Arc Welding Processes Handbook
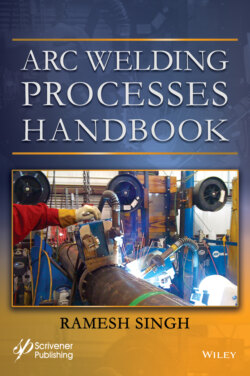
Реклама. ООО «ЛитРес», ИНН: 7719571260.
Оглавление
Ramesh Kumar Singh. Arc Welding Processes Handbook
Table of Contents
List of Illustrations
List of Tables
Guide
Pages
Arc Welding Processes Handbook
List of Figures
List of Tables
Foreword
Preface
1. Introduction to Welding Processes. 1.1 Synopsis
1.2 Keywords
1.3 Welding
1.4 Defining Welding
1.5 Welding and Joining Processes
1.6 Arc Welding
1.6.1 Carbon Arc Welding
1.6.2 Shielded Metal Arc Welding (SMAW)
1.6.3 Gas Tungsten Arc Welding (GTAW)
1.6.4 Gas Metal Arc Welding (GMAW)
1.6.5 Submerged Arc Welding (SAW)
1.7 Efficiency of Energy Use
1.8 Welding Procedures
1.9 Qualification of Welders and Operators
2. Shielded Metal Arc Welding (SMAW) 2.1 Synopsis
2.2 Keywords
2.3 Introduction
2.4 Process Fundamentals
2.5 How the Process Works
2.6 Power Sources
2.6.1 Constant Current and Constant Voltage Power Source
2.6.2 Constant Current Curve
2.6.3 Constant Voltage Curve
2.7 AC Power Sources
2.7.1 The Alternator Type AC Welding Machines
2.7.2 Movable Coil Type Control
2.7.3 Movable Shunt Type Control
2.7.4 Movable Core (Reactor) Type of Control
2.7.5 Magnetic Amplifier Method of Current Control
2.7.6 Diode
2.7.7 Silicon-Controlled Rectifiers (SCRs)
2.7.8 Transistors
2.8 Direct Current Power Sources
2.8.1 Generator
2.8.2 Alternator
2.8.2.1 Power Source Remote Control
2.8.3 Installation of Welding Machines
2.8.3.1 Cooling System for Welding Power Sources
2.8.3.2 Welding Connections – Welding Cable and Electrode Holders
2.8.4 Electrode Holders
2.8.5 Arc Welding Power Source Classification by NEMA
2.8.5.1 Duty Cycle
2.8.5.2 Power Requirement
2.9 Welding Safety and Personal Protecting Equipment
2.9.1 Shields and Helmets
2.9.2 Optical Clarity for Welding
2.9.3 Other Essential Clothing for Welders
2.10 Covered Electrodes Used in SMAW Process
2.10.1 Coating Types
2.10.1.1 Cellulose-Coated Electrodes
2.10.1.2 Rutile-Coated Electrodes
2.10.1.3 Basic-Coated Electrodes
2.10.2 Portfolio of SMAW Electrode
2.10.3 Identification of Welding Electrode
2.10.4 Need for the Covered Electrode
2.10.5 Electrode Conditioning
2.11 Welding Training – Making of a Welder
2.11.1 Joint Design and Preparation
2.11.2 SMAW Welding of Plate
2.11.3 Making of a SMAW Welder
2.11.3.1 SMAW Welding Practice Step 1
2.11.3.2 SMAW Welding Practice Step 2
2.11.3.3 SMAW Welding Practice Step 3
2.11.4 Inspection of the Weld
2.11.4.1 Appearance of the Weld
2.11.5 Step 3 Practice 2
2.11.6 SMAW Welding Step 4
2.11.7 SMAW Welding Step 5
2.11.8 Set a Next Goal to Achieve
2.11.9 SMAW Welding of Pipes
2.11.9.1 Pipe Welding Step 1
2.11.10 Pipe Welding Technique and Pipeline Welding
2.11.10.1 Vertical Up Technique
2.11.10.1.1 Procedure for Vertical-Up Welding Technique
2.11.11 In-Plant Piping
2.11.12 Pipeline Welding
2.11.12.1 Making a Root Pass
2.12 Welding Other Metals
2.12.1 SMAW Welding Aluminum
2.12.2 Aluminum Alloys and Their Characteristics
2.12.2.1 1xxx Series Alloys
2.12.2.2 2xxx Series Alloys
2.12.2.3 3xxx Series Alloys
2.12.2.4 4xxx Series Alloys
2.12.2.5 5xxx Series Alloys
2.12.2.6 6XXX Series Alloys
2.12.2.7 7XXX Series Alloys
2.12.3 The Aluminum Alloy Temper and Designation System
2.12.4 Wrought Alloy Designation System
2.12.5 Cast Alloy Designation
2.12.6 The Aluminum Temper Designation System
2.12.6.1 Aluminum Welding Electrodes
2.12.6.2 Electrical Parameters
2.12.7 SMAW Welding of Stainless Steel
2.12.8 Introduction to Stainless-Steels
2.12.8.1 Cutting Stainless Steel for Fabrication
2.12.8.2 Finishing
2.12.9 Fabrication of Stainless Steel
2.12.9.1 Why Use Stainless Steel
2.12.10 General Welding Characteristics
2.12.10.1 Protection Against Oxidation
2.12.11 Welding and Joining Stainless Steel
2.12.12 Importance of Cleaning Before and After Welding
2.12.13 Filler Metals
2.12.14 Austenitic Stainless Steels
2.12.14.1 Metallurgical Concerns Associated with Welding Austenitic Stainless Steels
2.12.14.2 Mechanical Properties of Stainless Steels
2.12.15 Welding of Austenitic Stainless Steels
2.12.16 Super-Austenitic Stainless Steels
2.12.17 Welding and Joining of Supper-Austenitic Stainless Steels
2.12.17.1 Difficulties Associated with Welding Stainless Steel
2.12.18 Martensitic Stainless Steels
2.12.18.1 Properties and Application
2.12.18.2 Welding Martensitic Stainless Steels
2.12.19 Welding Ferritic Stainless Steels
2.12.19.1 Properties and Application
2.12.20 Welding Ferritic Steel
2.12.21 Precipitation Hardening (PH) Stainless Steels. 2.12.21.1 Properties and Application of Precipitation Hardening Steels
