Handbook of Plastics Testing and Failure Analysis
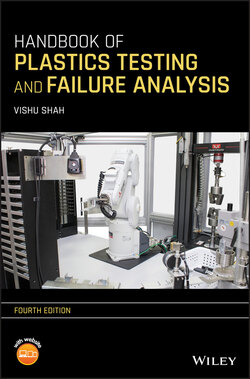
Реклама. ООО «ЛитРес», ИНН: 7719571260.
Оглавление
Vishu Shah. Handbook of Plastics Testing and Failure Analysis
Table of Contents
List of Tables
List of Illustrations
Guide
Pages
HANDBOOK OF PLASTICS TESTING AND FAILURE ANALYSIS
PREFACE TO THE FOURTH EDITION
PREFACE TO THE THIRD EDITION
PREFACE TO THE SECOND EDITION
PREFACE TO THE FIRST EDITION
BIOGRAPHY OF VISHU SHAH
ABOUT THE COMPANION WEBSITE
1 BASIC CONCEPTS AND ADVANCEMENT IN TESTING TECHNOLOGY. 1.1. BASIC CONCEPTS
1.2. SPECIFICATION AND STANDARDS
1.3. PURPOSE OF SPECIFICATIONS
1.4. BASIC SPECIFICATION FORMAT
1.4.1. Classification System
1.4.2. Requirements
1.4.3. Sampling and Conditioning
1.4.4. Test Methods
1.5. ADVANCEMENTS IN TESTING TECHNOLOGY
1.6. NEW DEVELOPMENTS AND TRENDS IN TESTING TECHNOLOGY
REFERENCES
2 MECHANICAL PROPERTIES. 2.1. INTRODUCTION
2.2. TENSILE TESTS (ASTM D 638, ISO 527‐1)
2.2.1. Apparatus
2.2.2. Test Specimens and Conditioning
2.2.3. Test Procedures. A. Tensile Strength
B. Tensile Modulus and Elongation
2.2.4. Factors Affecting the Test Results. A. Specimen Preparation and Specimen Size
B. Rate of Straining
C. Temperature
2.3. FLEXURAL PROPERTIES (ASTM D 790, ISO 178)
2.3.1. Apparatus
2.3.2. Test Specimens and Conditioning
2.3.3. Test Procedures and Calculations
2.3.4. Modulus of Elasticity (Flexural Modulus)
2.3.5. Factors Affecting the Test Results. A. Specimen Preparation
B. Temperature
C. Test Conditions
2.4. COMPRESSIVE PROPERTIES (ASTM D 695, ISO 604)
2.4.1. Apparatus
2.4.2. Test Specimens and Conditioning
2.4.3. Procedure
2.5. CREEP PROPERTIES (ISO 899‐1, ISO 899‐2, ASTM D2990, ISO 16770)
2.5.1. Tensile Creep
2.5.2. Flexural Creep
2.5.3. Interpretation and Applications of Creep Data
2.5.4. Isochronous Stress–Strain Curves
2.5.5. Effects of Stress and Temperature on Creep Modulus
2.5.6. Basic Procedures for Developing and Applying Creep Modulus Data
2.6. STRESS RELAXATION
2.7. IMPACT PROPERTIES. 2.7.1. Introduction
2.7.2. Factors Affecting the Impact Strength. A. Rate of Loading
B. Notch Sensitivity
C. Temperature
D. Orientation
E. Processing Conditions and Types
F. Degree of Crystallinity, Molecular Weight
G. Method of Loading
H. Specimen Clamping
2.7.3. Types of Impact Tests
A. Pendulum Impact Tests. Izod–Charpy Impact Test (ASTM D‐256, ASTM D4812 ISO 179)
Apparatus and Test Specimens
Test Procedures
Effect of Test Variables and Limitations
B. High‐Rate Tension Test
C. Falling‐Weight Impact Test
Drop Impact Test
Test Variables and Limitations
D. Instrumented Impact Testing
Interpreting Impact Data
E. High‐Speed Impact Tests (ASTM D3763, ISO 6603‐2)
F. Miscellaneous Impact Tests
2.8. SHEAR STRENGTH (ASTM D 732)
2.8.1. Test Specimen and Apparatus
2.8.2. Test Procedures
2.8.3. Significance and Limitations
2.9. ABRASION. 2.9.1. Introduction
2.9.2. Abrasion Resistance Tests
2.10. FATIGUE RESISTANCE. 2.10.1. Introduction
