inspirations from Rock Mechanics
References
5 Creep Fundamentals. CHAPTER MENU
5.1 Overview
5.2 On Rheology and Rheological Terminology
5.3 Forms of Creep and Deformation Maps. 5.3.1 Generalization for Polycrystalline Materials
5.3.2 Nabarro–Herring Creep
5.3.3 Coble Creep
5.3.4 Harper–Dorn Creep
5.3.5 Ashby–Verrall Creep
5.3.6 Deformation Mechanism Maps
5.4 Grain‐Boundary Shearing or Sliding
5.5 Creep Curves – Classical Primary, Secondary, and Tertiary Descriptions
5.5.1 Elasticity and Annealing of Glass
5.5.2 Phenomenological Rheology of Glass
5.5.3 Normalized Creep – Another Presentation of Rheology of Glass
5.6 Phenomenology of Primary Creep in Metals, Ceramics, and Rocks
5.7 Primary Creep in Ice: Launching SRRT Technique and EDEV Model
5.8 Grain‐Boundary Shearing (gbs) and Grain‐Size Dependent Delayed Elasticity
5.9 Generalization of EDEV Model: Introduction of Grain‐Size Effect
5.10 Logarithmic Primary Creep: An Alternative Form of the EDEV Model
5.11 Shifting Paradigms: Emphasizing Primary Creep of Polycrystalline Materials
5.12 SRRT for Primary Creep and EDEV Model of a Titanium‐Base Superalloy (Ti‐6246)
5.13 SRRT for Primary Creep and EDEV Model for a Nickel‐Base Superalloy (Waspaloy)
5.14 SRRT for Primary Creep of a Nickel‐Rich Iron‐Base Alloy (Discaloy)
5.15 SRRTs for Primary Creep and EDEV Model of a Nickel‐Base Superalloy (IN‐738LC)
5.16 EDEV‐Based Strain‐Rate Sensitivity of High‐Temperature Yield Strength
5.16.1 Constant Strain‐Rate Yield
5.16.2 Yield Strength of Ti‐6246 at 873 K (0.45 Tm)
5.16.3 Yield Strength of Waspaloy at 1005 K (0.62 Tm)
5.17 Single‐Crystal (SX) Superalloy Delayed Elasticity and γ/γ′ Interface Shearing
5.18 Creep, Steady‐State Tertiary Stage, and Elasto–Viscous (EV) Model for Single Crystals
5.19 Creep Fracture and EV Model for CMSX‐10 SXs
5.20 Fracture and Inhomogeneous Deformation
5.21 Dynamic Steady‐State Tertiary Creep of Several Nickel‐Base SXs
5.21.1 MAR‐M‐247 Single Crystal
5.21.2 CMSX‐3 Single Crystal
5.21.3 CMSX‐4 Single Crystal with Rhenium
5.21.4 CMSX‐4 Single Crystal
5.21.5 TMS‐75 Single Crystal
5.21.6 SRR99 Single Crystal
References
6 Phenomenological Creep Failure Models. CHAPTER MENU
6.1 Creep and Creep Failure
6.2 Steady‐State Creep
6.3 Commonly Used Creep Experiments and Strength Tests
6.3.1 Constant Stress and Constant Deformation (CD) Rate Tests
6.3.2 A Short Glimpse of Creep Tests
6.3.3 Power Law for Creep
6.3.4 Larsen and Miller Concept
6.3.5 Monkman and Grant (M‐G) Relationship
6.3.6 Rabotnov–Kachanov Concept for Creep Fracture
6.3.7 Breaking Tradition – θ‐Projection Concept
6.4 Modeling Very Long‐Term Creep Rupture from Short‐Term Tests
6.4.1 Traditional Approaches for Power‐Generation Operations
6.4.2 Captivating and Entrenched Focus on Minimum Creep Rate
6.5 High‐Temperature Low‐Cycle Fatigue (HT‐LCF) and Dwell Fatigue
6.6 Crucial Tests on Rate Sensitivity of High‐Temperature Strength
