Control of Mechatronic Systems
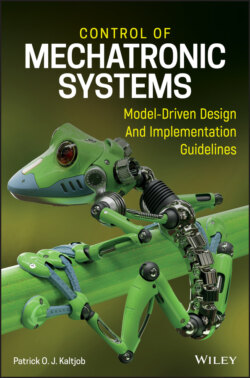
Реклама. ООО «ЛитРес», ИНН: 7719571260.
Оглавление
Patrick O. J. Kaltjob. Control of Mechatronic Systems
Table of Contents
List of Tables
List of Illustrations
Guide
Pages
Control of Mechatronic Systems. Model-Driven Design and Implementation Guidelines
Preface
Acknowledgment
About the Companion Website
1 Introduction to the Control of Mechatronic Systems. 1.1 Introduction
1.2 Description of Mechatronic Systems
Example 1.1
Example 1.2
1.3 Generic Controlled Mechatronic System and Instrumentation Components
1.3.1 The Data Processing and Computing Unit
1.3.2 Data Acquisition and Transmission Units
1.3.3 Electrically-driven Actuating Units
1.3.4 Measuring and Detecting Units
1.3.5 Signal Conditioning Units
1.4 Functions and Examples of Controlled Mechatronic Systems and Processes
Example 1.3
Example 1.4
Example 1.5
Example 1.6
1.5 Controller Design Integration Steps and Implementation Strategies
Exercises and Problems
Bibliography
2 Physics-Based Systems and Processes: Dynamics Modeling. 2.1 Introduction
2.2 Generic Dynamic Modeling Methodology
2.3 Transportation Systems and Processes. 2.3.1 Sea Gantry Crane Handling Process
2.3.1.1 Model 1
2.3.1.2 Model 2
2.3.2 Vertical Elevator System
2.3.3 Hybrid Vehicle Powertrain with Parallel Configuration
2.3.3.1 Motor Driving and Regenerating Model
2.3.3.2 Vehicle Gear Box Model
2.3.3.3 Brake System Model
2.3.4 Driverless Vehicle Longitudinal Dynamics
2.3.5 Automated Segway Transportation Systems
2.4 Biomedical Systems and Processes. 2.4.1 Infant Incubator
2.4.2 Blood Glucose-Insulin Metabolism
2.5 Fluidic and Thermal Systems and Processes. 2.5.1 Mixing Tank
2.5.2 Purified Water Distribution Process
2.5.3 Conveyor Cake Oven
2.5.4 Poultry Scalding and Defeathering Thermal Process
2.6 Chemical Processes. 2.6.1 Crude Oil Distillation Petrochemical Process
2.6.2 Lager Beer Fermentation Tank
2.7 Production Systems and Processes. 2.7.1 Single Axis Drilling System
2.7.2 Cement-Based Pozzolana Portal Scraper
2.7.3 Variable Pitch Wind Turbine Generator System
Exercises and Problems
Bibliography
3 Discrete-Time Modeling and Conversion Methods. 3.1 Introduction
3.2 Digital Signal Processing Preliminaries. 3.2.1 Digital Signal Characterization
Example 3.1
3.2.2 Difference Equation: Discrete-Time Signal Characterization Using Approximation Methods
3.2.2.1 Numerical Approximation Using Forward Difference
3.2.2.2 Numerical Equivalence Using Backward Difference
3.2.2.3 Numerical Equivalence Using Bilinear Transform
Example 3.2 Discretization of a Nonlinear Model
Example 3.3 Comparison of Discrete Equivalences
Example 3.4
Example 3.5
Example 3.6
A Discrete-Time Approximation Method using Zero-Pole Matching Equivalence
3.2.3 Z-Transform and Inverse Z-Transform: Theorems and Properties
Example 3.7
3.2.4 Procedure for Discrete-Time Approximation of the Continuous Process Model
3.2.4.1 Z-Transfer Functions and Block Diagram Manipulation
Example 3.8
Example 3.9
3.2.5 Conversion and Reconstruction of the Continuous Signal: Sampling and Hold Device. 3.2.5.1 Sampler and Hold-Based Process Model
Zero-Order Hold (ZOH)
Example 3.10 Third-Order Process with ZOH
Triangle Hold Equivalent
Time Delay Associated with Hold Equipment
3.2.5.2 Construction Methods of a Continuous Signal from a Data Sequence
Signal Reconstruction Using Linear Interpolation
Signal Construction Using Cubic (Third-Order) Polynomials
Signal Construction Using Three Spline Functions
Example 3.11
Example 3.12 Process Command Data Sequence Interpolation
3.3 Signal Conditioning
Example 3.13
3.4 Signal Conversion Technology
3.4.1 Digital-to-Analog Conversion
Example 3.14
3.4.2 Analog-to-Digital Conversion
Example 3.15
Example 3.16
Example 3.17
Example 3.18
3.5 Data Logging and Processing. 3.5.1 Computer Bus Structure and Applications
Example 3.19
Example 3.20
3.6 Computer Interface and Data Sampling Issues
Example 3.21
Example 3.22 Multiple Sampling Rates
3.6.1 Signal Conversion Time Delay Effects
3.6.1.1 Nyquist Sampling Theorem and Shannon's Interpolation Formula
Oversampling Case
Undersampling (Below the Nyquist Rate)