2.10.2. Flexural Fatigue Test
2.10.3. Tensile Fatigue Test
2.10.4. Factors Affecting the Test Results and Limitation of Fatigue Tests
2.11. HARDNESS TESTS. 2.11.1. Introduction
2.11.2. Rockwell Hardness (ASTM D 785)
A. Test Apparatus and Specimen
B. Test Procedures
2.11.3. Durometer Hardness (ASTM D 2240, ISO 868)
2.11.4. Barcol Hardness (ASTM D 2583)
A. Anisotropy
REFERENCES
SUGGESTED READING
3 THERMAL PROPERTIES. 3.1. INTRODUCTION
3.2. TESTS FOR ELEVATED TEMPERATURE PERFORMANCE
3.2.1. Short‐Term Effects. A .Heat Deflection Temperature (HDT) (ASTM D 648, ISO 75‐1 & 75‐2)
Apparatus and Test Specimens
Oil‐Free Apparatus
Test Procedure
Test Variables and Limitations
B. Vicat Softening Temperature (ASTM D 1525, ISO 306)
C. Torsion Pendulum Test (ASTM D 2236)
3.2.2. Long‐Term Effects
A. Long‐Term Heat‐Resistance Test (ASTM D 794) (Withdrawn 1998)
B. UL Temperature Index
Relative Thermal Indices
Relative Thermal Index Based Upon Historical Records
Relative Thermal Index Based Upon Long‐Term Thermal Aging
C. Creep Modulus/Creep Rupture Tests
3.3. THERMAL CONDUCTIVITY (ASTM C 177, ISO 8302)
3.4. THERMAL EXPANSION
3.4.1. Coefficient of Linear Thermal Expansion (ASTM D 696)
3.5. BRITTLENESS TEMPERATURE (ASTM D 746, ISO 974)
3.5.1. Test Apparatus and Procedures
REFERENCES
SUGGESTED READING
4 ELECTRICAL PROPERTIES. 4.1. INTRODUCTION
4.2. DIELECTRIC STRENGTH (ASTM D 149, IEC 243‐1)
4.2.1. Factors Affecting the Test Results. A. Specimen Thickness
B. Temperature
C. Humidity
D. Electrodes
E. Time
F. Mechanical Stress
G. Processing
4.2.2. Test Limitations and Interpretations
4.3. DIELECTRIC CONSTANT AND DISSIPATION FACTOR (ASTM D 150, IEC 250) 4.3.1. Dielectric Constant (Permittivity)
4.3.2. Dissipation Factor
4.4. ELECTRICAL RESISTANCE TESTS
4.5. ARC RESISTANCE (ASTM D 495)
4.6. UL REQUIREMENTS
4.6.1. Material Properties
A. Short‐Term Properties—UL 746 A
B. Long‐Term Properties—UL 746 B
4.6.2. Evaluation of Plastic Materials Used in Electrical Equipments—UL 746 C
4.6.3. Polymeric Materials—Fabricated Parts UL 746 D
4.7. EMI/RFI SHIELDING (10) 4.7.1. Introduction
4.7.2. Regulations and Standards
4.7.3. Shielding Effectiveness Measurement
A. Open‐Field Testing Technique
B. Shielded‐Box Technique, Coaxial Transmission Line Technique, and Shielded‐Room Technique
4.7.4. Conductivity Measurement
A. Surface Resistivity
B. Volume Resistivity
C. Ohms‐per‐Square Testing
4.7.5. Adhesion Testing
REFERENCES
SUGGESTED READING
5 WEATHERING PROPERTIES. 5.1. INTRODUCTION
5.1.1. UV Radiation
5.1.2. Microorganisms
5.1.3. Oxygen, Moisture, Thermal Energy, and Other Environmental Factors
5.2. ACCELERATED WEATHERING TESTS
5.2.1. Fluorescent UV Exposure of Plastics (ASTM D4329, ISO 4892‐3)
5.2.2. Filtered Open‐Flame Carbon Arc‐Type Exposures of Plastics (ASTM D 1499) and Enclosed Carbon Arc Exposures of Plastics (ASTM D 6360)
5.2.3. Xenon Arc Exposure of Plastics Intended for Outdoor Applications (ASTM D 2565, G 155, ISO 4892‐2)
