The Rheology Handbook
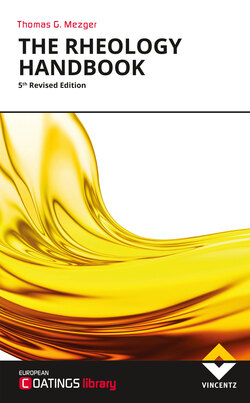
Реклама. ООО «ЛитРес», ИНН: 7719571260.
Оглавление
Thomas Mezger. The Rheology Handbook
Foreword. Why was this book written?
How did this book come into existence?
What is the target audience for this book? For which industrial branches will it be most interesting?
1Introduction. 1.1Rheology, rheometry and viscoelasticity. a) Rheology
b) Rheometry
c) Appendix
d) Information for “Mr. and Ms. Cleverly”
1.2Deformation and flow behavior
Experiment 1: Behavior of mineral oil , plasticine, and steel
Experiment 2: Playing with “bouncing putty ” (some call it “Silly Putty”)
Experiment 3: Do the rods remain in the position standing up straight?
Summary
1.3References
2Flow behavior and viscosity
2.1Introduction
2.2Definition of terms
Experiment 1: The stack of beer mats
2.2.1Shear stress
2.2.2Shear rate
a) Definition of the shear rate using differential variables
b) Calculation of shear rates occurring in technical processes
1) Coating processes: painting, brushing, rolling or blade-coating
Examples. 1a) Painting with a brush:
1b) Buttering bread:
1c) Applying emulsion paint with a roller
2) Flow in pipelines, tubes and capillaries
Examples. 2a) Pipeline transport of automotive coatings [2.8][2.9]
2b) Drinking water supply, transport in pipelines [2.10]
2c) Filling bottles using a filling machine (e. g. drinks in food industry):
2d) Squeezing an ointment out of a tube (e. g. pharmaceuticals):
2e) Filling ointment into tubes using a filling machine (e. g. medicine):
2f) Transport process of a stucco gypsum suspension during production of architectural plates [2.11]
3) Sedimentation of particles in suspensions
Examples. 3a) Sedimentation of sand particles in water
3b) Sedimentation of sand particles in water containing a thickener
2.2.3Viscosity
a) Shear viscosity
b) Kinematic viscosity
Example. Conversion of the values of kinematic viscosity and shear viscosity
2.3Shear load-dependent flow behavior
Experiment 2: The double-tube test, or the contest of the two fluids (see Figure 2.4)
2.3.1Ideal-viscous flow behavior. a) Viscosity law
Examples of ideal-viscous materials
b) The dashpot model
Ideal-viscous flow behavior, explained by the behavior of a dashpot. 1) When under load
2) When removing the load
Summary: Behavior of the dashpot model
Comparison: Dashpot fluid and viscosity law
Note: Viscous behavior, viscous shear-heating , and lost deformation energy
2.4Types of flow illustrated by the. Two-Plates model
2.5References
3Rotational tests
3.1Introduction
3.2Basic principles. 3.2.1Test modes-controlled shear rate (CSR) and controlled shear stress (CSS), raw data and rheological parameters. a) Tests with controlled shear rate (CSR tests)
b) Tests with controlled shear stress (CSS tests)
Examples from nature
3.3Flow curves and viscosity functions
3.3.1Description of the test. Preset
a) Extended test programs (including intervals at rest, for temperature equilibration, and pre-shear)
Example 1: Testing resins
Example 2: Testing chocolate melts (at the test temperature T = +40 °C)
b) Time-dependent effects, steady-state viscosity and transient viscosity (at low shear rates)
Illustration, using the Two-Plates model (see also Figure 2.9, no.5)
Example 1: Useful measuring point duration to avoid transient effects
Example 2: Suggestions for test profile presets, with γ ̇ (t) as a ramp function. 1) Linear preset
2) Logarithmic preset
Example 3: Occurrence of a “transient viscosity peak” when presetting a too short measuring point duration in the low-shear range (e. g. when testing dispersions and gels)
Summary: When testing dispersions and gels
3.3.2Shear-thinning flow behavior
Examples of shear-thinning materials
Note 1: Shear-thinning, time-dependent and independent of time
Note 2: Very simple evaluation methods
3.3.2.1Structures of polymers showing shear-thinning behavior. The entanglement model
a) Shear range 1 at low-shear conditions: the “low-shear range”
Superposition of two processes
Summary of this superposition
1) Zero-shear viscosity in mathematical notation
2) Dependence of η0 on the polymer concentration c
3) Dependence of η0 on the average molar mass M [3.9][3.10]
b) Shear range 2 at medium shear rates: the “flow range”
c) Shear range 3 at high-shear conditions: the “high-shear range”
Infinite-shear viscosity in mathematical notation
3.3.2.2Structures of dispersions showing shear-thinning behavior
3.3.3Shear-thickening flow behavior. Experiment 3.1: Shear-thickening of a plastisol dispersion (see Figure 3.14)
Examples of shear-thickening materials
Example 1: Plastisols in automotive industry
Example 2: Paper coatings
Example 3: Hair shampoos containing surfactant superstructures
Example 4: Shear-induced or flow-induced dilatant behavior of elastomers
Example 5: “Nano-fluids” or “smart fluids” for shock-resistant or bullet-proof materials
Example 6: Turbulent flow of water
3.3.3.1Structures of uncrosslinked polymers showing. shear-thickening behavior
3.3.3.2Structures of dispersions showing shear-thickening behavior
Illustration, using the Two-Plates model (see Figure 2.1)
Example: Creaming effect of pharmaceuticals and cosmetic products
3.3.4Yield point. Experiment 3.2: Squeezing toothpaste out of the tube (see Figure 3.20)
Experiment 3.3: Sticking rods into hand cream and silicone
3.1.2.1.3Examples of materials which may show a yield point
3.3.4.1Yield point determination using the flow curve diagram
3.3.4.2Further information on yield points. 3.3.4.2.1a) Time-dependence of the yield point
3.3.4.2.2b) Interaction forces and network of forces
3.3.4.2.3c) Plastic behavior
3.3.4.2.4Example 1: Plastic behavior of metals for cold forging processes
3.3.4.2.5Example 2: Plastic deformation of the landscape and soil flow (solifluction )
3.3.4.2.6Example 3: Plastic land subsidence caused by mining or dike construction
3.3.4.2.7Example 4: Plastic flow of debris and mud avalanches in the mountains
3.3.4.2.8Illustration, using the Two-Plates model (see Figure 2.9: no. 4)
3.3.4.2.9Examples of plastic materials
3.3.4.2.10Summary
3.3.4.2.11Note by the way
3.3.4.2.12d) Practical example: Yield point and wet layer thickness of a coating
3.3.4.2.13Summary
3.3.4.2.14Examples
3.3.5Overview: flow curves and viscosity functions
3.1.2.1.1a) Diagrams on a linear scale
3.1.2.1.2b) Diagrams on a logarithmic scale
3.1.2.1.3c) Three-dimensional diagrams of flow curves and viscosity functions
3.3.6Fitting functions for flow and viscosity curves
3.3.6.1Model function for ideal-viscous flow behavior. according to Newton
3.3.6.2Model functions for shear-thinning and shear-thickening flow behavior
3.3.6.2.1a) Ostwald/de Waele, or power-law: τ = c ⋅ γ ̇ p
3.3.6.2.2b) Steiger/Ory: γ ̇ = c1 ⋅ τ + c2 ⋅ τ3
