Root Cause Failure Analysis
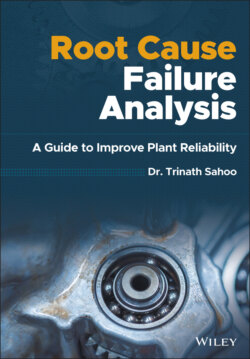
Реклама. ООО «ЛитРес», ИНН: 7719571260.
Оглавление
Trinath Sahoo. Root Cause Failure Analysis
Table of Contents
List of Tables
List of Illustrations
Guide
Pages
Root Cause Failure Analysis: A Guide to Improve Plant Reliability
Preface
About the Author
Acknowledgment
1 FAILURE: How to Understand It, Learn from It and Recover from It
Failure Type
Preventable Failures
Unavoidable Failures in Complex Systems
Intelligent Failures
Building a Learning Culture
Detecting Failure
Analyzing Failure
Share the Lessons
Benefits of Failure Analysis
Conclusion
2 What Is Root Cause Analysis
The Causes of TITANIC disaster
What Is Root Cause Analysis?
Different Levels of Causes
Physical Roots
Human Roots
Latent Roots
When RCA Is Justified. Equipment Damage or Failure
Operating Performance
Product Quality
Capacity Restrictions
Economic Performance
Safety
Top Reasons Why We Need to Perform RCFA
Root Cause Analysis in a Larger Context
Conclusion
3 Root Cause Analysis Process
What is root cause analysis
Define the problem
Collection of data
Interviews
Analyze Sequence of Events
Design Review
Operating and Maintenance Manuals
Operating Procedures and Practices
Maintenance History
Operating Envelope
Maintenance Procedures and Practices
Misapplication
Management Systems
Identify Possible Causal Factors. What Is a Causal Factor?
What Is a Root Cause?
What Is the Difference Between a Causal Factor and a Root Cause?
The Five Whys
When to Use 5 Why
How to Use the 5 Whys
Fishbone Diagram
Fishbone Diagram Structure
How to Create a Cause and Effect Diagram
Fault Tree Analysis
Drawing Fault Trees: Gates and Events
FTA Gate Notes
How to Undertake a Fault Tree Analysis?
Benefits of Fault Trees
Identify the Root Cause
Recommend and Implement Solution
Conclusion
4 Managing Human Error and Latent Error to Overcome Failure
Review of Some of the Accidents
Types of Human Failure: What Types of Errors Do Humans Make?
Active Failures
Latent Failures
What Factors Influence Human Reliability?
What Factors Influence Human Variability
The Prevention of Human Error
Ways to Reduce Human Error. The Procedures
Audits
Increased Discipline
Increased Automation
Improved Training
Motivational Campaigns
Conclusion
5 Metallurgical Failure
Understanding the Basics
Elastic Limit
Elastic and Plastic Ranges
Yield Point
Ultimate Strength
Rapture Strength
Elastic Deformation
Plastic Deformation
Identification of Types of Failures
Brittle vs. Ductile Fracture characteristics
Ductile Fracture
Brittle Fracture
Example: Failure of a Pipe
Stages in Ductile Fracture
Brittle Fracture Characteristics
Origin of Fractures (Ductile and Brittle)
Fatigue Failures
Stress Concentration
Thermal Fatigue Failure
Stress Corrosion Cracking
How to Prevent SCC
Chloride SCC
Hydrogen Damage
Failure Due to Hydrogen Damage
Addressing Hydrogen Damage
Corrosion Damage
How to Control Corrosion
Wear and Erosion Damage
Failure Investigation
Stages of a Failure Analysis
Collection of Background Data and Samples
Visual Examination
Testing
Non‐Destructive Evaluation/Non‐Destructive Testing (NDE/NDT)
Mechanical Testing
Macroscopic Examination
Microscopic Examination
Metallographic Examination
Chemical Analysis
Simulations
Data Analysis, Conclusions and Report
