Hybridized and Coupled Nanogenerators
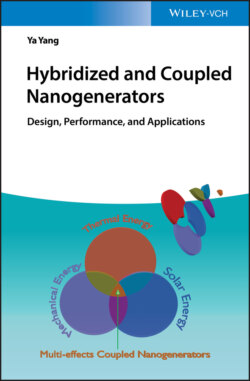
Реклама. ООО «ЛитРес», ИНН: 7719571260.
Оглавление
Ya Yang. Hybridized and Coupled Nanogenerators
Table of Contents
List of Illustrations
Guide
Pages
Hybridized and Coupled Nanogenerators. Design, Performance, and Applications
Forewords
Preface
1 Overview. 1.1 Introduction
1.2 Hybridized Nanogenerators
1.2.1 Hybrid Energy Cells
1.2.2 Electromagnetic–Triboelectric Hybridized Nanogenerators
1.2.3 Other Hybridized Nanogenerators
1.3 Coupled Nanogenerators
1.3.1 Pyroelectric and Photovoltaic Coupled Nanogenerators
1.3.2 Multi‐effects Coupled Nanogenerators
1.4 Applications
1.5 Conclusion and Prospects
References
Note
2 Wind‐Driven Triboelectric Nanogenerators. 2.1 Introduction
2.2 Conventional Wind Harvester. 2.2.1 Working Mechanisms and Devices Structure
2.2.2 Applications
2.3 Triboelectric Nanogenerators for Scavenging Wind Energy
2.3.1 Fundamental Modes and Structure
2.3.1.1 Vibrating Plate‐Based TENGs
2.3.1.2 Enhanced Plate‐Based TEGs
2.3.1.3 Elasto‐aerodynamics‐Driven TENGs
2.3.1.4 Others
2.3.2 Materials
2.3.2.1 Cellulose
2.3.2.2 Metal
2.3.2.3 Polymer
2.3.2.4 Nanoparticle and Nanowire
2.3.3 Performance
2.3.3.1 Mechanical Behavior
2.3.3.2 Electrical Output
2.3.4 Applications
2.3.4.1 Self‐Powered Printer
2.3.4.2 Wind Gauging System
2.3.4.3 Polarization of Ferroelectric Materials
2.3.4.4 Self‐Powered Wearable Electronics
2.3.4.5 Others
2.4 Comparison
2.5 Conclusion
References
Note
3 Electromagnetic–Triboelectric Hybridized Nanogenerators. 3.1 Introduction
3.2 Working Mechanisms
3.3 Hybridized Devices Structure and Working Mechanisms
3.3.1 Shared‐Electrode‐Based EMG–TENG
3.3.2 Rotating‐Disk‐Based EMG–TENG
3.3.3 Spring‐Based EMG–TENG
3.3.4 Stretchable EMG–TENG
3.3.5 Others
3.4 Materials
3.4.1 Glass Fibers/Silver Nanowires
3.4.2 Composite Materials
3.4.3 Materials with Rough Structures
3.4.4 Others
3.5 Performance
3.5.1 Conjunction Manipulation
3.5.2 Output Characteristics
3.6 Applications
3.6.1 Powering Electronic Devices
3.6.2 Self‐Powered Wearable Electronics
3.6.3 Others
3.7 Summary and Perspectives
References
Note
4 Other Hybridized Nanogenerators. 4.1 Introduction
4.1.1 Nanogenerators for Harvesting Solar Energy
4.1.2 Nanogenerators for Harvesting Electrochemical Energy
4.2 Hybridized Photoelectric and Piezoelectric Nanogenerator
4.2.1 Typical Materials and Structure Design
4.2.2 Principles
4.2.3 Applications and Performances
4.3 Hybridized Photoelectric and Triboelectric Nanogenerator
4.3.1 Materials and Fabrication
4.3.2 Principles and Performances
4.3.3 Applications
4.4 Hybridized Photoelectric and Pyroelectric Nanogenerator
4.4.1 Materials and Structure Design
4.4.2 Principles and Applications
4.4.3 Performances
4.5 Conclusions and Prospects
References
Note
5 Hybridizing Nanogenerators and Sensors. 5.1 Introduction
5.2 Materials. 5.2.1 Organic Materials
5.2.2 Inorganic Materials
5.3 Design of Self‐Powered Sensors. 5.3.1 Pressure Sensors
5.3.2 Strain Sensors
5.3.3 Temperature Sensors
5.3.4 Photodetectors
5.3.5 Magnetic Sensors
5.4 Performance. 5.4.1 Sensitivity
5.4.2 Response Speed
5.4.3 Stability
5.5 Applications. 5.5.1 Touch and Motion Detection
5.5.2 Strain Detection