5.2.4. Metal halide light sources
5.2.5. Interpretations and Limitations of Accelerated Weathering Test Results
5.3. OUTDOOR WEATHERING OF PLASTICS (ASTM D 1435, ISO‐877)
5.3.1. Outdoor Accelerated Weathering (ASTM G 90)
5.4. RESISTANCE OF PLASTIC MATERIALS TO FUNGI (ASTM G 21)
5.5. RESISTANCE OF PLASTIC MATERIALS TO BACTERIA (ASTM G 22)
5.6. LIMITATIONS OF ACCELERATED MICROBIAL GROWTH RESISTANCE TESTING
5.7. OUTDOOR EXPOSURE TEST FOR STUDYING THE RESISTANCE OF PLASTIC MATERIALS TO FUNGI AND BACTERIA AND ITS LIMITATIONS
REFERENCES
SUGGESTED READING
6 OPTICAL PROPERTIES. 6.1. INTRODUCTION
6.2. REFRACTIVE INDEX (ASTM D 542, ISO 489)
6.2.1. Refractometric Method
6.2.2. Microscopical Method
6.3. LUMINOUS TRANSMITTANCE AND HAZE (ASTM D 1003)
6.3.1. Test Procedure
6.4. PHOTOELASTIC PROPERTIES
6.4.1. Stress‐Optical Sensitivity Examination
6.5. COLOR
6.5.1. Instrumented Color Measurement
6.5.2. Visual Color Evaluation (ASTM D 1729)
6.6. SPECULAR GLOSS (ASTM D2457, D523)
REFERENCES
SUGGESTED READING
7 MATERIAL CHARACTERIZATION TESTS. 7.1. INTRODUCTION
7.2. MELT INDEX TEST (ASTM D 1238, ISO 1133) 7.2.1. Significance
7.2.2. Test Procedures
7.2.3. Factors Affecting the Test Results
7.2.4. Interpretation of Test Results
7.2.5. Advancement in Melt Index Testing Technology
7.3. RHEOLOGY
7.3.1. Torque Rheometer
7.3.2. Rotational Rheometers/Viscometers
7.3.3. Capillary Rheometer
7.4. VISCOSITY TESTS
7.4.1. Dilute Solution Viscosity of Polymers (ASTM D 2857)
A. Relative Viscosity (Viscosity Ratio)
B. Specific Viscosity
C. Reduced Viscosity (Viscosity Number)
D. Inherent Viscosity (Logarithmic Viscosity Number)
E. Intrinsic Viscosity (Limiting Viscosity Number)
7.4.2. Applications and Limitations of Dilute Solution Viscosity Measurements
7.5. GEL PERMEATION CHROMATOGRAPHY
7.5.1. GPC Instrumentation
A. Solvent Delivery System
B. Injector
C. Columns
D. Detectors
E. Recorder
7.5.2. Test Procedure
7.5.3. Interpreting the GPC Curve
7.6. THERMAL ANALYSIS TECHNIQUES
7.6.1. Differential Scanning Calorimetry (ASTM D 3418, ISO 11357)
7.6.2. Thermogravimetric Analysis (TGA)
7.6.3. Thermomechanical Analysis (TMA)
7.6.4. Dynamic Mechanical Analysis (DMA)
7.7. SPECTROSCOPY
7.8. MATERIAL CHARACTERIZATION TESTS FOR THERMOSETS
7.8.1. Apparent (Bulk) Density, Bulk Factor, and Pourability of Plastic Materials (ASTM D 1895)
A. Determination of Apparent Density
B. Determining Bulk Factor
C. Pourability
7.8.2. Flow Tests
A. Factors Affecting Flow
B. Spiral Flow of Low‐Pressure Thermosetting Compounds (ASTM D 3123)
C. Cup Flow Test (ASTM D 731)
7.8.3. Viscosity Tests for Thermosets
A. Bubble Viscometer
7.8.4. Gel Time and Peak Exothermic Temperature of Thermosetting Resins (ASTM D 2471)
REFERENCES
GENERAL REFERENCES
SUGGESTED READING
8 FLAMMABILITY. 8.1. INTRODUCTION
8.2. FLAMMABILITY TEST (NONRIGID SOLID PLASTICS) (ASTM D 4804)
8.3. FLAMMABILITY TEST (SELF‐SUPPORTING PLASTICS IN HORIZONTAL POSITION) (D 635)