3.3.6.2.3c) Eyring/Prandtl/Ree or Ree-Eyring: γ ̇ = c1 ⋅ sinh(τ/c2)
3.3.6.3Model functions for flow behavior with zero-shear viscosity and infinite-shear viscosity
3.3.6.3.1a) Cross:
3.3.6.3.2b) Carreau:
3.3.6.3.3c) Krieger/Dougherty:
3.3.6.3.4d) Vinogradov/Malkin:
3.3.6.3.5e) Ellis and Sisko:
3.3.6.3.6f) Exponential or e-function: η( γ ̇ ) = η0 ⋅ exp (–c ⋅ γ ̇ )
3.3.6.3.7g) Philipps/Deutsch:
3.3.6.3.8h) Reiner/Philippoff:
3.3.6.4Model functions for flow curves with a yield point
3.3.6.4.11) “Yield stress” (YS) using a straight line through two measuring points
3.3.6.4.2Example: with nH = 100, nL = 10, DRH = 50, DRL = 40, then: YS is read off as 38. 3.3.6.4.32) “Plasticity index” (PI)
3.3.6.4.4Example: with nH, nL, DRH, DRL and YS as above, then:
3.3.6.4.5b) Casson:
3.3.6.4.6c) Herschel/Bulkley:τ = τHB + c ⋅ γ ̇ p
3.3.6.4.7d) Windhab:τ = τ0 + (τ1 - τ0) ⋅ [1 – exp (- γ ̇ / γ ̇ *)] + η∞ ⋅ γ ̇
3.3.6.4.8e) Tscheuschner:τ = τ0 + c1 ⋅ γ ̇ p + c2 ⋅ γ ̇
3.3.6.4.9f) Polynomials
3.3.6.4.10Example: third order polynomial τ = c1 + c2 ⋅ γ ̇ + c3 ⋅ γ ̇ 2 + c4 ⋅ γ ̇ 3
3.3.7The effects of rheology additives. in water-based dispersions
3.1.2.1.1a) Water-based dispersions containing clay as the thickening agent
3.1.2.1.2b) Water-based dispersions containing dissolved polymer as the thickening agent
3.1.2.1.3d) Water-based polymer dispersion containing an associative thickener
3.4Time-dependent flow behavior and. viscosity function
3.4.1Test description. 3.1.2.1.1Preset
3.1.2.1.2Measuring result
3.4.2Time-dependent flow behavior of samples. showing no hardening
3.1.2.1.1Example: Testing lubricating grease (according to DIN 51810-1)
3.4.2.1Structural decomposition and regeneration (thixotropy and rheopexy) 3.4.2.1.1a) Thixotropic behavior. 3.4.2.1.2Experiment 3.4: Shaking bottles containing ketchup and paraffin oil
3.4.2.1.3Examples of thixotropic materials
3.4.2.1.4b) Non-thixotropic behavior. 3.4.2.1.5Experiment 3.5: Stirring yogurt
3.4.2.1.6c) Rheopectic behavior
3.4.2.1.7Examples of rheopectic materials
3.4.2.1.8Example: Testing a dispersion under the following conditions
3.4.2.2Test methods for investigating thixotropic behavior
3.4.2.2.1a) Step test consisting of three intervals
3.4.2.2.2Example 1: Presetting shear rates for all intervals
3.4.2.2.3Example 2: Presetting shear stresses for all intervals
3.4.2.2.4Example
3.4.2.2.5Example (to method M3): Testing PVC plastisol pastes
3.4.2.2.6Example (to method M4): Comparison of two coatings
3.4.2.2.7b) Flow curves and hysteresis area (for evaluating thixotropic behavior)
3.4.2.2.8Example 1: Preset of the shear rate
3.4.2.2.9Example 2: Preset of the shear stress
3.4.2.2.10Measuring result
3.4.2.2.11c) Very simple evaluation methods (for evaluating thixotropic behavior)
3.4.3Time-dependent flow behavior of samples. showing hardening
3.1.2.1.1a) Gelation time and gel time, gel point and gelation point
3.1.2.1.2Example 1: Testing epoxy resins
3.1.2.1.3Example 2: The isothermal viscosity development of reactive resin mixtures (acc. to DIN 16945)
3.1.2.1.4Example 3: The gelation time of reaction resins, when reaching the thousandfold viscosity value
3.1.2.1.5b) Comparison of controlled shear rate (CSR) , and controlled shear stress (CSS) tests
3.5Temperature-dependent flow behavior and viscosity function
3.5.1Test description
3.5.2Temperature-dependent flow behavior of samples showing no hardening
3.5.3Temperature-dependent flow behavior of samples showing hardening
3.1.2.1.1Examples (here in alphabetic order):
3.5.4Fitting functions for curves of the. temperature-dependent viscosity
3.1.2.1.1a) Arrhenius relation, flow activation energy EA, and Arrhenius curve
3.1.2.1.2b) Viscosity/temperature shift factor aT, and Arrhenius plot
3.1.2.1.3Example: Calculation of flow activation energy and viscosity/temperature shift factor of a mineral oil, and determination of viscosity values at further temperatures
3.6Pressure-dependent flow behavior and viscosity function
3.2.1.1.1Viscosity/pressure shift factor ap
3.2.1.1.2Example 1: Calculation of viscosity/pressure coefficient and shift factor of a mineral oil, and determination of viscosity values at further pressures
3.2.1.1.3Example 2: Calculation of the viscosity/pressure coefficient of a crude oil
3.7References
4Elastic behavior and. shear modulus
4.1Introduction
4.2Definition of terms
4.2.1Deformation and strain
4.2.2Shear modulus
4.3Shear load-dependent. deformation behavior. 4.2.1.1.1Experiment 4.1: Playing with a spiral spring
4.2.1.1.2Experiment 4.2: Playing with a steel ball
4.3.1Ideal-elastic deformation behavior. 4.1.2.1.1a) Elasticity law
4.1.2.1.2b) The spring model
4.1.2.1.3Ideal-elastic behavior, explained by the behavior of a spring. 4.1.2.1.41) When under load
4.1.2.1.52) When removing the load
4.4Yield point determination using the shear stress/deformation diagram. 4.2.1.1.1a) Yield point at the limit of the linear-elastic range, using a single fitting line
4.2.1.1.2b) Yield point by the “tangent crossover method”, using two fitting lines
4.2.1.1.3c) Yield zone (flow transition range)
4.2.1.1.4d) Yield point and flow point in the shear stress/deformation diagram
4.2.1.1.5e) Yield point by the method of maximum deviation from the fitting line
4.5References
5Viscoelastic behavior
5.1Introduction
5.2Basic principles. 5.2.1Viscoelastic liquids according to Maxwell. 5.1.2.1.1Experiment 5.1: The thickened liquid in a glass beaker
5.1.2.1.25.2.1.1The Maxwell model
5.1.2.1.3a) Viscoelastic flow behavior , illustrated by use of the Maxwell model (see Figure 5.2): 5.1.2.1.41) Before applying a load
5.1.2.1.52) When under load
5.1.2.1.63) When removing the load
5.1.2.1.7b) Differential equation according to the Maxwell model
5.1.2.1.85.2.1.2Examples of the behavior of VE liquids in practice. 5.1.2.1.9a) Die swell, or post-extrusion swelling effect (see Figure 5.3) 5.1.2.1.10Experiment 5.2: Extrusion, using a small toy extruder, producing spaghetti-like strands
5.1.2.1.11Examples: Materials showing die swell
5.1.2.1.12b) The Weissenberg effect when stirring. 5.1.2.1.13Experiment 5.3: The two stirrer vessels, containing water and a polymer solution (Figure 5.4)
5.1.2.1.14Examples: Materials showing the Weissenberg effect
5.1.2.1.15c) Tack and stringiness when performing coating processes
5.1.2.1.16d) Mouth sensation
5.2.2Viscoelastic solids according to Kelvin/Voigt. 5.1.2.1.1Experiment 5.4: Breaking behavior of a silicone rubber with a low degree of crosslinking
5.1.2.1.2Experiment 5.5: Comparison of two rubber balls
5.1.2.1.35.2.2.1 The Kelvin/Voigt model
5.1.2.1.4a) Viscoelastic behavior, illustrated by use of the Kelvin/Voigt model (see Figure 5.7): 5.1.2.1.51) Before applying a load
5.1.2.1.62) When under load
5.1.2.1.73) When removing the load