6.7 Rational Approach Inspired by the Principle of “Hindsight 20/20”
References
7 High‐Temperature Grain‐Boundary Embrittlement and Creep. CHAPTER MENU
7.1 Fracture and Material Failure
Trinity of Fracture
7.1.1 Griffith's Model for Crack Propagation
7.1.2 Crack Nucleation Mechanisms at Low Homologous Temperatures
7.1.3 Acoustic Emissions and Cracks
7.1.4 A Novel Treatment of AE and Cracks in Ice Engineering
7.2 Grain Size Effects on Strength. 7.2.1 Popular Low‐Temperature Concept of Strength
7.2.2 Problems with Estimating Grain Size
7.2.3 Inapplicability of the Hall–Petch Relation at High Temperatures
7.3 Grain‐Boundary Shearing (gbs) Induced Crack Initiation
7.3.1 Groundwork for a High‐Temperature Crack‐Initiation Hypothesis
7.3.2 Gold's Classic Studies on Creep Cracking by Visual Observations
7.3.3 Forensic Microstructural Examinations of First Creep Cracks
7.3.4 First Grain‐Facet‐Sized Cracks and Critical Delayed Elastic Criterion
7.3.5 Critical Time and Stress for Onset of Creep Fracture
7.3.6 Critical Strain for First Cracks (or Fracture Failure)
7.3.7 Apparent Activation Energy for First Cracks and Fracture
7.3.8 Kinetics of Creep Cracking
References
8 Microstructure and Crack‐Enhanced Elasto – Delayed‐Elastic – Viscous Models. CHAPTER MENU
8.1 Physics‐Based Holistic Model Approach
8.1.1 On Transient Creep and the Shape of Creep Curves
8.1.2 On “Limiting Transient Creep Strain” (εT)
8.1.3 On the Traditions of Creep Testing and Shifting Paradigms
8.2 Kinetics of Microcracking and Structural Damage
8.3 Microcrack‐Enhanced EDEV Model
8.4 EDEV‐Based Algorithm for Constant Strain Rate, Encompassing Cracking
8.4.1 EDEV‐Based Stress–Strain Diagrams
8.5 Constant Stress, Crack‐Enhanced Creep: EDEV Predictions
8.5.1 Apparent Brittle–Ductile Transition in Constant Stress Creep
8.5.2 Power‐Law Breakdown for Minimum Creep Rate
8.5.3 Grain‐Size Effects on Creep with Crack Formation
8.5.4 Creep Dilatation in Polycrystalline Columnar‐Grained and Equiaxed Solids
8.5.5 Crack Damage at Minimum Creep Rate and Upper Yield
8.5.6 Strain‐Rate Sensitivity of Initial Deformation, Dilatancy, and Residual Strength
8.6 Cyclic Fatigue
8.6.1 Low‐Cycle Constant Strain Rate Loading
8.6.2 Low‐Cycle, High‐Strain Fatigue: Repeated Constant Load
8.7 Crack Healing or Closure of w‐Type Voids Generating r‐Type Cavities
References
9 Stress Relaxation at High Temperatures. CHAPTER MENU
9.1 The Role of Stress Relaxation Tests at High Temperatures
9.1.1 Traditional SRTs
9.1.2 Phenomenology of Stress Relaxation
9.1.3 Capabilities and Inadequacies of SRT for Creep Estimation
9.1.4 Rationalization of SRT Processes
9.1.5 SRT on Coarse‐Grained Materials
9.1.6 New Approaches for Examining Applicability of SRT for Fine‐Grained Materials
9.1.7 Grain‐Size‐Based Optimization of Initial Strain, ε0, for SRT
9.2 Constitutive Equations without Effect of Grain Size. 9.2.1 Constitutive Equation for Uniaxial Creep at High Temperatures