2.12.22 Welding Precipitation Hardened (PH) Steels
2.13 Welding and Fabrication of Duplex Stainless Steels
2.13.1 Mechanical Properties
2.13.2 Heat Treatment
2.14 SMAW Welding Nickel Alloys
2.14.1 Welding of Precipitation Hardenable Nickel Alloy
2.14.2 Welding of Cast Nickel Alloy
2.14.3 Nickel – Chromium Alloys
2.14.4 Nickel – Copper (Cupro-Nickle Alloys)
2.14.5 Nickel – Iron – Chromium Alloys
2.15 Minimizing Discontinuities in Nickel and Alloys Welds
2.15.1 Porosity
2.15.2 Weld Cracking
2.15.3 Stress Corrosion Cracking
2.15.4 Effect of Slag on Weld Metal
2.16 Review Your Knowledge
3. Gas Tungsten Arc Welding. 3.1 Synopsis
3.2 Keywords
3.3 Introduction to Gas Tungsten Arc Welding Process
3.4 Process Description
3.5 How the Process Works
3.6 Process Advantages and Limitations
3.7 Power Sources
3.7.1 AC Power Sources
3.7.1.1 The Alternator Type AC Welding Machines
3.7.1.2 Movable Coil Movable Core (Reactor)
3.7.1.3 Magnetic Amplifier Method of Current Control
3.7.1.4 AC Inverters for GTAW Process
3.7.2 Other Control Methods
3.7.2.1 Wave Forms
3.7.2.1.1 Advanced Square Wave
3.7.2.1.2 Soft Square Wave
3.7.2.1.3 Sine Wave
3.7.2.1.4 Triangular Wave
3.7.2.2 Independent Amperage Control
3.7.2.3 Adjustable AC Output Frequency
3.7.2.4 Extended Balance Control
3.7.3 Diode
3.7.4 Silicon-Controlled Rectifiers (SCRs)
3.7.5 Transistors
3.7.6 A Direct Current Power Source for GTAW
3.7.6.1 Generator
3.7.6.2 Alternator
3.7.6.3 The Output Current
3.7.6.4 Duty Cycle
3.7.7 The Inverter Machines
3.8 Shielding Gases
3.9 Gas Regulators and Flowmeters
3.10 GTAW Torches, Nozzles, Collets, and Gas Lenses
3.10.1 Gas Lens
3.11 Tungsten Electrodes
3.11.1 Grinding of Tungsten Electrode Tips
3.11.2 Tungsten Grind Angles and How They Affect Weld Penetration
3.11.2.1 The Impact of Tungsten Tip Angles on Weld
3.12 Joint Design
3.13 Power Source Remote Control
3.14 Installation of Welding Machines
3.15 Power Source Cooling System
3.16 Welding Connections – Welding Cable and Welding Torch Connections
3.17 Welding Power Source Classification by NEMA
3.18 Welding Personal Protecting Equipment
3.19 Other Essential Clothing for Welders
3.20 Filler Wires Used in GTAW Process
3.21 Classification and Identification of Welding Wires
3.21.1 Designation of Aluminum Welding Wires
3.21.2 Aluminum Alloys and Their Characteristics
3.22 The Aluminum Alloy Temper and Designation System
3.22.1 Wrought Alloy Designation System
3.22.2 Cast Alloy Designation
3.22.3 The Aluminum Temper Designation System
3.23 Welding Metals Other Than Carbon and Alloy Steels
3.24 GTAW Welding of Aluminum
3.25 GTAW Welding of Stainless Steel
3.25.1 Introduction to Stainless-Steels
3.25.1.1 Cutting Stainless Steel for Fabrication
3.25.1.2 Finishing
3.25.2 Fabrication of Stainless Steel
3.25.3 Why Stainless Steel
3.25.4 General Welding Characteristics
3.25.5 Protection Against Oxidation
3.25.6 Welding and Joining
3.25.7 Importance of Cleaning Before and After Welding
3.25.8 Filler Metals
