Automation of Water Resource Recovery Facilities
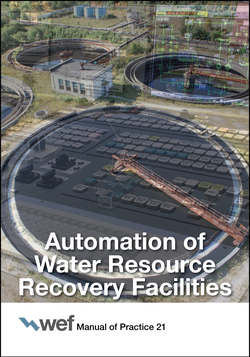
Реклама. ООО «ЛитРес», ИНН: 7719571260.
Оглавление
Water Environment Federation. Automation of Water Resource Recovery Facilities
Contents
List of Figures
List of Tables
Preface
Chapter 1. Introduction to Automation of Water Resource Recovery Facilities. Robert D. Hill, Ph.D, P.E
1.0 WHAT IS COMPLETE AUTOMATION DESIGN?
2.0 MOTIVATION FOR UPDATING THIS MANUAL
3.0 TECHNOLOGY AS A STRATEGY, NOT A LIMITATION
4.0 WHAT THIS MANUAL DOES AND DOES NOT INCLUDE
5.0 INTENDED AUDIENCE
6.0 MANUAL OF PRACTICE CHAPTER CONTENTS
7.0 REFERENCES
8.0 SUGGESTED READINGS
Chapter 2. The Business Case for Automation. David B. Kubel, P.E. Dave W. Roberts, P.E
1.0 INTRODUCTION
2.0 BENEFITS OF AUTOMATION
2.1 Tangible Economic Benefits
2.1.1 Labor Savings
2.1.2 Energy Savings
2.1.3 Chemical Savings
2.1.4 Additional Savings
2.2 Intangible Economic Benefits. 2.2.1 Compliance Monitoring
2.2.2 Improved Process Performance and Reliability
2.2.3 Improved Responsiveness
2.2.4 Enhanced Decision Making
2.2.5 Reduced Risk
2.2.6 Workforce Morale and Aging
2.2.7 Customer Satisfaction
3.0 AUTOMATION COSTS
3.1 Planning and Engineering
3.2 Equipment Procurement
3.3 Installation, Commissioning, Testing, and Training
3.4 Post Acceptance Support and Maintenance
3.5 Intangible Costs
3.6 Hardware and Software Life Expectancy
4.0 COST–BENEFIT ANALYSIS
4.1 Financial Analysis
4.1.1 Simple Payback Period
4.1.2 Return on Investment
4.1.3 Life Cycle Costs and Net Present Value
4.2 Risk Analysis
4.3 Approaches to Incorporate Intangible Benefits
4.3.1 Asset Management
4.3.2 Triple Bottom Line
4.3.3 Balanced Scorecard
5.0 FORMULATING THE BUSINESS CASE
6.0 REFERENCES
7.0 SUGGESTED READINGS
Chapter 3. Complete Automation Design. Peter R. Craan, P.E., CAP
1.0 THE DESIGN PROCESS
1.1 Project Structure
1.2 Predesign Phase
1.3 Detailed Design Phase
1.4 Final Design Phase
2.0 DESIGN DOCUMENTS
2.1 Bid Documents. 2.1.1 Specifications
2.1.1.1 General Requirements for Process Automation Systems
2.1.1.2 Factory Testing
2.1.1.3 Panel Enclosure
2.1.1.4 Operator Interface Terminals
2.1.1.5 Panel-Mounted Devices
2.1.1.6 Networking Equipment
2.1.1.7 Input/Output List
2.1.1.8 Instrument List or Index
2.1.1.9 Network Cabling
2.1.1.10 Uninterruptible Power Supplies
2.1.1.11 Process Control Narratives
2.1.1.12 Programming Standards
2.1.1.13 Field Instruments
2.1.2 Drawings. 2.1.2.1 Process Flow Diagrams
2.1.2.2 Process and Instrument Diagrams
2.1.2.3 Process Control System Architecture Diagram
2.1.2.4 Elementary Wiring Diagrams
2.1.2.5 Instrumentation and Panel Location Drawings
2.1.2.6 Instrumentation Installation Details
2.2 Automation Design Implementation Documents
2.2.1 Loop Diagrams
2.2.2 Interconnecting Wiring Diagrams
2.2.3 Control Panel Design Drawings
2.2.4 Programmable Logic Controller Program
2.2.5 Distributed Control System Configuration
2.2.6 Instrument Data Sheets
2.2.7 Detailed Process Control Narratives
2.2.8 Logic Diagrams and Detailed Process Control Sequence Flow Charts
2.3 Sources of Technical Design Information. 2.3.1 Technical Societies
2.3.2 Vendors
2.3.2.1 Selecting Vendors and Technologies
2.3.2.2 Incorporating Selected Technologies to Design
2.3.3 Books and Periodicals
2.3.4 The Internet. 2.3.4.1 Web Sites
2.3.4.2 Social Media
2.3.5 Training
2.3.6 Previous Design Experience
3.0 POSTDESIGN PHASE. 3.1 Design Services During Construction
3.1.1 Submittals
3.1.2 Change Orders. 3.1.2.1 Change Order Management
3.1.2.2 Common Risk Areas for Change Orders
3.1.3 Responding to Requests for Information and Request for Clarifications
3.1.4 Meetings with Contractors and Suppliers
3.1.5 Site Visits
3.1.6 Factory Acceptance Tests
3.1.6.1 System Performance
3.1.6.2 Hardware Testing
3.1.6.3 Software Testing
3.1.6.4 Simulation Software
3.1.6.5 Operator Interface Terminals and Operator Workstations
3.2 Construction Management
3.2.1 Installation Inspections
3.2.2 Instrument Calibrations
3.2.3 Field Tests
3.2.4 Wiring Tests
3.2.5 Loop Testing
3.2.6 Integrated System Testing
3.2.7 Commissioning and Final Acceptance
3.2.8 As-Built Drawings and Final Control System Documentation
4.0 REFERENCES
5.0 SUGGESTED READINGS
Chapter 4. Process and Instrumentation Diagram. Peter R. Craan, P.E., CAP
1.0 INTRODUCTION
2.0 HOW TO CREATE A PROCESS AND INSTRUMENTATION DIAGRAM
2.1. Process Flow Diagrams
2.1.1 Symbols
2.1.2 Computer-Aided Design Software
2.2 Instrument List
2.3 Input/Output List
2.4 Panel List
2.5 Cable and Conduit List
2.6 Process Control Narratives
2.7 Panel and Field Instrument Specifications
2.8 Electrical Schematics
2.9 Instrument Loop Diagrams
2.10 Equipment Location Drawings
2.11 Control System Architecture Diagram
3.0 PROCESS AND INSTRUMENTATION DIAGRAMS AS COMMUNICATION TOOLS. 3.1 Contract Bid Documents
3.2 End User and Owner Feedback
3.3 Operator Training
3.4 Operator-Interface Graphics Development
3.5 As-Built Documentation
3.6 Coordination with Other Design Disciplines
4.0 INTELLIGENT PROCESS AND INSTRUMENTATION DIAGRAMS
4.1 Streamlined Diagram Development
4.1.1 Object-Based Schematics
