Paint Analysis
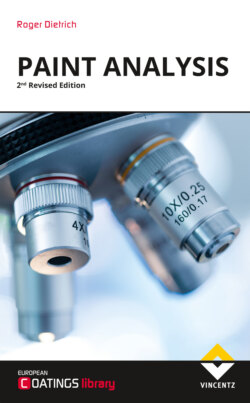
Реклама. ООО «ЛитРес», ИНН: 7719571260.
Оглавление
Roger Dietrich. Paint Analysis
Foreword
Part IGeneral information about paint analysis
1The surface
3.1.1.1Definition of the term surface
2Why paint analysis?
3Relevance of modern analytical techniques to paint analysis
4General considerations
5Chemical mapping
5.1Infrared microscopy mapping
5.2TOF-SIMS imaging
5.3SEM-EDS mapping
6Depth profiling
7Instrumentation
1The bumpy road to knowledge
2The analytical procedure
2.1Inquiry
2.2Inspection. 2.2.1Macroscopic inspection
2.2.2Microscopic inspection
2.3Informed guess
2.4Instrument selection
2.5Investigation
2.6Interpretation
2.7Iterance
2.8Implementation
2.9Incumbency
3The power of sampling. 3.1The role of sampling in the analytical procedure
3.2Random sampling and representativeness
13.2.1.1 Example 1: Bernoulli experiment
13.2.1.2Example 2: Zero defect sampling
13.2.1.3 Example 3: Random sampling of binders
3.3Targeted sampling
3.4Non-destructive sampling. 3.4.1Wipe sampling
13.4.1.1 Wiping procedure (wet wiping)
13.4.1.2 Wiping procedure (dry wiping):
3.4.2Rinse sampling
3.4.3Abrasive sampling
3.5Typical sampling failures
3.5.1Wrong sample collection
3.5.2Non-representative sampling
3.5.3 Selecting the wrong amount of samples
3.5.4Application of a wrong sampling procedure
3.5.5Inappropriate sampling tools and containers
3.5.6Insufficient storing and shipping of samples
3.6Microsampling
4Paint failures and. their analytical approach. 4.1Some considerations on failure reasons
4.1.1Insufficient workpiece preparation
14.1.1.1Surface treatment of metal substrates
14.1.1.2 Polymer surface cleaning and pretreatment
4.1.2Handling failures
4.1.3Application conditions
4.1.4Environment and climate
4.2Investigation of adhesion failures
4.2.1Delamination due to substrate contamination
4.2.2Adhesion defects caused by migration processes
14.2.2.1Example: Paint adhesion failure of a 2K PU paint
4.2.3Delamination caused by moulding conditions
4.2.4Delamination due to application faults
14.2.4.1 Example: Delamination of a 2K polyester polyurethane paint from a polymer surface
4.2.5Delamination due to insufficient pretreatment
14.2.5.1 Example: Delamination of a coating from a PC-PET surface
4.3Paint cratering and “fisheyes”
4.3.1Cratering caused by contamination of the paint material
4.3.2Craters and pinholes caused by substrate contaminants
4.3.3Craters caused by paint additive agglomeration
14.3.3.1Example 1: KTL flat craters due to additive enrichment
14.3.3.2Example 2: Powder coating craters caused by a filler
4.3.4Cratering caused by the application conditions
4.4Bubbles and blisters
4.5Discolouration
4.6Hazes and stains
14.2.1.1Example: Polyurethane high gloss coating showing a haze
4.7Paint spots
14.2.1.1Example: Paint spot on a polymer substrate
4.8Orange peel
4.9References
Part IIIQuality control and process analysis
1 Quality control of raw material
1.1 Binders
1.1.1 Identity check
1.1.2Detection of trace contaminants
1.2 Solvents
1.3 Pigments. and fillers
2Quality control of paint production
2.1Analysis of filter residues
2.1.1SEM/EDS analysis of filter residues
2.1.2FT-IR analysis of filter residues
2.2Analysis of fogging residues
2.3Quality check of finished and. semi-finished products
2.3.1ATR-FT-IR screening
17.3.1.1Example: White automotive paint
2.3.2TOF-SIMS analysis
2.3.3Headspace GC-MS analysis
2.4Paint quality tests
3Field analysis
3.1Process analysis of paint shops
3.2Aerosol analysis
3.3Operating test
3.4Sampling of the painting air
3.5Monitoring of pretreatment steps
3.6Investigation of the degree of. crosslinking in 2-pack paints
18.2.1.1Example: Binder/hardener ratio of 2-pack polyester-polyurethane paint
3.7Investigation of paint additive migration
3.8Marine and aircraft coating inspection
3.9Handhelds and portables
3.10References
1 Optical light microscopy