3.25.9 Austenitic Stainless Steels. 3.25.9.1 Metallurgical Concerns Associated with Welding Austenitic Stainless Steels
3.25.9.2 Mechanical Properties of Stainless Steels
3.25.9.3 Welding of Austenitic Stainless Steels
3.25.10 Welding Super-Austenitic Stainless Steels. 3.25.10.1 Material Properties and Applications
3.25.10.2 Welding and Joining of Supper-Austenitic Stainless Steels
3.25.10.3 Difficulties Associated with Welding Stainless Steel
3.25.11 Welding Martensitic Stainless Steels - Properties and Application
3.25.12 Welding Martensitic Stainless Steels
3.25.13 Welding Ferritic Stainless Steels
3.25.13.1 Welding Ferritic Steel
3.25.14 Welding Precipitation Hardening Stainless Steels
3.25.14.1 Welding Precipitation Hardened (PH) Steels
3.26 Mechanical Properties
3.26.1 Heat Treatment of Duplex Steels
3.26.2 How to Weld Duplex Stainless Steel
3.26.2.1 Filler Metal
3.26.2.2 Heat Input and Interpass Temperatures
3.26.2.3 Quality Checks
3.27 Welding Nickel Alloys
3.27.1 Welding of Precipitation Hardenable Nickel Alloy
3.27.2 Welding of Cast Nickel Alloy
3.27.3 Nickel – Chromium Alloys
3.27.4 Nickel – Copper (Cupro-Nickle Alloys)
3.27.5 Nickel – Iron – Chromium Alloys
3.27.6 Minimizing Discontinuities in Nickel and Alloys Welds
3.27.6.1 Porosity
3.27.6.2 Weld Cracking
3.27.6.3 Stress Corrosion Cracking
3.27.6.4 Effect of Inclusions on Weld Metal
3.28 Later Developments in GTAW Process
3.29 Plasma Arc Welding
3.30 Review Your Knowledge
4. Gas Metal Arc Welding. 4.1 Synopsis
4.2 Keywords
4.3 Introduction to Gas Metal Arc Welding Process
4.3.1 Developmental History of GMAW Process
4.3.2 The Advantages of GMAW
4.3.3 Limitations of GMAW
4.4 Process Description. 4.4.1 Gas Metal Arc Welding (GMAW) Process Introduction
4.4.1.1 Short Circuiting Transfer (GMAW-S)
4.4.1.2 Globular Transfer
4.4.1.3 Spray Transfer
4.4.1.4 Pulsed Spray Transfer Mode
4.4.2 Gas Metal Arc Welding: Newer Variants
4.5 Components of the Welding Arc
4.5.1 Shielding Gases for GMAW
4.5.1.1 Argon Gas
4.5.1.2 Helium Gas
4.5.2 Dissociation and Recombination. 4.5.2.1 Dissociation and Recombination of CO2 Gas
4.5.2.2 Oxygen as Shielding Gas
4.5.2.3 Hydrogen Gas
4.5.3 Binary Shielding Gases
4.5.3.1 Argon + Helium
4.5.3.2 Argon + CO2
4.5.4 Shielding Gases by Transfer Mode. 4.5.4.1 Common Short-Circuiting Transfer
4.5.4.2 Common Axial Spray Transfer
4.5.5 Ternary Gas Shielding Blends
4.5.5.1 Common Ternary Gas Shielding Blends
4.6 Effects of Variables on Welding
4.6.1 Current Density
4.6.2 Electrode Efficiencies
4.6.2.1 Calculation of Required Electrode Based on the Electrode Efficiency (EE)
4.6.3 Deposition Rate
4.6.4 Electrode Extension and Contact Tip to Work Distance
4.7 Advanced Welding Processes for GMAW
4.8 The Adaptive Loop
4.9 Advanced Waveform Control Technology. 4.9.1 Surface Tension Transfer™ (STT™)
4.10 Equipment for GMAW Process
4.11 GMAW Power Sources
4.11.1 The Transformer Rectifiers
4.11.2 Inverters
4.12 Installation of Welding Machines
4.12.1 GMAW Torches
4.12.1.1 Welding Torches for Automation and Robotic GMAW
4.12.1.2 The Wire Drive and Accessories
