Deepwater Flexible Risers and Pipelines
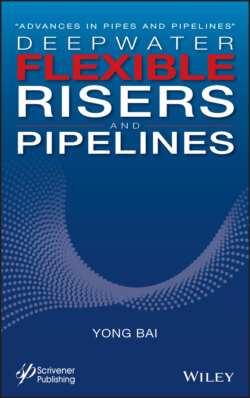
Реклама. ООО «ЛитРес», ИНН: 7719571260.
Оглавление
Yong Bai. Deepwater Flexible Risers and Pipelines
Table of Contents
List of Illustrations
List of Tables
Guide
Pages
Deepwater Flexible Risers and Pipelines
Preface
Acknowledgment
About the Author
1. Introduction. 1.1 Flexible Pipelines Overview
1.2 Environmental Conditions
1.3 Flexible Pipeline Geometry
1.4 Base Case-Failure Modes and Design Criteria
1.5 Reinforcements
1.6 Project and Objectives
References
2. Structural Design of Flexible Pipes in Different Water Depth. 2.1 Introduction
2.2 Theoretical Models
2.3 Comparison and Discussion
2.4 Conclusions
References
3. Structural Design of High Pressure Flexible Pipes of Different Internal Diameter. 3.1 Introduction References
3.2 Analytical Models
3.2.1 Cylindrical Layers
3.2.2 Helix Layers
3.2.3 The Stiffness Matrix of Pipe as a Whole Helix Layers
3.2.4 Blasting Failure Criterion
3.3 FEA Modeling Description
3.4 Result and Discussion
3.5 Design
3.6 Conclusions
References
4. Tensile Behavior of Flexible Pipes. 4.1 Introduction
4.2 Theoretical Models. 4.2.1 Mechanical Model of Pressure Armor Layer
4.2.2 Mechanical Behavior of Tensile Armor Layer
4.2.3 Overall Mechanical Behavior
4.3 Numerical Model
4.3.1 Pressure Armor Stiffness
4.3.2 Full Pipe
4.4 Comparison and Discussion
4.5 Parametric Study
4.6 Conclusions
References
5. Design Case Study for Deep Water Risers. 5.1 Abstract
5.2 Introduction
5.3 Cross-Sectional Design
5.4 Case Study
5.5 Design Result
5.6 Finite Elements Analysis
5.7 Conclusion
References
6. Unbonded Flexible Pipe Under Bending. 6.1 Introduction
6.2 Helical Layer Within No-Slip Range
6.2.1 Geometry of Helical Layer
6.2.2 Bending Stiffness of Helical Layer
6.3 Helical Layer Within Slip Range
6.3.1 Critical Curvature
6.3.2 Axial Force in Helical Wire Within Slip Range
6.3.3 Axial Force in Helical Wire Within No-Slip Range
6.3.4 Bending Stiffness of Helical Layer
References
7. Coiling of Flexible Pipes. 7.1 Introduction
7.2 Local Analysis. 7.2.1 Dimensions and Material Characteristics
7.2.2 Tension Test
7.2.3 Bending Test
7.2.4 Summary
7.3 Global Analysis. 7.3.1 Modeling
7.3.2 Interaction and Mesh
7.3.4 Discussion of the Results
7.4 Parametric Study
7.4.1 Diameter of the Coiling Drum
7.4.2 Sinking Distance of the Coiling Drum
7.4.3 Reeling Length
7.4.4 The Location of the Bearing Plate
7.5 Conclusions
References
8. Flexible Risers and Flowlines. 8.1 Introduction
8.2 Flexible Pipe Cross-Section
8.2.1 Carcass
8.2.2 Internal Polymer Sheath
8.2.3 Pressure Armor
8.2.4 Tensile Armor
8.2.5 External Polymer Sheath
8.2.6 Other Layers and Configurations
8.3 End Fitting and Annulus Venting Design. 8.3.1 End Fitting Design and Top Stiffener (or Bellmouth)
8.3.2 Annulus Venting System
8.4 Flexible Riser Design. 8.4.1 Design Analysis
8.4.2 Riser System Interface Design
8.4.3 Current Design Limitations
References
9. Lazy-Wave Static Analysis. 9.1 Introduction
9.2 Fundamental Assumptions
9.3 Configuration Calculation
9.3.1 Cable Segment. 9.3.1.1 Hang-Off Section
9.3.1.2 Buoyancy Section
9.3.1.3 Decline Section
9.3.2 Boundary-Layer Segment
9.3.3 Touchdown Segment
9.3.4 Boundary Conditions
9.4 Numerical Solution
9.5 Finite Element Model
9.5.1 Environment
9.5.2 Riser
9.5.3 Boundary Conditions
9.6 Comparison and Discussion
9.7 Parameter Analysis. 9.7.1 Effect of Seabed Stiffness
9.7.2 Effect of Hang-Off Inclination Angle
9.7.3 Effect of Buoyancy Section Length
9.8 Conclusions
References
10. Steep-Wave Static Configuration. 10.1 Introduction