4.1.2 Modular System
4.1.3 Integration with External Data Sources
4.1.4 Interoperability
4.1.5 Symbol Management Tools
4.1.6 Review and Navigation Tools
4.1.7 Component Management Tools
4.2 Automatically Generated Lists
4.3 Design History for As-Built Drawings
4.4 Construction, Startup, Operation, Maintenance, and Asset Management Uses
5.0 PROCESS AND INSTRUMENTATION DIAGRAMS FOR NONPROCESS SYSTEMS
6.0 REFERENCES
7.0 SUGGESTED READINGS
Chapter 5. Process Control Narratives. Jeff Coulson, P. Eng, PMP. Jack Geisenhoff, P.E., PMP
1.0 PURPOSE OF PROCESS CONTROL NARRATIVES
2.0 TYPICAL PROCESS CONTROL NARRATIVE COMPONENTS
2.1 Equipment and Tag Numbers
2.2 Process and Instrumentation Diagrams
2.3 System Components
2.4 Flow Charts
2.5 Control Hierarchy
2.5.1 Local Controls
2.5.2 Motor Control Center Functions
2.5.3 Controller Functions
2.5.4 Remote Manual Controls
2.5.5 Remote Automatic Controls
2.6 Alarms
2.7 Setpoints
2.8 Performance Reporting Data
3.0 OTHER METHODS OF CONVEYING PROCESS DESCRIPTIONS
3.1 Animations
3.2 Static Process Models
3.3 Interactive Process Models
4.0 DEVELOPMENT, UPDATES, AND PRESENTATION
4.1 Document Development and Updates
4.2 Document Storage and Presentation
5.0 REFERENCE
Chapter 6. Specifications. Thomas H. Powell, P.E., C.C.S. Mohamad Bassidgi, P. Eng
1.0 RELATIONSHIP OF SPECIFICATIONS AND DRAWINGS
2.0 SPECIFICATIONS. 2.1 Standard Specifications
2.2 Project-Specific Specifications
2.3 Vendor-Supplied and -Suggested Specifications
2.4 Master Specification Guidelines
2.5 MasterFormat 1995
2.6 MasterFormat 2004
2.7 Whole Building Design Guide
3.0 REVISIONS TO TECHNICAL CONTENT. 3.1 Notes to Specifiers
3.2 Installation Lessons Learned
4.0 INSTRUMENT DATA SHEETS
5.0 CONSTRUCTION SPECIFICATIONS INSTITUTE. 5.1 Performance-Based Specifications
5.2 Descriptive Specifications
6.0 OWNER-DEVELOPED SPECIFICATIONS
7.0 COORDINATION WITH OTHER DISCIPLINES
8.0 REFERENCES
9.0 SUGGESTED READINGS
Chapter 7. Process Control Strategies. Jack Geisenhoff, P.E., PMP. Mike Abbott, P.E. Jeff Coulson, P. Eng, PMP. Richard S. Haugh, P.E. Robert D. Hill, Ph.D, P.E
1.0 OBJECTIVE OF AUTOMATIC PROCESS CONTROL
2.0 CONTROL THEORY
3.0 MISTAKE PROOFING
4.0 CONTROL CONCEPTS
4.1 On–Off Control Versus Modulating Control
4.2 Open-Loop Versus Closed-Loop Control
4.3 Feed Forward Versus Feedback Control
4.4 Step Control
4.5 Proportional–Integral–Derivative Control
4.6 Cascade Control
4.7 Rules-Based Control
4.8 Model Predictive Control
4.9 Artificial Neural Networks
4.9.1 Artificial Neural Network Models
4.9.2 Artificial Neural Network Models Used for Process Modeling
4.9.3 Artificial Neural Network Models Used for Process Control
4.10 Control Strategies
4.10.1 Lead–Lag Control
4.10.2 Most-Open Valve Control
5.0 PUMPING AND FLOW CONTROL STRATEGIES. 5.1 Process Description
5.1.1 Well Pumping
5.1.2 Flow Pumping
5.1.3 Flow Splitting
5.2 Process Variables
5.3 Controlled Variables
5.4 Control Strategies. 5.4.1 Well Pumping—Constant-Speed Pumps
5.4.2 Well Pumping—Variable-Speed Pumps
5.4.3 Flow Pumping
5.4.4 Flow Splitting with Valves or Gates
6.0 SCREENING, GRIT REMOVAL, AND CONVEYANCE CONTROL STRATEGIES. 6.1 Process Description
6.1.1 Bar Screens
6.1.2 Grit Removal
6.1.3 Conveyance Systems
6.2 Process Variables
6.3 Controlled Variables
6.4 Control Strategies. 6.4.1 Bar Screen Velocity Control
6.4.2 Bar Screen Cleaning Control
6.4.3 Grit Settling Velocity Control
6.4.4 Grit Removal Control
6.4.5 Conveyance System Control
7.0 PRIMARY SLUDGE AND SCUM CONTROL STRATEGIES. 7.1 Process Description
7.1.1 Sludge Removal
7.1.2 Scum Removal
7.2 Process Variables
7.3 Controlled Variables
7.4 Control Strategies. 7.4.1 Sludge Removal Control—Dedicated Pump
7.4.2 Sludge Removal Control—Valve to Common Pump
7.4.3 Scum Trough Operation Control
7.4.4 Scum Pit Level Control
8.0 ACTIVATED SLUDGE SYSTEM CONTROL STRATEGIES. 8.1 Dissolved Oxygen Control. 8.1.1 Process Description
8.1.2 Process Variables
8.1.3 Controlled Variables
8.1.4 Control Strategies
8.2 Ammonia Control
8.2.1 Process Description
8.2.2 Process Variables
8.2.3 Controlled Variables
8.2.4 Control Strategies
8.3 Denitrification Control. 8.3.1 Process Description
8.3.2 Process Variables
8.3.3 Controlled Variables
8.3.4 Control Strategies
8.4 Activated Sludge Clarifier Blanket Level Control. 8.4.1 Process Description
8.4.2 Process Variables
8.4.3 Controlled Variables
8.4.4 Control Strategies
8.5 Waste Sludge Control. 8.5.1 Process Description
8.5.2 Process Variables
8.5.3 Controlled Variables
8.5.4 Control Strategies
9.0 CHEMICAL FEED SYSTEMS. 9.1 Disinfection Control
9.1.1 Process Description
9.1.2 Process Variables
9.1.3 Controlled Variables
9.1.4 Control Strategies
9.1.4.1 Feed-Forward Flow Proportioning
9.1.4.2 Simple Residual Feedback Control
9.1.4.3 Flow and Residual Control
9.2 Dechlorination Control
9.2.1 Process Description
9.2.2 Process Variables
9.2.3 Controlled Variables
9.2.4 Control Strategies
9.2.5 Difficult-to-Measure Process Variable
9.2.6 Time Delays
9.2.7 Feed-Forward Control
9.2.8 Feedback and Compound Control
9.2.9 Two-Step Control
9.2.10 Dechlorinated Final Effluent Residual Measurement
