Adhesives for Wood and Lignocellulosic Materials
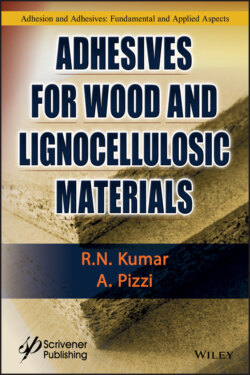
Реклама. ООО «ЛитРес», ИНН: 7719571260.
Оглавление
R. N. Kumar. Adhesives for Wood and Lignocellulosic Materials
Contents
Guide
List of Illustrations
List of Tables
Pages
Adhesives for Wood and Lignocellulosic Materials
Preface
References
Chapter 1 Wood as a Unique Adherend. 1.1 Introduction
1.2 Wood, An Adherend with Hierarchical Structure
1.3 Details of Structural Hierarchy in Wood
1.3.1 Physical Structure
1.3.1.1 Growth Rings and Ring-Porous and Diffuse-Porous Wood
1.3.1.2 Wood Cells
1.3.1.3 Organization of Cell Walls in Wood
1.4 Chemical Composition
1.4.1 Cellulose
1.4.2 Hemicelluloses
1.4.3 Lignin
1.4.3.1 Lignin Isolation
1.4.3.2 Functional Groups in Lignin
1.4.3.3 Evidences for the Phenylpropane Units as Building Blocks of Lignin
1.4.3.4 Dehydrogenation Polymer (DHP)
1.5 Influence of Hierarchical Structure of Wood on Wood–Adhesive Interaction
1.5.1 Penetration
1.5.1.1 Penetration in Different Size Scales
1.5.2 Other Wood-Related and Process-Related Factors
1.6 Effect of Hierarchical Structure of Wood on Adhesive Penetration
1.7 Wood Factors Affecting Penetration
1.8 Influence of Resin Type and Formulation on Penetration
1.9 Effect of Processing Parameters on Penetration
References
Chapter 2 Fundamentals of Adhesion. 2.1 Introduction
2.2 Definitions
2.2.1 Adhesion
2.2.2 Cohesion
2.2.3 Adhesive
2.2.4 Adherend
2.2.5 Bonding
2.2.6 Adhesive, Assembly
2.3 Mechanism of Adhesion
2.3.1 Specific Adhesion
2.3.1.1 London Dispersion Force
2.3.1.2 Dipole-Dipole Interaction
2.3.1.3 Dipole–Induced-Dipole Interaction
2.3.1.4 Ion–Dipole Interaction
2.3.1.5 Hydrogen Bonds
2.3.1.6 Ionic Bonds
2.3.1.7 Chemical Bonds
2.4 Theories of Adhesion
2.4.1 Mechanical Theory
2.4.1.1 lllustration of Mechanical Adhesion for Wood
2.5 Electronic Theory
2.6 Diffusion Theory
2.7 Adsorption/Covalent Bond Theory
2.8 Adhesion Interactions as a Function of Length Scale
2.9 Wetting of the Substrate by the Adhesive
2.10 Equilibrium Contact Angle
2.11 Thermodynamic Work of Adhesion
2.12 Spreading Coefficient
2.13 Zisman’s Rectilinear Relationship—Zisman’s Plots and Critical Surface Tension of a Solid
2.14 Effect of Surface Roughness on Contact Angle
2.15 Weak Boundary Layer Theory
2.16 Measurement of the Wetting Parameters for Wood Substrate
2.16.1 Some Results on Surface Energy of Wood
2.17 Covalent Bond Formation
References
Chapter 3 Urea–Formaldehyde Resins. 3.1 Introduction
3.2 Historical Review of UF Resins (Plastic Historical Society) [3]
3.3 Reaction between Urea and Formaldehyde
3.4 Reaction Sequence
3.5 Manufacture of UF Resin
3.6 Chemistry of Reaction—Conventional Process (Alkaline–Acid Process/Three-Step Process)
3.6.1 First Stage—Reaction under Alkaline Conditions
3.6.1.1 Reaction Mechanism [14]
3.6.2 Second-Stage Condensation Reaction under Acid Conditions: Chain Extension
3.6.2.1 Reaction Chemistry
3.6.2.2 Reaction Mechanism
3.6.3 Third Stage—Neutralization and Addition of Second Urea
3.6.3.1 Reactions Involving Migration of Hydroxymethyl Groups