5.5.3 Temperature Detection
5.5.4 Image Sensor
5.6 Conclusion and Prospects
References
Note
6 Hybridizing Nanogenerators and Energy Storage Devices. 6.1 Introduction
6.2 Working Mechanisms
6.2.1 Piezoelectric Nanogenerator‐Based Energy Storage Devices. 6.2.1.1 PENG‐Based Li‐ion Batteries
6.2.1.2 PENG‐Based Supercapacitors
6.2.2 Triboelectric Nanogenerator‐Based Energy Storage Devices
6.2.2.1 TENG‐Based Lithium‐Ion Batteries
6.2.2.2 TENG‐Based Supercapacitors
6.3 Materials
6.3.1 Typical Piezoelectric Materials
6.3.2 Typical Triboelectric Materials
6.3.3 Materials for Lithium‐Ion Batteries
6.3.4 Materials for Supercapacitors
6.4 Devices Structure and Design
6.4.1 Piezoelectric Nanogenerator‐Based Energy Storage Devices
6.4.2 Triboelectric Nanogenerator‐Based Energy Storage Devices
6.5 Performance
6.5.1 The Charging/Discharging Performance of Lithium‐ion Batteries and Supercapacitors Based on Piezoelectric Nanogenerators
6.5.2 The Charging/Discharging Performance of Triboelectric Nanogenerator‐Based Lithium‐Ion Batteries and Supercapacitors
6.6 Applications
6.6.1 Powering Electronic Devices
6.6.2 Wearable/Portable Electronics
6.6.3 Other Applications
6.7 Conclusions and Prospects
References
Note
7 Pyroelectric and Thermoelectric Nanogenerators. 7.1 Introduction
7.2 Working Mechanisms
7.2.1 Pyroelectric Nanogenerators
7.2.2 Thermoelectric Nanogenerators
7.2.3 Comparison of Pyroelectric and Thermoelectric Nanogenerators
7.3 Progress of Pyroelectric Nanogenerators
7.3.1 Typical Pyroelectric Materials
7.3.2 Structure Design
7.3.3 Performance of Pyroelectric Nanogenerators
7.3.4 Applications for Sensing and Electrochemistry
7.4 Progress of Thermoelectric Nanogenerators
7.4.1 Typical Thermoelectric Materials
7.4.2 Structure Design
7.4.3 Thermoelectric Performance
7.4.4 Applications in Various Fields
7.5 Conclusions and Prospects
References
Note
8 Photovoltaic–Pyroelectric Coupled Effect Nanogenerators. 8.1 Introduction
8.2 Basic Principle. 8.2.1 Pyroelectric Effect
8.2.2 Photovoltaic Effect
8.2.3 Photovoltaic–Pyroelectric Coupled Effect
8.2.4 Temperature Dependence of Photovoltaic–Pyroelectric Coupled Effect
8.3 Materials. 8.3.1 ZnO Nanowires
8.3.2 BTO Materials
8.3.3 BFO Materials
8.3.4 Other Materials
8.4 Device Design. 8.4.1 Vertical Structure
8.4.2 Planar Structure
8.5 Performance. 8.5.1 Output Electric Signals
8.5.2 Resistance
8.5.3 Comparison of Vertical‐ and Planar‐Structured Nanogenerators
8.5.4 Temperature Dependence
8.6 Applications
8.6.1 Common Photodetection
8.6.2 Image Photodetection
8.7 Conclusions and Prospects
References
Note
9 Multi‐effects Coupled Nanogenerators. 9.1 Introduction
9.2 Materials
9.2.1 Semiconductors
9.2.2 Inorganic Ferroelectrics
9.2.3 Polymeric Ferroelectrics
9.3 Device Design and Working Principle. 9.3.1 Electrode/Bulk Semiconductor/Electrode Structure
9.3.2 Electrode/Heterojunction/Electrode Structure
9.3.3 Electrode/Ferroelectrics/Electrode Structure
9.3.4 Other Structures
9.4 Performance. 9.4.1 Output Characteristics for Harvesting Thermal and Light Energies
9.4.2 Output Performance for Scavenging Thermal and Mechanical Energies
9.4.3 Output Characteristics for Harvesting Light and Mechanical Energies