9.2.11 Recommendations
10.0 THICKENING CONTROL
10.1 Gravity Thickening Control Strategies. 10.1.1 Process Description
10.1.2 Process Variables
10.1.3 Controlled Variables
10.1.4 Control Strategies. 10.1.4.1 Sludge Removal Flow Control
10.1.4.2 Sludge Blanket Control
10.1.4.3 Solids Concentration Control
10.1.4.4 Rake Torque Control
10.2 Dissolved Air Floatation Control Strategies. 10.2.1 Process Description
10.2.2 Process Variables
10.2.2.1 Dissolved Air Floatation Sludge Thickener
10.2.2.2 Dissolved Air Floatation Sludge Well
10.2.3 Controlled Variables
10.2.3.1 Dissolved Air Floatation Sludge Thickener
10.2.3.2 Dissolved Air Floatation Sludge Well
10.2.4 Control Strategies
10.2.4.1 Dissolved Air Floatation Air-to-Solids Ratio Control
10.2.4.2 Dissolved Air Floatation Solids Retention Time Control
10.2.4.3 Sludge Blanket Control
10.2.4.4 Polymer Feed Control
10.2.4.5 Thickened Dissolved Air Floatation Sludge Pump Control
10.3 Gravity Belt Control Strategies. 10.3.1 Process Description
10.3.2 Process Variables
10.3.2.1 Gravity Belt Sludge Thickener
10.3.2.2 Gravity Belt Sludge Well
10.3.3 Controlled Variables
10.3.3.1 Gravity Belt Sludge Thickener
10.3.3.2 Gravity Belt Sludge Well
10.3.4 Control Strategies
11.0 DEWATERING CONTROL
11.1 Centrifuge Control Strategies. 11.1.1 Process Description
11.1.2 Process Variables
11.1.3 Controlled Variables
11.1.4 Control Strategies
11.2 Belt Press Control Strategies. 11.2.1 Process Description
11.2.2 Process Variables
11.2.3 Controlled Variables
11.2.4 Control Strategies
12.0 ANAEROBIC DIGESTION CONTROL
12.1 Digester Feed and Level Control Strategies. 12.1.1 Process Description
12.1.2 Process Variables
12.1.3 Controlled Variables
12.1.4 Control Strategies
12.2 Digester Temperature Control Strategies. 12.2.1 Process Description
12.2.2 Process Variables
12.2.3 Controlled Variables
12.2.4 Control Strategies
12.3 Digester Gas Withdrawal Control Strategies. 12.3.1 Process Description
12.3.2 Process Variables
12.3.3 Controlled Variables
12.3.4 Control Strategies
13.0 INCINERATION CONTROL
13.1 Incineration Oxygen Control Strategies
13.1.1 Multiple-Hearth Incinerators. 13.1.1.1 Process Description
13.1.1.2 Process Variables
13.1.1.3 Controlled Variables
13.1.1.4 Control Strategies
13.1.2 Fluid Bed Incinerators. 13.1.2.1 Process Description
13.1.2.2 Process Variables
13.1.2.3 Controlled Variables
13.1.2.4 Control Strategies
13.2 Incineration Temperature Control Strategies
13.2.1 Multiple-Hearth Incinerators. 13.2.1.1 Process Description
13.2.1.2 Process Variables
13.2.1.3 Controlled Variables
13.2.1.4 Control Strategies
13.2.2 Fluid Bed Incinerators. 13.2.2.1 Process Description
13.2.2.2 Process Variables
13.2.2.3 Controlled Variables
13.2.2.4 Control Strategies
13.3 Incineration Pressure Control Strategies. 13.3.1 Process Description
13.3.2 Process Variables
13.3.3 Controlled Variables
13.3.4 Control Strategies
13.4 Offgas Wet Scrubber Control Strategies. 13.4.1 Process Description
13.4.2 Process Variables
13.4.3 Controlled Variables
13.4.4 Control Strategies
13.5 Flue Gas Carbon Feed and Baghouse Control Strategies. 13.5.1 Process Description
13.5.2 Process Variables
13.5.3 Controlled Variables
13.5.4 Control Strategies
13.6 Flue Gas Electrostatic Precipitator Control Strategies. 13.6.1 Process Description
13.6.2 Process Variables
13.6.3 Controlled Variables
13.6.4 Control Strategies
14.0 ENERGY MANAGEMENT STRATEGIES
14.1 Real-Time Power Monitoring
14.2 Controlling On-Peak Energy Demand
14.3 Controlling Power Factor
15.0 REFERENCES
16.0 SUGGESTED READINGS
Chapter 8. General Instrument Characteristics. Robert Lagrange, Ph.D. Nicholas Camin, BSEE, MBA
1.0 BACKGROUND
2.0 INSTRUMENT CLASSIFICATIONS. 2.1 Measurement Types
2.1.1 Discrete
2.1.2 Analog Continuous
2.1.3 Analog Batch
2.2 Sampling Method
2.2.1 Point Sensors
2.2.2 Nonpoint Sensors
2.3 Measurement Method
2.3.1 Direct Measurements
2.3.2 Indirect Measurements
2.3.3 Inferential Measurements
2.4 Transmitters
2.4.1 Terminal Strip
2.4.2 Power Supply
2.4.3 Printed Circuit Cards
2.4.4 Connectors
2.4.5 Display
3.0 INSTRUMENT CHARACTERISTICS. 3.1 Properties
3.1.1 Range
3.1.2 Span
3.1.3 Rangeability
3.1.4 Limit of Detection
3.1.5 Limit of Quantification
3.1.6 Over-Range
3.1.7 Zero Suppression, Elevation, and Offset
3.1.8 Damping
3.2 Static Characteristics
3.2.1 Zero Error
3.2.2 Span Error
3.2.3 Hysteresis
3.2.4 Deadband
3.2.5 Linearity
3.2.6 Drift
3.2.7 Repeatability
3.3 Dynamic Characteristics
3.4 Conversions to Engineering Units
3.4.1 Linear Conversion
3.4.2 Nonlinear Conversion
3.4.3 Nonlinear, Non-Zero-Based Conversion
4.0 ENVIRONMENTAL CONCERNS AND DESIGN CONSIDERATIONS
4.1 Wastewater Characteristics
4.1.1 Plastic Products
4.1.2 Hair and Fibers
4.1.3 Solids
4.1.4 Grease
4.1.5 Color
4.1.6 Sulfides and Hydrogen Sulfide
4.1.7 Diurnal and Seasonal Changes
4.1.8 Composition Changes
4.2 Temperature
4.3 Moisture
4.3.1 Short-Circuits
4.3.2 Swelling
4.4 Corrosion
4.5 Ultraviolet Light
4.6 Electrical Concerns. 4.6.1 Voltage Spikes and Sags
4.6.2 Surge-Protective Devices
4.6.3 Grounding
4.6.4 Shielding
4.7 Responses to Environmental Concerns