8.4. FLAMMABILITY TEST (SOLID PLASTICS IN VERTICAL POSITION) (D 3801)
8.5. IGNITION PROPERTIES OF PLASTICS. 8.5.1. Introduction
8.5.2. Ignition Temperature Determination (ASTM D 1929)
8.5.3. Ignition Response Test (ASTM D 3713)
8.6. OXYGEN INDEX TEST (ASTM D 2863, ISO 4589) 8.6.1. Introduction
8.6.2. Test Procedures
8.6.3. Factors Affecting the Test Results
8.7. SURFACE BURNING CHARACTERISTICS OF MATERIALS
8.7.1. Surface Flammability of Materials Using a Radiant Heat Energy Source (ASTM E 162)
8.7.2. Surface‐Burning Characteristics of Building Materials (ASTM E 84)
8.8. FLAMMABILITY OF CELLULAR PLASTICS—VERTICAL POSITION (ASTM D 3014)
8.9. FLAMMABILITY OF CELLULAR PLASTICS—HORIZONTAL POSITION (ASTM D 1692)
8.10. FLAME RESISTANCE OF DIFFICULT‐TO‐IGNITE PLASTICS (FEDERAL STD. NO 406 METHOD 203)
8.11. SMOKE GENERATION TESTS
8.11.1. Smoke Density Test (ASTM D 2843)
8.11.2. Surface Flammability Tests (ASTM E 84)
8.11.3. Specific Optical Density of Smoke Generation (ASTM E 662)
8.11.4. Gravimetric Determination of Smoke Particulates from Burning of Plastic (ASTM D 4100)
8.11.5. Radiant Panel Test (ASTM E 162)
8.11.6. OSU Release Rate Test
8.12. UL 94 FLAMMABILITY TESTING
8.12.1. Horizontal Burning Test for Classifying Materials (HB)
8.12.2. Vertical Burning Test for Classifying Materials (V‐0, V‐1, V‐2)
8.12.3. Vertical Burning Test for Classifying Materials (5V)
8.12.4. Vertical Burning Test for Classifying Materials (VTM‐0, VTM‐1, or VTM‐2)
8.12.5. Horizontal Burning Test for Classifying Foam Materials (HBF‐1 or ‐2)
8.12.6. Factors Affecting UL 94 Flammability Testing
8.13. MEETING FLAMMABILITY REQUIREMENTS
8.13.1. Agencies Regulating Flammability Standards. A. Government Agencies
B. Industry Associations
C. Private Institutions
D. Insurance Underwriters
E. Other Agencies
8.13.2. Steps in Meeting Flammability Requirements
REFERENCES
SUGGESTED READING
9 CHEMICAL PROPERTIES. 9.1. INTRODUCTION
9.2. IMMERSION TEST (ASTM D 543, ISO 22088)
9.3. STAIN RESISTANCE OF PLASTICS
9.3.1. Resistance of Plastics to Sulfide Staining (ASTM D 1712)
9.4. SOLVENT STRESS‐CRACKING RESISTANCE
9.5. ENVIRONMENTAL STRESS‐CRACKING RESISTANCE (ASTM D 1693, ISO 22088)
9.5.1. Test Procedure
9.5.2. Alternate Constant Strain Test
REFERENCES
10 ANALYTICAL TESTS. 10.1. INTRODUCTION
10.2. DENSITY AND SPECIFIC GRAVITY (ASTM D 792, ISO 1183)
10.2.1. Method A
10.2.2. Method B
10.3. DENSITY‐BY‐DENSITY GRADIENT TECHNIQUE (ASTM D 1505, ISO R 1183‐2)
10.4. BULK (APPARENT) DENSITY TEST (ASTM D 1895)
10.5. WATER ABSORPTION (ASTM D 570, ISO 62)
10.6. MOISTURE ANALYSIS
10.6.1. Loss on Drying (LOD) Method
A. LOD Using a Laboratory Oven
B. LOD Using an Instrument (ASTM D 6980)
10.6.2. Karl Fischer Method
10.6.3. Sensor‐Based Technology (ASTM D 7191)
10.6.4. Microwave Technology
10.7. SIEVE ANALYSIS (PARTICLE SIZE) TEST (ASTM D 1921)
REFERENCES
11 CONDITIONING PROCEDURES. 11.1. CONDITIONING (ASTM D 618, ISO 291)
11.2. DESIGNATION FOR CONDITIONING