4.12.1.3 Special Wire Feeding Considerations
4.12.1.4 Shielding Gas Regulation
4.12.1.5 Welding Cables and Other Accessories
4.12.1.6 Welding Personal Protecting Equipment
4.12.1.7 Other Essential Clothing for Welders
4.13 Welding Various Metals
4.13.1 Carbon Steel
4.13.2 Aluminum and Aluminum Welding
4.13.2.1 Understanding Aluminum
4.13.2.2 Designation of Aluminum Welding Wires
4.13.3 Aluminum Metallurgy and Grades
4.13.3.1 1xxx Series Alloys
4.13.3.2 2xxx Series Alloys
4.13.3.3 3xxx Series Alloys
4.13.3.4 4xxx Series Alloys
4.13.3.5 5xxx Series Alloys
4.13.3.6 6XXX Series Alloys
4.13.3.7 7XXX Series Alloys
4.13.4 The Aluminum Alloy Temper and Designation System
4.13.5 Wrought Alloy Designation System
4.13.6 Cast Alloy Designation
4.13.7 The Aluminum Temper Designation System
4.13.8 Welding Aluminum
4.13.8.1 Electrode Selection
4.13.9 Welding Stainless Steel with the Gas Metal Arc Process
4.13.10 Introduction to and Understanding Stainless Steel
4.13.11 Alloying Elements and Their Impact on Stainless Steel
4.13.11.1 The Elements that Promote Ferrite are
4.13.11.2 The Elements that Promote Austenite are
4.13.11.3 Neutral Effect Regarding Austenite & Ferrite
4.13.12 Weldability of Stainless Steels
4.13.12.1 Welding Austenitic Steels
4.13.12.2 Challenges of Welding Austenitic Steels
4.13.12.3 Sensitization
4.13.12.4 Intergranular Corrosion in the Heat Affected Zone Control of Carbide Precipitation
4.13.12.5 Hot Cracking
4.13.12.6 Design for Welding Stainless Steels
4.13.12.7 Determining and Measuring the Ferrite in Welds
4.13.12.8 Welding Ferritic Stainless Steels
4.13.12.9 Properties and Application
4.13.12.10 Welding Ferritic Steel
4.13.12.11 Precipitation Hardening Stainless Steels
4.13.12.12 Welding Precipitation Hardened (PH) Steels
4.13.12.13 Martensitic Stainless Steels
4.13.12.14 Properties and Application
4.13.12.15 Welding Martensitic Stainless Steels
4.13.12.16 Duplex Stainless Steels
4.13.12.17 Mechanical Properties
4.13.12.18 Heat Treatment
4.14 Welding Nickel Alloys
4.14.1 Welding of Precipitation Hardenable Nickel Alloy
4.14.2 Welding of Cast Nickel Alloy
4.14.3 Nickel – Chromium Alloys
4.14.4 Nickel – Copper (Cupro-Nickle Alloys)
4.14.5 Nickel – Iron – Chromium Alloys
4.15 Minimizing Discontinuities in Nickel and Alloys Welds
4.15.1 Porosity
4.15.2 Weld Cracking
4.15.3 Stress Corrosion Cracking
4.15.4 Effect of Slag on Weld Metal
4.16 Calculating Heat Input in Pulsed Arc GMAW
4.17 Review Your Knowledge
5. Flux Cored Arc Welding (FCAW) Process. 5.1 Synopsis
5.2 Keywords
5.3 Introduction to Flux Cored Arc Welding (FCAW) Process
5.4 Process Description
5.4.1 Self Shielding Flux Cored Arc Welding (FCAW-S) Process
5.4.2 Flux Core Arc Welding (FCAW-G) Gas Shielding Process
5.5 Welding Wires/Electrodes
5.5.1 Construction of FCAW Electrodes
5.5.2 Sheath Thickness Variations
5.5.3 Important FCAW Variables
5.5.4 Contact Tip to Work Distance (CTWD)
5.5.5 Travel Angle
5.5.6 Single Pass Limitations
5.5.7 Thickness Restrictions
5.5.8 Charpy V-Notch Toughness Properties