4.7.1 Enclosures and Electronic Standards
4.7.2 Enclosed Spaces
4.7.3 Explosive Areas
4.7.4 Temperature Controls
4.7.5 Fire Ants and Pests
5.0 TESTING AND QUALITY ASSURANCE
5.1 Testing
5.1.1 Need for Instrumentation Testing
5.1.2 Instrumentation Test Reports
5.1.3 Testing
5.2 Standards, Calibration, and Verification. 5.2.1 Standards
5.2.1.1 Sources and Types
5.2.1.2 Other Standards
5.2.2 Calibrations
5.2.2.1 Primary Standards
5.2.2.2 Secondary Standards
5.2.2.3 Traceable Standards
5.2.2.4 Portable Standards
5.2.3 Verification
6.0 SAMPLING AND BYPASS LINES FOR INSTRUMENTS
6.1 Basic Considerations
6.2 Other Considerations
6.3 Advance Sampling
7.0 SMART PROCESS INSTRUMENTATION
7.1 Digital Sensors
7.2 Control System Connections
7.2.1 Buses
7.2.2 Ethernet
8.0 DOCUMENTATION
9.0 REFERENCES
10.0 SUGGESTED READINGS
Chapter 9. Sensors. Charles K. Aycock. Ron Bur dick, P.E. Cesar Canal. Bob Dabkowski. Tracy Doane-Weideman. Robert Lagrange, Ph.D
1.0 INTRODUCTION
2.0 FLOW METERS
2.1 Process Fluid
2.2 Process Variants
2.3 Flowrate
2.4 Meter Performance. 2.4.1 Error
2.4.2 Repeatability
2.4.3 Installation
2.4.4 Maintenance
2.4.5 Life Cycle
2.5 Electromagnetic Flow Meters
2.5.1 Operating Principles
2.5.2 Construction Materials
2.5.3 Error and Interferences
2.5.4 Installation
2.5.5 Maintenance Requirements
2.6 Ultrasonic Flow Meters
2.6.1 Operating Principles
2.6.2 Construction Materials
2.6.3 Error and Interferences
2.6.4 Installation
2.6.5 Maintenance Requirements
2.7 Weirs and Flumes
2.7.1 Operating Principle
2.7.2 Construction Materials
2.7.3 Error and Interferences
2.7.4 Installation
2.7.5 Maintenance Requirements
2.8 Differential Pressure. 2.8.1 Pitot Tube-Type Flow Meters
2.8.1.1 Operating Principles
2.8.1.2 Construction Materials
2.8.1.3 Error and Interferences
2.8.1.4 Installation
2.8.1.5 Maintenance Requirements
2.8.2 Venturi Flow Meters
2.8.2.1 Operating Principles
2.8.2.2 Construction Materials
2.8.2.3 Error and Interferences
2.8.2.4 Installation
2.8.2.5 Maintenance Requirements
2.9 Mechanical—Rotary, Turbine, or Propeller
2.9.1 Operating Principles
2.9.2 Construction Materials
2.9.3 Error and Interferences
2.9.4 Installation
2.9.5 Maintenance Requirements
2.10 Variable Area
2.10.1 Operating Principles
2.10.2 Construction Materials
2.10.3 Error and Interferences
2.10.4 Installation
2.10.5 Maintenance Requirements
2.11 Mass
2.11.1 Coriolis
2.11.1.1 Operating Principles
2.11.1.2 Construction Materials
2.11.1.3 Error and Interferences
2.11.1.4 Installation
2.11.1.5 Maintenance Requirements
2.11.2 Thermal Dispersion
2.11.2.1 Operating Principles
2.11.2.2 Construction Materials
2.11.2.3 Error and Interferences
2.11.2.4 Installation
2.11.2.5 Maintenance Requirements
3.0 LEVEL
3.1 Continuous
3.1.1 Bubbler
3.1.1.1 Operating Principles
3.1.1.2 Construction Materials
3.1.1.3 Error and Interferences
3.1.1.4 Installation
3.1.1.5 Maintenance Requirements
3.1.2 Capacitance
3.1.2.1 Operating Principles
3.1.2.2 Construction Materials
3.1.2.3 Error and Interferences
3.1.2.4 Installation
3.1.2.5 Maintenance Requirements
3.1.3 Differential Pressure. 3.1.3.1 Operating Principles
3.1.3.2 Construction Materials
3.1.3.3 Error and Interferences
3.1.3.4 Installation
3.1.3.5 Maintenance Requirements
3.1.4 Sonic and Ultrasonic
3.1.4.1 Operating Principles
3.1.4.2 Construction Materials
3.1.4.3 Error and Interferences
3.1.4.4 Installation
3.1.4.5 Maintenance Requirements
3.1.5 Microwave (Radar)
3.1.5.1 Operating Principles
3.1.5.2 Construction Materials
3.1.5.3 Error and Interferences
3.1.5.4 Installation
3.1.5.5 Maintenance Requirements
3.2 Level Switches
3.2.1 Operating Principles
3.2.2 Construction Materials
3.2.3 Error and Interferences
3.2.4 Installation
3.2.5 Maintenance Requirements
4.0 PRESSURE
4.1 Operating Principles
4.2 Construction Materials
4.3 Error and Interferences
4.4 Installation
4.5 Maintenance Requirements
5.0 TEMPERATURE
5.1 Principles of Operation. 5.1.1 Thermocouple
5.1.2 Resistance
5.1.3 Thermister
5.2 Construction Materials
5.3 Error and Interferences
5.4 Installation
5.5 Maintenance Requirements
6.0 DISSOLVED OXYGEN
6.1 Operating Principles
6.1.1 Conventional Galvanic Measuring Cell
6.1.2 Clark Polarographic Measuring Cell
6.1.3 Ross Polarographic Measuring Cell
6.1.4 Luminescent Dissolved Oxygen Sensor
6.2 Construction Materials
6.3 Error and Interferences
6.4 Installation
6.5 Maintenance Requirements
7.0 CHLORINE RESIDUAL
7.1 Operating Principles
7.1.1 N, N-diethyl-p-phenylenediamine Colorimetric Method Analyzer
7.1.2 Amperometric Bare-Electrode Analyzer
7.1.3 Amperometric Membrane-Covered-Electrode Analyzer
7.2 Construction Materials
7.3 Error and Interferences
7.4 Installation
7.5 Maintenance Requirements
8.0 pH
8.1 Operating Principles. 8.1.1 Glass pH Sensor
8.1.2 Ion-Sensitive Field Effect Transistor
8.2 Construction Materials
8.3 Error and Interferences
8.4 Installation
8.5 Maintenance Requirements
9.0 OXIDATION–REDUCTION POTENTIAL
9.1 Operating Principle
9.2 Construction Materials
9.3 Error and Interferences
9.4 Installation
9.5 Maintenance Requirements
10.0 CONDUCTIVITY
10.1 Principles of Operation
10.2 Construction Materials