Example
REFERENCES
SUGGESTED READING
12 MISCELLANEOUS TESTS
12.1. TORQUE RHEOMETER TEST (ASTM D 2538)
12.2. PLASTICIZER ABSORPTION TESTS
12.2.1. Plasticizer Absorption—Burette Method
12.2.2. Plasticizer Absorption Using a Torque Rheometer (ASTM D 2396)
12.2.3. Plasticizer Absorption Under Applied Centrifuge Force (ASTM D 3367 ISO 4608)
12.3. CUP VISCOSITY TEST
12.4. BURST STRENGTH TEST
12.4.1. Quick‐Burst Strength Test (ASTM D 1599)
12.4.2. Long‐Term‐Burst Strength Test (ASTM D 1598)
12.4.3. Developing Long‐Term Hydrostatic Design Stress Data and Pressure Rating
12.5. CRUSH TEST
12.6. ACETONE IMMERSION TEST (ASTM D 2152)
12.7. ACETIC ACID IMMERSION TEST (ASTM D 1939)
12.8. END‐PRODUCT TESTING
12.9. ASH CONTENT (ASTM D 5630, ASTM D 2584, ISO 3451)
REFERENCES
GENERAL REFERENCES
13 IDENTIFICATION ANALYSIS OF PLASTIC MATERIALS. 13.1 INTRODUCTION
13.1.1. Melting‐Point Determination
13.1.2. Solubility Test
13.1.3. Copper Wire Test
13.1.4. Specific Gravity Test
13.2. ADVANCED METHODS FOR IDENTIFICATION
13.2.1. Fourier Transform Infrared Analysis
13.2.2. Thermogravimetric Analysis
13.2.3. Differential Scanning Calorimetry (DSC)
13.2.4. Thermomechanical Analysis (TMA)
13.2.5. Nuclear Magnetic Resonance (NMR)
13.2.6. Chromatography (GCMS/LCMS/PYMS/GPC)
A. Gas Chromatography‐Mass Spectrometry (GC‐MS)
B. Liquid Chromatography‐Mass Spectrometry (LC‐MS)
C. Pyrolysis‐Mass Spectrometry (PY‐MS)
D. Gel Permeation Chromatography (GPC)
13.2.7. Mass Spectrometry (MS)
13.2.8. X‐Ray Fluorescence
13.2.9. Microscopy (SEM/TEM)
13.3. IDENTIFICATION OF PLASTIC MATERIALS. 13.3.1. Thermoplastics. A. ABS
B. Acetal
C. Acrylic
D. Cellulose Acetate
E. Cellulose Acetate Butyrate
F. Cellulose Propionate
G. Fluorocarbons (FEP, CTFE, PTFE, PVF)
H. Nylons
I. Polycarbonate
J. Thermoplastic Polyester
K. PVC
L. Polyethylene
M. Polypropylene
N. Polystyrene
O. Polyphenylene Oxide (PPO)
P. Polysulfone
Q. Polyurethane (Thermoplastic)
R. Polyphenylene Sulfide (PPS)
13.3.2. Thermosetting Plastics. A. Diallyl Phthalate (DAP)
B. Epoxy
C. Phenol Formaldehyde
D. Urea Formaldehyde
E. Melamine Formaldehyde
F. Polyesters
G. Silicones
13.3.3. Elastomers. A. Styrenic TPE (S‐TPE)
B. Polyurethanes (TPUs)
C. Copolyesters (COPS)
D. Olefinics (Thermoplastic Elastomeric Olefins—TEOs)
E. Thermoplastic Vulcanizates (TPVs)
REFERENCES
GENERAL REFERENCES
14 TESTING OF CELLULAR PLASTICS. 14.1. INTRODUCTION
14.2. RIGID FOAM TEST METHODS. 14.2.1. Density (ASTM D 1622, ISO 845)
14.2.2. Cell Size (ASTM D 3576, ISO 2896)
14.2.3. Open‐Cell Content (ASTM D 6226, ISO 4590)
14.2.4. Compressive Properties (ASTM D 1621, ISO 844)
14.2.5. Tensile Properties (ASTM D 1623)
14.2.6. Shear Properties (ASTM C 273)
14.2.7. Flexural Properties (ASTM D 790, ISO 178)
14.2.8. Dimensional Stability (ASTM D 2126, ISO 2796)
14.2.9. Water Absorption (ASTM D 2842, ISO 2896)
14.2.10. Water Absorption of Core Materials for Structural Sandwich Constructions (ASTM C 272)