5.1.2.1.8b) Differential equation according to the Kelvin/Voigt model
5.1.2.1.95.2.2.2Examples of the behavior of VE solids in practice
5.1.2.1.10Elastic behavior
5.1.2.1.11Viscous behavior
5.1.2.1.12Examples from daily practice: 5.1.2.1.13a) Rubber buffers, and damping of mechanical vibrations
5.1.2.1.14b) Noise protection, and damping of sound waves
5.1.2.1.15c) Car tires, deformation energy and viscous heating
5.1.2.1.16d) Automotive bumpers
5.1.2.1.17e) Shock absorbers, and the Kelvin/Voigt model
5.1.2.1.18f) Equipment for sportive activities, and viscoelastic properties
5.1.2.1.19g) Biological materials, and synthetic “bio-materials”
5.1.2.1.20h) Haptic perception (haptics) of the consistency of a material, or of a system
5.3Normal stresses
5.4References
6Creep tests
6.1Introduction
6.2Basic principles. 6.2.1.1.1Experiment 6.1: Creep and reverse creep of a hot-melt adhesive
6.2.1Description of the test. 6.1.2.1.1Preset: Shear stress step function τ(t), see Figure 6.1
6.1.2.1.2Example: Test preset for a polymer sample
6.2.2Ideal-elastic. behavior
6.2.3Ideal-viscous. behavior
6.2.4Viscoelastic. behavior
6.3Analysis. 6.3.1Behavior of the molecules
6.1.2.1.1a) At rest, before the step in stress
6.1.2.1.2b) Under constant stress, in the creep phase
6.1.2.1.3c) After releasing the stress, in the creep recovery phase
6.3.2The Burgers model
6.3.3Curve discussion
6.1.2.1.1a) Creep curve
6.1.2.1.2b) Creep recovery curve
6.3.4Definition of terms. 6.3.4.1Zero-shear viscosity
6.3.4.1.1a) Determination of the value of zero-shear viscosity via creep curves
6.3.4.1.2b) Zero-shear viscosity and average molar mass
6.3.4.1.3c) Comparison: different methods to determine η0
6.3.4.2Creep compliance , and creep recovery compliance
6.3.4.2.1a) Instantaneous compliance
6.3.4.2.2b) Creep recovery, and equilibrium compliance
6.3.4.2.3c) Determination of the limiting value of the LVE range
6.3.4.3Retardation time
6.3.4.3.1a) Retardation time Λ in the Kelvin/Voigt model
6.3.4.3.2b) Retardation time Λ in the Burgers model
6.3.4.4Retardation time spectrum
6.3.4.4.1a) Generalized Kelvin/Voigt model
6.3.4.4.2b) Discrete retardation time spectrum
6.3.4.4.3c) Continuous retardation time spectrum
6.3.5Data conversion
6.1.2.1.1Example: Conversion of creep test data to frequency sweep data
6.3.6Determination of the molar mass distribution
6.4Determination of the yield point. via creep tests
6.2.1.1.1Example: Determination of the yield point of a bentone suspension
6.5References
7Relaxation tests
7.1Introduction
7.2Basic principles. 7.2.1Description of the test
7.1.2.1.1Example: Test preset for a polymer sample
7.2.2Ideal-elastic behavior. 7.1.2.1.1Experiment 7.1: Twisting an eraser
7.2.3Ideal-viscous behavior
7.2.4Viscoelastic behavior. 7.1.2.1.1Experiment 7.3: Rotating a spatula in a silicone polymer
7.3Analysis. 7.3.1Behavior of the molecules
7.1.2.1.1a) At rest, before the step in strain
7.1.2.1.2b) Performing the step in strain
7.1.2.1.3c) In the stress relaxation phase
7.3.2Curve discussion. 7.1.2.1.1a) Before the effective strain step
7.1.2.1.2b) During the strain step
7.1.2.1.3c) Stress relaxation curve
7.3.3Definition of terms. 7.3.3.1Relaxation modulus
7.3.3.1.1a) Instantaneous shear modulus
7.3.3.1.2b) Equilibrium shear modulus
7.3.3.1.3c) Determination of the limiting value of the LVE range
7.3.3.2Relaxation time
7.3.3.3Relaxation time spectrum
7.3.3.3.1a) Generalized Maxwell model
7.3.3.3.2b) Discrete relaxation time spectrum
7.3.3.3.3c) Continuous relaxation time spectrum
7.3.4Data conversion
7.1.2.1.1Examples. 7.1.2.1.21) Relaxation modulus G(t) frequency functions G’ & G’’(ω)
7.1.2.1.32) Frequency functions G’ & G’’(ω) relaxation modulus G(t)
7.1.2.1.43) Frequency functions G’ & G’’ at high ω-values G(t) or J(t)
7.1.2.1.54) Frequency functions G’ & G’’ at low ω-values relaxation modulus G(t)
7.1.2.1.65) Creep compliance J(t) relaxation modulus G(t)
7.3.5Determination of the molar mass. distribution
7.4References
8Oscillatory tests
8.1Introduction
8.2Basic principles
8.2.1Ideal-elastic behavior
8.2.2Ideal-viscous behavior
8.2.3Viscoelastic behavior. 8.1.2.1.1Preset
8.1.2.1.2Measuring result
8.2.4Definition of terms. 8.1.2.1.1a) Complex shear modulus, storage modulus, loss modulus, and loss factor
8.1.2.1.2 Note 1: The sol/gel transition point (gel point), and tanδ
8.1.2.1.3Note 2: Tack and stringiness, and tanδ
8.1.2.1.4Example: Stringiness of adhesives, and tanδ
8.1.2.1.5Note 3: Meltability of cheese and tanδ
8.1.2.1.61) Notation of G’ and G’’ in terms of sine and cosine functions
8.1.2.1.72) Vector diagram illustrating G*, G’, G’’ and tanδ
8.1.2.1.8b) The complex viscosity , its real and imaginary parts
8.1.2.1.91) Notation of η’ and η’’ in terms of sine and cosine functions. 8.1.2.1.10Real part of the complex viscosity
8.1.2.1.11Imaginary part of the complex viscosity
8.1.2.1.122) Vector diagram illustrating η*, η’, η’’ and tanδ
8.1.2.1.13Note 1: Elastic behavior in terms of G’ or η’’, and viscous behavior as G’’ or η’
8.1.2.1.14Note 2: The term (absolute) dynamic viscosity
8.1.2.1.15Note 3: Unusual terms used for η’ and η’’
8.1.2.1.16c) Presentation of the parameters in complex notation
8.1.2.1.17d) Conversion between shear deformation (or shear strain) and shear rate (or strain rate)
8.2.5The test modes controlled shear strain and controlled shear stress, raw data and rheological parameters
8.1.2.1.1a) Tests with controlled shear strain, also called “controlled shear deformation” CSD
8.1.2.1.2b) Tests with controlled shear stress (CSS tests)
8.1.2.1.3c) Recommendation: Scaling of diagrams showing measuring curves
8.1.2.1.4 d) Recommendation: Specification of parameters in test protocols (data tables)
8.3Amplitude sweeps
8.3.1Description of the test
8.1.2.1.1Note 2: Three-dimensional diagrams of amplitude sweeps at different temperatures
8.1.2.1.2Note 3: Test preparation: Thermal-stability time of polymer melts
8.1.2.1.3a) Gel-like state or solid state, if G’ > G’’
8.1.2.1.4b) Liquid state like fluids or sols, if G’’ > G’
8.1.2.1.5c) At the gel point, if G’ = G’’ in the LVE range
8.3.2Limiting value of the LVE range
8.1.2.1.1a) Visual or manual analysis
8.1.2.1.2b) Automatic analysis using a software analysis program
8.3.2.1Limiting value of the LVE range in terms of the shear strain
8.3.2.1.1Example 1 (to Note 3): Types of structures of lube greases, and the G’’ peak [8.77]
8.3.2.1.2Example 2 (to Note 3): Comparison of foam systems via the G’’-maximum [8.76]
8.3.2.1.3Example 3 (to Note 3): Solid polymers, formation of micro-cracks, and the G’’ curve
8.3.2.1.4Example 4 (to Note 3): Two maxima in the G’’ curve of a colloidal suspension with a gel-like structure, [8.79]
8.3.2.2Limiting value of the LVE range in terms of the shear stress