3.7 Composition of the Commercial UF Resins
3.7.1 Monomeric Species
3.7.2 Oligomeric Species
3.7.3 General Structure of Commercial UF Resins
3.7.4 Urons
3.8 Reactions of UF during Storage
3.9 Reaction Parameters in the Production of Amino Resins (General)
3.10 Four-Step Process for Low Formaldehyde Emission
3.11 Curing of UF Resins
3.11.1 Ammonium Salts
3.12 Cross-Linked Structure
3.13 Triazinone for Curing the UF Resin
3.14 Distinguishing Feature of UF from other Synthetic Resin Adhesives such as MUF and PF
3.15 Other Curing Agents
3.16 Protic Ionic Liquids as a New Hardener-Modifier System
3.17 Improvement of Water Resistance and Adhesive Performance of UF Resin [71]
3.18 Characterization of UF Resin
3.18.1 13C NMR Data
3.18.2 Free Formaldehyde Content in the Resin
3.18.3 Molecular Weight and Molecular Weight Distribution
3.18.4 Size Exclusion Chromatography
3.18.5 MALDI-TOF MS Method
3.18.6 Cure Time
3.18.7 Differential Scanning Calorimetry
3.19 UF Resin Cure Kinetics
3.20 UF Resins with Low Formaldehyde Emission
3.21 Modification by Polyamines
3.22 Cyclic Urea Prepolymer
3.22.1 Preparation of Cyclic Urea Prepolymer [116]
3.22.2 Cyclic Urea Prepolymer as a Modifying Resin for other Adhesives
3.23 Improvement of UF and MUF Resins by Addition of Hyperbranched Dendrimers
3.23.1 Urea and Melamine Resins without Formaldehyde
References
Chapter 4 Melamine–Formaldehyde Resin. 4.1 Introduction
4.2 Chemistry
4.2.1 Formation of Methylolmelamine
4.2.2 Condensation of Methylolmelamines
4.2.3 Cross-Linking
4.3 Melamine–Urea–Formaldehyde (MUF) Resin
4.3.1 Liquid MUF Resin Preparation
4.3.2 Phenol–MUF (PMUF) Resins
4.3.3 Melamine–Formaldehyde Resin Modification by Acetoguanamine for Post-Formable High-Pressure Laminate
4.3.4 MUF Adhesive Resins of Upgraded Performance
4.3.5 Cold-Setting MUF Adhesives
References
Chapter 5 Phenol–Formaldehyde Resins. 5.1 Introduction
5.2 Historical
5.3 Definitions and Types of Phenolic Resins
5.4 Basic Chemistry
5.4.1 Resols
5.4.2 Novolacs
5.4.3 Difference between the Acid and Base Catalysis
5.4.4 Reaction between Phenol and Formaldehyde (Sodium Hydroxide Catalyzed) 5.4.4.1 Electron Delocalization in Phenol and Phenoxide Anion
5.4.4.2 Hydroxymethylation of Phenol and Further Condensation (under Alkaline Conditions)
5.4.5 Formation of Chelate Ring
5.4.6 Reaction between Phenol and Formaldehyde (Ammonia and Amine Catalysis)
5.4.7 Manufacture of Phenolic Resins. 5.4.7.1 Principles of Manufacture
5.5 Effect of Process Variables. 5.5.1 Catalyst Types and pH of Resin
5.5.2 Effect of Viscosity
5.5.3 MW and Its Distribution of PF Resin
5.6 Commercial Phenolic Resin for Wood Products
5.6.1 Spray Drying of Phenolic Resin
5.6.1.1 The Spray Drying Process
5.6.2 Phenolic Dry Resin Film
5.6.2.1 Types and Grades of Dry Glue Film
5.6.2.2 Process of Making the Dry Adhesive Film [7]
5.7 Curing of Phenolic Resin
5.7.1 PF Cure Acceleration
5.7.2 PF Cure Acceleration by Additives
5.7.3 Mechanism
References
Chapter 6 Resorcinol–Formaldehyde Resins and Hydroxymethyl Resorcinol (HMR and n-HMR) 6.1 Introduction