14.2.11. Water Vapor Transmission (ASTM E 96)
14.2.12. Weathering Properties
14.2.13. Thermal Conductivity (ASTM C 177)
14.2.14. Flammability
14.2.15. Dielectric Constant and Dissipation Factor (ASTM D 1673)
14.3. FLEXIBLE CELLULAR MATERIALS TEST METHODS. 14.3.1. Introduction
14.3.2. Steam Autoclave Test
14.3.3. Constant Deflection Compression Set Test
14.3.4. Indentation Force Deflection Test
14.3.5. Air Flow Test
14.3.6. Compression Force Deflection Test
14.3.7. Dry Heat Test
14.3.8. Fatigue Test
14.3.9. Density Test
14.3.10. Tear‐Resistance Test
14.3.11. Tension Test
14.3.12. Resilience Test
14.4. FOAM PROPERTIES
GENERAL REFERENCES
15 FAILURE ANALYSIS. 15.1. INTRODUCTION
15.1.1. Material Selection
A. Material Selection Using Multipoint Data
B. Material Selection Process
C. Mechanical Properties
D. Thermal Properties
E. Exposure to Chemicals
F. Environmental Considerations
G. Regulatory Approval Requirements
H. Economics
I. Other Considerations
15.1.2. Design
15.1.3. Processing
A. Drying
B. Packing
C. Processing Temperature
D. Improper Additive/Regrind Mixing and Utilization
15.1.4. Service Conditions (Environmental Factors and User Abuse)
15.2. TYPES OF FAILURES
15.2.1. Mechanical Failure
A. Brittle Failures
B. Ductile Failures
C. Ductile to Brittle Transition
D. Fatigue Failures
E. Creep and Stress Relaxation
15.2.2. Thermal Failure
15.2.3. Chemical Failure
15.2.4. Environmental Failure
15.3. ANALYZING FAILURES
15.3.1. Visual Examination
15.3.2. Identification Analysis
15.3.3. Stress Analysis
A. Photoelastic Method
B. Brittle‐Coating Method
C. Strain Gauge Method
D. Chemical Method (Solvent Stress Analysis)
E. Heat Reversion Technique (ASTM F1057)
15.3.4. Microstructural Analysis (Microtoming)
15.3.5. Mechanical Testing
15.3.6. Thermal Analysis
15.3.7. Nondestructive Testing (NDT) Techniques
15.3.8. Fractography
15.3.9. Simulation Testing
15.4. CASE STUDIES
REFERENCES
GENERAL REFERENCES
CASE STUDY 1: COUNTERFEIT PLASTIC RESIN?* The Case
The Approach
End‐Group Analysis and Molecular Weight by NMR Spectroscopy
FTIR Analysis of Pressed Polymer Films
Extraction and Analysis of Additives
Conclusion
CASE STUDY 2: DUPLICATE FORMULATIONS*
The Approach
Fourier Transform Infrared Spectroscopy (FTIR)
Gas Chromatography (GC)
Notes
16 QUALITY CONTROL. 16.1. INTRODUCTION
16.2. STATISTICAL QUALITY CONTROL
16.2.1. Process Control Charts
A. Variables Control Charts ( and R Charts)
B. Control Charts for Attributes
16.2.2. Acceptance Sampling
A. Sampling Theory
B. Types of Sampling Plans
C. Classification of Sampling Plans
D. AQL Sampling Plan
E. Use of Sampling Tables
F. LTPD Sampling Plan
G .AOQL Sampling Plan
16.2.3. Process Capability. A. Introduction
B. Process Capability Studies
C. Process Capability Index, Cpk
16.2.4. Computerized Data Acquisition and Analysis
16.3. INTRODUCTION TO STATISTICAL PROCESS CONTROL. 16.3.1. Purpose of SPC
16.3.2. In‐Control Versus Out‐of‐Control Conditions