8.3.3Determination of the yield point and the flow point by amplitude sweeps
8.3.3.1Yield point or yield stress τy
8.3.3.1.1a) Visual or manual analysis of the yield point
8.3.3.1.2b) Automatic analysis of the yield point using a software program
8.3.3.2Flow point or flow stress τf
8.3.3.3Yield zone between yield point and flow point
8.3.3.3.1Example: The flow point and the flow transition index of lube grease (acc. to DIN 51810-2) [8.19][8.77]
8.3.3.4Evaluation of the two terms yield point and flow point
8.3.3.5Measuring programs in combination with amplitude sweeps
8.3.3.5.1Example 1: Amplitude sweep upwards and downwards for testing plastisols in. automotive industry
8.3.3.5.2Example 2: Combination of rotation, amplitude sweep and a shear phase for testing automotive adhesives
8.3.4Frequency-dependence of amplitude sweeps
8.1.2.1.1Example 1 (to Note 3): An adhesive, flowing at high frequencies but not at low ones
8.1.2.1.2Example 2 (to Note 3): Offset printing inks, solid at low frequencies but liquid at higher ones
8.3.5SAOS and LAOS tests, and Lissajous diagrams. 8.1.2.1.1a) Linear behavior in the LVE range and SAOS tests
8.1.2.1.2b) Non-linear behavior in the NL range and LAOS tests
8.1.2.1.3Examples of applications: complex materials
8.4Frequency sweeps
8.2.1.1.1Experiment 8.1: Bouncing or spreading of putty (PDMS)
8.2.1.1.21) Short-term behavior
8.2.1.1.32) Long-term behavior
8.4.1Description of the test
8.1.2.1.1Measuring result
8.4.2Behavior of uncrosslinked polymers (solutions and melts)
8.4.2.1The single Maxwell model for polymers showing a narrow molar mass distribution (MMD)
8.4.2.1.1a) Discussion of curves of polymers (solutions or melts) showing a narrow MMD
8.4.2.1.2b) Interpretation of frequency sweeps of uncrosslinked polymers
8.4.2.2The generalized Maxwell model for polymers showing a wide MMD
8.4.2.2.1a) Curve discussion for polymers showing a wide MMD (see Figure 8.19):
8.4.2.2.2b) Comparison of polymers concerning molar mass and MMD
8.4.2.2.3c) Optional methods to analyze frequency sweeps on polymers
8.4.3Behavior of crosslinked polymers
8.1.2.1.1a) Polymers showing a high degree of crosslinking
8.1.2.1.2Experiment 8.2: Bouncing rubber balls, and the damping factor tanδ
8.1.2.1.3b) Polymers showing a low degree of crosslinking
8.1.2.1.4c) Comparison of crosslinked and uncrosslinked polymers
8.4.4Behavior of dispersions and gels
8.1.2.1.1a) Structural strength at rest, dispersion stability, yield point, dimension stability, and frequency sweeps
8.1.2.1.2Example 1: Stability of uncured PU adhesives, evaluation via frequency sweeps
8.1.2.1.3Example 2: Specification of dispersion stability in terms of G’ instead of a yield point
8.1.2.1.4Example 3: Low-shear test for varnishes, instead of yield point tests via rotation
8.1.2.1.5b) Dispersion stability outside the LVE range. 8.1.2.1.6Example: Transport stability of dispersions
8.4.5Comparison of superstructures using frequency sweeps
8.4.6Multiwave test
8.4.7Data conversion
8.5Time-dependent behavior at. constant dynamic-mechanical and. isothermal conditions
8.5.1Description of the test
8.5.2Time-dependent behavior of samples showing. no hardening
8.5.2.1Structural decomposition and regeneration (thixotropy and rheopexy) 8.5.2.1.1a) Thixotropic behavior
8.5.2.1.2b) Rheopectic behavior
8.5.2.2Testing methods for investigating thixotropic behavior. 8.5.2.2.1a) Step test consisting of three intervals
8.5.2.2.2Example 1
8.5.2.2.3Note 1: Optimizing the step test conditions
8.5.2.2.4Note 2: Advantages of oscillatory tests over rotational tests
8.5.2.2.5Optional methods to analyze structural regeneration
8.5.2.2.6Example (to method M5): Comparison of two coatings
8.5.2.2.7b) Step test consisting of three intervals: oscillation/rotation/oscillation (ORO-test)
8.5.2.2.8Example of a preset
8.5.2.2.9c) Evaluating rheopectic behavior: step test consisting of three intervals in oscillation
8.5.3Time-dependent behavior of samples. showing hardening
8.1.2.1.1a) The onset of curing, and development of a chemical crosslinking reaction
8.1.2.1.2b) The sol/gel transition point, gel time, and gel point
8.1.2.1.3c) Further Notes and Examples. 8.1.2.1.4Eample 1: Testing an epoxy resin
8.1.2.1.5Example 2: Testing a solid coating layer after curing
8.1.2.1.6Example 3: The gelation time of reaction resins, when reaching the thousendfold of the G‘-value
8.6Temperature-dependent behavior at. constant dynamic mechanical conditions
8.6.1Description of the test
8.6.2Temperature-dependent behavior of samples. showing no hardening
8.6.2.1Temperature curves and structures of polymers
8.6.2.1.1a) Amorphous polymers
8.6.2.1.2b) Partially crystalline polymers
8.6.2.1.3Temperature curves of partially crystalline polymers (see Figure 8.40)
8.6.2.1.4c) Crosslinked polymers
8.6.2.2Temperature-curves of dispersions and gels. 8.6.2.2.1a) Softening, melting, solidification, crystallization, and freezing temperature
8.6.2.2.2b) Freeze-thaw-cycle tests for testing temperature stability of emulsions
8.6.3Temperature-dependent behavior of samples. showing hardening
8.1.2.1.1a) Onset of curing, and development of a chemical crosslinking reaction
8.1.2.1.2b) Melting temperature, sol/gel transition temperature, gel temperature and gel point
8.1.2.1.3c) The minimum viscosity
8.1.2.1.4d) Further Notes and Examples
8.1.2.1.5Example 2: The gelation temperature of reaction resins, when reaching the thousendfold of the G‘-value (or alternatively: value of the complex viscosity)
8.6.4Thermoanalysis (TA)
8.1.2.1.1a) DSC (differential scanning calorimetry)
8.1.2.1.2b) OIT (oxidative induction time)
8.1.2.1.3c) TG (thermogravimetry)
8.1.2.1.4d) TMA (thermo-mechanical analysis)
8.1.2.1.5e) DMA (dynamic-mechanical analysis)
8.7Time/temperature shift
8.7.1Temperature shift factor according to the WLF method
8.1.2.1.1a) Horizontal shift factor aT and the master curve
8.1.2.1.2 Example 1: Shifting the frequency-dependent parameters G’, G’’, G*, and |η*|
8.1.2.1.3Example 2: Shifting shear rate-dependent parameters
8.1.2.1.4Example 3: Shifting time-dependent parameters
8.1.2.1.5b) Time/temperature shift using the WLF relation
8.1.2.1.6The WLF shift factor
8.1.2.1.7c) Determination of the individual shift factors aTi. 8.1.2.1.81) Manual determination using the WLF diagram
8.1.2.1.9Example 1 (second section): Determination of the shift factors of the curves of G’ and G’’ at selected temperatures
8.1.2.1.10Example 2 (first section): Determination of the shift factors of the available measuring data of η0
8.1.2.1.11Example 2 (second section): Determination of the shift factors of η0-curves at selected temperatures
8.1.2.1.122) Automatic determination of aT and bT using an analysis software
8.1.2.1.13Example 3: Acoustic damping behavior of technical rubber