6.2 Reaction between Resorcinol and Formaldehyde
6.3 Comparison between Resorcinol and Phenol
6.4 Reactive Positions and Types of Linkages Comparison between Resorcinol and Phenol
6.5 Hydroxymethyl Resorcinol. 6.5.1 Introduction
6.5.2 Normal HMR
6.5.3 Formulation of HMR
6.5.3.1 Mixing Procedure
6.5.3.2 Limitations to the Use of HMR
6.6 Novolak-Based HMR
6.6.1 Preparation of n-HMR
6.7 Bonding Mechanism Using HMR. 6.7.1 Mechanism based on the Material Properties of HMR
6.7.2 Mechanism Based on Surface Chemistry
6.8 Applications of HMR and n-HMR. 6.8.1 Bonding to Preservative-Treated Wood
6.8.2 Epoxy–Wood Adhesion
6.8.3 Bonding of Fiber-Reinforced Polymer–Glulam Panels
6.8.4 Priming Agent for Bondability of Wax-Treated Wood
6.9 Special Adhesives of Reduced Resorcinol Content. 6.9.1 Fast-Setting Adhesive for Fingerjointing and Glulam
6.9.2 Branched PRF Adhesives [11, 12, 54]
6.9.3 Cold-Setting PF Adhesives Containing No Resorcinol
References
Chapter 7 Polyurethane Adhesives
7.1 Introduction
7.2 History
7.3 Reactions of Isocyanates
7.4 Raw Materials. 7.4.1 Isocyanates. 7.4.1.1 Aliphatic Isocyanates (Figure 7.2)
7.4.1.2 Aromatic Diisocyanates. 7.4.1.2.1 Toluene Diisocyanate
7.4.1.2.2 Diphenylmethane 4,4’ Diisocyanate (MDI)
7.4.1.2.3 Reactivity of MDI
7.5 Catalysts
7.6 Blocked Isocyanates
7.7 Advantages of pMDI
7.8 PU Adhesive–Wood Interaction
7.9 PU–UF Hybrid Adhesives
7.10 PU–PF Hybrid Adhesives
7.11 EMDI-Based Adhesives
7.11.1 Comparison between EMDI and pMDI
7.12 Emulsion Polymer Isocyanate (EPI) Adhesive
7.13 Non-Isocyanate Polyurethanes and Biobased PU Adhesives
References
Chapter 8 Wood Surface Inactivation (Thermal) 8.1 Introduction
8.2 Causes and Sources of Inactivation
8.3 Mechanisms of Inactivation
8.4 Factors Affecting Wood Surface Inactivation. 8.4.1 Effect of Wood Species
8.4.2 Inactivation Due to High-Temperature Drying
8.4.2.1 Effect of Drying Technique
8.5 Physical Mechanisms of Inactivation. 8.5.1 Effect of Extractives on Wettability and Adhesion
8.5.2 Molecular Reorientation at Surfaces
8.5.3 Micropore Closure
8.6 Chemical Mechanisms of Inactivation. 8.6.1 Elimination of Surface Hydroxyl Bonding Sites
8.6.2 Oxidation and/or Pyrolysis of Surface Bonding Sites
8.6.3 Chemical Interference with Resin Cure or Bonding
References
Chapter 9 Wood Surface Inactivation Due to Extractives. 9.1 Introduction
9.2 Migration of Extractives to the Wood Surface
9.3 Influence of Extractives on Bonding Properties of Wood
9.4 Effect of pH of Wood on the Adhesion
9.5 Effect of Extractive Migrations during Kiln Seasoning on Adhesion
9.6 Methods to Reduce the Influence of Extractives on Wood Adhesion. 9.6.1 Mechanical Method
9.6.2 Chemical Method
References
Chapter 10 Surface Modification of Wood. 10.1 Introduction
10.2 Surface Modification Methods. 10.2.1 Plasma and Corona Treatments
10.2.2 Corona Treatment
10.2.3 Plasma Applications for Wood Surface Plasma Treatments
10.3 Enzymatic Modification for Hydrophobicity
10.4 Modification of Wood Surface by Chemical Treatment—Functionalization of Wood