A. Out‐of‐Control Case 1: Outliers
B. Out‐of‐Control Case 2: Non‐normal Distribution
C. Out‐of‐Control Case 3: Time Dependencies
16.3.3. SPC, Process Capability and Quality
16.3.4. SPC Techniques
16.3.5. SPC Levels
16.4. QUALITY CONTROL SYSTEM. 16.4.1. Raw Material Quality Control
16.4.2. Process Quality Control
16.4.3. Product Quality Control
16.4.4. Visual Standards
16.4.5. Mold (Tool) Control
16.4.6. Workmanship Standards
16.4.7. Documentation
16.4.8. Quality Assurance Manual
16.5. GENERAL. 16.5.1. Quality Control and Machine Operators
16.6. SUPPLIER CERTIFICATION
REFERENCES
GENERAL REFERENCES
17 PRODUCT LIABILITIES AND TESTING. 17.1. INTRODUCTION
17.2. PRODUCT/EQUIPMENT DESIGN CONSIDERATIONS
17.3. PACKAGING CONSIDERATIONS
17.4. INSTRUCTIONS, WARNING LABELS, AND TRAINING
17.5. TESTING AND RECORDKEEPING
17.6. SAFETY STANDARDS ORGANIZATIONS
REFERENCES
SUGGESTED READING
18 NONDESTRUCTIVE TESTING AND MEASUREMENTS. 18.1. INTRODUCTION
18.2. ULTRASONIC
18.2.1. Pulse‐Echo Technique
18.2.2. Transmission Technique
18.2.3. Resonance Technique
18.3. APPLICATION OF ULTRASONIC NDT IN PLASTICS
18.4. GAMMA BACKSCATTER
18.5. BETA TRANSMISSION
18.6. SCANNING LASER
18.7. X‐RAY FLUORESCENCE
18.8. HALL EFFECT
18.9. CT SCANNING (X‐RAY COMPUTED TOMOGRAPHY)
REFERENCES
SUGGESTED READING
GENERAL REFERENCES
Note
19 PROFESSIONAL AND TESTING ORGANIZATIONS. 19.1. AMERICAN NATIONAL STANDARDS INSTITUTE (ANSI)
19.2. ASTM INTERNATIONAL
19.3. FOOD AND DRUG ADMINISTRATION (FDA)
19.4. NATIONAL INSTITUTE OF STANDARDS AND TECHNOLOGY (NIST)
19.5. NATIONAL ELECTRICAL MANUFACTURERS ASSOCIATION (NEMA)
19.6. NATIONAL FIRE PROTECTION ASSOCIATION (NFPA)
19.7. NATIONAL SANITATION FOUNDATION (NSF)
19.8. SOCIETY OF PLASTICS ENGINEERS (SPE)
19.9. PLASTICS INDUSTRY ASSOCIATION
19.10. UNDERWRITERS LABORATORIES (UL)
19.11. INTERNATIONAL ORGANIZATION FOR STANDARDIZATION (ISO)
20 UNIFORM GLOBAL TESTING STANDARDS. 20.1. INTRODUCTION
20.2. ISO/IEC STANDARDS
20.3. ISO AND ASTM
20.4. TEST DATA ACQUISITION AND REPORTING
20.4.1. Mold Design and Construction
20.4.2. Test Specimen Dimensions
20.4.3. Process Parameters
20.4.4. Injection Molding Machine
20.5. COMPUTER‐AIDED MATERIAL PRESELECTION BY UNIFORM STANDARDS (CAMPUS)
20.6. PLASTIC MATERIAL DATABASES
REFERENCES
APPENDIX A INDEX OF TEST EQUIPMENT MANUFACTURERS
ALPHABETICAL INDEX OF COMPANIES ADDRESSES, PHONE NUMBERS, AND WEBSITES
APPENDIX B ABBREVIATIONS: POLYMERIC MATERIALS
APPENDIX C GLOSSARY. A
B
C
D
E
F
G
H
I
K
L
M
N
O
P
R
S
T
U
V
W
Y
Z
APPENDIX D TRADE NAMES*
Note
APPENDIX E STANDARDS ORGANIZATIONS. American Gas Association (AGA)
American National Standards Institute (ANSI)
American Society for Quality (ASQ)
ASTM International
American Society of Safety Engineers
Association of Home Appliance Manufacturers
BSI Group, UK
European Organization for Quality (EOQ)
EUROLAB (A European Organization for Laboratory Testing)
FM Global
International Association of Plumbing and Mechanical Officials (IAPMO)