3.6.2 Estimation of the Minimum Sampling Rate to Be Selected
3.6.2.1 Remarks on Sample Periods
Example 3.23
Exercises and Problems
Bibliography
4 Discrete-Time Analysis Methods. 4.1 Introduction
4.2 Analysis Tools of Discrete-Time Systems and Processes. 4.2.1 Discrete Pole and Zero Location
Example 4.1 Applying the Magnitude and Angle Condition for Root Locus Sketching
Example 4.2
4.2.2 Discrete Frequency Analysis Tools: Fourier Series and Transform (DFT, DTFT, and FFT)
4.2.2.1 Discrete System Frequency Response
4.2.2.2 Sketching Procedure for the Frequency Response of a Discrete System
4.2.2.3 Properties of a Frequency Response
Example 4.3 Bode Plot Diagram for Discrete-Time Systems
4.3 Discrete-Time Controller Specifications
4.3.1 Time Domain Specifications
4.3.2 Frequency Response Specifications
4.4 Discrete-Time Steady-State Error Analysis
4.5 Stability Test for Discrete-Time Systems
4.5.1 Bound-Input Bound-Output (BIBO) Stability Definition
4.5.2 Zero-Input Stability Definition
4.5.3 Bilinear Transformation and the Routh–Hurwitz Criterion
Example 4.4
4.5.4 Jury–Marden Stability Test
4.5.5 Frequency-Based Stability Analysis
4.6 Performance Indices and System Dynamical Analysis
Exercises and Problems
Bibliography
5 Continuous Digital Controller Design. 5.1 Introduction
5.2 Design of Control Algorithms for Continuous Systems and Processes
5.2.1 Direct Design Controller Algorithms
Example 5.1 Deadbeat Controller Design
5.2.2 Discrete PID Controller Algorithms
5.2.2.1 Proportional Control Algorithm
5.2.2.2 Derivative Control Algorithm
5.2.2.3 Integral Control Algorithm
5.2.2.4 PI Control Algorithm
5.2.2.5 PD Control Algorithm
5.2.2.6 Classical PID Controller Algorithm
5.2.2.7 Properties of and Some Remarks on PID Controller Algorithms
5.2.3 PID Controller Gains Design Using a Frequency Response Technique
5.2.3.1 Design Procedure for PID Controller Design
PID Discrete Compensator Design Method
Discrete PI Controller Design (θ<0)
Discrete PD Controller Design (θ>0)
Exact Solution for Discrete PID Controller Design
Example 5.2 PI Controller Design Using a Frequency Response Method
Example 5.3
Remarks on Higher-Order Systems
Example 5.4 PD Controller Design
Example 5.5 Deadbeat and PI Controller System
Example 5.6 PID Controller Design Using Frequency Response
5.2.4 PID Controller Gains Design Using a Root Locus Technique
5.2.4.1 Design Procedures
Lead or Lag Continuous-Based Controller Design Approach
Lead or Lag Discrete Controller Design Approach
Example 5.7 Controller Design Using Root Locus
Design Procedures for Lead-Lag Compensation
Remarks on Compensation Controller Properties
Common Guidelines for PID Family Control Loops
5.2.5 Feedforward Control Methods
5.2.5.1 Command Input Feedforward Control Algorithm
Example 5.8
Example 5.9
5.2.5.2 Disturbance Feedforward Control Algorithm
5.3 Modern Control Topologies
5.3.1 State Feedback PID Control Algorithms
Cascade Controller Design Procedure
Example 5.10 Cross-Coupled Discrete-Time Model of a DC Motor
Example 5.11 Cascade Control and State Control of a DC Motor Using Only Position Feedback
Example 5.12 State-Variable DC Motor Motion Controller Design with Separated Poles
Example 5.13 Controlled DC Motor Using Estimated State Feedback Control
5.3.2 MPC Algorithms
Example 5.14 Blood Glucose Control of Diabetes Type 1 Patient
5.3.3 Open-Loop Position Control Using Stepping Motors
Example 5.15
5.4 Induction Motor Controller Design
5.4.1 Scalar Control (V/f Control)
5.4.1.1 Open-Loop Scalar Control
5.4.1.2 Closed-Loop Scalar Control (Slip Control)
5.4.2 Vector Control
5.4.2.1 Direct Torque Control
5.4.2.2 Speed Control of AC Motors
5.4.2.3 Speed Control of DC Motors
Armature Voltage Control, Va(t)
Field Control (φ)
Armature Resistance Control (Ra)
Exercises and Problems
Bibliography
6 Boolean-Based Modeling and Logic Controller Design. 6.1 Introduction
6.2 Generic Boolean-Based Modeling Methodology
6.2.1 System Operation Description and Functional Analysis
6.2.2 Combinatorial and Sequential Logic Systems
6.2.2.1 Combinational Modeling Tools: Truth Table, SOP, Product of Sums (POS), K-Maps
6.2.2.2 Sequential Modeling Tools: Sequence Table, Switching Theory, and State Diagram
