Viscoplastic Flow in Solids Produced by Shear Banding
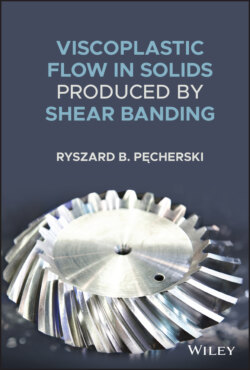
Реклама. ООО «ЛитРес», ИНН: 7719571260.
Оглавление
Ryszard B. Pecherski. Viscoplastic Flow in Solids Produced by Shear Banding
Table of Contents
List of Illustrations
Guide
Pages
Viscoplastic Flow in Solids Produced by Shear Banding
Preface
Acknowledgements
References
1 Introduction. 1.1 The Objective of the Work
1.2 For Whom Is This Work Intended?
1.3 State of the Art. 1.3.1 Motivation Resulting from Industrial Applications
1.3.2 KOBO Processes Resulting in Viscous Effects
1.4 Summary of the Work Content
Acknowledgements
References
2 Physical Basis. 2.1 Introductory Remarks
2.2 Deformation Mechanisms in Single Crystals
2.2.1 Plastic Glide and Twinning
2.2.2 Hierarchy of Plastic Slip Processes
Observation 2.1
2.2.3 Localised Forms of Plastic Deformation
2.2.4 Physical Nature of Shear Bands
Observation 2.2
2.3 Plastic Deformation in Polycrystals. 2.3.1 Mechanisms of Plastic Deformation and the Evolution of Internal Micro‐Stresses
Observation 2.3
Observation 2.4
2.3.2 Micro‐shear Bands Hierarchy and Their Macroscopic Effects
Observation 2.5
Observation 2.6
Observation 2.7
2.3.3 Physical Nature of Micro‐shear Bands in Polycrystals
2.3.4 Comments on ‘adiabatic’ Micro‐shear Bands
References
3 Incorporation of Shear Banding Activity into the Model of Inelastic Deformations
3.1 Plastic Deformation of Metallic Solids vis‐à‐vis the Continuum Mechanics
3.2 Hypothesis on the Extension of the RVE Concept
Observation 3.1
Hypothesis 3.1
3.3 Model of Shear Strain Rate Generated by Micro‐shear Bands
References
4 Basics of Rational Mechanics of Materials
4.1 A Recollection of Rational Continuum Mechanics
4.2 The Rational Theory of Materials – Epilogue
4.2.1 The Concept of the Deformable Body
4.2.2 The Motion of the Body
4.2.3 The Deformation of a Body
4.2.4 The Deformation Gradient
References
5 Continuum Mechanics Description of Shear Banding
5.1 System of Active Micro‐shear Bands Idealised as the Surface of Strong Discontinuity
Observation 5.1
5.1.1 On Finite Inelastic Deformations with High Lattice Misorientation
5.2 Macroscopic Averaging
References
6 Deformation of a Body Due to Shear Banding – Theoretical Foundations. 6.1 Basic Concepts and Relations of Finite Inelastic Deformation of Crystalline Solids
6.2 Continuum Model of Finite Inelastic Deformations with Permanent Lattice Misorientation
6.3 Basic Concepts and Relations of Constitutive Description – Elastic Range
6.4 The Yield Limit Versus Shear Banding – The ‘extremal surface’
Observation 6.1
References
7 The Failure Criteria Concerning the Onset of Shear Banding. 7.1 The Yield Condition for Modern Materials – the State of the Art
Definition 7.1
7.2 The Yield Condition for the Isotropic Materials Revealing the Strength Differential Effect
Hypothesis 7.1
7.3 Examples and Visualisations of the Particular Burzyński Failure Criteria
7.3.1 Ellipsoidal Failure Surface
7.3.2 Paraboloid Failure Surfaces
7.4 Remarks on the Extension Including Anisotropic Materials
References
8 Constitutive Description of Viscoplasticity Accounting for Shear Banding
8.1 The Model of Plastic Flow with Nonlinear Development of Kinematic Hardening
8.2 The Perzyna Viscoplasticity Model Accounting for Shear Banding
8.3 Identification of the Viscoplasticity Model
8.4 The Crystal Plasticity Modelling of Deformation Processes in Metals Accounting for Shear Banding
8.5 Viscoplastic Deformation of Nanocrystalline Metals
References
9 Conclusions. 9.1 Concluding Remarks. 9.1.1 Shear Banding‐Mediated Flow vis‐à‐vis Ductile Failure Analysis
9.1.2 Application of Peridynamic Numerical Simulations of Shear Banding Processes
References
Subject Index. b
c
d
e
f
g
i
k
m
n
o
p
r
s
t
v
y
z
Name Index. a
b
c
d
e
f
g
h
i
j
k
l
m
n
o
p
q
r
s
t
v
w
y
z
WILEY END USER LICENSE AGREEMENT
Отрывок из книги
Ryszard B. Pęcherski
.....
Source: Korbel and Szyndler 2010. Copyright of Włodzimierz Bochniak.
The paper (Bochniak et al. 2006) deals with the KOBO method of forming bevel gears from structural steel. The study's subject is a single operation of complex forging on a press with the reversible rotating die displayed in Figure 1.6. Comparing the KOBO method's forging process with the conventional ones reveals that the punch pressure and temperature are considerably lower. Despite such a reduction, the products represent the die shape correctly, the structure becomes homogeneous, and the material has desired mechanical properties (see Figure 1.4) containing an example of the regular bevel gear obtained by the KOBO method from structural steel at the studied temperature of 850 °C (Bochniak et al. 2006). Let us also recall a nice illustrative picture of the bevel gear displayed on the book's cover. The image provided kindly by the editorial staff comes from other sources, and the shown example of bevel gear is the traditional milling effect.
.....