Код Toyota. Секреты самого сильного производства в мире
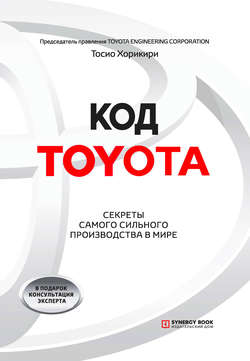
Реклама. ООО «ЛитРес», ИНН: 7719571260.
Оглавление
Тосио Хорикири. Код Toyota. Секреты самого сильного производства в мире
Предисловие
Глава 1. О Всеобщей производственной системе Toyota (Total Toyota Production System, T-TPS)
1.1. Проблемы прежней модели TPS (Toyota Production System, производственная система Toyota)
1.1.1. Проблемы, с которыми сталкиваются руководители и собственники компаний при внедрении TPS
1.1.2. Типичные ситуации
1.1.3. Основные проблемы TPS до появления T-TPS (Total-TPS)
1.2. Уроки, извлеченные из примеров
1.2.1. Причины отсутствия энтузиазма на рабочих местах
1.2.2. С чего начинать развертывание TPS?
1.2.3. Визуализация текущего состояния компании (завода)
1.2.4. Опережающее совершенствование, совершенствование вспомогательных подразделений и новейшая модель TPS
1.3. Что такое Total-TPS (Всеобщая производственная система Toyota)?
1.4. История становления Т-TPS
1.4.1. Прежняя модель TPS – проведение кайдзен-работы по указаниям сверху вниз
1.4.2. Переход к Т-TPS
1.5. Эффект Т-TPS
1.5.1. Повышение уровня профессионализма производственного подразделения
1.5.2. Результат внедрения Т-TPS
1.6. Активизация персонала и рабочих мест (АПРМ)
1.6.1. Активизация персонала и рабочих мест
1.6.2. Формула активизации персонала
1.6.3. Формула активизации рабочих мест
1.6.4. Английские выражения TPS
Глава 2. Основы T-TPS
2.1. Основные элементы производственной системы Toyota
2.2. Столпы, на которых держится Т-TPS
2.2.1. Автономизация (повышение качества) → завершенность своего процесса (T-TPS)
2.2.2. От «точно вовремя» к сокращению времени производственного цикла
2.2.3. Общепринятое плановое производство (метод выталкивания)
2.2.4. Исключение потерь – совершенствование рабочих операций → сокращение себестоимости и управление себестоимостью
2.3. Обеспечение сроков и объемов поставок
2.3.1. Сбалансированное (выровненное) производство
2.3.2. Малое серийное производство
2.3.3. Система канбан
2.4. Сокращение операций
2.4.1. Стандартизированная работа
2.4.2. Сокращение потерь
2.4.3. Развертывание кайдзен-работы
2.5. Совершенствование качества
2.5.1. Встраивание качества в процессы
2.5.2. Система остановки в фиксированном месте
2.5.3. Пропускная способность технологического процесса (табл. 2-5-3)
2.5.4. Пока-ёкэ (средства защиты от непреднамеренных ошибок)
2.5.5. Разработка операции сдачи качества
2.5.6. Деятельность кружков качества
2.6. Техника безопасности и обслуживание оборудования
2.6.1. Техника безопасности прежде всего
2.6.2. Обслуживание оборудования
2.7. Создание рабочих мест, где хочется работать
2.7.1. Роль линейных руководителей
2.7.2. Обучение смежным специальностям
2.7.3. Система кайдзен-предложений
Глава 3. Обеспечение качества
3.1. Основы обеспечения качества
3.2. Обеспечение качества в Toyota
3.3. Качество посредством завершенности каждого процесса
3.3.1. Обеспечение качества внутри производственного процесса
3.3.2. Qm matrix (Quality management matrix), матрица управления качеством (Qa network, Quality assurance network, система сквозного качества)
3.3.3. Завершенность собственного процесса
3.3.4. QCMS (Система управления цепочкой качества)
3.3.5. Опережающее обеспечение качества
3.3.6. Повышение качества посредством активизации персонала и рабочих мест (АПРМ)
Глава 4. Активизация персонала и рабочих мест (АПРМ)
4.1. Введение
4.1.1. Работа производственного подразделения Toyota
4.1.2. Цель АПРМ
4.1.3. Активизация персонала и рабочих мест
4.1.4. Почему эффективна АПРМ?