9.2.2 SR Based on Constitutive Equation
9.2.3 Type‐A Engineering Prediction for SRT
9.2.3.1 Global Strain Rate (GSR) During SRT
9.2.3.2 Apparent Power‐Law Breakdown in GSR
9.2.3.3 Comments on SRT in Bending
9.3 Temperature and Grain‐Size Effects on SR. 9.3.1 EDEV Constitutive Equation Incorporating Grain Size and Temperature
9.3.2 EDEV‐Based SRT Algorithm for Grain‐Size and Temperature Dependency
9.3.3 Lack of Grain‐Size‐Dependent Data on Primary Creep of Engineering Materials
9.4 Forecasting Grain‐Size Effects on SR in Pure Ice Based on EDEV Equation
9.4.1 Basis of Calculation for Ice
9.4.2 Effect of Strain, ε0 (Constant Temperature and Grain Size)
9.4.3 Effect of Temperature (Constant Strain and Grain Size)
9.4.4 Effect of Grain Size (Constant Strain and Temperature)
9.4.5 Strain (ε0) Dependence of Strain Components (Constant Temperature and Grain Size)
9.4.6 Grain‐Size Effect on Strain Components During SRT (Constant Strain and Temperature)
9.4.7 Comments on SRTs Related to Ice and Field Experience
9.5 High‐Temperature Forming, Delayed Spring‐Back, and Grain‐Size Effects on SR in Metals
References
10 Ice Age and Intraglacial Depression and Postglacial Rebound of Earth's Crust. CHAPTER MENU
10.1 Tectonic Plates, Lake Ice, and High‐Temperature Materials: What Is the Connection?
10.2 On Glaciers and Oceanic Ice Cover: Past and Present
10.2.1 Rise of Canada – Postglacial Uplift
10.2.2 Postglacial Adjustments of North America's Landscape
10.3 Dow's Lake Studies
10.3.1 Dow's Lake Ice Sheet: Crowd Load/Unload During Winter of 1985
10.3.2 Swimming Pool Loading Experiment on Dow's Lake Ice in 1986
10.4 Elasto–Delayed‐Elastic (EDE) Theory for Plates
References
11 Plate Tectonics and Polar Sea Ice. CHAPTER MENU
11.1 Retrospective Introduction
11.2 Earth and Plate Tectonics
11.2.1 On Sea Ice: Analog for Tectonic Plates
11.2.2 Trinity of Tectonic Plates
Trinity of Tectonic Plates
11.2.3 Trinity of Tectonic Plate Boundaries
Trinity of Plate Boundaries
11.3 Scale of Observations
11.3.1 Messengers of Earth Below and Sky Above
11.4 Vertical Temperature Profiles of Earth and Ice Sheet
11.5 Time–Temperature Shift Function
11.6 Nonlinear, Grain‐Size‐Dependent Delayed Elasticity (Anelasticity) of Mantle
11.7 Stress Field of Earth's Crust
11.8 Koyna and Warna Dams in India and Reservoir‐Triggered Seismicity (RTS)
11.9 Movement of Tectonic Plates, Indentation, and Fracture
11.10 Looking Forward
References
Index
a
b
c
d
e
f
g
h
i
k
l
m
n
o
p
q
r
s
t
u
v
w
y
z
WILEY END USER LICENSE AGREEMENT
Отрывок из книги
Nirmal K. Sinha
Retired, Institute for Aerospace Research, National Research Council of Canada, Ottawa, Ontario, Canada
.....
The chronology of the development of the three‐term rheological model, called EDEV model, is described in Chapter 5. This model relies on the incorporation of grain‐boundary shearing processes to relate with the delayed elastic phenomenon. A review of the phenomenological aspects of the failure processes at elevated temperatures is presented in Chapter 6. The crucial roles played by the phenomenon of delayed elasticity are examined in depth. Delayed elasticity can be linked to the predictability of the conditions necessary for the onset of grain‐facet‐sized crack formation and the kinetics of microcracking (Chapter 7). This leads to the development of the crack‐enhanced EDEV model that can handle, for example, the strain‐rate sensitivity of strength of polycrystalline solids at high temperatures (Chapter 8). EDEV is a nonlinear constitutive equation for high‐temperature applications. It consists of elastic, delayed elastic, and viscous components corresponding to three micromechanisms: lattice deformation, intergranular shearing/sliding, and intragranular dislocation motion. The model incorporates the predictability of the onset of cracking activity and damage accumulation due to the mechanism(s) of high‐temperature grain‐boundary embrittlement.
Grain facet long cracks develop when a critical grain‐boundary sliding or shearing (gbs) displacement or an equivalent delayed elastic strain is reached. Further damage is given in terms of the excess gbs, displacement over its critical value. As cracks form, they enhance the deformation matrix affecting the overall creep rate, leading to a minimum rate and then tertiary creep. Formulations have been developed in Chapter 8, using this model, for predicting the deformation and cracking activity for conditions of constant strain‐rate strength tests. The theory was tested with published experimental data on the strain‐rate sensitivity of the compressive strength of transversely isotropic, columnar‐grained, pure polycrystalline ice with a load applied in the plane of isotropy. Calculations using material constants were obtained from constant‐stress creep and recovery (SRRT) experiments totally independent of the strength tests. One‐to‐one correspondence of theory and experiments was noted for the dependence of strength, failure strain, and failure time on strain rate. The theory has the capabilities for predicting the popular empirically obtained relations between these quantities, such as the MG relationship. The EDEV theory also points out the limitations of the empirical relations, for example the inapplicability of the empirical power‐law relation between t f and σ f or between ε f and strain rate. It is shown that strain‐rate sensitivity of volumetric dilatation can also be reasonably predicted.
.....