9.4.4 Output Characteristics for Harvesting Thermal, Light, and Mechanical Energies
9.5 Applications
9.5.1 Energy‐Storage Device Charging
9.5.2 Electrics Powering
9.5.3 General Sensing
9.5.4 Multifunctional Sensing
9.5.5 Image Sensing
9.6 Conclusions and Prospects
References
Note
10 Coupled Nanogenerators for New Physical Effects. 10.1 Introduction
10.2 Pyro‐Phototronic Effect. 10.2.1 Introduction
10.2.2 Possible Semiconducting Materials
10.2.3 Applications
10.3 Ferro‐Pyro‐Phototronic Effect. 10.3.1 Introduction
10.3.2 Possible Ferroelectric Materials
10.3.3 Applications
10.4 Thermo‐Phototronic Effect. 10.4.1 Introduction
10.4.2 Possible Thermoelectric Materials
10.4.3 Applications
10.5 Conclusions and Prospects
References
Note
Index
WILEY END USER LICENSE AGREEMENT
Отрывок из книги
Ya Yang
Zhong Lin Wang, Professor
.....
The constraint mode analysis was studied via finite element method to optimize the vibration mode of the device. Figure 2.9c shows six modes under different frequencies. The working frequency of the TEG is about 155 Hz, which coincides with the simulated fourth order mode, as shown in Figure 2.9d. Bae et al. explored dynamic characteristics of flutters in the flutter‐driven TENG, where the woven flag displayed a vibrating node [37]. The fluttering amplitude was very small above the node, but the amplitude below the node increased with increasing distance. By studying different regimes of dynamic interactions, such as single‐contact, double‐contact, and chaotic modes, the fluttering performance could be optimized to increase the performance of the TENGs. Zhang et al. used a high‐speed camera to capture the dynamic process of the contact‐separation process between two strips in the lawn‐structured TENG, and studied different modes via the finite element method [41]. The strips could be bent to contact together at the origin state under wind blow. The contact process could occur again when the atmospheric pressure exceeded the elastic restoration.
The wind flutter effect could affect the performance of the TENG. Wang et al. explored the interaction between the flow and the film by simulating the structure–fluid model [34]. This model consists of a fluid part and a solid mechanic part (solved with the Navier–Stokes equations). The results show that the bending mode was the main working condition for the film at different inlet wind speeds, as illustrated in Figure 2.10a–c. Figure 2.10d,e shows pressure and wind flow velocity distributions at a wind speed of 15 m/s. It was found that the vibrating film could work stably when the wind speed exceeded 10 m/s. On the other hand, the vibrating film worked on twist motion at low inlet wind speed (5 m/s), where the edge area of the thin film deformed more than the trailing edge. The twist motion would fade and fluttering mode form when wind speed approaches the critical wind velocity, which could be estimated by the frequency ratio of first order bending and twist mode and the respective damping ratio. Figure 2.10f shows the natural frequencies and the mode shapes of the mode shapes of first six order vibration mode, which coincides with the actual vibrations of the film observed via a high‐speed camera.
.....