1.1Extended focus imaging (EFI)
1.2Differential interference contrast (DIC)
2Fluorescence microscopy
3 Infrared spectroscopy
3.1Physical background
3.2Characteristic absorptions
3.3Instrumentation
3.4Sample preparation
3.5Spectrum representation
3.6Quantification
3.7 Data analysis and evaluation
3.7.1Data processing
3.7.2Use of databases
4 Surface infrared spectroscopy
4.1 ATR-FT-IR spectroscopy
4.1.1Physical background
4.1.2 Depth of penetration
4.1.3 Information depth
4.1.4 Effective path length
4.1.5 Quantification
4.1.6 Detection limit
4.1.7 Instrumentation
23.1.7.1 ATR crystal material
4.1.8Sample preparation
4.2Reflection infrared spectroscopy
4.2.1Physical background
4.2.2External reflection
23.2.2.1Reflection from thin films on reflecting substrates
23.2.2.2Reflection from thin films on non-metallic surfaces
4.2.3Instrumentation
4.3Diffuse reflection spectroscopy
4.3.1Physical background. 23.3.1.1Lambert`s law
23.3.1.2 The Kubelka-Munk theory
4.3.2Penetration depth
4.3.3Influences of variable parameters on the spectrum
4.3.4Sample preparation
4.3.5Instrumentation
4.3.6Quantification
4.3.7Optimization of the measuring parameters
4.3.8Repeatability
5Infrared microscopy
5.1Instrumentation
5.2Sample preparation
5.3Infrared microscopy, infrared transmission mode
5.4 Infrared microscopy, reflection mode
24.2.1.1Application examples: smooth polymer or coating surfaces
24.2.1.2Analysis of cross sections
5.5Infrared microscopy, ATR mode
5.6Line-scan und mapping analysis
24.2.1.1Application example paint spots
6Raman spectroscopy
6.1.1Physical background
6.1.2Instrumentation
6.1.3Advantages and limitations
6.1.4Quantification
6.1.5Applications. 25.0.5.1 Paint failure analysis
25.0.5.2Forensic paint investigation
25.0.5.3Identification of unknown micro-particles
7Time-of-flight secondary. ion mass spectrometry
7.1.1Physical background. 26.0.6.1a) Excitation of the surface
26.0.6.2 b) Detection of the secondary ions
7.1Instrumentation
7.2Calibration and mass resolution
7.3 Sample preparation
7.4Spectral evaluation
7.5Imaging mode
7.6 Quantification
7.7Summary
7.8Applications
26.2.1.1 Studies of laquers, binders and resins
26.2.1.2 Quality control of raw materials
26.2.1.3 Structural analysis
8 Scanning electron microscopy
8.1Physical background
27.2.1.1Secondary electrons
27.2.1.2 Back-scattered electrons
27.2.1.3 Characteristic X-ray radiation
8.2Lateral resolution
8.3 Instrumentation
8.4Sample condition
27.2.1.1 Information depth
9Electron microanalysis
9.1Physical background
9.2 Quantification
9.3 Detection limits
9.4EDS-Imaging
9.5Applications
10X-ray photoelectron spectroscopy
10.1Physical background
10.2 Information depth
10.3 Lateral resolution
10.4Information retrieval
10.5 Quantification
10.6Instrumentation
10.7Applications
10.8Technical data
11GC-MS
11.1Physical background of GC
11.2Headspace
30.2.1.1Instrumentation
30.2.1.2Sample preparation
30.2.1.3GC separation
30.2.1.4Detection
11.3Data evaluation
11.4Application. 30.2.1.1Example: Comparison of two paint batches
12Thin layer chromatography TLC-ATR-FT-IR
12.1General principle
12.2Separation procedure
12.3Identification
12.4Performance parameters of selected methods
13References
Author
Acknowledgements
Index
Отрывок из книги
European Coatings Library
Roger Dietrich
.....
The results of both analyses are listed in Table II.2, and seem to be unequal and contradictory. How can this happen? Did one or even both laboratories work inaccurately? The answer is “No!” Rather, the method selection limits the results to one aspect of the real composition.
One of the laboratories used the TOF-SIMS method for the analysis of the extracts from the activated carbons, because it has an extremely high sensitivity to PWIS (paint wetting impairment substances). It was deliberately accepted that volatile compounds are not detected by the TOF-SIMS method.
.....