10.2 Configuration Calculation
10.2.1 Touch-Down Segment
10.2.2 Buoyancy Segment
10.2.3 Hang-Off Segment
10.2.4 Boundary Conditions
10.3 Numerical Solution
10.4 Comparison and Discussion
10.5 Parametric Analysis. 10.5.1 Effect of Buoyancy Segment’s Equivalent Outer Diameter
10.5.2 Effect of Buoyancy Segment Length
10.5.3 Effect of Buoyancy Segment Location
10.5.4 Effect of Current Velocity
10.6 Conclusions
References
11. 3D Rod Theory for Static and Dynamic Analysis. 11.1 Introduction
11.2 Nomenclature
11.3 Mathematical Model. 11.3.1 Governing Equations
11.3.2 Bending Hysteretic Behavior
11.3.3 Bend Stiffener Constraint
11.3.4 Pipe-Soil Interaction
11.4 Case Study
11.5 Results and Discussion
11.5.1 Static Analysis
11.5.2 Dynamic Analysis
11.5.2.1 Top-End Region
11.5.2.2 Touchdown Zone
11.5.3 Effect of Bend Stiffener Constraint
11.5.4 Effect of Bending Hysteretic Behavior
11.5.5 Effect of Top Angle Constraint
11.6 Conclusions
References
12. Dynamic Analysis of the Cable-Body of the Deep Underwater Towed System. 12.1 Introduction
12.2 Establishment of Towed System Dynamic Model
12.3 Numerical Simulation and Analysis of Calculation Results
12.3.1 The Effect of Different Turning Radius
12.3.2 The Effect of Different Turning Speeds
12.3.3 Dynamic Analysis of the Towed System with the Change of the Parameters of the Cable
12.3.4 The Effect of the Diameters of the Towed Cable
12.3.5 The Effect of the Drag Coefficients of the Towed Cable
12.3.6 The Effect of the Added Mass Coefficient of the Towed Cable
12.4 Conclusions
Acknowledgments
References
13. Dynamic Analysis of Umbilical Cable Under Interference. 13.1 Introduction
13.2 Dynamic Model of Umbilical Cable
13.2.1 Establishment of Mathematical Model
13.2.2 The Discrete Numerical Method for Solving the Lumped Mass Method
13.2.3 Calculation of the Clashing Force of Umbilical Cable
13.3 The Establishment of Dynamic Simulation Model in OrcaFlex. 13.3.1 The Equivalent Calculation of the Stiffness of the Umbilical Cable
13.3.2 RAO of the Platform
13.3.3 The Choice of Wave Theory
13.3.4 Establishment of Model in OrcaFlex
13.4 The Calculation Results. 13.4.1 The Clashing Force of Interference
13.4.2 The Variation of the Effective Tension Under Interference
13.4.3 The Variation of Bending Under Interference
13.5 Conclusion
References
14. Fatigue Analysis of Flexible Riser. 14.1 Introduction
14.2 Fatigue Failure Mode of Flexible Riser
14.3 Global Model of Flexible Risers. 14.3.1 Pipe Element
14.3.2 Bending Stiffener
14.3.3 Sea Condition
14.3.4 Platform Motion Response
14.3.5 Time Domain Simulation Analysis
14.4 Failure Mode and Design Criteria
14.4.1 Axisymmetric Load Model
14.4.2 Bending Load Model
14.5 Calculation Method of Fatigue Life of Flexible Riser
14.5.1 Rainflow Counting Method
14.5.2 S-N Curve
14.5.3 Miner’s Linear Cumulative Damage Theory
14.5.4 Modification of Average Stress on Fatigue Damage
14.6 Example of Fatigue Life Analysis of Flexible Riser
References
15. Steel Tube Umbilical and Control Systems. 15.1 Introduction. 15.1.1 General
15.1.2 Feasibility Study
15.1.3 Detailed Design and Installation
15.1.4 Qualification Tests
15.2 Control Systems. 15.2.1 General
15.2.2 Control Systems
15.2.3 Elements of Control System
15.2.4 Umbilical Technological Challenges and Solutions
15.3 Cross-Sectional Design of the Umbilical
15.4 Steel Tube Design Capacity Verification
15.4.1 Pressure Containment
15.4.2 Allowable Bending Radius
15.5 Extreme Wave Analysis
15.6 Manufacturing Fatigue Analysis
15.6.1 Accumulated Plastic Strain
15.6.2 Low Cycle Fatigue
