Practical Power Plant Engineering
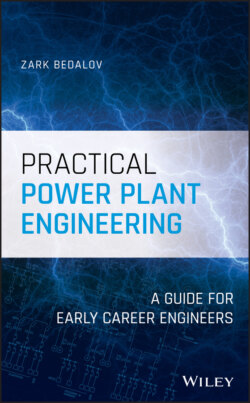
Реклама. ООО «ЛитРес», ИНН: 7719571260.
Оглавление
Zark Bedalov. Practical Power Plant Engineering
Table of Contents
List of Tables
List of Illustrations
Guide
Pages
Practical Power Plant Engineering. A Guide for Early Career Engineers
Preface – Why This Book?
Acknowledgments
About the Author
1 Plant from Design to Commissioning. CHAPTER MENU
1.1 Planning
1.1.1 Plant Design Procedure
1.1.2 Codes and Standards
1.2 Project Development. 1.2.1 Type of Project
1.2.2 Conceptual Design for Feasibility Study
1.2.3 Detailed Design
1.2.3.1 Cost of Change
1.2.4 Engineering Documents
1.2.5 Equipment Specifications and Data Sheets
1.2.6 Equipment Numbering
1.2.7 Load List
1.2.8 Generated Cable List
1.2.9 Schematic/Wiring Diagrams
1.3 Precommissioning and Commissioning
1.3.1 Precommissioning
1.3.2 Commissioning
1.3.3 Reliability Run
1.3.4 Power Plant Grid Tests
1.3.5 Commissioning Reports
1.4 Project Economics. 1.4.1 Budget Estimate
1.4.2 Levelized Cost of Energy (LCOE)
1.4.3 Marginal Cost of Energy
1.4.4 Profitability of an Industrial Plant
Reference
Note
2 Plant Key One‐Line Diagram. CHAPTER MENU
2.1 One‐Line Diagrams
2.1.1 What Is the One‐Line Diagram, or Single‐Line Diagram?
2.2 The Electrical Project
2.3 Site Conditions. 2.3.1 Source of Power
2.3.2 Ambient Derating Factors
2.3.3 Reliability Criteria
2.4 Connection to Power Utility
2.4.1 Source Impedance
2.4.2 Line Conductor
2.4.3 HV Circuit Breaker Fault Interrupting
2.4.4 Double or Single Incomer Connection
2.4.5 Utility Generating Capacity
2.4.6 Firm Capacity
2.4.7 Line Protection
2.4.8 Lightning
2.5 Main Plant Substation
2.6 Load Site Placement
2.6.1 Crushing
2.6.2 Grinding and Conveying
2.7 The Key One‐Line Diagram. 2.7.1 Load Investigation
2.7.2 Connected Load – Operating Load
2.7.3 Voltage Level Selection
2.7.4 Switchgear Breaker Ratings
2.7.5 Single Incomer Substation for a Small Plant
2.7.6 13.8 or 33 kV Switchgear for a Larger Plant
2.7.7 Transformer Connections: Cable, Cable Bus, or Bus Duct?
2.7.8 Medium Voltage Switchgear and Controllers (4.16 kV)
2.7.9 Low Voltage Service Voltage
2.7.10 Bus Tie Breaker Switching. 2.7.10.1 Incoming Transformer Failure
2.7.10.2 Switching from Control Room
2.7.11 Plant Transformation
2.7.12 Voltage Regulation. 2.7.12.1 Voltage Regulation ΔV
2.7.12.2 Motor Start Voltage Drop
2.7.12.3 Conclusion
2.7.13 Overhead Distribution Lines
2.8 Transformer System Grounding
2.8.1 Transmission Level
2.8.2 MV Systems
2.8.3 LV Systems
2.8.4 Generator Neutrals
2.9 Transformer Winding Configurations and Phasing
2.10 Standby Power
2.11 Insulation Coordination
2.11.1 Substation Shielding
2.12 Plant Control System
2.13 Fire Protection
Reference
Note
3 Switching Equipment. CHAPTER MENU
3.1 MV Switchgear
3.1.1 Breaker Ratings
3.1.2 Switchgear “Constant MVA” or “Constant kA” Interrupting
3.1.3 Breaker Status Contacts
3.1.4 Switchgear Arc Flash Design