10.3 Error and Interferences
10.4 Installation
10.5 Maintenance Requirements
11.0 STREAMING CURRENT
11.1 Operating Principles
11.2 Construction Materials
11.3 Error and Interferences
11.4 Installation
11.5 Maintenance Requirements
12.0 NUTRIENT ANALYZERS
12.1 Ammonia and Ammonium
12.1.1 Operating Principles
12.1.1.1 Ion-Selective Electrode
12.1.1.2 Gas-Sensing Electrode
12.1.1.3 Colorimetric Methods
12.1.2 Construction Materials
12.1.3 Error and Interferences
12.1.4 Installation
12.1.5 Maintenance Requirements
12.2 Nitrate and Nitrite
12.2.1 Operating Principles. 12.2.1.1 Ultraviolet Absorbance
12.2.1.2 Ion-Selective Electrode
12.2.2 Construction Materials
12.2.3 Error and Interferences
12.2.4 Installation
12.2.5 Maintenance Requirements
12.3 Total Nitrogen
12.3.1 Operating Principles
12.3.2 Construction Materials
12.3.3 Error and Interferences
12.3.4 Installation
12.3.5 Maintenance Requirements
12.4 Orthophosphate and Total Phosphorus
12.4.1 Orthophosphate
12.4.1.1 Operating Principles
12.4.1.2 Construction Materials
12.4.1.3 Error and Interferences
12.4.1.4 Installation
12.4.1.5 Maintenance Requirements
12.4.2 Total Phosphorus
12.4.2.1 Operating Principles
12.4.2.2 Construction Materials
12.4.2.3 Error and Interferences
12.4.2.4 Installation
12.4.2.5 Maintenance Requirements
12.5 Organics
12.5.1 Total Organic Carbon
12.5.1.1 Operating Principles. 12.5.1.1.1 HIGH-TEMPERATURE COMBUSTION
12.5.1.1.2 HEATED PERSULFATE ULTRAVIOLET OXIDATION
12.5.1.1.3 SUPERCRITICAL WATER OXIDATION
12.5.1.1.4 TWO-STAGED ADVANCED OXIDATION
12.5.1.1.5 ULTRAVIOLET ABSORPTION
12.5.1.2 Construction Materials
12.5.1.3 Error and Interferences
12.5.1.4 Installation
12.5.1.5 Maintenance Requirements
12.5.2 Biochemical Oxygen Demand
12.5.2.1 Operating Principles
12.5.2.2 Construction Materials
12.5.2.3 Error and Interferences
12.5.2.4 Installation
12.5.2.5 Maintenance Requirements
12.5.3 Chemical Oxygen Demand
12.5.3.1 Operating Principles. 12.5.3.1.1 COLORIMETRIC
12.5.3.1.2 ELECTROCHEMICAL OXIDATION
12.5.3.1.3 THERMAL OXIDATION
12.5.3.2 Construction Materials
12.5.3.3 Error and Interferences
12.5.3.4 Installation
12.5.3.5 Maintenance Requirements
13.0 ONLINE SOLIDS MEASUREMENT. 13.1 Total Suspended Solids
13.1.1 Operating Principles. 13.1.1.1 Near-Infrared Analyzers
13.1.1.2 Microwave Analyzers
13.1.2 Construction Materials
13.1.3 Error and Interferences
13.1.4 Installation
13.1.5 Maintenance Requirements
13.2 Interface/Sludge Blanket Level Analyzers
13.2.1 Operating Principles. 13.2.1.1 Ultrasonic Interface/Sludge Blanket Level Analyzers
13.2.1.2 Optical Interface/Sludge Blanket Level Analyzers
13.2.2 Construction Materials
13.2.3 Error and Interferences
13.2.4 Installation
13.2.4.1 Inline with Skimmers or Flights
13.2.4.2 Offline with Skimmers or Flights
13.2.4.3 Fixed Submerged Location
13.2.5 Maintenance Requirements
13.3 Turbidity
13.3.1 Operating Principles. 13.3.1.1 White Light
13.3.1.2 Near Infrared
13.3.2 Construction Materials
13.3.3 Errors and Interferences
13.3.4 Installation
13.3.5 Maintenance
14.0 GAS ANALYZERS. 14.1 Operating Principles
14.1.1 Catalytic
14.1.2 Infrared
14.1.3 Electrochemical
14.1.4 Solid-State Sensing
14.2 Construction Materials
14.3 Error and Interferences
14.4 Installation
14.5 Maintenance Requirements
15.0 VIBRATION
15.1 Operating Principles
15.1.1 Velocity Transducers
15.1.2 Acceleration Transducers
15.1.3 Displacement Transducers
15.2 Construction Materials
15.3 Accuracy and Interferences
15.4 Installation
15.4.1 Flush-Mount Transducers
15.4.2 Surface-Mount Transducers
15.5 Maintenance Requirements
16.0 REFERENCES
17.0 SUGGESTED READINGS
Chapter 10. Final Control Elements. Edward Baltutis
1.0 WHAT IS A FINAL CONTROL ELEMENT?
1.1 Outputs
1.2 Signal Conditioners
1.3 Power Source or Actuator and Coupling
1.4 Final Control Element
1.5 Mechatronics
2.0 VALVES. 2.1 Components of a Valve
2.2 Valve Characteristics
2.3 Valve Types
2.3.1 Globe Valves
2.3.2 Solenoid Valves
2.3.3 Ball Valves
2.3.4 Diaphragm Valves
2.3.5 Plug Valves
2.3.6 Butterfly Valves
2.3.7 Gate Valves
2.3.8 Other
2.4 Valve Standards
2.5 Valve Selection
2.6 Valve Sizing
2.7 Valve Actuators
2.7.1 Solenoid
2.7.2 Electric Motor
2.7.3 Pneumatic
2.7.4 Hydraulic
2.7.5 Failure Mode
2.8 Valve Positioners
3.0 PUMPS, AERATORS, AND MIXERS (MATERIAL TRANSFER EQUIPMENT)
3.1 Pumps (Material Transfer Equipment)
3.1.1 Components of a Pump
3.1.2 Pump Types
3.1.2.1 Displacement Pumps
3.1.2.2 Nondisplacement Pumps
3.1.2.3 Lift Pumps
3.2 Blowers
3.3 Fans and Compressors
3.4 Aerators and Mixers
4.0 ELECTRIC MOTORS
5.0 STARTERS
6.0 DRIVES
6.1 Variable-Frequency Drives
6.2 Wire-Wound Motor Control
6.3 Variable-Torque Speed Controls
7.0 CONTROL SIGNAL INTERFACE
8.0 SMART EQUIPMENT (VALVES, PUMPS, AND BLOWERS)
9.0 OTHER FINAL CONTROL DEVICES
10.0 SUGGESTED READINGS
Chapter 11. Communications and Connectivity. Bob “SCADAbob” Rutemiller, M.S. John Weber
1.0 OVERVIEW OF COMMUNICATIONS
2.0 BASIC COMMUNICATIONS CONCEPTS. 2.1 System Terminology
2.1.1 Bandwidth
2.1.2 Client
2.1.3 Distributed Control System
2.1.4 Driver
2.1.5 Ethernet
2.1.6 Human–Machine Interface
2.1.7 Input/Output Server