Impact of working condition on metallurgical failure
Improper Design
Improper Selection of the Materials
UnFavorable Manufacturing Processing Conditions
Poor Assembling
Poor Service Conditions
Poor Maintenance Strategy
Conclusion
6 Pipe Failure
Classification of Failure Mechanisms
Low‐Temperature Brittle Cleavage
Ductile Rupture
Fatigue (Mechanical and/or Thermal)
Embrittlement
Creep Stress‐Rupture
Stress‐Corrosion Cracking
Causes of Premature Failures in Piping
Design Deficiencies
Material Defect
Base Material Defects
Manufacturing Defects
Heat Treatment Defects
Dimensional and Geometrical Defects
Storage‐ (Environmental Effects)
Fabrication and Erection Defect
Service‐Related Deterioration
Specific Operational and Service Problems. Overpressure
Thermal Strain Cycling
Mechanical Strain Cycling
External Factors
Corrosion and/or Erosion
Uniform Attack
External Corrosion
Galvanic or Two‐Metal Corrosion
Crevice Corrosion
Pitting
Inter‐Granular Corrosion
Selective Leaching
Erosion Corrosion
Stress‐Corrosion Cracking
Microbiologically Influenced Corrosion
Other Causes for Pipe Failure. Interior Pipe Deposits
Insulation Failure
Weathering Damage
Wet Pipe Insulation
Failure Due to Vibration
Flow Induced Vibration
Acoustic Induced Vibration
Flow Induced Pulsation
Pipe Failure Due to Water Hammer in Steam Systems
Failure Due to Pipe Support
How to Overcome Piping System Failure
Design, Construction and Installation
Operation and Maintenance (Useful Life)
Operating Window
Factors That Affect Rate of Corrosion on a Piping System. The pH of the Fluid
Amount of Oxygen in the Fluid
Chemical Makeup of Fluid
Galvanic Corrosion
Temperature
Water Velocity
How to Mitigate Corrosion
Cathodic Protection (CP)
How to Reduce the Risk of Water Hammer
Inspection and Maintenance Plan to Avoid Failure
Understand the Ways in Which the Piping Can Fail
Determine the Likelihood of Piping Failure
Carefully Determine the Scope and Frequency of Inspection
Specify the Inspection
Assess the Inspection Results
Assessing the Piping Integrity
Report and Monitor Trends
Use the Integrity Outcomes to Revise the Inspection Approach
Conclusion
7 Failure of Flanged Joint
Creating the Seal
Forces Acting on a Gasket Joint
How to Achieve a Successful Seal
Integrity of the Bolted Flange Connections
Fastener Related
Factors to Be Considered During Selection of Bolts
Protection of Bolts. Plating
Passivation
Thread lubricants
Elevated Temperatures
Gasket
Gasket Seating Stress
Some of the Commonly Used Gasket Material
Gasket Reliability
Gasket Performance Depends Upon the Following Factors
Failure Related to Flange
Surface Finish
Gasket, Flange, Fastener as a System
Gasket Removal and Installation
Common Causes of Flange Joint Failure. Bolt Related
Gasket Related
Environmental Factors
Flange Related
Problems with Installation
Conclusion
8 Failure of Coupling
Flanged Rigid Couplings
Ribbed Rigid Couplings
Sleeve Rigid Couplings
Quill Shaft Rigid Couplings
Flexible Coupling
Functions of Flexible Couplings
Transmit Power
End Movement
Types of Flexible Couplings (General)
Types of General‐Purpose Couplings
Special‐Purpose Coupling
How General‐Purpose Couplings Work
Gear Couplings
Grid Couplings
Disc Couplings
Elastomeric Couplings
Pin and Bush Type Coupling
Jaw/Spider Type Coupling