3.2 Circuit Breakers
3.3 MV MCC Motor Controllers. 3.3.1 4.16 kV MCC Assembly
3.3.2 Motor Controllers
3.3.3 Key Interlocks
3.4 LV Unit Substations. 3.4.1 LV Distribution
3.4.2 Unit Substation, Equipment Features
3.4.3 LV Switchgear
3.5 Motor Control Centers (MCCs) 3.5.1 Assembly
3.5.2 Motor Starters
3.5.3 Branch Circuit Breakers for Feeders
3.5.4 Branch Circuit Breakers for Motors
3.5.5 MCC Interrupting Capacity
3.5.6 MCC Breaker Characteristics
3.5.7 Motor Starter Selection
3.5.8 Breaker and Contactor Operation
3.5.9 Arc Flash Modern MCC Design
References
4 Designing Plant Layout. CHAPTER MENU
4.1 Plant Power Distribution Routes
4.2 Underground Installations. 4.2.1 Concrete Duct Banks
4.2.2 Soil Thermal Resistivity
4.3 Plant Electrical Rooms
4.4 Plant Design. 4.4.1 Room Numbering
4.4.2 Cable Floor Openings
4.4.3 Process Plant Enclosures
4.4.4 NFPA Concerns for the Electrical Rooms
4.5 Transformer Vault Design. 4.5.1 NFPA Fire Guidelines
4.5.2 Oil Containment
4.6 Plant Control Rooms
References
5 System Grounding. CHAPTER MENU
5.1 Methods of Grounding
5.1.1 Ungrounded Systems
5.1.2 Neutral Point Solid Grounding
5.1.3 Neutral Point Resistance Grounding
5.1.4 Reactance and Resonance Neutral Grounding Systems
5.1.5 Summary
5.2 Specific Applications
5.2.1 Generator Grounding
5.2.1.1 Generator Unit System Grounding
5.2.2 Transformer Grounding. 5.2.2.1 ϒ/Δ or Δ/Y Transformers
5.2.2.2 Y/Y Transformers
5.2.2.3 Y/Y Transformers with Delta Tertiaries
5.2.2.4 Autotransformers
5.2.3 Grounding Transformers. 5.2.3.1 Zg or ϒ/Δ
References
6 Site and Equipment Grounding. CHAPTER MENU
6.1 Requirements
6.1.1 Grounding Grid Design
6.1.2 Soil Conditions
6.1.3 Test Measurements. 6.1.3.1 Soil Resistivity Measurements
6.1.3.2 Grounding Grid Test Measurements
6.2 Ground Potential Rise and Step and Touch Potential. 6.2.1 Ground Potential Rise (GPR)
6.2.2 Step Potential
6.2.3 Touch Potential
6.2.4 Reducing Step and Touch Potential Hazards
6.2.5 Human Tolerance
6.3 Computer Study Report. 6.3.1 The Study
6.4 Below Ground Equipment Grounding
6.4.1 Connections to Rebar
6.4.2 Foundation Grounding (Ufer)
6.5 Above Ground Equipment Grounding
6.6 Telecommunications in HV Substations
6.7 Fence Grounding
6.8 Plant Control System Grounding
6.9 Overhead Line Grounding
6.10 Remote Site Grounding
6.11 Effect of Overhead Ground Wires and Neutral Conductors
References
7 Plant Lighting. CHAPTER MENU
7.1 The Big Picture
7.2 Lighting Design Criteria
7.2.1 Lighting Application
7.3 Definitions
7.4 Illumination Level
7.4.1 Candlepower Distribution Curves
7.5 Outdoor Building and Road Lighting
7.6 Lighting Hardware. 7.6.1 Transformers for Lighting
7.6.2 Cables and Wiring
7.6.3 Lighting Fixtures
7.6.3.1 Lighting panels
7.6.3.2 Outlets (Receptacles)
7.6.3.3 Welding Receptacles
7.7 Lamps Inside the Fixtures. 7.7.1 Color Rendering Index (CRI)
7.7.2 Fluorescent
7.7.3 Metal Halide (MH)
7.7.4 Low‐Pressure Sodium (LPS)