5.5.9 Electrode Care and Packaging
5.6 Power Sources
5.6.1 Arc Voltage (Constant Voltage)
5.6.2 CTWD, ESO and WFS
5.7 Other Accessories to Power Source. 5.7.1 Welding Cable
5.7.2 Semiautomatic Wire Feeders
5.7.3 Welding Guns
5.7.4 Reverse Bend Gun Tubes
5.7.5 Gun Angles
5.7.6 Polarity
5.8 Shielding Gases
5.8.1 Attributes of Shielding Gases
5.8.2 How Shielding Gas Works?
5.8.3 Properties of Shielding Gases
5.8.4 Limits on the Use of Inert Gases
5.8.5 Argon and Carbon Dioxide Gas Blends
5.8.6 How the Shielding Gas and Blends Affect the Mechanical Properties of the Weld Metal?
5.8.7 Understanding the Performance of Various FCAW-G Gases
5.8.7.1 Shielding Gas Cost
5.8.7.2 Overall Operator Appeal and Impact on Productivity
5.8.7.3 Typical Use of Shielding Gas
5.9 Welding Various Metals
5.9.1 Applicable Base Metals
5.9.2 Types of Welding Procedure Specifications (WPS)
5.9.3 FCAW Welding Austenitic, Ferritic Stainless Steels and Duplex Steels
5.9.3.1 Stainless Steel
5.9.3.2 Duplex Steels
5.9.3.3 Welding Ferritic Stainless Steels
5.9.3.4 Choice of Shielding Gases
5.9.4 FCAW Welding of Aluminum
5.9.5 Welding Nickel and Nickel Alloys by FCAW Process
5.10 Tips for Good Welding by FCAW Process
5.11 Test Your Knowledge
6. Submerged Arc Welding (SAW) 6.1 Synopsis
6.2 Keywords
6.3 Introduction to Submerged Arc Welding (SAW) Process
6.4 Operating Characteristics
6.5 Submerged Arc Welding (SAW) Process
6.5.1 Advantages and Limitations of Submerged Arc Welding
6.6 How the SAW Process Works
6.6.1 Depositing a Root Pass with SAW Process
6.6.2 Travel Mechanism
6.6.3 Variables of the SAW Process
6.7 SAW Process Variants
6.7.1 Variants Based on Use of Welding Wire
6.7.1.1 Multi-Wire Systems
6.7.1.2 Use of Hot-Wire
6.7.2 Adding Iron Powder to the Flux
6.7.3 The Utilization of a Strip Electrode for Surfacing
6.8 SAW Power Source and Equipment
6.9 Welding Heads (Gun)
6.10 Fluxes
6.10.1 Types of Granular Fluxes
6.10.2 Fused Fluxes versus Bonded Fluxes
6.10.3 Fused Fluxes
6.10.4 Bonded Fluxes
6.10.5 Neutral Fluxes
6.10.6 Acid Fluxes
6.10.7 Basic Fluxes
6.10.8 Selection of Specific Flux
6.11 Submerged Arc Welding Various Metals
6.12 Test Your Knowledge
7. Useful Data and Information Related to Welding and Fabrication. 7.1 Common Weld Symbols and Their Meanings
7.2 Fillet Welds
7.3 Groove Welds
7.4 Pipe Schedule
7.5 Terms and Abbreviations
7.5.1 ASME Section IX QW 432 - F Number Table for Carbon and Alloy Steel
7.6 Procedure Qualification Range as Per the Material Group
7.7 Material Qualification Rage for Procedure Qualification Based on P-Numbers
7.8 Temperature Conversion
7.9 Useful Calculations
7.10 Effect of Temperature on Gas Cylinder Pressure
Index
WILEY END USER LICENSE AGREEMENT
Отрывок из книги
Scrivener Publishing 100 Cummings Center, Suite 541J Beverly, MA 01915-6106
.....
Figure 3.7.2.2 Effect of Independent AC amperage control on weld penetration and weld bead profile
Figure 3.7.2.3 Effect of variation in AC frequency on the weld profile and penetration
.....