Corded Tire Couplings
Special‐Purpose Couplings
High‐Performance Gear Couplings (Mechanical Element Type)
Metallic Element Couplings
Disc
Disc Type Coupling
Diaphragm Type
Elastomeric Block Couplings (Elastomeric Element Type)
Coupling Selection for Reliability
Safety Factors
Service Factors
Balancing Requirements
Coupling Fit
Clearance Fit (with Keys and Setscrews)
Shrink Fit
Shrink Fit on Tapered Shafts
Cause of Coupling Failure
Improper Selection
Effects of Thermal Variations and Misalignment
Failures Caused by Wear
Fatigue Failure
Fretting
Brittle Fracture
Hardware Failure
Time ‐related Failure
Incorrect Installation
Other important points to be considered during installation. Bolting
Distance Between Shaft Ends
Spacer Installation
Proper System Maintenance
Special‐Purpose Coupling Failure Mode. Failure Modes of Gear Coupling
Disc Coupling Failure Modes
Diaphragm Coupling Failure Modes
Elastomeric Coupling Failure Mode
Conclusion
9 Bearing Failure
Anti‐Friction Bearings
AntiFriction Bearing – Type, Selection, and Failure Mode
Bearing Basics. Types of Rolling Element Bearings
Radial bearing Designs, Features, and Applications. Features of Deep Groove Radial Bearings
Angular Contact Ball Bearings
Self‐aligning Ball Bearings
Radial Roller Designs, Features, and Applications
Tapered Roller Bearings
Spherical Roller Bearings
Needle Roller Bearings
Bearing Selection Process
Mounting Space
Loading
Speed Requirements
Rigidity Requirements
Misalignment Considerations
Mounting and DisMounting Considerations
Bearing Service Life
Antifriction bearing failure mechanism
Preoperational Causes of Damage
Application
Storage of Bearings
Bearing Handling Precautions
Bearing Tolerances, Fits, and Clearances
Bearing Internal Clearance
Static Misalignment
Faulty mounting practices
Passage of excessive electric voltage through the bearing
Material fatigue (subsurface‐initiated)
Ineffective lubrication
Ineffective Sealing
Sealing Devices
Integral Bearing Sealing Solutions
Journal Bearing
Sleeve Journal Bearings
Multilobe Bearings
Tilting Pad Journal Bearings (TPJB)
Journal Bearing Failure Mechanisms
Lack of Lubricant
Lubricant Contamination
Wrong viscosity grade
Bearing melting
Abnormal load
Fatigue
Cavitation
Corrosion
Creep
Wiping
Surface Displacement Can Be Termed Creep or Wiping
“Loss of Material”, or Scratches
Problem with bearing installation
Conclusion
10 Mechanical Seals Failure
Type of Mechanical Seal
Pusher Seal. Facts About Pusher Seal
Non‐Pusher Seal
Facts About Non‐Pusher Seal
Bellows seal
Application
Temperature Control in seal
Cooling System and API Plans
Selection of Flushing Plans. Clean, Not Harmful, Neutral, Not Flammable Products
Fluids Crystallizing When in Contact with Atmosphere
Acid Products
Hot Liquids
Aqueous Solutions Prone to Solidify or Produce Sediments
Toxic, Poisonous or Highly Viscous Fluids
Abrasive Fluids
Flammable Fluids
Hot Water
Seal Failure Causes
Pump Design Affect Seal Reliability
Shaft flexibility
Diffuser design
Chamber Design Affects Seal Reliability
Seal Chamber Selection Criteria
Review of Suction Piping System
Fluid Characteristics Affect Seal Reliability
Fluid Temperature Margin
Environmental Control
Off‐Design Pump Operation and Seal Performance
Other Design Requirements
Train Your Operators!