7.7.5 High‐Pressure Sodium (HPS)
7.7.6 LEDs
References
8 DC System, UPS. CHAPTER MENU
8.1 Project Requirements
8.2 DC Battery and Chargers
8.2.1 Battery Ampere‐hour (Ah) Capacity
8.2.2 Battery Float/Boost Charge
8.2.3 Battery Types
8.2.4 Lead–Acid Battery Room Requirements
8.3 Battery Chargers
8.4 Ratings
8.5 Uninterruptible Power Supply (UPS)
References
9 Plant Power Distribution. CHAPTER MENU
9.1 Plant Overhead Distribution. 9.1.1 Introduction
9.1.1.1 Standards for Design of Distribution Lines in USA
9.1.2 Line Construction Elements
9.2 Types of Distribution
9.2.1 Line Design
9.3 Structure (Pole) Types
9.4 Overhead vs. Underground
9.5 Clearances. 9.5.1 Line to Roads
9.5.2 Phase Clearances
9.6 Line Voltage Drop Calculations
9.7 Power Loss Calculations
9.8 Line Conductor Sag and Tension
9.9 Aerial Bundled Cable (ABC) Distribution
9.10 Line and Cable Charging Current
References
10 Insulation Coordination, Lightning Protection. CHAPTER MENU
10.1 Economic Design
10.2 Overvoltages
10.3 Lightning Wave Phenomena and Propagation
10.4 Equipment Testing. 10.4.1 Switching Surge
10.4.2 Lightning Impulse Test
10.4.3 Chopped Wave Insulation Level
10.5 Shielding. 10.5.1 Transmission Lines
10.5.2 Substations (Switchyards)
10.6 Equipment Withstand Capability
10.6.1 Standard BIL Levels
10.6.2 Insulation Coordination
10.6.3 Arrester Charts
10.6.4 Arrester Energy Capability
10.7 Arrester Selection
10.7.1 Arrester Classification
10.7.2 Method of System Grounding
10.7.3 MCOV(IEEE) = Uc or Uk(IEC)
10.7.4 Arrester Selection Steps
Examples
10.8 Motor Surge Protection
10.9 Building Lightning Protection. 10.9.1 Material Classifications
10.9.2 Lightning Protection for Special Structures
References
11 Voltage and Phasing Standards. CHAPTER MENU
11.1 Supply and Utilization Voltages
11.2 System Phase Sequence
11.2.1 Motors
11.2.2 Generation
11.2.3 Phase Sequence Convention CCW and CW
11.2.4 Phase Sequence Blunders
11.2.5 Conclusions
11.3 World Plugs/Sockets
References
12 Cables and Supporting Equipment. CHAPTER MENU
12.1 Cables
12.1.1 Cable Shielding
12.1.2 Conductor Insulation
12.1.3 Armoring and Jackets
12.1.4 Current Ratings
12.1.4.1 Designations
12.1.4.2 Sizing of Power Cables
12.1.4.3 Voltage Drops
12.1.4.4 Derating Factors
12.1.4.5 Short Circuit Rating
12.1.5 Single or Three Core Power Cables
12.1.5.1 Cable Shield/Armor Grounding
12.2 Power Cables
12.2.1 Power Cable Selection
12.2.2 Sample MV Cable Specification
12.2.3 LV Power Cables
12.2.4 EHV Cables
12.2.4.1 HV Cable (300 kV) Terminations
12.2.4.2 HV Cable Data (300 kV)
12.2.5 Power Cable Terminations
12.2.5.1 Phisterer Connectors (CONNEX™)
12.2.6 Cable Jacket and Wire Color Coding
12.3 Control and Instrumentation Cables
12.3.1 Typical Characteristics
12.4 Specialty Cables
12.4.1 Ethernet Cables
12.4.2 DeviceNet Cables
12.4.3 Fiber Optic Cables
12.4.4 Thermocouples
12.4.5 FieldBus Cables
12.5 Cable Trays. 12.5.1 Tray Materials, Support Span, and Loading