2.1.8 Inverter
2.1.9 Internet Protocol Address
2.1.10 Master
2.1.11 Media
2.1.12 Motor Control Center
2.1.13 Packet
2.1.14 Personal Computer
2.1.15 Peer-to-Peer
2.1.16 Proportional–Integral–Derivative
2.1.17 Programmable Logic Controller
2.1.18 Power over Ethernet
2.1.19 Protocol
2.1.20 The RJ-45 Connector
2.1.21 The RS-232 Standard
2.1.22 The RS-422 and RS-485 Standards
2.1.23 Remote Terminal Unit
2.1.24 Supervisory Control and Data Acquisition
2.1.25 Serial
2.1.26 Server
2.1.27 Transmission Control Protocol/Internet Protocol
2.1.28 Transport
2.1.29 Variable-Frequency Drives
2.2 Network Components
2.2.1 Application Protocols
2.2.2 Network Protocol Transport
2.2.3 Physical Transport Media
2.2.4 How Network Components Relate
3.0 COMMUNICATION DETAILS. 3.1 Network Types
3.1.1 Serial Networks
3.1.2 Proprietary Networks
3.1.3 Master Versus Peer-to-Peer
3.1.4 Fieldbus Networks
3.1.5 Ethernet Networks
3.1.6 Virtual Private Networks
3.2 Application Protocols. 3.2.1 Proprietary Versus Open
3.2.2 Modbus Family Protocols
3.2.3 The DF1 Protocol
3.2.4 Distributed Network Protocol 3
3.2.5 EtherNet/Internet Protocol
3.2.6 Industrial Ethernet
3.2.7 DeviceNet
3.2.8 ControlNet
3.2.9 ProfiBUS and ProfiNET
3.2.10 Highway Addressable Remote Transducer
3.2.11 The S908 Network
3.2.12 Remote Input/Output
3.3 Hardware. 3.3.1 Basic Network Hardware
3.3.1.1 Hubs Versus Switches
3.3.1.2 Routers Versus Switches
3.3.1.3 Routers Versus Firewalls
3.3.2 Integrated Network Control Systems
3.3.3 Thick Clients Versus Thin Clients
3.3.3.1 Terminal Servers
3.3.3.2 Thin Servers
4.0 ETHERNET INDEPTH
4.1 Defining Ethernet
4.2 Wiring Types
4.2.1 Twisted-Pair Copper Ethernet
4.2.2 Fiber Optic Cable
4.2.2.1 Multimode Versus Single Mode
4.2.2.2 Fiber Optic Star Configuration
4.2.2.3 Fiber Optic Ring Configuration
4.2.2.4 Single Fiber Optic Ring
4.2.2.5 Redundant Fiber Optic Ring
4.2.2.6 Fiber Optic Termination Standards
4.2.3 Fiber Optic Is Not Always Ethernet
4.3 Ethernet Wireless Transports
4.4 Bridging the Gap to Non-Ethernet Devices
4.5 Ethernet Encapsulation
4.6 Ethernet/Proprietary Network Bridges
4.7 Common Ethernet Application Protocols
5.0 COMMUNICATIONS TROUBLESHOOTING. 5.1 Importance of Basic Troubleshooting Concepts
5.2 Variables in Communications
5.3 Communications Protocol Troubleshooting Concepts and Tools
5.4 Monitoring for Problems Before They Happen—Tools and Techniques. 5.4.1 Network Infrastructure
5.4.2 Computers
5.5 Leveraging Digital Communications
5.6 Leveraging Embedded-Device Web Pages
5.7 Troubleshooting Checklist
6.0 WIRELESS CONNECTIVITY
6.1 Spread-Spectrum Communications
6.2 Cellular Communications
6.3 Static Versus Dynamic Addressing
6.4 Data Use Considerations
6.5 Programming Requirements
6.6 Signal Strength
6.7 Service Provider Interruptions
6.8 Purchasing Bulk Data Service
6.9 In-Facility Wireless Applications
6.10 Remote-Site Wireless. 6.10.1 Connection to Hardware
6.10.2 Network Address Translation
6.10.3 Special Value of Distributed Network Protocol 3
6.11 Wireless Security
6.12 Wireless Ethernet Radio Reliability
6.13 Cellular Reliability
6.14 Cellular-on-Wheels
6.15 Wireless Solutions and Communications Software
7.0 COMMUNICATIONS REDUNDANCY
7.1 Types of Redundancy
7.1.1 Device or Controller Redundancy
7.1.2 Network Interface in the Device or Controller and Computer and Network Media Redundancy
7.2 Communications Software Redundancy
7.3 Human–Machine Interface/Supervisory Control and Data Acquisition Software Redundancy
8.0 COMMUNICATIONS AND CONNECTIVITY SOFTWARE
8.1 Input/Output Drivers. 8.1.1 Proprietary Drivers
8.1.2 Visual Studio.NET Drivers
8.1.3 Openness, Productivity, and Connectivity Standards-Based Drivers
8.1.4 Legacy Drivers—ActiveX and Dynamic Data Exchange. 8.1.4.1 ActiveX Drivers
8.1.4.2 Dynamic Data Exchange Drivers
8.2 Communications Software. 8.2.1 Role of Human–Machine Interface or Supervisory Control and Data Acquisition Software
8.2.2 Internet and Web Browser Connectivity
8.3 Role of Virtual Servers. 8.3.1 What Is Virtualization?
8.3.2 Benefits of Virtualization
8.3.3 Types of Virtualization Systems
8.4 Cloud Computing
8.4.1 Private Versus Public Versus Community Versus Hybrid Cloud
8.4.2 Vendor Cloud Supervisory Control and Data Acquisition Systems
9.0 CONCLUSIONS
Chapter 12. Physical and Cyber Security. Corinne M. Tuozzoli, P.E. Victor Einfeldt. Daniel Groves, P.E. Ryan J. Kowalski, P.E. Joshua A. Ross. Shannon D. Spence, P.E
1.0 CRITICAL INFRASTRUCTURE
2.0 PHYSICAL SECURITY
2.1 General Physical Security Design
2.2 Intrusion Detection
2.3 Access Control
2.4 Closed-Circuit Television
2.5 Coordination of Controls and Security Data
3.0 CRITICAL INFORMATION NETWORKS
4.0 CYBER SECURITY RISKS FOR INDUSTRIAL CONTROL SYSTEMS
4.1 Threats
4.2 Vulnerabilities
4.3 Risk Assessment
4.4 Likelihood
4.5 Consequences
4.6 Risks
5.0 CYBER SECURITY REGULATIONS
6.0 STANDARDS AND GUIDELINES
6.1 International Society of Automation Industrial Automation and Control System Security Standards
6.2 International Standards Organization and International Electrotechnical Commission Series for Information Security Management Systems