8.1.2.1.14d) Inverse master curve
8.1.2.1.15 e) Data conversion
8.8The Cox/Merz relation
8.2.1.1.1Scope of the Cox/Merz relation
8.9Combined rotational and oscillatory tests. 8.9.1Presetting rotation and oscillation in series
8.1.2.1.1Example 1: Test consisting of three intervals in the form of an O-R-O series
8.1.2.1.2Example 2: Test with seven intervals in series to get a fast overview (as a “fingerprint”)
8.9.2Superposition of oscillation and rotation
8.1.2.1.1Example 1: Testing leveling behavior of an emulsion paint by superposition of O & R
8.1.2.1.2 Description of the test. 8.1.2.1.3 1) Pre-test
8.1.2.1.42) Sole oscillation
8.1.2.1.53) Superposition of O & R
8.1.2.1.6Practical example (to Example 1): Emulsion paint (see Table 8.9)
8.1.2.1.7Example 2: Drilling fluids at pulsing flow conditions
8.10References
9Complex behavior, surfactant systems
9.1Surfactant systems. 9.1.1Surfactant structures and micelles. 9.1.2.1.1a) Surfactant molecules
9.1.2.1.2b) Superstructures of surfactants (micelles) in aqueous solutions, dispersions and gels
9.1.2.1.3c) Spherical micelles
9.1.2.1.4d) Rod-like, cylindrical and worm-like micelles
9.1.2.1.5e) Planar sheet micelles (lamellae)
9.1.2.1.6Single bilayers of surfactants
9.1.2.1.7Example: Bio-membranes
9.1.2.1.8Multiple layer systems of bilayer lamellae
9.1.2.1.9f) Vesicles as hollow spheres showing a single surfactant bilayer
9.1.2.1.10Example 1: Biological vesicles, liposomes
9.1.2.1.11Example 2: Vesicle systems as “capsules in the capsule”
9.1.2.1.12Example 3: Microspheres or microcapsules in food
9.1.2.1.13Example 4: “Self-healing” or self-repairing coatings
9.1.2.1.14Example 5: Functional coatings with a reversibly switchable wettability
9.1.2.1.15Vesicles showing multiple surfactant bilayers
9.1.2.1.16Comment: Vesicles and transporters in bioscience
9.1.2.1.17Example: SEDDS (self-emulsifying drug delivery systems) used as drug transporters
9.1.2.1.18g) Complex superstructures
9.1.2.1.19h) Micelle structures in the. sol-state and in the gel-state
9.1.2.1.20Example 1: Hydrogels used for reproduction of artificial tissues which are similar to biological ones [9.19]
9.1.2Emulsions
9.1.2.1.1a) Oil-in-water emulsions (o/w)
9.1.2.1.2Examples: o/w emulsions
9.1.2.1.3b) Water-in-oil emulsions (w/o)
9.1.2.1.4Examples: w/o emulsions
9.1.2.1.5 c) w/o/w and o/w/o emulsions
9.1.3Mixtures of surfactants and polymers, polymers containing surfactant components
9.1.2.1.1Example 1: Surfactants for stabilizing latex particles in a water-based dispersion
9.1.2.1.2Example 2: Surfactants building bridges between polymer molecules
9.1.2.1.3Example 3: Associative. thickeners of dispersions as polymers containing surfactant components
9.1.2.1.4Example 4: Dispersions containing. associative polymers and surfactants
9.1.2.1.5Example 5: Bio-materials, spider silk via hydrophilic and hydrophobic zones of proteins
9.1.2.1.6E5a) Proteins in the state of storage within the body of a spider, in the form of mono- disperse micelles in an aqueous solution
9.1.2.1.7E5b) Destabilization and aggregation of protein micelles
9.1.2.1.8E5c) Fiber formation by spontaneous self-organization of the proteins during the spinning process
9.1.2.1.9Mechanical properties of spinning fibers, and their environmental sustainability
9.1.2.1.10Example 6: Mucus in the human body
9.1.4Applications of surfactant systems
9.1.2.1.1Consumer and home care products, detergents
9.1.2.1.2Personal care, health and beauty care products, cosmetics
9.1.2.1.3Life sciences, pharmaceuticals, bio-tech
9.1.2.1.4Food technology
9.1.2.1.5Surface treatment, paints and “smart coatings”
9.1.2.1.6Petrochemical industry, mining, transportation in pipe lines
9.1.2.1.7Agrochemicals, crop science
9.2Rheological behavior of. surfactant systems
9.2.1.1.1Note: Surfactants, and measurement of the rheological behavior at interfaces
9.2.1Typical shear behavior. 9.1.2.1.1Ideal-viscous flow behavior
9.1.2.1.2Shear-thinning flow behavior
9.1.2.1.3Viscoelastic behavior
9.1.2.1.4Behavior of viscoelastic liquids
9.1.2.1.5Behavior of viscoelastic solids, gel-like structures
9.1.2.1.6Time-dependent structural regeneration , and thixotropic behavior
9.2.2Shear-induced effects, shear-banding and “rheo chaos ”
9.1.2.1.1a) Reasons for shear-induced structures
9.1.2.1.2b) Effects on the flow type
9.1.2.1.3c) Results when measuring deformation and flow behavior
9.1.2.1.4Examples of materials which may show shear-banding
9.1.2.1.5Note: Rheo-optical observation of micelle structures in a flow field
9.1.2.1.6Example 1: Shear-induced structural modifications in colloidal protein dispersions [9.41]
9.1.2.1.7Example 2: Rheo-optical observation of flow velocity profiles
9.3References
10Measuring systems. 10.1Introduction
10.2Concentric cylinder measuring systems (CC MS) 10.2.1Cylinder measuring systems in general. 10.2.1.1Geometry of cylinder measuring systems showing a large gap
10.2.1.1.1Note: Materials used for cylinder measuring systems
10.2.1.2Operating methods
10.2.1.2.1a) Searle method
10.2.1.2.2b) Couette method
10.2.1.3Calculations
10.2.1.3.1 a) Shear stress in a large cylinder gap
10.2.1.3.2b) Shear rate in a large cylinder gap
10.2.1.3.3c) The viscosity in a large cylinder gap
10.2.2Narrow-gap concentric cylinder measuring systems according to ISO 3219
10.2.2.1Geometry
10.2.2.1.1a) The standard geometry: Ratio of the radii of cup and bob
10.2.2.1.2 Note 1: ISO specifies only the ratio of the radii
10.2.2.1.3Note 2: Denomination of the ratio of the radii as δcc (and not as δ)
10.2.2.1.4b) The standard geometry: Cylinder dimensions according to ISO and DIN
10.2.2.2Calculations
10.2.2.2.1a) The representative shear stress in a narrow cylinder gap
10.2.2.2.2Summary for practical users in order to select the optimal MS geometry
10.2.2.2.3b) The representative shear rate in a narrow cylinder gap
10.2.2.2.4Summary for practical users in order to select the optimal MS geometry
10.2.2.2.5Note: The shear rate range in the gap of an ISO cylinder MS
10.2.2.2.6c) The representative shear viscosity in a narrow cylinder gap
10.2.2.3Conversion between raw data and rheological parameters. 10.2.2.3.1a) Torque M and shear stress τ
10.2.2.3.2b) Rotational speed n and shear rate γ ̇
10.2.2.3.3c) Deflection angle φ and shear deformation γ
10.2.2.4Flow instabilities and secondary flow effects in. cylinder measuring systems
10.2.2.4.1a) Taylor vortices and the Ta number in the annular gap of a Searle cylinder MS [10.10]
10.2.2.4.2Example: Measurement of water using an ISO cylinder MS (at T = +20 °C)
10.2.2.4.3Calculation
10.2.2.4.4b) Reynolds number in the circular gap of a cylinder MS [10.16]
10.2.2.4.5Example: Measurement of water using an ISO cylinder MS (at T = +20 °C)