12.5.2 Cable Fill and Classification
12.5.2.1 Cable Tray Fill
12.5.3 Cable Minimum Bending Radius
12.6 Conduits and Accessories
12.7 Bus Duct or Cable Bus Systems. 12.7.1 Bus Duct
12.7.2 Cable Bus
12.7.3 Typical Cable Bus Data Sheet
References
Note
13 Power Factor Correction. CHAPTER MENU
13.1 Power Factor and Penalties for Low pf
13.2 Leading and Lagging Power Factor
13.3 pf Correction. 13.3.1 Calculations
Example
13.3.2 Capacitor Applications and Switching
13.3.3 Synchronous Motors, Condensers, and Generators
13.4 Power Factor at Diesel Engine Generating Plant
13.5 Voltage Improvement by Adding Capacitors
13.5.1 Other Relations
13.6 Harmonic Issues with the Capacitors. 13.6.1 Nonlinear Loads
13.6.2 How Does pf Correction Affect Harmonics?
13.6.3 Capacitor Fusing and Grounding
13.7 Other Applications. 13.7.1 Surge Packs
13.7.2 Series Capacitors
13.7.3 Reactors
References
14 Motor Selection. CHAPTER MENU
14.1 Motor Selection
14.2 Motor Characteristics
14.3 NEMA Torque Classification (Design Code)
14.4 NEMA, IEC Frame Sizes
14.5 NEMA Starter Sizes
14.6 Motor Enclosures
14.7 Large Motor Starting. 14.7.1 Induction Motors, Short Circuit Requirements. 14.7.1.1 Case 1
14.7.1.2 Case 2
14.8 Synchronous Motors
14.9 Motor Service Factor
14.10 Motor Starting Criteria
14.11 Premium Efficiency Motors. 14.11.1 NEMA Premium™ Motors, the New Standard
14.11.2 Motor Efficiencies by IEC
14.11.3 Replacing a Serviceable Standard Efficiency Motor
14.11.4 Premium Motor Inrush Current and Starting Issues
References
15 Variable Frequency Drives (VFDs) and Harmonics. CHAPTER MENU
15.1 Why Are Variable Frequency Drives (VFDs) Needed? 15.1.1 Introduction
15.1.2 Principles of Operation
15.1.3 Power and Torque
15.2 Vector VFDs for Low‐Speed Operation
15.3 VFDs: Variable or Constant Torque?
15.4 Regenerative VFDs
15.5 Motor and Cable Harmonics Issues
15.6 How to Mitigate the Harmonics? 15.6.1 What are Harmonics?
15.6.2 Mitigation of Harmonics
15.7 Harmonic Order Limits
References
Note
16 Relay Protection and Coordination. CHAPTER MENU
16.1 The Objective
16.1.1 Relay Operation
16.2 IEEE Equipment and Device Designation
16.3 CTs and PTs. 16.3.1 Introduction
16.3.2 Polarity
16.3.3 Metering Accuracy Class
16.3.3.1 Metering Accuracy
16.3.3.2 Burden
16.3.3.3 0.15 Accuracy Instrument Transformers
16.3.4 CT Relaying Accuracy Class
16.3.4.1 Continuous Thermal Rating Factor (RF)
16.3.4.2 Multiratio CTs
16.3.4.3 Connections
16.3.4.4 Conclusion
16.4 Relay Protection. 16.4.1 Multifunction Relays (MFR)
16.4.2 Terminology
16.5 Major Equipment Protection
16.5.1 Transformer and Generators
16.5.2 Motors
16.5.3 Transformers Current Reflections
16.5.4 Synchronizing and Synchrocheck Relays: What is the Difference?
16.6 Relay Coordination
16.7 Protection Function Elements. 16.7.1 Overcurrent (50/51, 50/51N)
16.7.2 Overcurrent Instantaneous (50, 50N)
16.8 Time Grading
16.9 Time–Current Grading
16.10 Reclosing