6.3 North American Electric Reliability Corporation Critical Infrastructure Protection
6.4 National Institute of Standards and Technology Standards and Guidelines
6.5 Cyber Security Guidelines
6.6 Standards and Guidelines—The Last Word
7.0 COMPREHENSIVE CYBER SECURITY PROGRAM. 7.1 Overview
7.2 Benefits
7.3 Senior Management
7.4 Cross-Functional Team
7.5 Critical Assets
7.6 Risk Assessment
7.7 Mitigation Controls
7.8 Training and Security Awareness
7.9 Updates
8.0 CYBER SECURITY-ENHANCING MEASURES
8.1 Topology, Routing, and Protocols
8.2 Firewalls
8.3 Internet Protocol Security Virtual Private Network
8.4 Wireless and Modem Links
8.5 Object Linking and Embedding for Process Control Security
8.6 Computer Security
8.6.1 Universal Serial Bus Ports
8.6.2 Portable Client Devices
8.7 User and Device Authentication (Password Management)
8.8 Intrusion Detection and Prevention System
8.9 Personnel Security
8.10 Physical Security
8.11 Network Architecture
8.12 Network Access Limits
8.13 Context-Aware Security Controls
9.0 REFERENCES
10.0 SUGGESTED READINGS
Chapter 13. Human–Machine Interfaces. Ryan J. Kowalski, P.E. Caseyann Sarli
1.0 INTRODUCTION
1.1 Why Do We Care About Human–Machine Interfaces?
1.2 Transforming the Role of the Operator
1.3 Rethinking Entrenched Practices
2.0 UNDERSTANDING SITUATIONAL AWARENESS
2.1 Levels of Human Assessment
2.2 The Challenges of Situational Awareness
2.3 Human–Machine Interfaces and Loss of the “Big Picture”
2.4 Symptoms of Technology-Centric Human–Machine Interface System Design
2.5 Steps for Creating a High-Performance Human–Machine Interface
3.0 FIELD DISPLAY AND ANNUNICATION METHODS. 3.1 Real-Time Display and Control Devices
3.1.1 Types of Control Panels
3.1.2 Device Arrangement
3.2 Visual and Auditory Stimuli
3.2.1 Annunciators and Lightboxes
3.2.2 Status-Indicating Lights
3.2.3 Switches and Pushbuttons
3.2.4 Strobe Lights and Horns
3.2.5 Bar Graphs and Loop-Controller Displays
3.3 Control Panel Distribution and Task Analysis
3.3.1 Local Control Panels
3.3.2 Vendor-Supplied Control Panels
3.3.3 Area, Master, and Main Control Panels
3.4 Computerized Displays
3.4.1 Text Displays
3.4.2 Proprietary Graphic Displays
3.4.3 Industrial Computer Displays
3.4.4 Wireless Human–Machine Interfaces and Mobile Devices
3.5 Remote Alarming Systems
3.5.1 Audible Alarming
3.5.2 Autodialers
3.5.4 Page Party Systems
3.5.5 Text Messaging
3.5.6 E-Mail
4.0 DISPLAY CONTROL ROOMS AND HUMAN ENGINEERING
4.1 Ergonomics
4.2 Control Room Displays. 4.2.1 Console Displays
4.2.2 Video Projectors
4.2.3 Large, Flat-Panel, Multisegment Graphic Displays
4.3 Equipment Layout
4.4 Physical Security
4.5 Fire Protection
4.6 Heating, Ventilation, and Air Conditioning
4.7 Lighting and Electrical Considerations
4.8 Control Room Alarming
4.9 Consoles and Furniture
4.9.1 Console Subsystem
4.9.2 Console Surface and Appurtenances
4.9.3 Chairs
5.0 ADOPTING THE HUMAN–MACHINE INTERFACE PHILOSOPHY—DEVELOPING THE STANDARD
5.1 Designing for Predictive Versus Reactive Actions
5.2 Graphics
5.2.1 Design Methods
5.2.1.1 Piping and Instrumentation Drawing Design Method
5.2.1.2 Three-Dimensional Design Method
5.2.1.3 “Next Generation” Design Method
5.2.2 Backgrounds
5.2.3 Contrast, Repetition, Alignment, and Proximity
5.2.3.1 Contrast
5.2.3.2 Repetition
5.2.3.3 Alignment
5.2.3.4 Proximity
5.2.4 Process Flow, Pipelines, and Equipment
5.2.5 Text and Values
5.3 Color
5.3.1 Color Blindness
5.3.2 Color Consistency
5.3.3 Color Use
5.4 Layout
5.5 Navigation
5.6 Display Levels
5.6.1 Tier 1—Overview Displays
5.6.2 Tier 2—Process Displays
5.6.3 Tier 3—Process Detail Displays
5.6.4 Tier 4—Process Support and Diagnostic Displays
6.0 PERFORMANCE INDICATORS—EFFECTIVE USE OF TRENDING AND DATA
6.1 Analog Display
6.2 Trending Displays
6.2.1 Real-Time Trends
6.2.2 Historical Trends
6.2.3 Trending “Roadmaps”
6.3 Advanced Performance Displays—Profile Displays and Radar Plots
6.4 Collecting and Displaying Historical Data. 6.4.1 Update Times and Sampling Intervals
6.4.2 Deadband
6.4.3 Smoothing
6.5 Using Statistical Analysis Features
7.0 IMPLEMENTATION OF HUMAN–MACHINE INTERFACE DESIGN
7.1 Object Development. 7.1.1 Use of Object-Oriented Programming
7.1.2 Using “Wizards” and “Tag Substitution”
7.1.3 Personal Computer Controllers
7.2 Information Technology and Network Considerations for Human–Machine Interfaces. 7.2.1 Access Security Policies and Levels