10.5 Sol–Gel Method
References
Chapter 11 The Chemistry of Condensed Tannins. 11.1 Introduction
11.2 Reactions of Condensed Flavonoid Tannins
11.2.1 Hydrolysis and Acid and Alkaline Condensation
11.2.2 Sulphitation
11.2.3 Catechinic Acid Rearrangement
11.2.4 Catalytic Tannin Autocondensation
11.2.5 Tannin Complexation of Metals
11.2.6 Tridimensional Structure
11.2.7 Reactivity and Orientation of Electrophilic Substitutions of Flavonoids
11.2.8 Influence of Tannin Colloidal Behavior on Reactions
11.2.9 New and Unusual Tannin Reactions
11.2.10 Modern Instrumental Methods of Analysis
11.3 Conclusions
References
Chapter 12 Thermosetting Adhesives Based on Bio-Resources for Lignocellulosic Composites. 12.1 Introduction
12.2 Tannin Adhesives
12.2.1 New Technologies for Industrial Tannin Adhesives
12.2.2 Tannin–Hexamethylenetetramine (Hexamine) Adhesives
12.2.3 Hardening by Tannin Autocondensation
12.3 Lignin Adhesives
12.4 Protein Adhesives
12.5 Carbohydrate Adhesives
12.6 Unsaturated Oil Adhesives
12.7 Wood Welding without Adhesives
12.8 Conclusions
References
Chapter 13 Environmental Aspects of Adhesives—Emission of Formaldehyde. 13.1 Introduction
13.2 Scientific Analysis of the Problem
13.3 Factors Affecting the Amount of Formaldehyde Emission
13.4 Exposure
13.5 Safe Level of Formaldehyde Exposure
13.6 Evolution of Formaldehyde Emission Standards
13.6.1 US HUD Manufactured Housing Standard
13.6.2 California Air Resources Board (CARB) Air Toxic Control Measure for Composite Wood Products
13.7 CARB Green Adhesive Formaldehyde Emission Standards
13.8 Japanese JIS/JAS Formaldehyde Adhesive Emission Standards [21–23]
13.9 European Formaldehyde Emission Standards [24–33]
13.10 Standardization and Test Methods
13.10.1 Reference Methods
13.10.2 Certification Methods
13.10.3 Quality Control Methods
13.11 Different Standards and Test Methods
13.11.1 Reference Method. 13.11.1.1 Chamber Methods
13.11.1.2 ASTM E 1333 [16]
13.11.1.3 ASTM D6007-02(2008) Standard Test Method for Determining Formaldehyde Concentration in Air from Wood Products Using a Small-Scale Chamber [34]
13.11.1.4 ISO 12460-1 and Part 2: 2007 [35]
13.11.1.5 Japanese Small Chamber Method JIS A1901 [22]
13.11.2 Derived Methods. 13.11.2.1 Gas Analysis according to EN 717-2 [29]
13.11.2.2 Flask Method
13.11.2.3 Desiccator Method
13.11.2.4 Criteria of Acceptance for Different Grades are Given in the following Table:
13.11.2.5 The Perforator Method (EN 120) [24]
References
Chapter 14 Rheology and Viscoelasticity of Adhesives. 14.1 Rheology of Adhesives
14.2 Viscosity—Theory
14.3 Capillary Viscometry
14.4 Rotational Viscometers
14.4.1 Spring Type
14.4.2 Servo Systems
14.5 Cone-and-Plate Viscometer
14.6 Parallel Plate Viscometer
14.7 Concentric Cylinder Viscometer
14.8 Ford Cup Viscosity
14.9 Gardner–Holt Tubes
14.10 Newtonian and Non-Newtonian Fluids
14.10.1 Types of Non-Newtonian Fluid Behavior
14.11 Viscoelasticity of Adhesives
14.11.1 Phenomenological Models for Viscoelastic Materials
14.11.1.1 Maxwell Element (Elastic Deformation + Flow)