16.10.1 Breaker Duty Cycle and Interrupting Capability
16.11 Load Shedding and Automatic Quick Start of Generators
16.12 (86) Lockout and (94) Self‐Reset Trip Relays
16.12.1 Lockout Trip Relays
16.12.2 Self‐Reset Trip Relays
16.12.3 Trip Supervision Relay
References
17 Plant Automation and Data Networking. CHAPTER MENU
17.1 Plant Control
17.1.1 Relay Logic
17.1.2 Programmable Logic Control (PLC)
17.1.2.1 PLC Scan
17.1.3 Distributed Control System (DCS)
17.1.4 Interposing Relays
17.1.5 Input/output (I/O) Cards
17.1.6 Digital I/O
17.1.7 Analog I/O Channels
17.1.7.1 Scaling
17.2 Motor Controls Integration
17.3 Human Machine Interface (HMI)
17.3.1 Screen Elements
17.3.2 Colors
17.3.3 Critical Alarms
17.4 PLC or DCS: What Is the Difference?
17.5 Data Networking
17.6 Means of Communication. 17.6.1 Transfer Data
17.6.2 Physical Media
17.6.3 Logical Schemes and Arbitration
17.6.4 Open Industry Standards
17.6.5 Open Protocols
17.7 Web‐based HMI
17.7.1 Work Place
17.7.2 Creating Interface Screens
17.8 SCADA Applications and Communication Protocols in Power Industry
References
18 Generation. CHAPTER MENU
18.1 Types of Generating Plants
18.1.1 Power Plant One‐Line Diagrams
18.1.2 Generator Capacity Curve and Limits
18.1.2.1 Thermal Limits
18.1.2.2 Mechanical and Electromagnetic Limits
18.1.3 Generator Excitation and V Curves
18.1.4 Short Circuit Ratio (SCR)
18.1.5 Generator Impedances
18.1.6 Generator Transient Conditions
18.1.7 Generator Stator Core Test
18.1.8 Generator, Motor Testing after Installation
18.2 Governors
18.2.1 Digital Governors
18.2.2 Auxiliary Equipment
18.3 Excitation: Control for Voltage and Reactive Power. 18.3.1 Generator (Motor) Magnetizing
18.3.2 Static or Brushless Excitation
18.4 Generator Circuit Breaker
18.5 Generator Step‐up Transformers
18.6 Heat‐Rate Curve
18.7 Hydraulic Turbine Cavitation
18.8 Generator Cooling
18.9 Plant Black Start
18.10 Synchronous Motor
18.10.1 Damper Winding
18.11 Plant Capacity and Availability Factors
18.11.1 Typical Capacity Factors for Power Plants
References
19 Power Dispatch and Control. CHAPTER MENU
19.1 Plant and System Operation
19.1.1 Load Variability
19.1.2 Plant Scheduling
19.2 Load – Frequency Control
19.2.1 Moment of Inertia H
19.2.2 Governor Control
19.2.3 Deadband
19.2.4 Speed Droop
19.2.5 Generator Droop Control
19.2.6 Generator Operation
19.2.6.1 Single Generator Operating in Parallel on Grid
19.2.6.2 Multiple Engines on Isolated Bus
19.3 Voltage Reactive Power Control. 19.3.1 AVR Droop Characteristic
19.3.2 Generation Operation Modes, Reactive Power Sharing
19.3.2.1 Island Mode, Single Generator
19.3.2.2 Single Unit, Synchronized with Grid
19.3.2.3 Island Operation with Paralleled Generators
19.4 Line Transfers, Import/Export Power
References
20 Diesel Engine Generator Plant and Standby Power. CHAPTER MENU
20.1 Gen‐Set Ratings and Classifications
20.2 Plant Design
20.3 Unit Performance
20.3.1 Example 1
20.3.2 Example 2