4.2. АПРМ в действии
4.2.1. Деятельность кружков качества
4.2.2. Освоение смежных специальностей и операций, ротация персонала
4.2.3. Система кайдзен-предложений
4.2.4. Обеспечение безопасности на рабочих местах
4.2.5. Обслуживание оборудования
4.2.6. Соревнование за звание «Лучший участок по производительности»
4.2.7. Развитие персонала
4.2.8. Организация рабочих мест
4.3. Совершенствование линий серийного производства
4.3.1. Кайдзен оборудования
4.3.2. Совершенствование работы
4.3.3. Совершенствование качества
4.3.4. Кайдзен-работа по сокращению себестоимости
4.4. Опережающее совершенствование при разработке новой продукции (advanced kaizen)
4.4.1. Синхронизированный инжиниринг
4.4.2. Подготовка технологии производства
4.4.3. Подготовка к массовому производству
4.5. Почему деятельность по активизации эффективна?
Глава 5. Роль руководителей
5.1. Важность АПРМ
5.2. Визуализированное управление
5.3. Роль руководителей
5.4. Роль линейных руководителей и топ-менеджеров в Toyota
Глава 6. Кайдзен-работа по методу «большой комнаты»
6.1. АПРМ по методу «большой комнаты»
6.2. Необходимость визуализации
Глава 7. Практические примеры кайдзен-работы по методу «большой комнаты»
7.1. Примеры стандартов
7.2. Пример работы на рисоочистительном заводе
7.3. Пример работы в компании по производству автокомпонентов
7.4. Пример работы на заводе по производству электронных компонентов в Китае
7.5. Пример работы на заводе-производителе автокомпонентов в России
Глава 8. Мировой сравнительный анализ компаний (Global Benchmarking, ГБМ)
8.1. Методика оценки производственной компании по принципам T-TPS
8.2. Таблица оценки компании
8.3. Реальная ситуация в компаниях по миру (фактический уровень)
8.4. Направления развития компании после ее оценки
Глава 9. Опережающее совершенствование
9.1. Опережающее совершенствование
9.2. Синхронизированный инжиниринг (Se)
9.3. Деятельность по обеспечению качества
9.4. Подготовка технологии производства
9.5. Подготовка производства (изготовления)
9.6. Итоги главы «Опережающее совершенствование»
Глава 10. Изменение управления на основе T-TPS
10.1. TMS (Toyota & Total management System) – всеобщая система управления Toyota
10.2. АПРМ в непроизводственных подразделениях
10.3. Применение и развитие T-TPS в реформировании управления
10.4. Глобальная система управления и менеджмента будущего
Отрывок из книги
Собранный в 1978 году исполнительным вице-президентом компании Toyota Motor Т. Оно опыт в виде книги «Производственная система Toyota» (Toyota Production System, TPS) получил распространение в 1980-х годах в США под названием Lean Production (бережливое производство). Затем система стала известна в Европе, а после и в России.
Со времени знакомства Запада с TPS прошло 30 лет. За это время она была значительно усовершенствована и, пройдя многие этапы, преобразовалась в финальную версию – Всеобщую производственную систему Toyota (Total Toyota Production System, T-TPS).
.....
В настоящее время заводы Toyota благодаря высокой активизации персонала наполнены оригинальными идеями рабочих, которые самостоятельно внедряют многие усовершенствования. Если посетить такой завод, то можно повсюду увидеть примеры усовершенствований – АПРМ налицо и на высоком уровне. Если сравнивать с этапами образования, то это уровень университета. С другой стороны, больше половины компаний, впервые внедряющих TPS, находятся на начальном уровне (на уровне учеников начальной школы). Существующие книги разъясняют основы TPS на уровне средних и старших классов. Образно говоря, если вдруг ученик начальной школы начнет решать примеры из программы средней или старшей школы, у него ничего не получится. Необходимо учиться последовательно и поэтапно развиваться шаг за шагом.
Необходимо, чтобы работники, руководители команд и групп, начальники производственных подразделений и другие сотрудники прошли разнообразную практику, достигли нужного уровня TPS. Данный путь подтвержден опытом Toyota.
.....