14.11.1.2 Voigt Element (Spring and Dashpot in Parallel)
14.11.1.3 Maxwell–Voigt Mixed Model (Figure 14.7)
14.12 Dynamic Mechanical Analysis
14.13 TTT and CHT Diagrams
14.14 Experimental Results
References
Chapter 15 Hot Melt Adhesives. 15.1 Introduction
15.2 Polymers Commonly Used for Hot Melt Adhesives
15.2.1 Ethylene Vinyl Acetate Copolymers
15.2.2 Styrenic Block Copolymers
15.3 Polyureathane Reactive Hot Melt Adhesives
15.4 Silane Reactive Hot Melt Adhesives
15.5 Polyamide Hot Melt Adhesives
15.6 Amorphous Polyolefin (APO/APAO) Hot Melt Adhesives
15.7 Tackifiers
15.7.1 Aromatic Hydrocarbon Resins
15.7.2 Aliphatic Hydrocarbon Resins
15.7.3 Mixed Aliphatic and Aromatic Resins
15.7.4 Terpene Resins
15.7.5 Terpene–Phenol Resins
15.7.6 Rosin and Rosin Derivatives
15.8 Antioxidants [22]
15.8.1 Oxidation-Sensitive Components in Hot Melts
15.8.2 Antioxidants Used in Hot Melts
15.9 Plasticizers
15.10 Mineral Oil and Wax
References
Chapter 16 Modification of Natural Fibers and Polymeric Matrices. 16.1 Introduction
16.2 Strategies to Treat the Biofibers for Compatibility. 16.2.1 Physical Methods
16.2.2 Steam Explosion Treatment
16.3 Chemical Methods
16.3.1 Mercerization
16.3.2 Acetylation of Natural Fibers
16.3.3 Silane Coupling Agents
16.3.4 Benzoylation Treatment
16.3.5 Acrylation of Natural Fibers
16.3.6 Treatment with Isocyanates
16.3.7 Peroxide Treatment
16.3.8 Permanganate Treatment
16.3.9 MAH Treatment
16.3.10 Treatment with Chlorotriazines
16.3.11 Additives
16.4 Functionalization of Matrices for Compatibility
16.5 MAH Grafted Polyolefins as Matrix Additives
16.6 Reactive Extrusion System
References
Chapter 17 Polymer Matrix: Unsaturated Polyester. 17.1 Introduction
17.2 Raw Materials. 17.2.1 Diols
17.2.2 Cyclopentadiene-Based Resin
17.2.3 Isophthalic-Acid-Based Resin
17.2.4 Bisphenol A Fumarate Resins
17.2.5 Vinyl Ester
17.3 Polyesterification Reaction
17.4 Cross-Linking Reaction
17.4.1 Curing at Elevated Temperatures
17.4.2 Curing at Room Temperatures
17.5 Sheet Molding Compounds Based on UP Resins
17.6 UV Curable Compositions Based on UP/Vinyl Ester Resins
17.7 Biocomposites Based on UP Matrix
References
Chapter 18 Polymer Matrix: Epoxy Resins. 18.1 Introduction
18.2 Resin Preparation
18.3 Characteristics of Epoxy Resins
18.3.1 Epoxy Equivalent
18.3.2 Enhancement of Properties
18.3.3 Types of Epoxy Resins
18.3.4 Bisphenol A Glycidyl Ethers
18.4 Preparation of DGEBA Epoxy Resin
18.4.1 Curing Agents
18.4.1.1 Tertiary Amines
18.4.1.2 Polyfunctional Amines
18.4.1.3 Calculations of the Proportion of Amines for Curing Epoxy Resins
18.4.1.4 Special Amines
18.4.1.5 Acid Anhydrides
18.4.1.6 Anhydride Curing Mechanism
18.5 Other Types of Epoxy Resins. 18.5.1 Epoxidized Novolac
18.5.2 Tetrabromo Bisphenol A Epoxy Resins
18.5.3 Epoxidized Vegetable Oils
18.5.4 Epoxidized Natural Rubber
18.6 Green or Sustainable Epoxy Matrix
18.7 Epoxy-Matrix-Based Biofiber Composites
References
Chapter 19 Polymer Matrix: Polyethylene. 19.1 Introduction
19.2 High-Pressure Process
19.3 Low-Pressure Processes—Catalysts for Polymerization