10.2.2.4.6Calculation
10.2.2.4.7Note: Critical values of the angular velocity
10.2.2.5Advantages and disadvantages of cylinder measuring systems. 10.2.2.5.1 a) Advantages
10.2.2.5.2b) Disadvantages
10.2.3Double-gap measuring systems (DG MS)
10.2.4High-shear cylinder measuring systems (HS MS)
10.1.2.1.1Example: High-shear cylinder measuring systems
10.1.2.1.2Note 1: Viscous heating at high shear rates
10.1.2.1.3Note 2: High-pressure capillary viscometers for testing at very high shear rates
10.3Cone-and-plate measuring systems (CP MS)
10.3.1Geometry
10.1.2.1.1Note 1: Optional specifications for angle units, degrees or rad
10.1.2.1.2Note 2: Transparent cone-and-plate systems
10.3.2Calculations. 10.1.2.1.1a) Shear stress in a CP gap
10.1.2.1.2Summary for practical users in order to select the optimal MS geometry
10.1.2.1.3b) Shear rate in a CP gap
10.1.2.1.4Example
10.1.2.1.5Summary for practical users in order to select the optimal MS geometry
10.1.2.1.6c) Viscosity in a CP gap
10.3.3Conversion between raw data. and rheological parameters. 10.1.2.1.1a) Torque M and shear stress τ
10.1.2.1.2b) Rotational speed n and shear rate γ ̇
10.1.2.1.3c) Deflection angle φ and the deformation γ
10.3.4Flow instabilities and secondary flow effects in. CP systems
10.3.5Cone truncation and gap setting
10.1.2.1.1Note: Exactly gap setting is essential and the required gap dimension has to be kept strictly on this value during the whole test
10.3.6Maximum particle size
10.3.7Filling of the cone-and-plate measuring system
10.3.8Advantages and disadvantages of cone-and-plate. measuring systems. 10.1.2.1.1a) Advantages
10.1.2.1.2 b) Disadvantages
10.1.2.1.3Note (to HSV): High-shear cone-and-plate viscometer, and “high-shear visosity”
10.4Parallel-plate measuring systems (PP MS)
10.4.1Geometry
10.1.2.1.1Note 1: Specifications of PP MS dimensions for testing polymer melts (ISO 6721-10)
10.1.2.1.2Note 2: Possible problems when selecting a too small plate distance
10.1.2.1.3Note 3: Transparent parallel-plate systems
10.4.2Calculations. 10.1.2.1.1a) Shear stress in a PP gap
10.1.2.1.2Summary for practical users in order to select the optimal MS geometry
10.1.2.1.3b) Shear rate in a PP gap
10.1.2.1.4Note: Comparing the measuring systems PP and CP in terms of the shear rates
10.1.2.1.5Summary for practical users in order to select the optimal MS geometry
10.1.2.1.6c) Viscosity in a PP gap
10.4.3Conversion between raw data and. rheological parameters. 10.1.2.1.1a) Torque M and mean shear stress τm
10.1.2.1.2b) Rotational speed n and mean shear rate γ ̇ m
10.1.2.1.3c) Deflection angle φ and mean shear deformation γm
10.4.4Flow instabilities and secondary flow effects. in a PP system
10.4.5Recommendations for gap setting. 10.1.2.1.1Note 1: Testing resins, polymer melts, and silicones (uncrosslinked PDMS)
10.1.2.1.2Note 2: Maximum particle size , and required gap setting
10.1.2.1.3Note 3: Special analysis is required when gap setting is less than 0.3 mm
10.4.6Automatic gap setting and automatic gap control. using the normal force control option. 10.1.2.1.1a) Target: Gap setting and gap control
10.1.2.1.2b) Target: Forced contact of sample and plates at a constant compression force, compression tests and shear test at a constant compression force or normal force
10.1.2.1.3c) Target: Compression-less but guaranteed contact between the sample and the plates
10.4.7Determination of the temperature gradient. in the sample
10.4.8Advantages and disadvantages of. parallel-plate measuring systems. 10.1.2.1.1a) Advantages
10.1.2.1.2b) Disadvantages
10.5Mooney/Ewart measuring systems (ME MS)
10.6Relative measuring systems
10.6.1Measuring systems with sandblasted, profiled. or serrated surfaces
10.6.2Spindles in the form of disks, pins, and spheres
10.1.2.1.1Summary: Using spindles, viscosity values are not absolute values but relative values
10.1.2.1.2Note 1: Low-shear viscosity LSV (ASTM D7394)
10.1.2.1.3Note 2: Disk-like and spherical rotors according to ISO 2884-2
10.1.2.1.4Note 3: Testing the solidification of liquid films using a T-bar spindle and a trough
10.6.3Krebs spindles
10.1.2.1.1Note: Medium-shear viscosity MSV (ASTM D7394)
10.6.4Paste spindles and rotors showing pins and vanes
10.6.5 Ball measuring. systems (motion along a circular path)
10.1.2.1.1Examples 1: Measuring samples for ball MS
10.1.2.1.2Examples 2: Food samples for ball MS
10.6.6Further relative measuring systems
10.7Measuring systems for solid torsion bars
10.2.1.1.1a) Automatic setting and control of the clamp distance
10.2.1.1.2Examples. 10.2.1.1.31) Target: Guaranteed stretching of the specimen bar by a constant tensile force
10.2.1.1.42) Target: Stress-less compensation of changes in the length of a specimen bar
10.2.1.1.53) Adjustment of the clamp distance
10.2.1.1.6b) Determination of the temperature gradient in a specimen
10.7.1Bars showing a rectangular cross section
10.1.2.1.1Note: Preparation of the specimens for temperature test
10.1.2.1.2a) Conversion between raw data and rheo- logical parameters for rectangular bars
10.1.2.1.31) Torque M and shear stress τ
10.1.2.1.42) Deflection angle φ and deformation γ
10.1.2.1.5b) Calculation of the complex shear modulus |G*|
10.7.2Bars showing a circular cross section
10.1.2.1.11) Torque M and shear stress τ
10.1.2.1.22) Deflection angle φ and deformation γ
10.1.2.1.3b) Calculation of the complex shear modulus |G*|
10.7.3Composite materials
10.1.2.1.1 Examples:
10.1.2.1.2Note: Testing fibers and rovings without the polymer matrix
10.8Special measuring devices
10.8.1Special measuring conditions which influence rheology
10.8.1.1Magnetic fields for magneto-rheological fluids
10.8.1.1.1Measuring examples
10.8.1.2Electrical fields for electro-rheological fluids
10.8.1.3Immobilization of suspensions by extraction of fluid
10.8.1.3.1Measuring examples
10.8.1.4UV light for UV-curing materials
10.8.1.4.1Measuring example
10.8.1.4.2Tips for users
10.8.1.5Relative humidity makes sticky or brittle
10.8.1.5.1 Preset of RH
10.8.1.5.2Application examples:
10.8.2Rheo-optical measuring devices
10.8.2.1Terms from optics
10.8.2.1.1a) Light, visible and invisible
10.8.2.1.2b) Radiation and wavelengths, light quanta or photons
10.8.2.1.3c) Lasers and monochromatic light showing only a single wavelength
10.8.2.1.4d) Polarization as a linear orientation of the oscillating waves along a single. propagation plane, and polarimeters
10.8.2.1.5e) Transmission, and a few coincidental interactions of light beam and sample
10.8.2.1.6f) Refraction of light and change of its direction, refractive index and refractometers
10.8.2.1.7g) Birefringence in optically anisotropic materials and propagation delay
10.8.2.1.8h) Absorption and conversion of energy