Example 6.1
Example 6.2
Example 6.3
6.3 Production Systems. 6.3.1 Portico Scratcher
6.4 Biomedical Systems. 6.4.1 Robot-Assisted Surgery
6.4.2 Laser Surgery Devices
6.5 Transportation Systems. 6.5.1 Elevator Motion Systems
6.5.2 Fruit-Picker Arm
6.5.3 Driverless Car
6.6 Fail-Safe Design and Interlock Issues
6.6.1 Logic Control Validation (Commissioning)
Exercises and Problems
Bibliography
7 Hybrid Controller Design. 7.1 Introduction
7.2 Requirements for Monitoring and Control of Hybrid Systems
7.2.1 Requirements for Hybrid Control System Design
7.2.2 Requirements for Operations Monitoring System Design
7.2.3 Process Interlock Design Requirements
7.3 Design Methodology for Monitoring and Control Systems
7.4 Examples of Hybrid Control and Case Studies
7.4.1 Elevator Motion System
7.4.2 Bottle-Cleaning Process
7.4.3 Cement-Drying Process
Exercises and Problems
Bibliography
8 Mechatronics Instrumentation: Actuators and Sensors. 8.1 Introduction
8.2 Actuators in Mechatronics
8.3 Electromechanical Actuating Systems
8.3.1 Solenoids
8.3.2 Digital Binary Actuators
Example 8.1
8.3.3 DC Motors
8.3.4 AC Motors
8.3.5 Stepping Motors
8.3.6 Transmission Mechanical Variables
8.4 Electro-Fluidic Actuating Systems
8.4.1 Electric Motorized Pumps
8.4.2 Electric-Driven Cylinders
8.4.3 Electrovalves
8.5 Electrothermal Actuating Systems
8.6 Sensors in Mechatronics
8.6.1 Measurement Instruments
8.6.1.1 Relative Position (Distance)
8.6.1.2 Angular Position Measurement Using an Encoder and a Resolver
8.6.1.3 Velocity Measurement
8.6.1.4 Acceleration Measurement
8.6.1.5 Force Measurement
8.6.1.6 Torque Measurement
8.6.1.7 Flow Measurement
8.6.1.8 Pressure Measurement
8.6.1.9 Liquid-Level Measurement
Example 8.2
8.6.1.10 Radio Frequency-Based Level Measurement
8.6.1.11 Smart and Nano Sensors
8.6.2 Detection Instruments
8.6.2.1 Electromechanical Limit Switches
8.6.2.2 Photoelectric Sensors
8.6.2.3 RFID-Based Tracking and Detection
8.6.2.4 Binary Devices: Pressure Switches and Vacuum Switches
Exercises and Problems
Bibliography
A Stochastic Modeling
A.1 Discrete Process Model State-Space Form
A.2 Auto-Regressive Model with an eXogenous Input: ARX Model Structure
A.3 The Auto-Regressive Model – AR Model Structure
A.4 The Moving Average Model – MA Model Structure
A.5 The Auto-Regressive Moving Average Model – ARMA Model Structure
A.6 The Auto-Regressive Moving Average with eXogenous Input Model – ARMAX Model Structure
A.7 Selection of Model Order and Delay
A.8 Parameter Estimation Methods
A.9 LS Estimation Methods
A.10 RLS Estimation Methods
A.11 Model Validation
A.12 Prediction Error Analysis Methods
A.13 Estimation of Confidence Intervals for Parameters
A.14 Checking for I/O Consistency for Different Models
B Step Response Modeling
C Z-Transform Tables
D Boolean Algebra, Bus Drivers, and Logic Gates
D.1 Some Logic Gates, Flip-Flops, and Drivers
D.2 Other Logic Devices: Drivers and Bus Drivers
D.3 Gated Latch
D.4 D-Type (Delay-Flip-Flop)
D.5 Register or Buffer
D.6 Adder
E Solid-State Devices and Power Electronics
E.1 Power Diodes
E.2 Diode–Transistor Logic (DTL)
E.3 Power Transistors
E.4 Resistor–Transistor Logic (RTL)
E.5 Transistor–Transistor Logic (TTL)
E.6 Metal Oxide Semiconductor FET (MOSFET)
E.7 Thyristors
Index
WILEY END USER LICENSE AGREEMENT
Отрывок из книги
Vice President and Editorial Director: Amanda L. Miller
Acquisitions Editors: Eric Willner and Anne Hunt
.....
Mechatronic systems and processes have built-in intelligence through either their advanced information processing systems such as multifunctional control systems or intelligent electromechanical systems (including thermal, fluid, and mechanical processes) such as power-efficient multi-axis actuation with motion precision and detection features or miniaturized smart devices with embedded information processing capabilities. The resulting controlled mechatronic systems and processes aim to achieve various objectives: synchronize, control and sequence process operations, or detect and monitor process status.
Table 1.1 presents some typical process control objectives and their corresponding control functions along with some illustrative examples.
.....