19.3.1 Ziegler–Natta Catalysts
19.4 Production of PE. 19.4.1 Solution Process
19.4.2 Slurry Process
19.4.3 Gas Phase Fluidized Bed Reactor
19.5 Compatibilizers
19.6 Relevant Property of PE. 19.6.1 Melt Flow Index
19.7 Treatment and Functionalizing of Biofibers and Matrix Materials
19.8 Biocomposites Based on PE. 19.8.1 Kenaf-Based Biocomposites
19.8.2 Sisal-Fiber-Based Biocomposites
19.8.3 Flax-Fiber-Based Biocomposites
19.8.4 Hemp-Fiber-Based Biocomposites
19.8.5 Miscellaneous
References
Chapter 20 Polymer Matrix: Polypropylene. 20.1 Introduction
20.2 PP Manufacture
20.2.1 Catalysts
20.2.2 α- and β-Forms of PP
20.2.3 Polymerization Methods. 20.2.3.1 Solvent Polymerization Process
20.2.3.2 Bulk Polymerization Process
20.2.3.3 Gas Phase Polymerization Process
20.3 Biofiber Composites Based on PP. 20.3.1 Kenaf-Based Composites
20.3.2 Oil-Palm-Fiber-Based Composites
20.3.3 Flax-Fiber-Based Composites
20.3.4 Sisal-Based PP Composites
20.3.5 Hemp-Based PP Composites
References
Chapter 21 Biodegradable Polymers as Matrix for Biocomposites. 21.1 Introduction
21.2 Polyhydroxyalkanoates
21.2.1 Poly(3-hydroxybutyrate) PHB
21.2.2 Poly(3-hydroxybutyrate-co-3-hydroxyvalerate)
21.3 Polylactic Acid
21.3.1 Synthesis of PLA
21.3.2 Direct Polymerization
21.3.2.1 Solution Polycondensation
21.3.2.2 Melt Polycondensation
21.3.2.3 Ring-Opening Polymerization
21.4 Polybutylene Adipate Terephthalate
21.5 All Green Composites
References
Index
Also of Interest. Check out these published and forthcoming related titles from Scrivener Publishing
WILEY END USER LICENSE AGREEMENT
Отрывок из книги
Scrivener Publishing 100 Cummings Center, Suite 541J Beverly, MA 01915-6106
Adhesion and Adhesives: Fundamental and Applied Aspects
.....
where Q is the liquid volume flow [m3 s–1], K is the specific permeability of wood [m2], A is the area perpendicular to the liquid flow [m2], L is the sample length in the direction of flow [m], η is the dynamic viscosity of the liquid [Pa s], and ΔP is the pressure gradient [Pa]. As described by Darcy’s law, the pressure gradient ΔP is the cause for the liquid penetration into wood.
The permeability and surface energy are the two wood-related factors controlling adhesive penetration [44]. Permeability varies with species and direction (e.g., tangential, radial, and longitudinal). However, longitudinal permeability may be as much as 104 times greater than transverse permeability [51]. Wood species with low permeability, such as Douglas-fir heartwood, severely restricts resin penetration in the radial and tangential directions. High permeability of the wood surface may be problematic to adhesive bonding if this leads to starvation at the bondline. Thus, bonding endgrain is difficult [44]. There are earlywood and latewood differences, as well as heartwood and sapwood differences. Pit aspiration sometimes occurs in softwoods during drying [51], thus severely reducing permeability. White [52] noted greater penetration of phenol-resorcinol into earlywood than latewood cells of southern pine.
.....