20.4 Plant Electrical One Line Diagram
20.5 Waste Heat Recovery (WHR)
20.6 Engines for Ships
References
Note
21 Reliability Considerations and Calculations. CHAPTER MENU
21.1 Definitions
21.2 Basic Reliability Engineering Concepts
21.2.1 Basic Mathematical Concepts in Reliability Engineering
21.2.2 Failure Rate and Mean Time Between/to Failure (MTBF/MTTF)
21.3 Different Failure Rates vs. Time Scenarios. 21.3.1 The “Bathtub” Curve
21.3.2 The Exponential Distribution
21.4 Estimating the System Reliability
21.4.1 Series Systems
21.4.2 Parallel Systems
21.4.3 Parallel and Serial Elements
21.4.4 Piper Alpha Rig Explosion
21.5 Common Mode Failure
21.5.1 Space Shuttle Program
21.6 Availability
21.6.1 Inherent Availability, Ai
21.6.2 Operational Availability, Ao
21.6.3 Availability Calculations
21.6.4 Availability in Series
Example
21.6.5 Availability in Parallel
References
22 Fire Protection. CHAPTER MENU
22.1 Plant Fire Protection System
22.1.1 Fire Detection and Monitoring
22.1.2 Smoke and Heat Detectors
22.1.3 Main Fire Alarm Panel (MFAP)
22.2 Fire Sprinkler Systems. 22.2.1 Sprinkler Heads
22.2.2 Wet‐Pipe Sprinkler System
22.2.3 Dry‐Pipe Sprinkler System
22.2.4 Preaction Systems
22.3 Gas Flooding Suppression. 22.3.1 Large Generators
22.3.2 Control Rooms
22.3.2.1 VESDA Systems
22.4 Fire Hydrants and Standpipes
22.4.1 Standpipes
22.5 Portable Fire Extinguishers
22.6 Fire Safety Dampers and Duct Vents
22.7 Deluge Systems
22.8 Fire Water Supply System
22.8.1 Water Storage Tanks
22.8.2 Fire Pumps
22.8.3 Pump Controllers
22.8.4 Fire Pump Sizing
22.9 Cables and Conduits used for Fire Protection Circuits
22.10 Fire Detection and Notification Witness Testing
References
23 Corrosion, Cathodic Protection. CHAPTER MENU
23.1 Process of Corrosion and Cathodic Protection
23.2 Galvanized Steel
23.3 Sacrificial Anodes. 23.3.1 Galvanic (Sacrificial) Anodes
23.4 Impressed Current Application
23.5 Soil Resistivity
23.6 Cathodic Protection for Ships
23.6.1 Parts Affected on Ship
23.6.2 Protection against Corrosion
23.7 Corrosion due to H2S Gas
23.7.1 Mitigation
References
24 Brief Equipment Specifications and Data Sheets. CHAPTER MENU
24.1 Power Transformers
24.1.1 Winding Configurations
24.1.2 Transformer Phase Shift
24.1.3 Tap Changers
24.1.4 Dry and Oil Type Transformers
24.1.5 Transformer Dielectric Tests
24.1.6 Basic Insulation Level (BIL)
24.1.7 Excitation Current
24.1.8 Inrush Current
24.1.9 Autotransformers
24.1.10 Transformer Parallel Operation
24.2 Motors up to 200 kW
24.2.1 Design Criteria
24.2.2 Torque
24.3 Motors > 200 kW (Medium Voltage Motors)
24.4 VFD Specification Requirements
24.5 13.8 kV Isolated Phase Bus + PTs (IPB)
24.6 Electrical Enclosures
24.6.1 NEMA Enclosures
24.6.2 CE and IEC Classifications for Enclosures
24.7 Technical Data Sheets
MCC Specific Details
References
25 Solar Power. CHAPTER MENU
25.1 Solar Resource
25.2 PV Panel Technology
25.3 Photovoltaic Plants
25.3.1 PV Equipment