Seal Installation, What to See
Mechanical Seal Installation Procedure
Conclusion
11 Centrifugal Pump Failure
Pump Failure Causes
Pump Selection
Material
Shaft Slenderness Ratio
Hydraulic Requirement
NPSH Requirement
Impeller Selection
Suction Specific Speed
ANSI vs. API – Which Specification to Follow
Failure Due to Operational Reasons. Hydraulic Disturbance Due to Capacity
Centrifugal Pump Hydraulic Disturbances. The Limits of the Centrifugal Pump Curve
Low Flow Operation
High Flow Operation
Hydraulic Stability Guidelines
Hydraulic Disturbance Due to Cavitation and NPSH. Cavitation
Net Positive Suction Head
Guidelines for selecting pumps free of hydraulic disturbances
Suction System Design Can Affect Hydraulic Disturbance
Suction Piping
Discharge Piping
Vortexing
Vertical Pump Trouble
Cooling Water Pump Trouble
Other Mechanical Consideration. Installation and Maintenance
Piping Stress
Misalignment
Casing
Casing Nozzle Loading
Casing Thermal Bowing
Shaft Displacement
Wear rings
Filters, Suction Strainers
Base Plates and Grounting
Bearing Failure
Proper Handling and Storage
Improper Lubrication
Overload
Improper Mounting
Misalignment
Corrosion
Fit
Fatigue
Seal Failure
Coupling Problem
Lubrication Related Problem in Pump
Quantity
Quality
Conclusion
12 Reciprocating Pumps Failure. Working Principle
Power Pump Operation and Construction
Uses and Applications for Reciprocating Pumps
The Failure Causes in Reciprocating Pump
Net Positive Suction Head
NPSHA
NPSHR
Problem of Inadequate NPSH
Test Criteria for NPSH
Typical Suction System Problems
Acceleration Head
Typical Discharge System Problems
Pulsation Control
Pulsation Dampener Design
Servicing the Dampener
Problem with Piping System
Pump Suction Piping System
Line Size
Be Short and Direct
Line Velocity
Pump Discharge Piping System
Piping Vibrations
Problems with Liquid End Components
Packing
Plungers
Stuffing Boxes
Valve
The Cause of Late Valve Closure
The Effects of Late Valve Events
Thermal Problems
Shaft Failures
Conclusion
13 Centrifugal Compressor Failure
Characteristics of Centrifugal Compressor
Major Components of a Centrifugal Compressor
Rotor
Impeller
Problems Related to Rotor
Impeller Forces and Shrink Fit
Rotor Position
Rotor Balancing
Rotor Dynamic Considerations. Rotor Instabilities
Critical Speed
Over speed Protection
Failure of Stationary Components. The Casing
Horizontal Split Casing
Barrel Casing
Diaphragms
Interstage Seals
Balance Piston
Impeller Thrust
Other Components. Bearings
Seals
Baseplate
Lubrication System
Seal Gas System
Seal Oil System
Suction KnockoutPots
Inter‐Cooler/After‐cooler
Recycle Valve
Control and Management Systems
Troubles Related to Process. Change in Process Parameter
Surge
How Surge takes place in Centrifugal Compressor. Suction Throttling
Discharge Valve Throttling
Change in Speed
Inlet Filter Chocking
Driver Input Speed
Change in Compressed Gas Property
Effect of Surge in Centrifugal Compressor
Liquids in the System
Fouling
The Causes of Fouling
Preventing and Correcting Fouling
Corrective measures
Cleaning Centrifugal Compressors
Mechanical Related Troubles. Alignment
Lubricating Oil Systems
Cooler
Intercooler
Control Related Troubles
Ancillaries
Seal Systems (Dry Gas Seals and Liquid Seals) Dry Gas Seal Systems
Liquid Seal Systems
Other Auxiliary Systems
Maintenance Intervals
Importance of Engineering Rounds
Online Checks and Inspections. Vibration Monitoring System
System Performance Monitoring of Auxiliary Systems
Conclusion
14 Reciprocating Compressor Failure
Major Components
Lubrication System
Rod Load
Reciprocating Compressor Failure Causes
Compressor Valves Failure Causes
Valve Failure Effect on System
Valves Failure Effect on Capacity‐
Environmental Causes of Valve Failure
Mechanical Causes of Valve Failure
How to Improve Valve Reliability
Pressure Packing Failure
Packing Care During Assembly
Piston Ring/Rider Ring Wear
Causes of Ring Wear. Cylinder
Dirt Generated by Process Gas
Lubrication