International Organization for Standardization (ISO)
Juvenile Products Manufacturer’s Association
National Association for Surface Finishing
National Electrical Manufacturers Association (NEMA)
National Fire Protection Association (NFPA)
National Institute of Standards and Technology (NIST)
National Safety Council (NSC)
NSF International (NSF)
Polyurethane Manufacturer’s Association (PMA)
Plastics Industry Association (Plastics)
Underwriters Laboratories (UL)
APPENDIX F LINKS TO RECOMMENDED OPEN SOURCE FOR QUICK LEARNING
APPENDIX G WEB RESOURCES
APPENDIX H FIGURE 15‐5. NEW APPLICATION CHECKLIST (Courtesy of Covestro)
INDEX
WILEY END USER LICENSE AGREEMENT
Отрывок из книги
FOURTH EDITION
VISHU SHAH
.....
Over the past two decades, plastics testing has changed dramatically. Significant advances in materials and the increasingly demanding nature of plastics applications have combined with global demand for uniformity to produce a requirement for data that goes beyond basic material comparison. Data today are used for design purposes and complex models for the prediction of a material’s end‐use compatibility. As a result, the testing technology that was adequate to provide data in the past has, in some cases, become obsolete and major advances in testing equipment sophistication have been developed to create a whole new environment in the plastics laboratory. One of the main areas for future advancement will be related to the use of plastics‐based composites in the Automobile Industry. Recent amendments to the United States Government Corporate Average Fuel Economy (CAFÉ) regulatory requirements set a national fuel economy standard of 35 mpg by 2020. One of the ways automobile manufacturers will try and meet this goal will be through “light‐weighting”—the replacement of heavy metal parts, both structural and nonstructural, with plastics and plastic‐based composites. Advanced test methods that relate specifically to these new applications will be crucial to the success of the industry to meet the challenge.
The traditional laboratory of the past generated material data using methods that were developed from metals standards and other industries. While adequate for comparing one material to another for basic similarities and differences, the information that was generated did not reflect the variables that are specific to polymers—that is, the effect of temperature on properties and the important role that polymer structure plays on its overall performance in the end‐use application. With the complexity of the applications for polymers increasing, the need for more sophisticated testing techniques has also increased. State‐of‐the‐art polymer testing laboratories today utilize test equipment that is fully instrumented and capable of collecting data with higher accuracy that not only includes the basic properties but also the more complicated effect of external variables on those properties.
.....