25.3.2 PV Projects
25.4 CSP
25.4.1 Power Tower Systems
25.4.2 Parabolic Trough Systems
25.4.3 Fresnel Linear Mirrors
25.4.4 CSP Costs
25.4.5 CSP Operating Plants and Projects
25.5 Thermal Storage
25.5.1 Balance of Power (BOP) Plant
25.5.2 Peaking Storage Plants
25.5.2.1 Hybrids: mixture of battery and gas turbines
25.5.2.2 Kauai (Hawaii) solar plant with litium ion battery storage
25.5.3 Battery Storage Costs
25.6 Conclusion. 25.6.1 PV Plants
25.6.2 Concentrated Solar Plants
References
26 Wind Power. CHAPTER MENU
26.1 Siting a Wind Farm
26.2 Wind Turbine Tower
26.3 Wind Resource. 26.3.1 Wind Gusts
26.3.2 Wind Rose
26.3.3 Power
26.3.4 Wind Tip Speed Ratio λ
26.3.5 Capacity Factor (CF)
26.3.6 Wind Energy Distribution
26.4 Wind Turbulence. 26.4.1 How Does It Affect the Turbine Performance?
26.4.2 What Causes Atmospheric Turbulence?
26.5 Wind Turbine Design Classification
26.6 Blade Design for Optimum Energy Capture
26.7 Individual Pitch (Blade) Control (IPC)
26.8 Wind Turbine Design Limits
26.9 Wind Turbine Components
26.10 Generators Used with Wind Turbines
26.10.1 Fixed Speed Wind Turbine Generators
26.10.2 Variable Speed Wind Turbine Generators
26.10.3 Synchronous Generator with In‐Line Frequency Control
26.10.4 Doubly Fed Induction (Asynchronous) Generator – DFIG
26.10.4.1 Converter – Grid Side Converter (GSC)
26.10.4.2 Machine Side Converter (MSC)
26.10.4.3 DFIG Control, Frequency
26.10.4.4 Voltage
26.10.4.5 DFIG Performance
26.11 Turbine Sizes
26.12 Building a Wind Farm
26.12.1 Grid Integration Issues. 26.12.1.1 Wind Farm Impacts on Utilities
26.12.1.2 Load Variability
26.12.1.3 Wind Turbine Start
26.12.1.4 Voltage Requirements
26.12.1.5 Reactive Power Requirements
26.12.2 Utility Stability Requirements for Wind Farms
26.12.2.1 HVRT Capability
26.12.2.2 LVRT Capability
26.12.3 Managing Variability and Voltage Regulation at Wind Farms
26.12.3.1 Impact On Cost
26.12.3.2 Impact On Stability
26.12.4 Methods of Transient Regulation of Power Generation. 26.12.4.1 AGC
26.12.4.2 Load Following
26.12.4.3 Unit Allocation
26.12.4.4 Reactive Power Charges
26.12.4.5 Availability
26.13 Wind Energy in Cold Climates
26.13.1 Gaspe Region
26.14 The Effect of Rain on the Wind Turbine Performance
26.14.1 Conclusion
26.15 Wind Turbines in the Desert Environment
26.15.1 Blades
26.15.2 Rotor Hub
26.15.3 Air Intakes and Exhausts
26.15.4 Bearings
26.15.5 Electronic/Electrical Systems
26.16 Cost, Component Percentage Share
References
Index
WILEY END USER LICENSE AGREEMENT
Отрывок из книги
Zark Bedalov Vancouver BC, CA
Starting as an engineer is not easy. You are facing a big transition. I'm certain this book will help get you through the most critical phase of your development as an electrical engineer and make you the confident and knowledgeable professional that you wanted to be when you decided to be an engineer.
.....
The units of LCOE are money/energy (usually $/MWh or c/kWh1).
.....