Rider Ring Clearances
Process Related Problems in Reciprocating Compressor. Gas Properties
Liquid in Process Gas
Temperature of process gas
Variation in Suction Pressure
Effect of Leakage
Change in Oil viscosity
Maintenance Related Issues. Compressor Alignment
Trouble with Cylinders
Trouble with Cylinder Liner
Valve Maintenance Related Issue
Bearing Clearances
Web Deflection
Piston Rod Run‐out
Horizontal Run‐Out
Vertical Run‐Out
Water Jackets
Machine Monitoring
Operating Condition Monitoring
Compression Ratios
Improper Cylinder Loading
Rod Load
Rod Load Reversal
Peak pressure
Discharge Temperature Delta
Condensed Liquids
Early Fault Recognition and Diagnosis
Temperature
Rod Drop Monitoring
Rod Run‐Out
Vibration
Frame Vibration
Crosshead Vibration
Cylinder Vibration
p–V Diagram Analysis
Efficiency Monitoring
Compression Efficiency
Varying Conditions
Conclusion
15 Lubrication Related Failure in Machinery. Introduction
Lubrication Related Failure in Sump and Circulating System of Turbomachinery. Water Contamination
Particle Contamination
Heat
Air Entrainment
Oil Degradation
Lubrication Related Failure Specific to Reciprocating Compressor
Factors Affecting Cylinder Lubrication
Rate of Oil Feed
Lubrication Program Management
Right Type
Right Quality
Right Amount
Right Place
Right Time
Right Lubrication Procedures
Important Points to Be Considered for Developing an Effective Lubrication Program. Lubricant Selection
Storage and Handling of Lubricants
Lubricant Degradation During Storage
Proper Storage Environment
Accurate Labelling
Oil Sampling
Strategic Sampling Considerations
Data Density and Data Disturbance
Strategic Sampling Considerations
Locations for Sampling
Contamination Control
Handling of Lubricating Oil
Prefiltering of Lubricants
Use of Sealable, Cleanable Top‐Up Containers
Understanding Oil Analysis: How It Can Improve Reliability
Trending
Conclusion
16 Steam Traps Failure
Thermodynamic Trap
Float Trap
Inverted Bucket Trap
Thermostatic Traps
Thermostatic Metallic‐Expansion Trap
Balanced‐Pressure Thermostatic Trap
Bimetallic Trap
Selection Criteria
Common Problems of Steam Traps
Sharing of Traps
Installation
Strainers
Maintenance of Steam Traps. Trap Checking Techniques
Sight
Sound
Temperature
Diagnosis
Steam Trap Audit
Conclusion
17 Proactive Measures to Avoid Failure
What Are Proactive Maintenance Tasks
Planned‐Maintenance Tasks
Condition‐Monitoring Tasks
Combination of Tasks
Failure‐Finding Tasks
Servicing and Routine Inspection
One‐Time Changes
Evolution of Different Type of Maintenance
Condition Monitoring Technologies
Vibration
Oil Analysis
Thermography
Motor Current Signature Analysis (MCSA)
Ultrasonic Emissions Evaluation
Proactive Inspection Program for Static Equipments
Equipment Modification Factor
Risk Based Inspection
Condition Monitoring and The Internet of Things
Equipment Condition Assessment and Decision Making
Operator‐Based Maintenance
Conclusion
Index. a
b
c
d
e
f
g
h
i
j
k
l
m
n
o
p
r
s
t
u
v
w
y
WILEY END USER LICENSE AGREEMENT
Отрывок из книги
Dr. Trinath Sahoo
.....
A fishbone diagram is a visual way to look at cause and effect. It is a more structured approach than some other tools available for brainstorming causes of a problem (e.g., the Five Whys tool). The problem or effect is displayed at the head or mouth of the fish. Possible contributing causes are listed on the smaller “bones” under various cause categories. A fishbone diagram can be helpful in identifying possible causes for a problem that might not otherwise be considered by directing the team to look at the categories and think of alternative causes. Include team members who have personal knowledge of the processes and systems involved in the problem or event to be investigated.
The left side of the diagram is where the causes are listed. The causes are broken out into major cause categories. The causes you identify will be placed in the appropriate cause categories as you build the diagram.
.....