10.8.2.1.9i) Dichroism, optically anisotropic and bi-colored, using a selective absorber
10.8.2.1.10k) Scattering on small particles, coherent bouncing, and incoherent secondary beams
10.8.2.1.11l) Diffraction on large particles, and lighting the shaded area
10.8.2.1.12m) Luminesence, fluorescence and color change, phosphorescence and after-glow
10.8.2.2Microscopy
10.8.2.2.1Note 1: STED microscopy, higher resolution due to encircled light points
10.8.2.2.2Note 2: Confocal 3D microscopy, dot by dot in focus
10.8.2.3Velocity profile of flow fields
10.8.2.4Devices for measuring anisotropy in terms of. optical rotation and birefringence
10.8.2.5SALS for diffracted light quanta
10.8.2.6SAXS for diffracted X-rays
10.8.2.7SANS for scattered neutrons
10.8.3Other special measuring devices. 10.8.3.1Interfacial rheology on two-dimensional liquid films
10.8.3.2Dielectric analysis, and DE conductivity of materials showing electric dipoles
10.8.3.2.1DEA measurement
10.8.3.2.2Examples of simultaneous combination of DEA and rheology tests:
10.8.3.3NMR, and resonance of magnetically active atomic nuclei
10.8.4Other kinds of testings besides shear tests
10.8.4.1Tensile tests, extensional viscosity, and extensional rheology. 10.8.4.1.1a) Extensional viscosity of ideal-viscous fluids, and Trouton relation
10.8.4.1.2b) Extensional viscosity of viscoelastic liquids
10.8.4.1.3Note 1: Tensile stress relaxation tests, and tensile creep and creep recovery tests
10.8.4.1.4Note 2: Stretch tests, and the critical point of extension
10.8.4.1.5Note 3: Tensile tests on solid films and laminates at a constant strain rate
10.8.4.1.6c) Extensional rheology, and oscillatory tensile tests
10.8.4.2Tack test, stickiness and tackiness
10.8.4.2.1Typical measurements consist of three intervals:
10.8.4.2.2Variants:
10.8.4.2.3Note: The Dahlquist criterion for adhesives in order to show sufficient tack
10.8.4.3Tribology
10.8.4.3.1Two examples of different measuring geometries [10.70][10.71]:
10.8.4.3.2a) Static friction (friction-at-rest)
10.8.4.3.3b) Kinetic friction
10.8.4.3.4c) Static friction, rolling. friction and roll-out time of a ball bearing
10.8.4.3.5d) Application examples for investigating frictional behavior
10.9References
11Instruments. 11.1Introduction
11.2Short overview: methods for testing. viscosity and elasticity
11.2.1Very simple determinations
11.2.2Flow on a horizontal plane
11.2.3Spreading or slump on a horizontal plane after. lifting a container
11.2.4Flow on an inclined plane
11.2.5Flow on a vertical plane or over a special tool
11.2.6Flow in a channel, trough or bowl
11.2.7Flow cups and other pressureless. capillary viscometers
11.2.8Devices showing rising, sinking, falling and. rolling elements
11.2.9Penetrometers, consistometers and texture analyzers
11.2.10Pressurized cylinder and capillary devices
11.2.11Simple rotational viscometer tests
11.2.12Devices with vibrating or oscillating elements
11.2.13Rotational and oscillatory curemeters (for rubber testing)
11.2.14Tension testers
11.2.15Compression testers
11.2.16Linear shear testers
11.2.17Bending or flexure testers
11.2.18Torsion testers
11.3Flow cups
11.3.1ISO cups
11.3.1.1Capillary length
11.3.1.2Calculations. 11.3.1.2.1a) Hydrostatic pressure in a capillary
11.3.1.2.2b) The shear stress at the capillary wall according to the Hagen/Poiseuille relation
11.3.1.2.3c) Shear rates in a capillary
11.3.1.3Flow instabilities, secondary flow effects, turbulent flow conditions in flow cups
11.3.2Other types of flow cups
11.4Capillary viscometers. 11.4.1Glass capillary viscometers
11.4.1.1Calculations
11.4.1.1.1a) Hydrostatic pressure in a capillary
11.4.1.1.2b) The shear stress at the capillary wall according to the Hagen/Poiseuille relation
11.4.1.1.3c) Shear rates in a capillary
11.4.1.2Determination of the molar mass of polymers using. diluted polymer solutions
11.4.1.2.1a) The relative viscosity or the viscosity ratio
11.4.1.2.2b) The logarithmic viscosity number or the inherent viscosity
11.4.1.2.3c) The specific viscosity or the viscosity relative increment
11.4.1.2.4d) The reduced viscosity or the viscosity number VN (or the Staudinger function)
11.4.1.2.5e) The intrinsic viscosity IV or the limiting viscosity number LVN (or the Staudinger index)
11.4.1.2.6Steps to determine the value of the intrinsic viscosity [η]
11.4.1.2.7Application example: Research on proteins structures
11.4.1.2.8f) The [η]-M relation
11.4.1.2.9 g) Notes
11.4.1.3Determination of the viscosity index VI of petrochemicals
11.4.1.3.1Analysis method A
11.4.1.3.2Analysis method B
11.4.2Pressurized capillary viscometers. 11.4.2.1MFR and MVR testers driven by a weight (low-pressure capillary viscometers)
11.4.2.1.1a) Test procedure
11.4.2.1.2b) Determinations
11.4.2.1.3Conversion between MFR and MVR values
11.4.2.1.4Flow curve determination using MFR and MVR testers
11.4.2.1.5 c) Calculations
11.4.2.1.61) Pressure values in the cylinder and in the die
11.4.2.1.72) Shear stress values at the wall of the die according to the Hagen/Poiseuille relation
11.4.2.1.83) The mean shear rate value at the wall of the die acc. to the Hagen/Poiseuille relation
11.4.2.1.94) Calculation of viscosity values
11.4.2.2High-pressure capillary viscometers driven by an electric drive, for testing highly viscous and paste-like materials
11.4.2.2.1a) Test methods
11.4.2.2.2b) Determinations
11.4.2.3High-pressure capillary viscometers driven by gas pressure, for testing liquids
11.4.2.3.1a) Test methods
11.4.2.3.2b) Determinations
11.4.2.3.3c) Calculations
11.5Falling-ball viscometers
11.2.1.1.1The measuring principle of falling ball viscometers, and calculations
11.6Stabinger viscometer
11.2.1.1.1Explanations of the measuring procedure, and calculations
11.7Rotational and oscillatory rheometers
11.7.1Rheometer set-ups
11.1.2.1.1a) Rheometer type 1: Single head rheometers, or combined motor transducer (CMT) system
11.1.2.1.2b) Rheometer type 2: Dual head rheometers, or separated motor transducer (SMT) system
11.1.2.1.3c) Rheometer type 3: Double rheometer system with two separated measuring heads, both with drive and detector [11.141]
11.7.2Control loops. 11.1.2.1.1a) Torque control
11.1.2.1.2b) Control of deflection angle and rotational speed, using a closed control loop
11.1.2.1.3Note: Direct strain oscillation (DSO)
11.7.3Devices to measure torques
11.1.2.1.1a) Torque measurements using mechanical force sensors
11.1.2.1.2b) Torque measurements via power consumption of an electromotor
11.7.4Devices to measure deflection angles and. rotational speeds
11.1.2.1.1a) Measurements of rotational speeds using tachogenerators
11.1.2.1.2b) Measurements of deflection angles and rotational speeds using incremental encoders
11.7.5Bearings
11.1.2.1.1a) Mechanical bearing (e. g. ball bearing)