15.7 In-Place Fatigue Analysis
15.7.1 Selection of Sea State Data From Wave Scatter Diagram
15.7.2 Analysis of Finite Element Static Model
15.8 Installation Analysis
15.9 Required On-Seabed Length for Stability
References
16. Stress and Fatigue of Umbilicals. 16.1 Introduction
16.2 STU Fatigue Models
16.2.1 Simplified Model
16.2.1.1 Axial and Bending Stresses
16.2.1.2 Friction Stress
16.2.1.3 Simplified Approach: Combining Stresses
16.2.1.4 Simplified (Combining Stresses) Fatigue Damage
16.2.1.5 Simplified Model Assumptions
16.2.2 Enhanced Non-Linear Time Domain Fatigue Model
16.2.2.1 Friction Stresses
16.2.2.2 Effect of Multiple Tube Layers
16.2.2.3 Combined Friction Stresses
16.2.2.4 Axial and Bending Stresses
16.2.2.5 Combining Stresses
16.2.2.6 Fatigue Life
16.2.2.7 Benefits of Enhanced Non-Linear Time Domain Fatigue Model
16.3 Worked Example
16.3.1 Time Domain vs. Simplified Approaches
16.3.2 Effect of Friction on STU Fatigue
16.3.2.1 Influence of High Tube Friction on Umbilical Fatigue
16.3.2.2 Influence of Low Tube Friction on Umbilical Fatigue
16.3.2.3 Influence of Metal-to-Metal Friction vs. Metal-to-Plastic Contact on Umbilical Fatigue
16.3.3 Effect of Increasing Water Depth
16.3.4 Effect of Increasing the Tube Layer Radius
16.4 Conclusions
16.5 Recommendations
References
17. Cross-Sectional Stiffness for Umbilicals. 17.1 Introduction
17.2 Theoretical Model of Umbilicals
17.3 Bending Stiffness of Umbilicals
17.4 Tensile Stiffness of Umbilicals
17.5 Torsional Stiffness of Umbilicals
17.6 Ultimate Capacity of Umbilicals. 17.6.1 Minimum Bending Curvature
17.6.2 Minimum Tensile Load
17.6.3 Tensile Capacity Curve
References
18. Umbilical Cross-Section Design. 18.1 Introduction. 18.1.1 General
18.1.2 Sectional Composition of the Umbilical Cable
18.1.3 Umbilical Cable Structure Features
18.2 Umbilicals Cross-Section Design Overview. 18.2.1 Umbilical Cross-Section Design Flowchart
18.2.2 Load Analysis
18.3 Umbilical Cable Cross-Section Design
18.3.1 Umbilical Cable Cross-Section Layout Design
18.3.2 Tensile Performance Design
18.3.3 Bending Performance Design
References
19. Collapse Strength of Fiber Glass Reinforced Riser. 19.1 Introduction
19.2 External Pressure Test
19.2.1 Testing Specimen
19.2.2 Testing System
19.2.3 Testing Results
19.3 Theoretical Analysis. 19.3.1 Fundamental Assumptions
19.3.2 Constitutive Model of Materials
19.3.3 Establish the Equations of Motion
19.3.4 Establish Virtual Work Equations
19.4 Numerical Analysis
19.5 Finite Element Analysis
19.5.1 Establish the Finite Element Model
19.5.2 The Results of the Finite Element Analysis
19.6 Conclusion
References
20. Burst Strength of Fiber Glass Reinforced Riser. 20.1 Introduction
20.2 Experiment. 20.2.1 Dimensions and Material Properties of FGRFP
20.2.2 Experiment Device
20.2.3 Experiment Results
20.3 Numerical Simulations. 20.3.1 Mesh and Interaction
20.3.2 Load and Boundary Conditions
20.3.3 Numerical Results
20.4 Analytical Solution. 20.4.1 Basic Assumptions
20.4.2 Stress Analysis
20.4.3 Boundary Condition
20.5 Results and Discussion
20.6 Parametric Analysis
20.6.1 Winding Angle of Fiber Glass
20.6.2 Diameter-Thickness Ratio
20.7 Conclusions
References
21. Structural Analysis of Fiberglass Reinforced Bonded Flexible Pipe Subjected to Tension. 21.1 Introduction
21.2 Experiment. 21.2.1 Basic Assumptions
21.2.2 Material Characteristics
21.2.3 Experimental Results
21.3 Theoretical Solution
21.3.1 Basic Assumptions
21.3.2 Cross-Section Simplification
21.3.3 Fiber Deformation
21.3.4 Cross-Section Deformation
21.3.5 Equilibrium Equations
21.4 Finite Element Model