7.2.2 Operating Systems
7.2.3 Client–Server Architectures
7.2.4 Browser-Based Human–Machine Interfaces
7.2.5 Wide Area Network and Local Area Network Deployment
7.2.6 Wireless and Mobile Deployments
7.2.7 Remote Access and Virtual Private Network Considerations
7.3 Programmable Logic Controller Connections and Performance
7.3.1 Programmable Logic Controller Drivers
7.3.2 Refresh Rates and Communications
7.4 Commissioning and Training
7.5 Licensing Updates and Support
7.6 Human–Machine Interface Historian and Data Management
8.0 ALARM MANAGEMENT—IMPLEMENTING BEST PRACTICES
8.1 Correlation to Process Control Performance
8.2 Trends in Alarm Management
8.2.1 Current Alarming Methods
8.2.2 Common Alarm Problems and Misuse
8.3 Coordination with Human–Machine Interface Graphics Development
8.4 The American National Standards Institute/International Society of Automation 18.2-2009 Alarm Management Standard
8.5 Steps to Develop an Effective Alarm System
8.6 Defining Alarm Priorities
8.6.1 Consequence and Time to Respond
8.6.2 High-Priority Alarms
8.6.3 Highly Managed Alarms
8.6.4 Priority Distribution
8.6.5 Priority Color
8.6.6 Priority Sound
8.7 Developing the Alarm Philosophy
8.7.1 Does the Event Require a Response?
8.7.2 Combination Alarms
8.7.3 Common Alarms
8.7.4 Fieldbus Alarms
8.7.5 System or Maintenance Alarms
8.7.6 Alarms that Trigger Automatic Action
8.7.7 Messages, Status Information, and Bad Inputs
8.8 Methodologies for Identifying and Documenting Alarms
8.8.1 Rationalizing Alarms
8.8.2 Inputs to Alarm Documentation
8.8.3 Using Results of Process Hazard Analysis or Failure Mode and Effects Analysis
8.8.4 Documentation Outputs
8.9 Human–Machine Interface Design and Implementation of the Alarm System
8.10 Alarm System Analysis and Benchmarking
8.10.1 Alarm Capacity
8.10.2 Benchmarking Data
8.11 Disabling Alarms and Change Management
8.11.1 Out-of-Service Alarms
8.11.2 Shelved Alarms
8.11.3 Alarms Suppressed by Design
8.12 Auditing and Performance Benchmarking
9.0 MANAGING CHANGE AND FUTURE CONSIDERATIONS
10.0 REFERENCES
11.0 SUGGESTED READINGS
Chapter 14. Process Controllers. Raluca F. Constantinescu, P.E
1.0 PROCESS CONTROL DESIGN
1.1 Design Criteria
1.1.1 Small and Large Projects
1.1.2 Instrumentation and Redundancy
1.1.3 Backup Systems
1.1.4 Maintenance
1.1.5 Existing Standards
1.1.6 Life Span
1.2 Control System Block Diagram. 1.2.1 “Big Picture”, “Zoom In”
1.2.2 Key Pointers
1.3 Controller Design Decisions
1.3.1 “Go with the Flow”
1.3.2 Revolution
2.0 PROCESS CONTROL HARDWARE. 2.1 Single-Loop Controller
2.1.1 Process Variable
2.1.2 Proportional–Integral–Derivative Control Action
2.1.3 Tuning
2.1.4 On–Off Control Action
2.2 Programmable Logic Controller
2.2.1 Scan Time
2.2.2 Memory Types
2.2.3 Real-Time Operating Systems
2.2.4 Programmable Automation Controller
2.2.5 Troubleshooting Hints
2.3 Remote Terminal Unit
2.4 Distributed Control System Versus Supervisory Control and Data Acquisition. 2.4.1 Control System Evolution
2.4.2 Beyond Names
2.5 Process Control Network
2.5.1 Hardwired Networks Media
2.5.1.1 Fiber Optics
2.5.1.2 Copper
2.5.2 Wireless Media and Radios
2.5.3 Ethernet Networking Hardware
2.6 Input/Output List
2.6.1 Process and Instrumentation Diagrams and Wiring
2.6.2 Modules. 2.6.2.1 Discrete Inputs
2.6.2.2 Discrete Outputs
2.6.2.3 Analog Inputs
2.6.2.4 Analog Outputs
2.6.2.5 Other Inputs and Outputs
3.0 PROCESS CONTROLLER SOFTWARE—CONTROL PROGRAMMING LANGUAGES. 3.1 Establish Standards
3.1.1 Function Blocks
3.1.2 Documentation
3.1.3 Mapping the “Real World”
3.2 Implementation
3.2.1 Control Narratives—Basis for Software Development
3.2.2 Ladder Logic
3.2.3 Structured Text
3.2.4 Sequential Function Chart
3.2.5 Function Block Organization
4.0 REFERENCES
Chapter 15. Maintenance and Troubleshooting. William J. Balzer, P.E
1.0 THEORY OF MAINTENANCE MANAGEMENT. 1.1 Types of Maintenance
1.1.1 Scheduled, Unscheduled, and Predictive Maintenance
1.1.2 Critical Versus Noncritical Maintenance
1.2 Maintenance Management Components
2.0 MAINTENANCE STRATEGY
3.0 MAINTENANCE MANAGEMENT SYSTEMS
3.1 Computerized Maintenance Management Systems
3.1.1 Planning and Scheduling
3.1.2 Work Management
3.1.3 Materials Management
3.1.4 Procurement
3.1.5 Integration with Other Systems
3.1.6 Reporting, Key Performance Indicators, and Dashboards
3.1.6.1 Custom Reports
3.1.6.2 Ad Hoc Reports
3.1.6.3 Key Performance Indicators and Dashboards
3.2 Facility Asset Management
3.3 Implementation Approach
3.4 Change Management
4.0 INSTRUMENT PERFORMANCE AND EVALUATION
4.1 Quality Control Procedures
4.2 Control Charts
4.3 Example
5.0 TROUBLESHOOTING THEORY. 5.1 The Importance of Details
5.2 Troubleshooting Considerations
5.3 Useful References
6.0 TROUBLESHOOTING STRATEGY
6.1 Define the Problem
6.2 Observe the System Closely
6.3 Isolate the Problem Area
6.4 Develop a Theory
6.5 Test the Theory
6.6 Implement Changes
6.7 Document the Problem
7.0 TROUBLESHOOTING METHODS. 7.1 Swapping Identical Parts
7.2 Removing Parallel Components
7.3 Divide the System into Parts and Test
7.4 Trap the Failure
8.0 TEST CASE
8.1 Define the Problem
8.2 Observe the System
8.3 Isolate the Problem Area
8.4 Develop a Theory
8.5 Test the Theory
8.6 Implement Changes
8.7 Document the Problem
9.0 TROUBLESHOOTING EQUIPMENT
10.0 SAFETY
11.0 REFERENCES
12.0 SUGGESTED READINGS
Chapter 16. Control Systems Training. Frank Mercado, P.E
1.0 THE COMPELLING NEED FOR TRAINING
2.0 SUSTAINABILITY OF A TRAINING PROGRAM. 2.1 Basic Requirements
2.2 Organization, Practices, and Technology
2.3 Training Budget
3.0 TRAINING PROGRAM DEVELOPMENT. 3.1 Established Training Development Methods
3.2 Viable Training Development Model for Wastewater Utilities
4.0 TRAINING PROGRAM DESIGN. 4.1 Learning Insights
4.2 From Skills Gap to Learning Objectives
4.3 Training Plan
4.4 Training Methods
4.4.1 Classroom Instruction
4.4.2 On-the-Job Training
4.4.3 Mentoring
4.4.4 Seminars and Training Courses
4.4.5 “Train the Trainer”
4.4.6 Web-Based Learning
4.5 Sources of Training Materials
4.5.1 Packaged Training Systems
4.5.2 Vendor Operation and Maintenance Manuals
4.5.3 Capital Project As-Built Drawings
4.5.4 Publications by Trade Organizations
4.5.5 Web-Based Tutorials and White Papers
4.6 Process Simulators
4.7 Tracking Training Progress
5.0 CONTROL SYSTEMS TRAINING
5.1 Operator Training
5.2 Maintenance Training
5.3 Engineering-Level Training
6.0 SUMMARY
7.0 REFERENCE
8.0 SUGGESTED READINGS
Index
Отрывок из книги
Prepared by the Automation of Water Resource Recovery Facilities Task Force of the Water Environment Federation
Robert D. Hill, Ph.D, P.E., Chair
.....
The PCN should provide simple descriptions of vendor-supplied package controls, their functions, and which parameters must be monitored or controlled remotely. Designers also should provide all related vendor information (e.g., functional descriptions, control panel drawings, wiring schematics, and equipment catalog cuts) to I&C and electrical engineers as soon as possible. In addition, designers should let I&C engineers know what instruments the packaged equipment will need that are not provided by the vendor so that these instruments can be included in I&C specifications. Finally, to ensure that the design is well coordinated, I&C and electrical engineers should be asked to review packaged-equipment specifications. Every effort should be made to match existing packaged control system (PCS) hardware whenever possible to alleviate long-term O&M requirements for facilities. The specifications should require that all licenses and copies of programs for all PCSs be provided to owners for maintenance if the owner desires.
The following standards, in particular, should be considered when specifying programming standards (see Chapters 13 and 14 for more details):
.....