11.1.2.1.2b) Air bearing
11.7.6Temperature control systems
11.1.2.1.1a) Liquid bath
11.1.2.1.2b) Electric heating
11.1.2.1.3c) Convection oven for heating and cooling with gas
11.1.2.1.4d) Induction heating
11.1.2.1.5e) Peltier elements
11.8References
12Guideline for rheological tests
12.1Selection of the measuring system (geometry)
12.2Rotational tests. 12.2.1Flow and viscosity curves
12.1.2.1.1Measuring results and analysis
12.1.2.1.2a) If no yield point exists (flow curve types 1 to 4)
12.1.2.1.3b) If a yield point exists (flow curve type 5)
12.1.2.1.4Measuring results, and determination of the yield point by rotational tests:
12.2.2Time-dependent flow behavior (rotation)
12.2.3Step tests (rotation): structural decomposition and regeneration (thixotropy)
12.2.4Temperature-dependent flow behavior (rotation)
12.1.2.1.1Measuring results and analysis:
12.3Oscillatory tests
12.3.1Amplitude sweeps
12.1.2.1.1Measuring results and analysis:
12.3.2Frequency sweeps
12.1.2.1.1a) Polymers: Measuring results and analysis, using the curves of G’ and G’’
12.1.2.1.2b) Polymers: Measuring results and analysis, using the curves of η*
12.1.2.1.3c) Further analysis with polymers
12.1.2.1.4d) Dispersions and gels: Measuring results and analysis
12.3.3Time-dependent viscoelastic behavior (oscillation)
12.3.4Step tests (oscillation): structural decomposition and regeneration (thixotropy) 12.1.2.1.1Preset, alternatives: 12.1.2.1.2a) Three test intervals: oscillation/rotation/oscillation (ORO; as in Figure 8.33)
12.1.2.1.3b) Three intervals: all in oscillation (as in Figure 8.30)
12.3.5Temperature-dependent viscoelastic behavior (oscillation)
12.1.2.1.1a) Polymers: Measuring results and analysis
12.1.2.1.2b) Crystallizing samples: Measuring results and analysis
12.1.2.1.3c) Gelation, hardening, curing: Measuring results and analysis
12.4Selection of the test type
12.4.1Behavior at rest
12.1.2.1.1a) Determination of the yield stress value τy (or yield point) and the flow stress value τf (or flow point)
12.1.2.1.21) Rotational tests
12.1.2.1.32) Oscillatory tests
12.1.2.1.4b) If there is no flow point: the plateau value of the zero-shear viscosity η0
12.1.2.1.5c) Structural strength in terms of the G’-value
12.1.2.1.6d) Long-term stability of dispersions and gels
12.1.2.1.7e) Material characterization: behavior at rest
12.4.2Flow behavior
12.4.3Structural decomposition and regeneration (thixotropic behavior, e. g. of coatings) 12.1.2.1.1Step test, consisting of three intervals at low/high/low shear conditions
12.5References
13Shear tests with powders. and bulk solids. 13.1Introduction
13.1.1Classification of bulk solids according to their. fluidizability
13.1.2Influences on the flow behavior of powder
13.2Shear test of highly compacted, consolidated bulk solids
13.2.1.1.1Note: Measuring variants of rheometers when operating with ring shear cells
13.2.1Pre-compaction of the bulk solid
13.2.2Pre-shear of the bulk solid
13.2.3Shear-to-failure of the bulk solid
13.2.4Further pre-shear and shear-to-failure cycles
13.2.5The Mohr´s circles
13.2.5.1Mohr´s circle for steady-state flow, and the determination of the consolidation stress
13.2.5.1.1Relevance of the consolidation stress σ1 for common practice
13.2.5.2Mohr´s circle for the determination of the. compressive strength
13.2.5.2.1Relevance of the compressive strength σc for common practice
13.2.5.3Flow function, from consolidation and compressive strength
13.2.6Further tests with shear cells
13.2.6.1Time consolidation, determined from the time flow locus
13.2.6.2Wall friction, determined from the wall yield locus
13.2.6.3Wall friction with time consolidation, determined from the time wall yield locus
13.3Shear test of slightly compacted. bulk solids, using the powder cell
13.3.1Powder cells
13.3.2Preparations for powder testing
13.1.2.1.1Preparation (PT-T1) of the bulk solid by weighing the powder
13.3.3Preliminary tests for fluidization behavior of powders
13.1.2.1.1Fluidization process
13.1.2.1.2Examples for fluidization:
13.1.2.1.3Example: Loosening of a powder, and pneumatic transport
13.1.2.1.4Optional analysis for the preliminary test PT-T2 (fluidization behavior): 13.1.2.1.5OA1) Comparison between fluidization and de-fluidization behavior of the powder
13.1.2.1.6OA2) De-aeration behavior of the fluidized bed
13.3.4Powder testing and the determination of the. cohesion strength
13.1.2.1.1PT-T3a) Fluidization of the powder
13.1.2.1.2PT-T3b) De-aeration of the powder
13.1.2.1.3PT-T3c) Testing the de-aerated powder
13.1.2.1.4Evaluation, with calculation of the cohesion strength S
13.1.2.1.5Examples for the cohesion strength S:
13.1.2.1.6Optional methods and evaluations: Flow curves of powders
13.4References
14Rheologists and the historical development of rheology
14.1Development until the 19th century
14.2Development between 1800 and 1900
14.3Development between 1900 and 1949
14.4Development between 1950 and 1979
14.5Development since 1980
14.6References
16Appendix. 15.1Symbols, signs and abbreviations used. 15.2.1.1.1a) Latin characters (small letters)
15.2.1.1.2b) Latin characters (capitals)
15.2.1.1.3c) Greek characters
15.2The Greek alphabet
15.3Conversion table for units
15.2.1.1.1a) Length L (ISO unit: m)
15.2.1.1.2b) Area A (ISO unit: m2)
15.2.1.1.3c) Volume V (ISO unit: m3)
15.2.1.1.4d) Volume flow rate V ˙ (ISO unit: m3/s)
15.2.1.1.5e) Mass m (ISO unit: kg)
15.2.1.1.6f) Density ρ (ISO unit: kg/m3)
15.2.1.1.7g) Force F (ISO unit: N)
15.2.1.1.8h) Torque M (ISO unit: Nm)
15.2.1.1.9i) Mechanical stress τ, and pressure p (ISO unit: Pa or N/m2)
15.2.1.1.10k) Angle φ (recommended: rad)
15.2.1.1.11l) Time t (ISO unit: s)
15.2.1.1.12m) Velocity v (ISO unit: m/s)
15.2.1.1.13n) Rotational speed n or angular velocity ω (ISO unit: rad/s or s-1)
15.2.1.1.14o) Frequency f or angular frequency ω (ISO unit: rad/s or s-1)
15.2.1.1.15p) Temperature T (ISO unit: K, but °C is more useful for the daily work)
15.2.1.1.16q) Energy E, and work W (ISO unit: J)
15.2.1.1.17r) Power P (ISO unit: W)
15.2.1.1.18s) Viscosity
15.4References
16Standards. 16.1ISO standards
16.2ASTM standards
16.3DIN, DIN EN, DIN EN ISO and. EN standards
16.4Important standards for users of. rotational rheometers
16.2.1.1.1a) Geometries of measuring systems
16.2.1.1.2b) Polymer testing
16.2.1.1.3c) Testing of other kinds of measuring samples
16.2.1.1.4d) Terms used in rheology and rheometry
16.5References
Author
Acknowledgements
Index
Отрывок из книги
Thomas G. Mezger
The Rheology Handbook
.....
gellant), 2) polymer molecules in solution, 3a) dispersed polymer particles, without an additive,
3b) polymer dispersion with a polymeric associative thickener, here, also surfactant molecules are integrated in the bridge-like clusters
.....