21.5 Comparison and Discussion
21.5.1 Tension-Extension Relation
21.5.2 Cross-Section Deformation
21.5.3 Fiberglass Stress
21.5.4 Contribution of Each Material
21.5.5 Summary
21.6 Parametric Study
21.6.1 Winding Angle
21.6.2 Fiberglass Amount
21.6.3 Diameter-Thickness Ratio
21.7 Conclusions
Acknowledgement
References
22. Fiberglass Reinforced Flexible Pipes Under Bending. 22.1 Introduction
22.2 Experiment
22.2.1 Experimental Facility
22.2.2 Specimen
22.2.3 Experiment Process
22.2.4 Experimental Results
22.3 Analytical Solution. 22.3.1 Fundamental Assumption
22.3.2 Kinematic Equation
22.3.3 Material Simplification
22.3.4 Constitutive Model
22.3.5 Principle of Virtual Work
22.3.6 Algorithm of Analytical Solutions
22.4 Finite Element Method
22.5 Result and Conclusion
22.6 Parametric Analysis
22.6.1 D/t Ratio
22.6.2 Initial Ovality
22.7 Conclusions
References
23. Fiberglass Reinforced Flexible Pipes Under Torsion. 23.1 Introduction
23.2 Experiments
23.3 Experimental Results
23.4 Analytical Solution. 23.4.1 Coordinate Systems
23.4.2 Elastic Constants of Reinforced Layers (k = 2, 3 … (n − 1))
23.4.3 Reinforced Layers Stiffness Matrix k = 2, 3… (n − 1)
23.4.4 Inner Layer and Outer Layer Stiffness Matrix (k = 1, n)
23.4.5 Stress and Deformation Analysis
23.4.6 Boundary Conditions
23.4.7 Interface Conditions
23.4.8 Geometric Nonlinearity
23.5 Numerical Simulations
23.6 Results and Discussions
23.7 Parametric Analysis. 23.7.1 Effect of Winding Angle
23.7.2 Effect of Thickness of Reinforced Layers
23.8 Conclusions
Acknowledgments
References
24. Cross-Section Design of Fiberglass Reinforced Riser. 24.1 Introduction
24.2 Nomenclature
24.3 Basic Structure of Pipe. 24.3.1 Overall Structure
24.3.2 Material
24.4 Strength Failure Design Criteria. 24.4.1 Burst Pressure
24.4.2 Burst Pressure Under Internal Pressure Bending Moment
24.4.3 Yield Tension
24.5 Failure Criteria for Instability Design. 24.5.1 Minimum Bending Radius
24.5.2 External Pressure Instability Pressure
24.6 Design Criteria for Leakage Failure
References
25. Fatigue Life Assessment of Fiberglass Reinforced Flexible Pipes. 25.1 Introduction
25.2 Global Analysis
25.3 Rain Flow Method
25.4 Local Analysis
25.5 Modeling
25.6 Result Discussion
25.7 Sensitivity Analysis
25.8 Fatigue Life Assessment
25.9 Conclusion
References
26. Typical Connector Design for Risers. 26.1 Introduction
26.2 Carcass
26.3 Typical Connector
26.4 Seal System
26.5 Termination of the Carcass
26.6 Smooth Bore Pipe
26.7 Rough Bore Pipe
26.8 Discussion
26.9 Conclusions
References
27. Bend Stiffener and Restrictor Design. 27.1 Introduction
27.2 Response Model
27.3 Extreme Load Description
27.4 General Optimization Scheme
27.5 Application Example
27.6 Non-Dimensional Bend Stiffener Design
27.7 Alternative Non-Dimensional Parameters
27.8 Conclusions
References
Appendix A: Non-dimensional bend stiffener design curves
28. End Termination Design for Umbilicals. 28.1 Introduction
28.2 Umbilical Termination Assembly. 28.2.1 General
28.2.2 UTA Design
28.2.3 UTA Structural Design Basis
28.3 Subsea Termination Interface
References
29. Mechanical Properties of Glass Fibre Reinforced Pipeline During the Laying Process. 29.1 Introduction
29.2 Theoretical Analysis. 29.2.1 Wave Load
29.2.2 Motion Response of the Vessel
29.2.3 Dynamic Numerical Solution
29.3 Static Analysis
29.4 Dynamic Characteristic Analysis
29.4.1 Influence of the Wave Direction
29.4.2 Influencing of Different Lay Angle
29.4.3 Influencing Submerged Weight
29.5 Conclusions
References
Index
Also of Interest
WILEY END USER LICENSE AGREEMENT